Brief History
“Winches are lifting, hauling or holding devices in which a tensioned rope is wound round a rotating drum “(Purohit & Purohit, 2006). Typically, power winches are mechanical devices used for pulling or adjusting the tension in a cable. Winches have a history dating back to the 4th century before BC. Historical Winches were made of wood and were mostly used for tightening cables or ropes across bridges. There is scantly information about the origin and history of winches, but the earliest records by Herodotus of Halicarnassus indicate that wooden winches dominated the architectural form as was referenced by Aristotle and might have been in use by the Assyrians at the that time for several purposes and particularly for tightening ropes used on bridges. Little is mentioned about any different varieties of winches at the time. However, it is crucial to note that winches played a significant role particularly in tightening cables to improve the tension in the wires that were used across bridges.
Application
Winches are designed to increase the tension in a wire or rope to give it the mechanical properties suitable for use in different lifting settings. Typical uses for winches include theatre lifting, in water treatment tensions, suspensions, sports rooms, and transport trailers. In this case, winches have the mechanaical properties that make them safe, a high capacity in this case of over 2 tons, and easily maneuverable. In addition, winches should have corrosion resistant properties where materials.
Winches come in various forms and applications. Industrial winches are among the types of winches with different applications based on each type and specifications. Typical examples include Capstan winches which are used in marine operations and can be “are powered manually, electrically, hydraulically, or pneumatically”. The mode of operation of the Capstan winches is that they accommodate a structure that allows for a line to be released at an angle from the drum with the drum positioned vertically while it is used horizontally. Another type of winches is the Friction winches. Friction winches are designed with two large friction drums with a larger drum that for rope storage. The two other drums are used for running the line. Another type is the hand winch that is designed for use in light weight applications. The winch functions by use of a manual device with a handle having a barrel with an axis that acts as a fulcrum. In this case, gears used fall into a number of categories. The gears include planetary gears mechanisms which are usually of low cost, have a compact size, provide smooth operation, and of low weight. Planetary gears suffer from the disadvantage of spooling of the drum which increases the operating temperature, and require the use brakes.
Other are where winches are applied includes in oilfields, military, automotive industry, mining, marine, recovery, and in the construction industry.
A typical example is the use of winches in the marine industry as demonstrated below.
It is critical when using winches to take various safety measures and observations that are provided and detailed in the manuals that are sold with the winches. While the safety observations and measures vary between the types of winches, general application areas, and other working conditions, the following are critical safety observations and measures to take.
- A winch should not be shifted while under load.
- One should not place the hand or lag near or on a moving part.
- A winch should not be operated when a vehicle is on unstable ground.
- A winch should not be shifted in a sudden manner that is likely to cause accident form occurring.
- One should not operate the winch while under the influence of alcohol
- Any person doing an adjustment or any repair should wear goggles and other protective clothing.
- A winch should not the used to pull more than the authorized load.
- Any area of operation of a winch should be kept clear of people.
Research studies show that any person operating a winch should read the manual for use, servicing, and installation manual to safely handle the device. That is in addition to the fact that winches come in different types and applications (Danny, 2005).
Technical Design
The technical design of a winch depends on where it is to be applied and the type of winch. Most winch designs are market driven, with several options provided to meet specific market needs. Winches should have technical properties such as being corrosion resistant using aluminum alloy for making the high speed rotating drums, bronze and stainless steel depending on the choice of material to be used.
Issues to consider when carrying out the technical design include identifying number of elements as discussed below:
In the technical specifications, the design should lift or lower a load of 2 tons and should be able to draw in the cable at the rate of 0.2 m/s as a performance requirement. It should also be possible for the winch to operate with the forward and reverse with a breaking system that operates at 150% of torque due to the winch.
Drive system: the drive system for the winch is based on an electric powered motor which depends on emerging technologies that optimize the use of flux vector drives. The controls can allow for speeds varying between 2 % and 100%. Other considerations to make for the designs of the power which include the product lifespan-In this case, the lifespan of the proposed winch should not exceed 10 years. That is in addition to making spare parts available within the lifespan provide of the winch (NTN, 1997).
Cables
In this case, the drum is designed with a heavy cylinder with two flanges integrated into the design to contain the cable. The purpose and the load to be handled by the winch are used to determine the material used for the cable. In this case, the working load must be equal to five times the working load. In this case the middle later is used to determine the force and speed on the winch.
Drum
To tidily guide the cable around the drum, a groove is used in this case. The hauling forces and the material used are determinant factors in determining the hauling forces of the winch.
Design
The materials use in the design and the loads are calculated using the optimum values.
Mechanism For Lifting
It is important to design a mechanism that factors each parameter that matters in each of the steps involved in the design process. In this design, suppose the lift rate is given by Lr, Aalt the number of actual lift time, LT the lift, and NL the number of lift actions, then the following equation holdGeas:
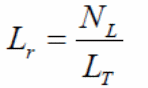
The above equation holds true for the lift rate or the number of time for each cycle of lifting. The whole process is executed by the winch lifting gear mechanism shown in diagram 1 below:
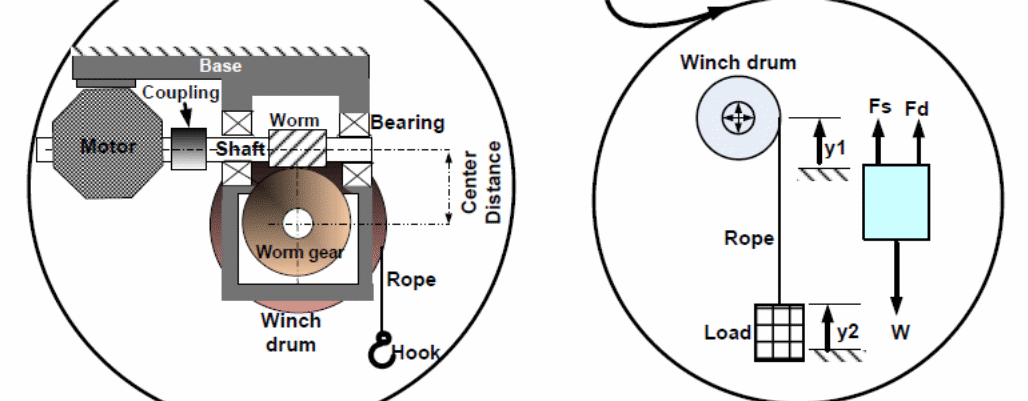
In figure 1 above, the driven winch mechanism is an assembly of a motor with a shaft connecting the gear mechanism of worm gears connected to the rope and a hook used for lifting. The total time, which is the lift fraction (Lf) is the time for lifting the load, lowering, and the static time, which is only utilized for lifting the load. The total nominal load (TNL), average velocity (AVL), the live load (LL) is calculated using the equations shown below. In this case, the weight of the rope and hook constitute the dead load. In the mathematical expressions, the vertical height is the Lh , through which the load is conveyed.
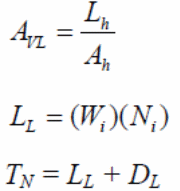
It is critical to calculate the power required for lifting using the following mathematical relation:
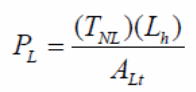
In this case, the angular velocity of the drum can be calculated using the following equation:
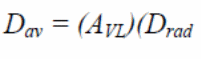
In this case, the radius of the drum in the above equation is calculated using the following equation:
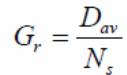
At this point, it is critical to determine the maximum dynamic loading which is Fmax, in this case should be determined to ensure no excess load is applied on the mechanism. It is critical to specify the weight W, the damper force Fd, and the spring force Fs which obey Newton’s second law of motion. In the above diagram, the relation is given by:
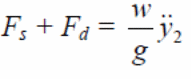
Fs can be computed as follows:

