- Introduction
- Diffusion
- The unit of the diffusion coefficient is cm2/second
- Diffusion in polymers
- Diffusion of thermosetting polymers
- Resol type Phenolic Resins
- The diffusion mechanism of phenolic (resol) polymer during curing process
- Factors that affect the water reduction
- Effect of temperature
- Reference List
Introduction
Diffusion is the movement of atoms or molecules from one place to another randomly. Molecules diffuse from a region of high concentration to a region of low concentration. The process of diffusion occurs in solids, liquids, and gases. It helps in all living as well as non-living systems. Diffusion helps the systems to reach an equilibrium state because diffusion takes place between two systems till the concentration of two regions becomes equal.
Fick’s equation is used to prove the diffusion theory. The diffusion process occurs in polymers also. The diffusion in polymers is usually at a slow rate because cross-links present in the polymers reduce diffusion. The polymer is a complex substance that contains a number of cross-linked chains in them. The rate of diffusion in a polymer depends on the chain length or size of the polymer. Thermosetting polymers are a class of polymers that are formed by the reaction of phenol and formaldehyde. The diffusion in this polymer also depends on the cross-links present in them. Also, smaller molecules can diffuse faster through a polymer than larger molecules.
The main aim of phenolic curing is to reduce the content of water in them. During the process of phenolic curing, there is a substantial reduction of the water content. Several factors contribute to water reduction. The phenolic curing process also takes into account the temperature, the size of the samples etc. It is explained in the following sections.
Diffusion
Diffusion is the process of movement of atoms from higher concentration region to lower concentration region.
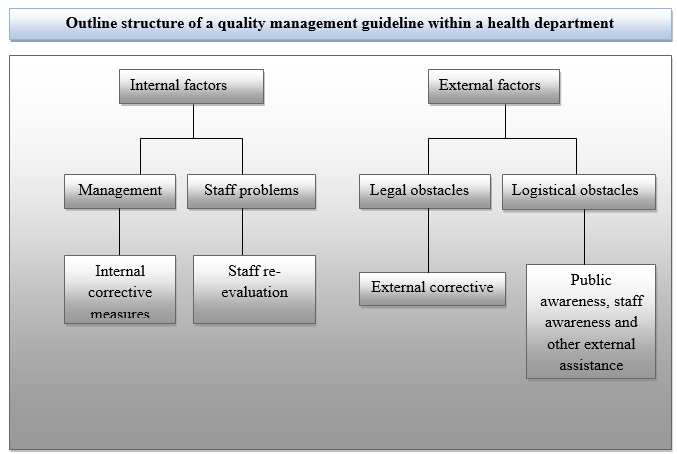
In this figure, at first, the extracellular space is the higher concentration region whereas the intracellular space is empty. The movement of atoms can take place depending upon the concentration gradient. Therefore, atoms of the higher concentration region tend to move to the lower concentration region. Hence, diffusion takes place. That is, the atoms at the extracellular space start to move to the intracellular space, finally, a concentration at both sides of the membrane becomes equal and the process of diffusion stops.
It can determine the physical and mechanical properties of the substances. The diffusion coefficient is the main term used in the diffusion process, which is a temperature-dependent one. The diffusion coefficient is “a factor of proportionality representing the amount of substance diffusing across a unit area through a unit concentration gradient in unit time.” (Diffusion coefficient 1989).
The unit of the diffusion coefficient is cm2/second
The diffusion coefficient gives an idea about the rate of diffusion, which is mainly dependent on the temperature and the energy required to start the diffusion process. The diffusion coefficient is also known as diffusivity. For the occurring of diffusion, some sort of external energy is needed. The external energy used in the diffusion process is mainly heat. The diffusion process occurs in solids, liquids and gases.
The diffusion process in gases and liquids is simpler because these atoms are loosely packed. There are different types of diffusion mechanisms. Some of them are Vacancy diffusion, interstitial diffusion, exchange, ring, Interstitialcy etc. Vacancy diffusion means atoms in one lattice site move to a vacancy site and another new vacancy site is formed. Interstitial diffusion means the diffusion of atoms from one interstitial site to another.
The vacancy is not an essential requirement for such a type of diffusion. Interstitial means the movement of atoms from the lattice site to interstitial sites. To move an atom from one location to another, external energy is required which is known as activation energy. At first, atoms in a molecular have some stable energy. To move an atom from one location to another it can acquire energy which is the activation energy denoted by Q. We have to supply energy that must always be greater than Q. Only then, diffusion of atoms in a molecule occurs. The activation energy of vacancy diffusion is high compared to interstitial diffusion.
The diffusion coefficient is calculated by using the equation,
D=D0 exp (-Q/RT)
Where,
Q is the activation energy, the unit is joule/mole
R is the universal gas constant, and its value is 8.314J/mole/Kelvin
T is the absolute temperature, and its unit is Kelvin
D0 is constant for a given system.
The activation energy Q and coefficient Do are obtained from a plot of the natural log of D vs. 1/RT called an Arrhenius plot.
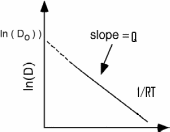
The figure shows the Arrhenius plot of diffusion constant. The slope of this graph gives the activation energy Q. The temperature and diffusion coefficients of the system are directly proportional. That is, when temperature increases the rate of diffusion increases and when the temperature applied is less, the rate of diffusion is also less. But the above equation reveals that a very small amount of thermal energy is needed to overcome the energy barrier.
Activation energy is generally high in tightly packed systems when compared to open crystal structures. Flux is an important term used in diffusion in solid. Flux is the rate at which the atom is diffused through a plane of unit area per unit time. The law connected to the general diffusion process such as the mass transfer phenomenon is Fick’s first and second law. The net distributions of materials are in response to the concentration gradient. The movement of atoms reduces the size of the gradient. The motion of atoms within a substance is random. Fick’s first and second laws are generally considered as the basic law of diffusion.
Fick’s first law is derived by Adolf Fick which gives “a relationship wherein the flux of a diffusing species is proportional to the concentration gradient:
Where
Jx = the flux of the diffusing species.
dC/dx = the incremental change in concentration with distance.
D = diffusivity or diffusion coefficient = the proportionality constant.” (Fick’s first law of diffusion 2009).
The negative sign of the equation shows that the impurities are flowing from the higher concentration region to the lower concentration region. By using Fick’s first law, the Rate of Diffusion is the ratio of the difference in concentration and the thickness of the wall, where the diffusion between two spaces takes place. Fick’s first law generally a steady-state representation provided a condition, the volume of diffusion is constant, and it is not altered concerning time. According to this law, the rate of diffusion increases with the difference between the high concentration and the low thickness. That is, the rate of diffusion is directly proportional to the concentration gradient. This equation is mainly used in transfer procedures in biopolymers.
Fick’s second law, which is also known as diffusion equation which “states that for a constant diffusivity D, the rate of change in concentration with time, is proportional to the rate at which the concentration gradient changes with distance in a given direction.
i.e.
For cases in which D does vary with concentration, we must use the more general form:
(Fick’s second law of diffusion n.d.).
Fick’s second law is derived from his first law of diffusion. This equation is generally represented in non-steady-state conditions and the volume of diffusion changes for time. By using Fick’s second law of diffusion, we have to calculate the concentration at any position by considering the time and the position of mass flow. Here also, impurities are flowing from higher concentration region to lower concentration region. Fick’s second law is applicable mainly in the case of the moisture absorption process in wood fibre/polymer-based composites. The flow rate is found out using Fick’s second law of diffusion by considering different temperature values.
Diffusion in polymers
Diffusion of polymers arises mostly in the amorphous region than the crystalline region as the amorphous polymers are simpler because of their low range of molecules. The movement of atoms can take place depending upon the concentration gradient. That means diffusion occurs from the high concentration region to the lower concentration region. There are gas, liquid, water and vapour diffusion of polymers as well as multi-component diffusion.
The diffusion between linear polymers is explained with the help of the Reptation model. According to this model, during the early stages of diffusion, the process is based on some discrete power laws. This model explains that “The molecule is described as sliding or ‘reptating’ through a ‘tube’ whose contours are defined by the locus of entanglements with neighbouring molecules” (Polymer diffusion n.d.).
The time taken for the diffusion of a polymer chain from a tube is called reptation time and motions inside the tube take place according to the time dependencies. The diffusion inside the tube is measured with the help of diffusion coefficient denoted by D, length of the polymer chain, degree of polymerization denoted by N and the polymer architecture. The interdiffusion among the polymers in an interface takes place in two steps.
The first stage of interdiffusion takes place at a time lesser than the reptation time, t r and due to the surrounded tube, the parts of the chain cannot cross the interface. The polymers which are produced from the entanglements with other chains recline on the same part of the interface. The tangled polymers will be excellent only if the existence of chain-end at the interface at an early phase, that is, the diffusion of the polymer should occur at a lesser time than the reptation time.