Ÿ and ý in this case are the values of the acceleration and velocity respectively. In the design process, the parameters to consider include the forces, torque, moments, safety factors because of the material used, and any deflections of particular sections of the winch. Standard tables are used for the selection of materials (Danny, 2005).
A complete design in this case is based on the set of wheel used. In this case, the solution is to use a set of worm gears because the design parameters require that the worm gears be used for the lift mechanism. In this case, the parameters used for deciding the type of design and mechanisms for lifting include the required input speed (N1), output speed (N2), and Torque (M1). It is critical to select the appropriate type of material to use for the gears based on for worm/wheel and diameter factor (q). It is also crucial to calculate the gear ratio in the design based on standards and the following equation:
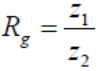
The worm Z1 and wheel Z2 have a number of threads defined using the following equations respectively:
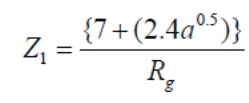
And
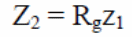
Shaft design
The shaft use di the design is circular in cross section for transmitting motion from or torque form the motor to the wheels. The materials used for the shaft are resistant to load stresses, strengthened from heat, low fatigue failure, and the usual material of choice is low carbon or medium carbon steel. Each of the shafts is designed with shoulders for carrying thrust loads. The shaft should also support torsional deflection and torsional stresses. Each of the mathematical relationship between the shafts and stresses are shown in the relationships below.
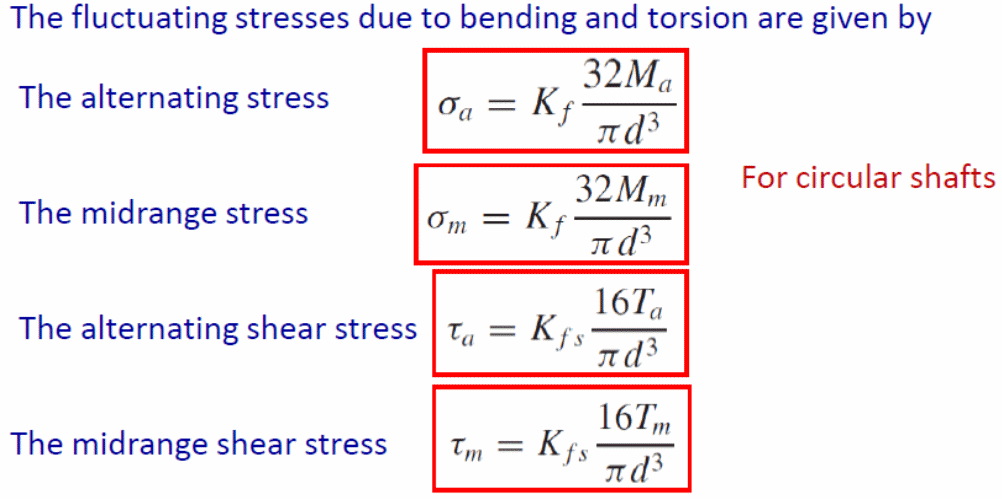
In this project, considering a shaft subjected to bending and torsional stresses, with a mechanical advantage (Ma) =70 n-m, then minimum shaft diameter is given by:
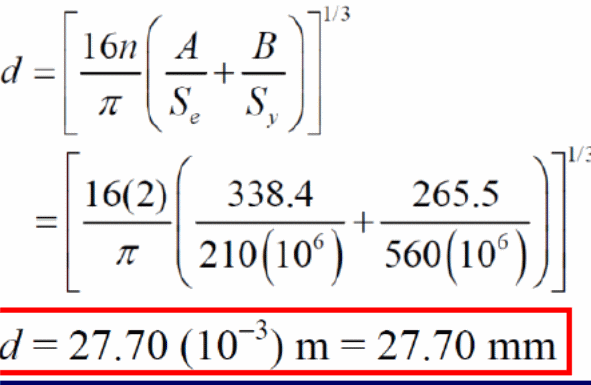
The diameter is calculated based on DE-Soderberg’s equation for analyzing the stress in a shaft.
Gears design Factor
Worm Gear
The power and torque transfer of the worm gear is rated above 35% and below 40% efficiency. The transfer power of the winch makes it able to self-brake while functioning under light or heavy loads. It is important to integrate into the assembly a breaking mechanism to provide free spooling. The advantage with worm gears is that they can “accommodate and work in a built-in braking mechanism, and have the additional capability to slow down the winch speed and work with a simple planetary gear mechanism, which can operate without a breaking mechanism” (Purohit & Purohit, 2006). Worm gears suffer from the primary drawback of the capability to reduce the speed of a winch especially the line speed when the rope or cable is not under tension or load conditions (NTN, 1997).
The worm gear mentioned above which was taken as the preferred choice in this study resembles a screw driver, and rotates in a direction that depends on the worm gears are cut. The rationale for using the worm gear is the area of application.
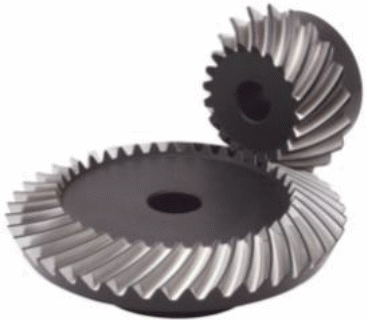
The nomenclature of the wheel is indicated in diagram 3 below. All the sections of the wheel are indicated in the diagram shown below.
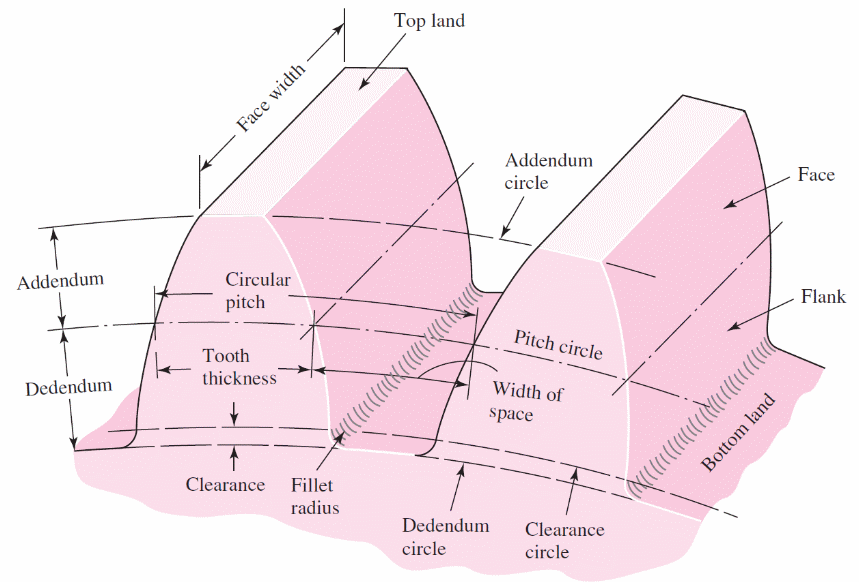
In figure 2 above, the pinion and the gear mate making the contact indicated in figure 3 below.
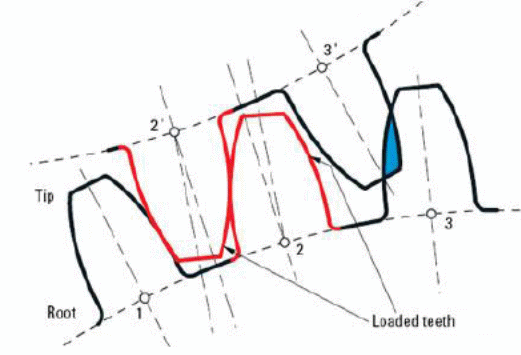
In the above design, the worm gears and the worm have different helix angles with the helix angle on the worm being very large compared with the helix angle of the smaller wheel, which is very small. In figure 1 above, we take the pinion gear with 20 teeth, the worm with 36 teeth, helix angle to be 36°, a pressure angle of 25°, and a pitch diameter of 4 teeth/in. We can find the normal circular pitch by:
Pn=π /Pn=π/ 4=0.7845 in
Axial circular pitch is given by:
= Px = Pt / tan ý=0.9069/tan 30°1.571 in
Transverse circular pitch is given by:


And the axial circular pitch is given by:


The normal circular pitch for the gears is given by:


The transverse diametrical pith is given by:
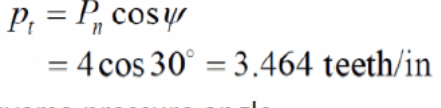
With the transverse pressure angle given by:
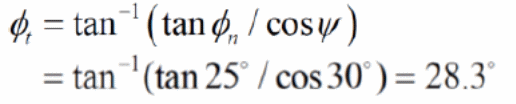
Each of the gears used in the assembly of the winch have the following mathematic relationships and values:



Bearings
The type of bearings used in this case is roller bearings. Roller bearings function on rolling and sliding movement actions. The motion of the bearings is indicated in the schematic figure 4 shown below (NTN, 1997). The actions of the bearing elements are non-linear, equi-pitched, with flexurally rigid races, operate under isothermal conditions, and deform according to Hertzian theory of elasticity. The effective elastic modulus is given by
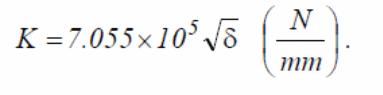
The values of δ* can be taken for the following table.
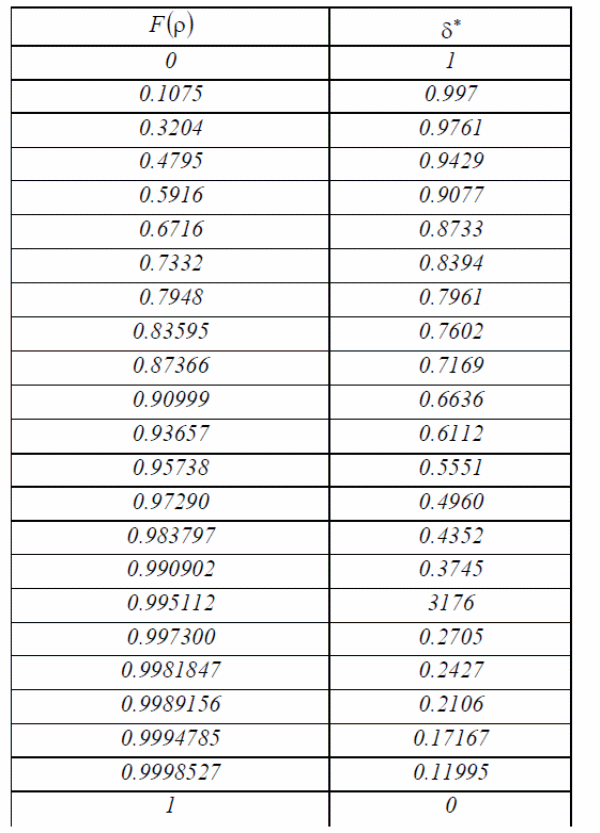
The above values are the Dimensional contact parameters by Harris (1991).
In this case, the geometry of contact is given illustrated in the figure 5 below.
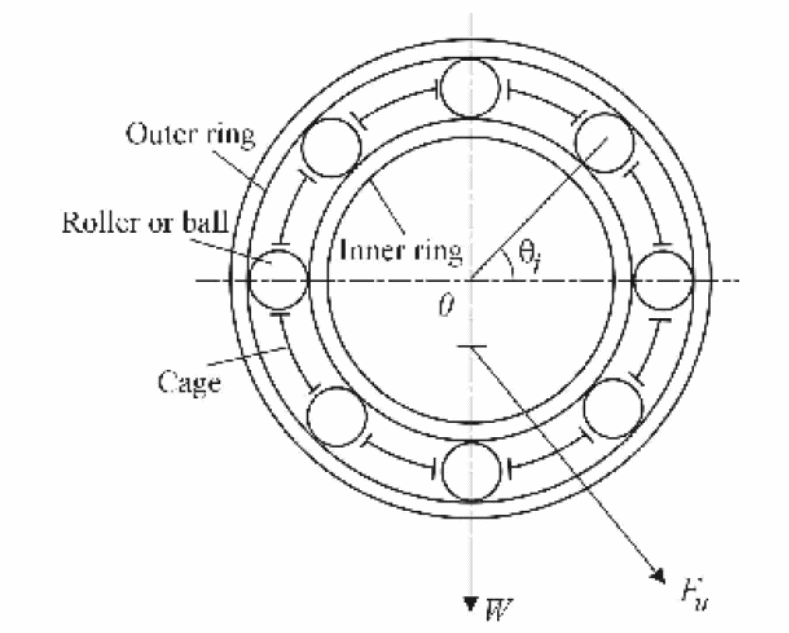
Figure 4, ball bearing schematic diagram.
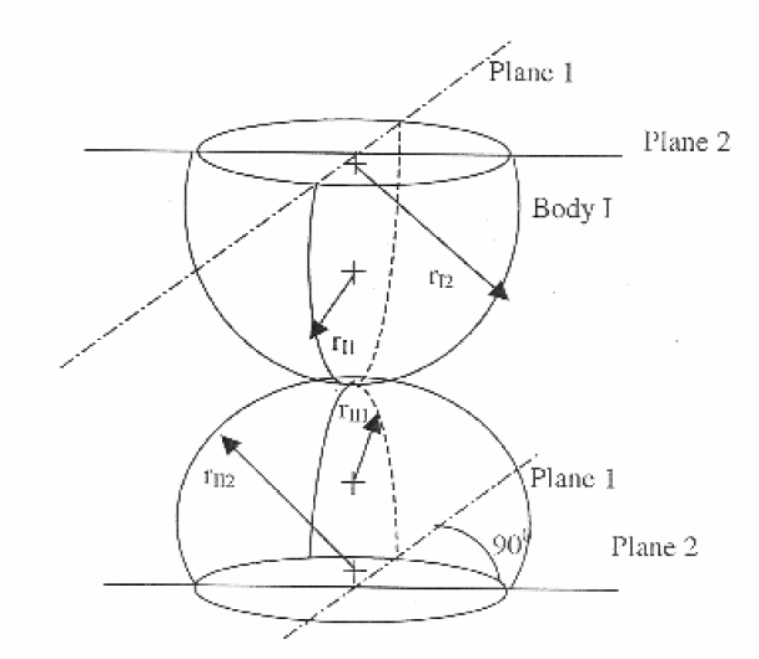
The following table provides the standard values that can be replaced above when designing and identifying the properties for the bearings to use.
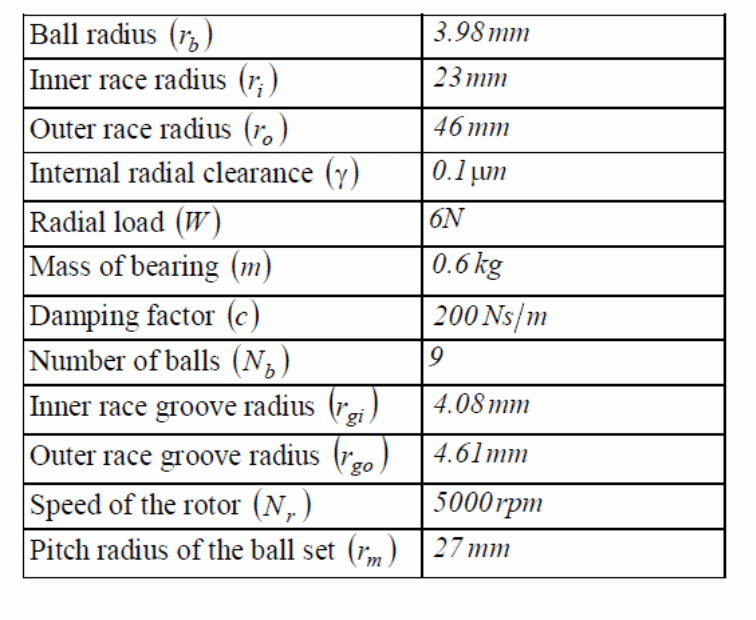
The expected lifespan of the bearings can be calculated based on the mathematical relation: L = T × n × 60. In this case, n is the number of revolutions per minute and T is the number of hours of operation of the ball bearing (Danny, 2005). Usually, the life-pan of the bearing is according to the following illustration:
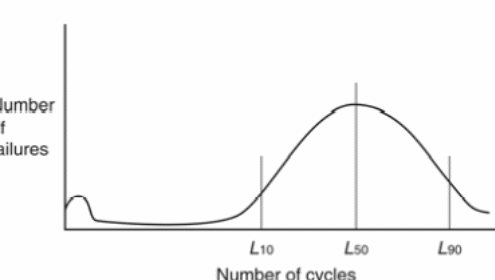
Since the general equation of the ball bearing is stated as below,
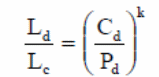
Here, the symbols used are as shown below.
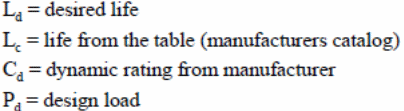
It is critical to note that the lifespan of the bearing decreases with time and load conditions. The equation can be changed to accommodate the ball bearings used in this case.
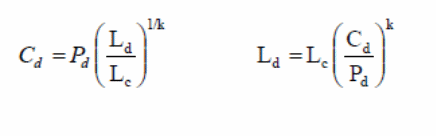
A typical example for the current study is where the ball bearing operates under a dynamic load rotating at a speed of 1750 rpm, the number of hours the bearing rotates is determined as follows:
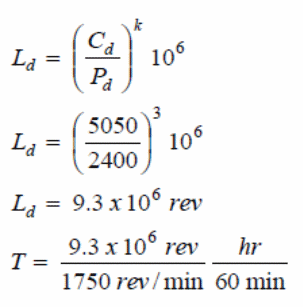
That gives a lifespan of T=88 hours.
To achieve maximum ball bearing capacity, then, an optimum number of ball bearings must be inserted so that the maximum radial load can be gained. The best method of inserting is through thermal expansion of the outer ring to take a greater thrust. Ball bearings are susceptible to different forms of failure and need due attention to increase their operating lifespan based on the following descriptions.
Hoop Stress
In this case, when the winch is under load, the cylindrical part of the machine is subjected to circumferential stress, an element that the designer should factors when designing a winch. In this case, the drum is subjected to internal and external pressures due to the fluid in this case air acting on the internal surface of the cylinder. Figure 2 below shows the direction the forces on the winch act in different directions.
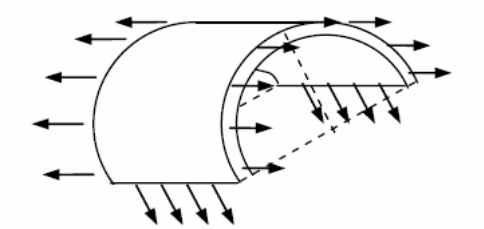
Suppose the pressure acting on the cylinder is p, taking the radius of the drum to be r, with a thickness equal to t, the total forces acting on the cylinder due to the pressure p can be calculated using the following mathematical relation:
P × (2r ×1), this force can be calculated based on the unit length of the cylinder. If the stress acting to oppose the force is given by σ1, then, for an equilibrium condition to be attained, the mathematical relation holds:

In the above case, the value of σ1 can be calculated using the following relation:
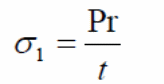
The value of σ1 plays an important role in the design because it is the circumferential stress also known as the hoop. It is critical to note in brief that the circumferential stress can be derived using the following equations:
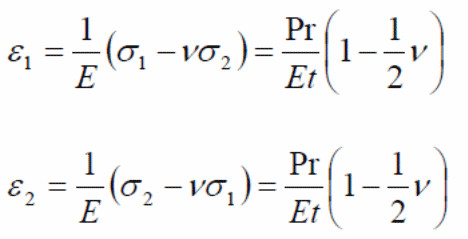
The mathematical relations imply that the materials used in elastic. However, the equations apply when the force acting on the hoop is constant. Sometimes when forces are acting on the winch, the wire coil, and the cylinder comes under tension leading to a hoop stress being generated ion the cylinder.
For equilibrium to be attained at this point, the pulling force is related to the hoop stress ion the following equation:

And the relation,holds.
Different standards provide different recommendations for the hoop stress and tension on the rope. One example is the DNV Standard which provides a maximum allowable load of 85% of the yield stress of the material sued in the construction of the component. Typically, the recommendations are critically analyzed and the allowable stress forces are within the limits recommended by the standards. The factors that determine the amount of stress and the work load includes the material used to make the components and the thickness of the drum. That is because the maximum allowed load enables the drum to work without buckling under the applied load and tension on the rope (Danny, 2005).
In this design, it is assumed that:
- The pitch is kept at 0.1 m of the pitch rope.
- No stiffeners are used to increase the tension in the rope.
The current winch can support a load of 2 tons with a load rope capacity of 2 tons.
From the above equations, then, the ultimate pulling force on the rope is given by:
S=1.1×2 ×103×9.81 =21.582 KN
Because the designed thickness of the hoop stress is 70 mm,
Then,
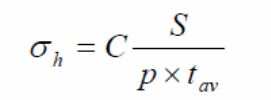
When c=1
=5.396MN/m2
Then, the allowable hoop stress =0.85×350=297.5 N/M2
The working hoop stress can be calculated suing the following table or any other standards provided.
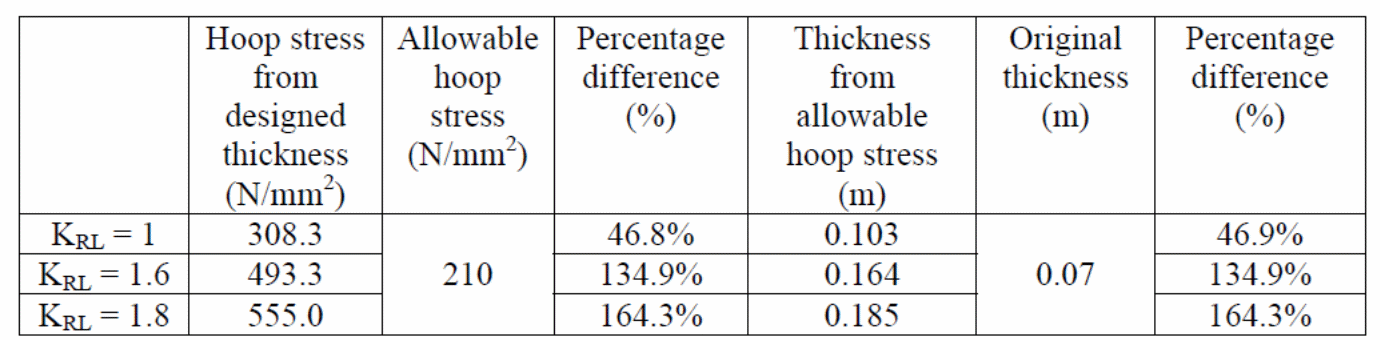
Motor Torque and Speed
Winches are subjected to different load and torque conditions while the motor is subjected to two types of forces, the stall torque and the no load speed. In both cases, it is critical to mathematically model the type and direction of the forces subjecting the motor. In this case, for our design, we assume it is a steady state motor.
In this design, the winch dissipates minimum power because of minimum friction because of the contact between the moving parts. The moving parts cannot be 100 % free from friction despite applying the lubricant.
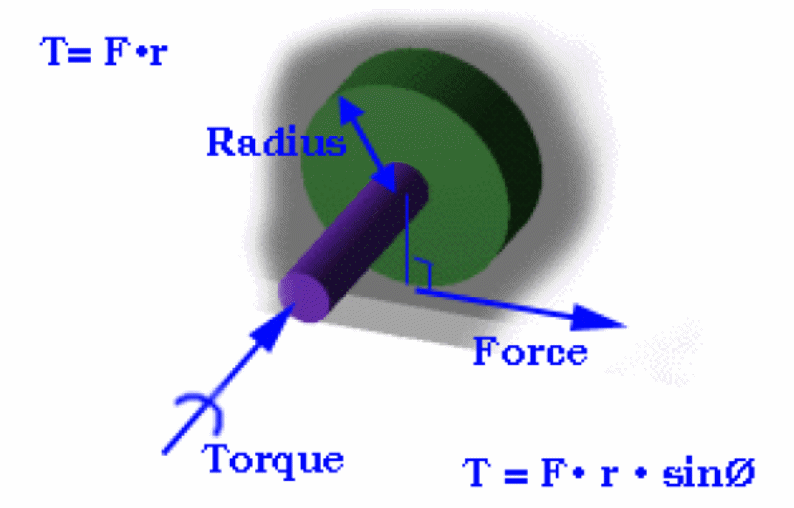
Taking the diameter of the above shaft to be 1.5 in, the tensile, torsional, and compressive shear stresses can be calculated based on the following position of the forces (Danny, 2005).
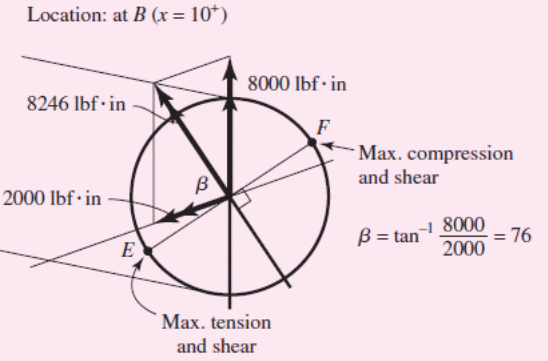
At the point b above, the force is given by:

At point c, the force is given by:

Since the net bending moment for the shaft is 8246 lbf, the optimal bending stress is given as

In this case, the since the maximum torsional stress occurs between C and B, then, it is given as:

Taking point E, it is possible to find the maximum tensile stress which is given as:

In this case, the maximum compressive stress is given at point F by:

And the extreme stress occurs on the points E and F, it is given by:

In the above case, the force acting on the winch or the wheel is tangential. If the motor rotates at a constant speed, then the motor power can be calculated as follows.
Since power is given as
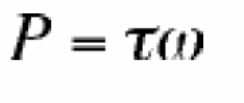
Then the power of the motor can be calculated as a function of the velocity of the motor and the torque due to the motor as shown below:
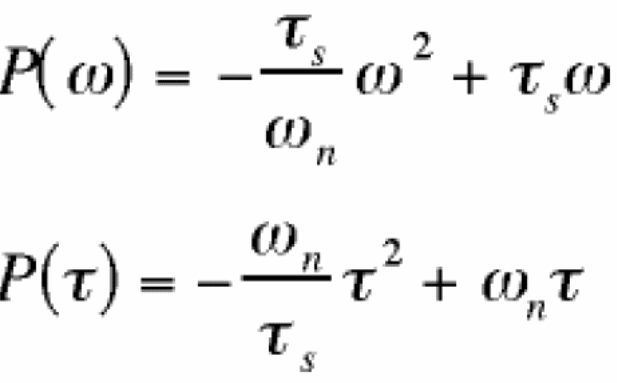
If a graph of the rotational speed vs the power of the motor is calculated, then, we have a graph as shown below. On the other hand, the graph of torque against the power produced is shown on figure 4 below.
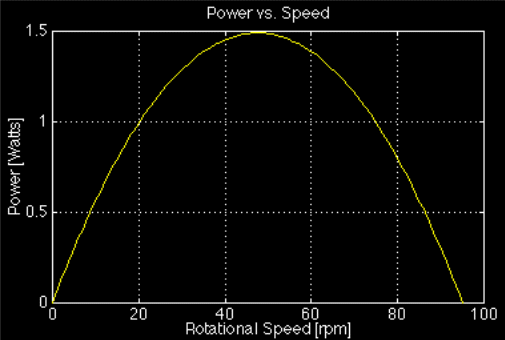
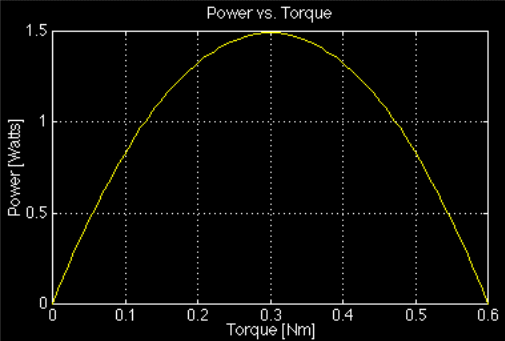
It can be shown that the maximum speed and load are half of the Ts and Wn respectively. In this case, the wheel should rotate at the speed, was shown mathematically below (Danny, 2005).
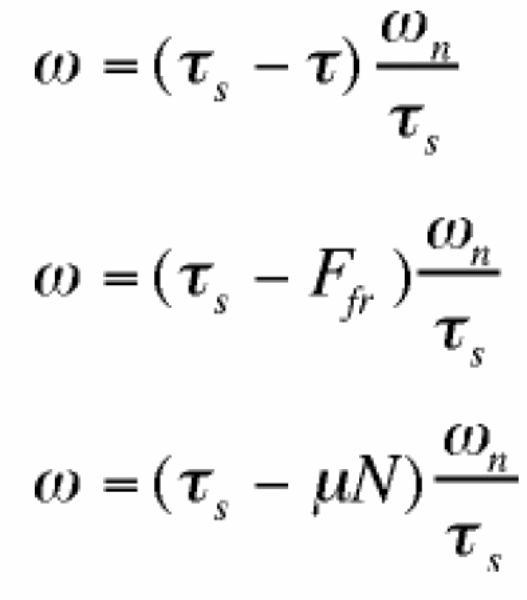
The torque on the shaft is calculated using the relation:
TA=F cos 20°(d / 2).
For the current winch design, the pitch diameter of the worm gear is 150 mm, if the pressure angle is 20°; the torque applied on the shaft is 340 nm, taking the factor of safety to be 2.5 and substituting the values in the equation for calculating the torque on the shaft, the torque on the shaft is:
F=2 TA/ (d cos 20°) = 2 (340) / (0.150 cos 20°) = 4824 N
The bending moment is optimal at a point and is given by:
Mc= 4824 (0.1000) = 482.4 N.M
Other Winch Components
When designing a winch, it is practical and critical to consider the most basic various components which when assembled make the winch. The most basic components are discussed below. Most of the “components are made from steel plate fabrications and the components joined together by welding them. It is possible to use other material such as aluminum and stainless steel”. On the other hand, an alternate assembly can be used to make the winch so as to avoid welding the parts together. The basic components of the winch being designed include the end cap, pawl pin, mandrel, sprocket, and the frame. It is typical for the end cap to be fabricated form steel tubing and assembled into the body of the winch to make a tight fit at the end of the mandrel (Danny, 2005).
The forces acting on the frame when under load and motion forces requires that the frame be made of a tough material in this case a steel plate. The two holes are created in the frame through a stamping process. The two holes provide a way through which to fit the mandrel with a smaller hole made into the body of the frame through which the pawl pin passes. Once the frame has been fitted with the components, it is then bent into a U shape (Danny, 2005).
In the design process, it is critical to attach the sprocket to the mandrel with the purpose of making sure that the system is properly aligned. Here, the sprawl and the sprocket are aligned correctly with the pawl for proper line adjustment.