The movement of the chain traverses the interface (t < t r), then the width of the interfacial raises by t¼. When the polymer chain reflects at the interface the huge density of the chain will finish close to the surface. Then the next stage of the interdiffusion takes place at a greater time than the reptation time. The Phenomenological models for experimenting with the diffusion of polymers is done by a logical method in which less computer process is used. Like the other models, it will not predict the diffusion of polymer which gives only some information based on the diffusion of polymers. There are many methods in Phenomenological models for doing the analytical functions.
In the Series of Activated jumps method, “the diffusive process is represented as a sequence of activated hopping motions; a specific molecular mechanism is assumed, and the resulting transition dynamics are calculated.” (Chapter 5 methods for studying diffusion in polymers n.d., p.3).
This model includes potential energy along with a diffusion path and Molecular dynamics methods. Potential energy along a diffusion path is the calculation of diffusion of polymers from the potential energy. This is done through computer calculation to compute the sensible potential energy and to produce the real structure of the polymer. A molecular dynamics method is done to predict the diffusion of polymers for the melts. It is the easiest and rapid way of experimentation.
Diffusion of thermosetting polymers
The phenolic polymers were discovered decades ago. Phenolic resin has a carbon cross-linked network. This carbon network is covalently bound which contributes to its thermal stability. It is responsible for the physical properties of the phenolic resin. Phenolic polymers are a type of thermosetting polymer. They are prepared from phenol and formaldehyde. Therefore, they are also known as phenol-formaldehyde resins. Phenolic resins are considered the most important thermosetting polymers.
Phenolic resins are used to form nanocomposites which are used to produce hybrid composites. The diffusion process occurs in the phenolic polymers while it is being post-cured. The catalyst is added along with the phenolic polymers during the process of impregnation. By adding catalysts into phenolic polymers, the conductive nature of the substance may change. “Thermosetting polymers have a network structure and are formed by the ‘condensation polymerisation’ process which produces water as a by-product of the chemical reaction occurring during setting.” (Engineering studies 2003). Thermosetting polymers have chemical bonds between them.
They are connected by these bonds. Condensation of phenol and formaldehyde will lead to the formation of both linear polymers as well as cross-linked polymers. The ortho and para directing nature of phenol help it to give different polymers on reaction with formaldehyde. The linear polymer formed by the reaction is novolac. Bakelite which is an example of a thermosetting polymer is formed when novolac is slightly warmed with hexamethylenetetramine. In thermosetting, the polymer network is interconnected irregularly through primary bonds. Thermosetting polymers are used in a variety of ways. They can be used as an insulating material for preparing electrical appliances etc. Their chemical structure contains a repeating unit. On heating, these polymers become rigid and infusible.
Their preparation is usually done from semi-fluid materials whose molecular mass is low. The heating of these substances creates too much cross-linking between their chains. This results in the formation of a three-dimensional network and a non-fusible and insoluble substance are produced. On melting, a permanent change occurs on the thermosetting polymer. This becomes a solid which cannot be changed back into a liquid. A thermosetting polymer is a condensation polymer because it is formed by the condensation reaction of two monomers.
Diffusion in any material causes the movement of atoms in it. The diffusion through a material will be characterized by many features. The diffusion of thermosetting polymers mainly depends on the cross-links between the chains. Thermosetting plastics will contain several cross-link chains in them. The cross-linking in the thermosetting polymers is the reason for its rigidity. The intermolecular interaction usually reduces the chain movement.
The length or size of the polymer chain affects the diffusion in polymers. The diffusion through thermosetting polymers is difficult because the chains in them remain twisted with each other, and therefore, it becomes difficult for the movement of molecules. The diffusion occurs mainly through amorphous regions of the polymer rather than through the crystalline regions. This is because the crystalline regions do not allow all the particles to pass through it. The measurement of diffusion depends on the structure of the thermosetting polymer. If the cross-links in the polymer are more, the diffusion will be less because it will be difficult for diffusion through the cross-links. So, diffusion will occur quickly if the numbers of cross-links are less.
Diffusion of smaller particles occurs faster than larger ones and also it occurs quickly through the open areas in the polymer. The movement of molecules can be increased by the application of some voltage or any external forces. So, the application of voltage or any other external force increases the diffusion rate. The rate of diffusion will be more at high temperatures. But, if the rate of diffusion is tried to increase by applying heat and pressure, it causes defects in the material.