It is important to fabricate the mandrel from steel. In addition, the mandrel is designed to accommodate other components such as the synthetic web tie down. It is important to incorporate smooth holes into the design to avoid sharp cutting edges penetrating into other components and slots during the design stage.
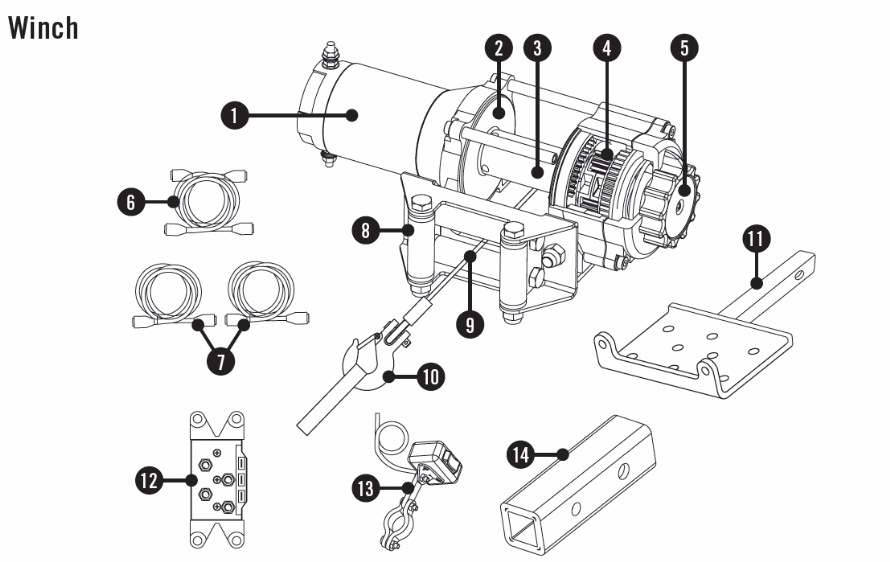
In the above case, the power winch is designed with a mort that provides
The Motor Type
A typical example of the motor to use for providing power to the winch is shown in figure 5. There are two types of power driven winches. These include DC driven motors or AC motor driven winches. In this case, DC motors are designed with a Series Wound Motors with Permanent Magnet Motors. Any electrically driven motor must have an armature which is a set of coils, contained inside another set of coils consisting of permanent magnets referred to as the starter. A magnetic field, when acted upon by an armature causes rotation due to the induced electric current. In this case, the current induces motion in the coils because of the torque produced when an electric current flows through. The torque and power produced by the motor depends on the number of coils made in the armature of the motor. The higher the horsepower rating, the higher the power rating of the motor, the more the torque produced by the motor, when driving a winch. The gear train can be used to rate the current winch in addition to using the torque, pulling power of the motor, and the motor speed. It is critical to examine the type of materials and construction of the motor to crystalize the application of the motors in providing power to drive the winch. Typically, one of the types is the permanent magnet motor type.
Permanent Magnet Motors
For this case, the starter is made of a permanent motor with the benefit that when the motor is running, the drain on the battery usually low when compared with series wound motors which uses coils to provide magnetic properties when current flows through the windings. The only disadvantage with permanent magnet motors is that they are suitable for use in light weight winches. That is in addition to the fact that they generate a lot of heat and in most times overheat when in motion and under loading conditions.
Series Wound Motors
Series wound motors provide another option to provide a power sources for driving the winch. In this case, the coils used to make the motor consist of a series of wound coil to make an armature. Such kind of motors provides better and higher performance drives when compared with the permanent magnet motors. The disadvantage is that such motors are more expensive though they have the advantage that they are suited for heavy duty work.
Winch Ratings
In this case, the rating for the winch limited to the maximum amperage draw which in most cases is approximately 400.
The following is a typical example of the winch assembly.
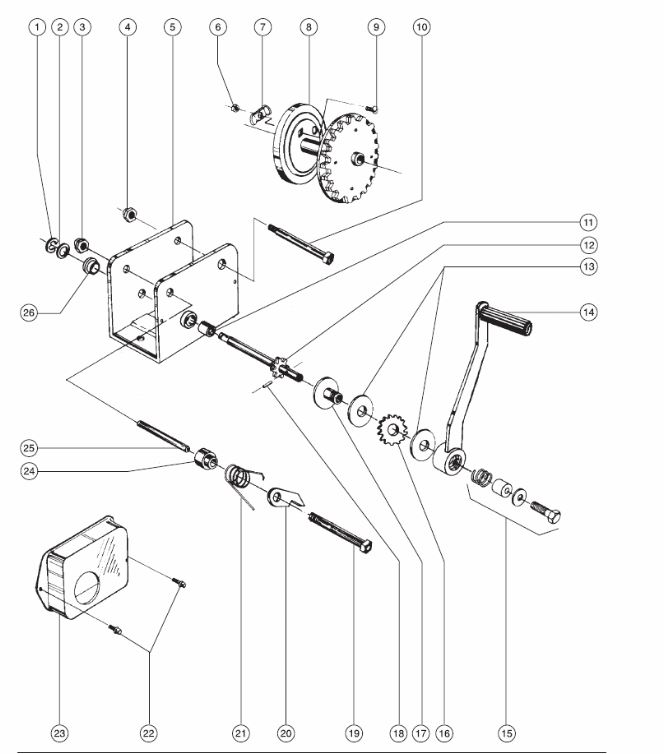
Figure 5 above provides an exploded view of the winch assembly that can be hand held. The following table provides a detailed list of the parts that make up the winch in figure 5 above.
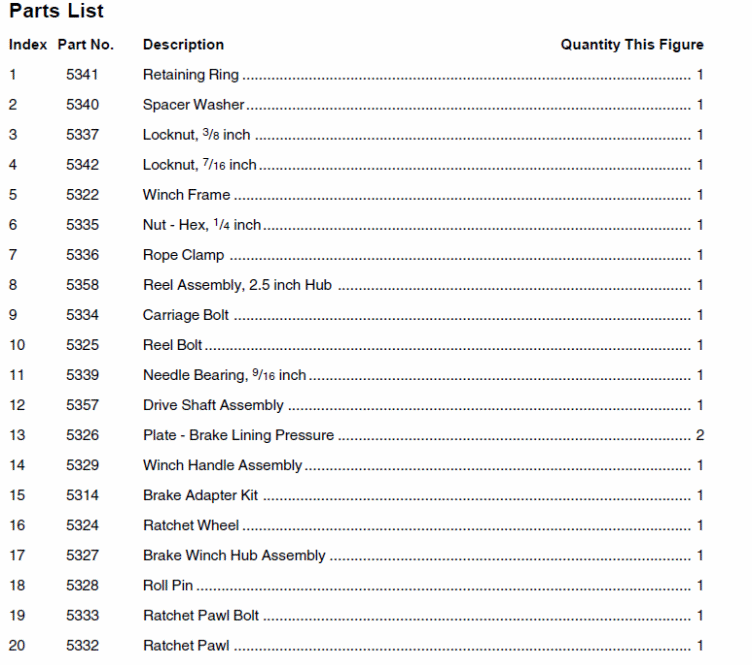
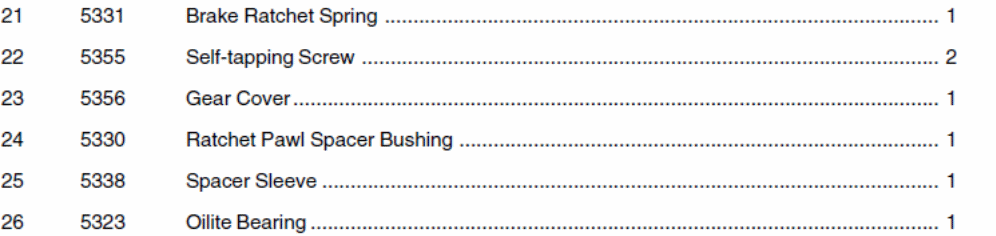
It is important to note that the materials used in the manufacture of the power winch are product specific and the details can be provided by the manufactures in the manufacturer’s manual. With the specifications and the parts clearly listed above, each of the parts fits into the other when mated producing the required winch.
Load and Stress analysis
Once the winch has been designed, it is critical to conduct a stress analysis on the components based on a specific model. Stress analysis provides appropriate numerical values and models to identify the best materials and the working load of the winch. Different models have been designed for conducting stress analysis, among them including atomic microscopy. In this case, the scanning is done on the material in question to reveal information about the chemical composition of the materials used for the winches. The method is very effective in revealing different material properties used in the winch, but the method is expensive and sometimes not available for use. Another approach for stress analysis is based on mathematical definitions of stress. In addition, stress the following analysis is based on different state conditions such as when at equilibrium,
From a theoretical perspective, if some forces are acting on the body of a component, in this case any of the components used in the assembly of the winch, then there are other forces acting against the force due to the winch as illustrated in the figure 7 below (Purohit & Purohit, 2006).
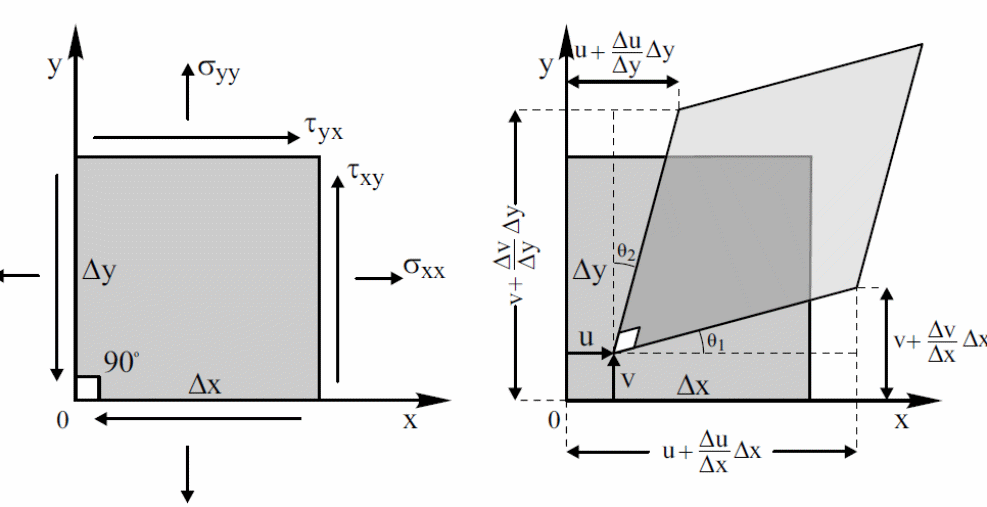
In the above case, the forces theoretically acting on the components in the form of u and v represent the shear and normal strains respectively. A unit change when a force is acting on a component produces a strain equivalent to €xx with a small displacement equivalent to
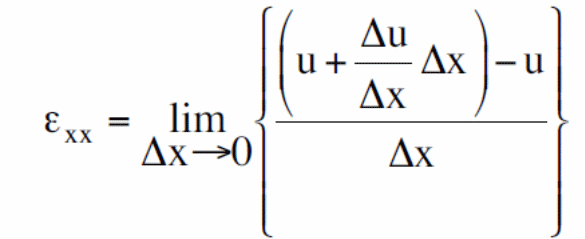
The unit changes are in the directions z and y. In this case, the strain is taken to be in a small amount and the normal strain can be calculated using the following formula:
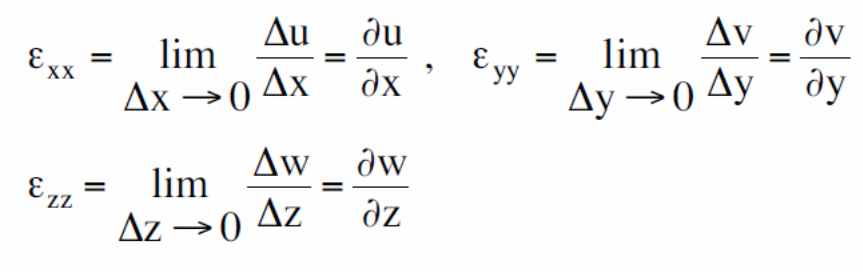
Note in the above mathematical relation that u, v, and w are the displacement components being considered in the test (Purohit & Purohit, 2006). The shear strain can be analyzed since it is the distortion that is experienced from the original angel of 90° causing a small deformation mathematically related as below.
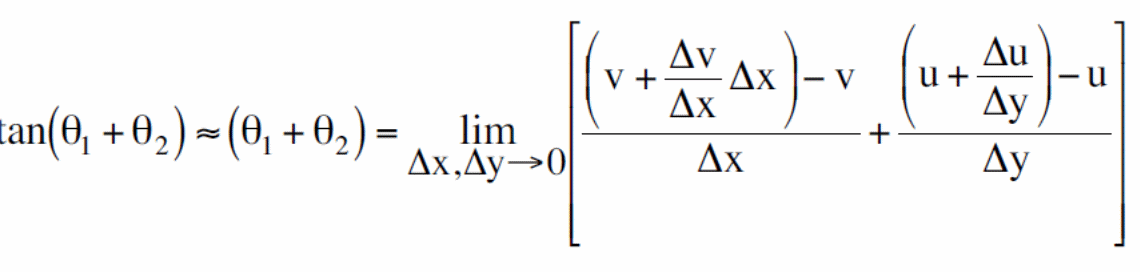
The results are three shear strain mathematical relationships as follows.

In this case, tensorial mathematics has been applied in calculating the stress and strain in the components used in the winch assembly. It is possible to model all the components of stress and strain in the winch assembly using the following matrix.
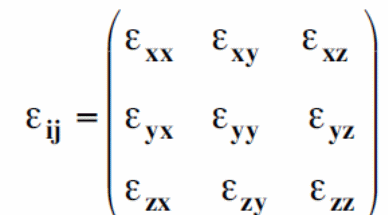
In this case, the strain matrix is symmetric and satisfies the condition:

Because some of the materials used in the winch assembly have elastic properties, then Hooke’s law can be applied in calculating the uniaxial stress and strain. In this case, the stress and strain are in three dimensional state if the material is isotropic and homogeneous as below.
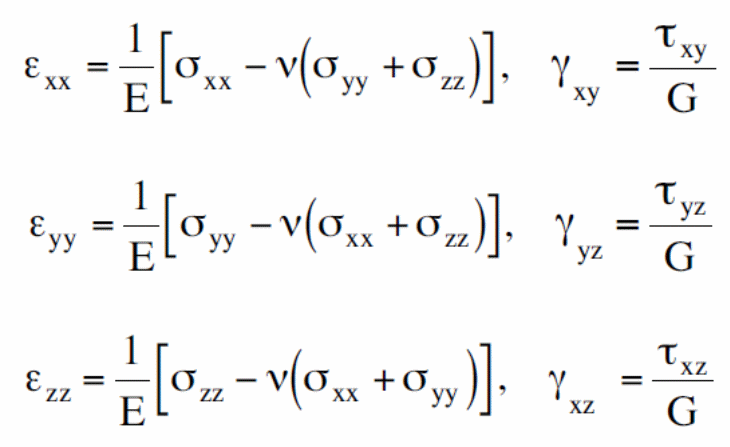
If the Young’s modulus, the shear modulus, and Poisson’s ratio in the equations are represented by E, G and V, respectively, then, equation provided below holds.
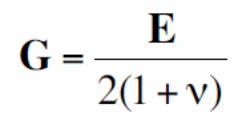
Once the theoretical approach of stress analysis has been discussed above, it is critical for the design process to integrate a method that is easily available to yield stress analysis values that can be used to calculate the safe working values for the winch in this study. While the above study provides theoretical stress analysis as the basis for this study, the following provides stress analysis for different classes of stress for different load and speed conditions (Purohit & Purohit, 2006).
Theoretically, the bending stress is given by, σ = Mc/I
The maximum stress the drive shaft can be subjected to can be tested by applying a bending force of 1600 N-m, by calculating the tensile and comprehensive tensile bending stresses As shown below:
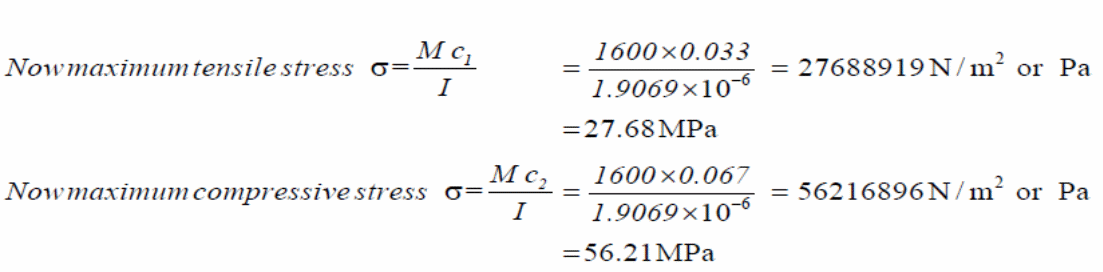
Winch Maintenance
Once a winch has been released into the market, it is subjected to different forces, torque and other load and working conditions. In this case, a winch has to be handled carefully through by following through maintenance procedures to increase the lifespan of the component when in use and when not in use. It is critical for the user to identify and be aware of the entire component assembly that makes the winch. In addition, the maintenance of a winch is pegged on the materials used to make each of the components, the equipment conditions, and manual references provided by the manufacturer. The general maintenance guidelines includes identifying ad removing all power controls, removing all assembled and removable parts of the winch. Each of the parts is then examined against the specifications provided on the manual provided by the manufacturer. Each of the components to inspect for wear include the drum, sealing surface, ring gears, worm gears, screws, and other removable and replaceable parts of the winch assembly. Any part identified to have been worn beyond the specifications and allowable tolerances by the manufacturer is replaced with a new part. It is important to ensure that when assembling the winch, all precautions are followed to ensure the assembly is fixed correctly to avoid any misalignments (Product information 401, 1994).
Recommended Operating Practices
Once a winch has been designed and manufactured, it is important to provide documentation about standard operating procedures. That is in addition to ensuring proper inspection of the winches. The process begins with proper section procedures as follows:
It is important to select a winch suitable for the type of work and the winch should be evaluated for proper strength for use in the area of application. It is important also to identify the working load limit for the winch, with all warnings and instructions carefully read and understood. It is important to ensure that the winch is not overloaded while in use, but is loaded with appropriate and recommended loading conditions. In addition, winches should be attached to the area of use following the appropriate installation procedure to optimize winch life and usage.
It is important to avoid using less than 2 wraps which are possibly able to result in strap slippage, excessive warping of the mandrel, excessive webbing of the mandrel, and the possibility of reducing the working load limit of the winch. To ensure the bracket used does not bend when assembling the winch, it is important to ensure that the screws given a snug tightness, because in the event of weak tightening, the winch might fail. A winch should be used in the appropriate area of application depending on the requirements or recommendations while avoiding being applied in areas not recommended for use only.
Inspection should be carried regularly by designated personnel to ensure the correct winch is used correctly. Inspection should be based on the frequency of usage, the nature and severity of conditions being used, and previous experience by other users of winches. Regular inspections provide the basis for lengthening the life of the winch because faulty components can be identified and replaced, and other components that require maintenance can be identified in advance. In addition, any required lubrication and regularly lubricating the moving parts adds further life to the machine.
References
Danny,L. B. T., 2005. Am16 Improvement in the Design of Winches. Web.
Product information 401, (1994). Bearing failures and their causes. Palmeblads Tryckeri AB
Purohit, R. K., & Purohit, K. (2006). Dynamic analysis of ball bearings with effect of preload And number of balls. Int. J. of Applied Mechanics and Engineering, vol.11, No.1, pp.77-91
NTN. (1997). Ball and Roller Bearings. NTN corporation. Web.