This type of diffusion thus can cause harm to the polymer. The properties of thermosetting polymers at large temperatures depend on diffusion. The diffusion normally takes place below the glass transition temperature. The diffusion of the molecules in a thermosetting polymer differs from crystal atoms. The polymer structure is usually very complex. This complex structure enables diffusion only at a small rate because the complex structure is made of chains which will reduce the diffusion process. So, the movement of molecules in a phenolic polymer is very less compared to other molecules. Also, such materials can only be used below 100 degrees Celsius.
The diffusion of phenolic polymers will, therefore, be very negligible. The strong molecules in the thermosetting polymer cause less diffusion. But smaller molecules can diffuse through a polymer very easily. The diffusion in thermoset will be comparatively easy because it has an open network polymeric structure. It will depend on the size of the diffusing molecule and also on the size of the network spaces. As the cross-links in the polymer increase, the gap in the network decreases. This will cause smaller molecules to diffuse through the network. These small molecules can easily pass through the gaps between the network structures. The movement of the chains in the polymer depends on the chain length.
Chain length is important in the diffusion process of thermosetting polymer. The increase in the length of the chain reduces the chain motion and causes an increase in strength and makes it hard. It also causes an increase in the glass transition temperature. This is caused due to the interactions like Vander Waals interaction. These interactions are caused due to the force of attraction between the molecules. Such interactions will make the chains stay in position strongly and they remain attracted to each other. It will also prevent any breaking between them. The diffusion through a material depends on how fast the molecules pass through the polymer.
If the molecules move very rapidly, the diffusion rate is high and if the movement of molecules is less the diffusion rate is low. The diffusion of molecules will be less below the glass transition temperature. It increases above the glass transition temperature because in this temperature there is more free volume, and the movement is more. There is more space for the movement of molecules in this temperature range. When there is more space, the movement of molecules becomes faster i.e., the rate of diffusion increases. Very small molecules of liquid and gas are usually thought to penetrate through a polymer rather than to diffuse through it.
Small molecules diffuse faster through the polymer because the polymer contains open spaces that are very small. Thus, it will be easy for small molecules to pass through these small spaces. These spaces, therefore, enhance the rate of diffusion in the polymers. In thermosetting polymers, the diffusion depends on the concentration gradient. Diffusion takes place from a region of high concentration to a region of lower concentration just like any other material. Due to the cross-linking in thermosetting polymers, it can attain high-temperature stability.
Resol type Phenolic Resins
The resins used in the curing process are always the resol type phenolic compounds. In the rubber industry, resol type phenolic resins are used to cure the various products of rubber so that the characteristic of high heat resistance is attained. The resols are produced by the reaction of the phenols with the aldehyde compounds under standard conditions in the presence of an alkaline catalyst. Phencat 382 is a good catalyst that can be used in phenolic resin curing. ELO is a good plasticizer that can be used to improve some of the mechanical properties of the resin. It helps in reducing the density of cross-linking. The factor noticed in that reaction is that the resol products are having a lower molar ratio than the reactants. The bye products of the reaction include only a very small quantity of the reactants.
The percentage of non-volatile components in the product mix is between 70 and 90. The viscosity identified is up to a maximum of 10000. The ph factor of the end product is calculated around the range of 6.8 to 7.2. The reacting temperature is always kept below 100 degrees centigrade at which the reacting time is identified to be about 3 hours. There are two types of resol type phenolic resins namely: Condensation type and Benzylic Ether type.
The major property identified in the case of resol type phenolic compounds is their thermo reactivity. The Thermo reactive materials are always inactive at normal temperatures and will become active and undergo various chemical reactions at abnormal temperature conditions. The quantity of curing resin used depends on the requirement of the application. The resol type phenolic resins have the curing capacity of their own, but it may be desirable at times to add a small helpful amount of additional chemicals like halogens. Halogens act as donors when used along with the resol type phenolic resins thereby helping them to achieve the necessary percentage of curing.
The applications of resol-type phenolic resins were identified in the field of adhesives. The alkaline conditions with a temperature higher than 100 degrees catalyse the pre condensation process which is succeeded by the curing action which itself is a self-condensation reaction. The condensation reactions of the resol type compounds result in the end products called modified phenolic resins if the reacting mixture contains some starting products. “The modification brings about a fundamental improvement incompatibility with other binders.” (Stoye, Freitag & Beuschel 1996, p.148). The modifications can be done in various methods including physical modifications like amalgamation, curing with different chemicals, etherification and various other chemical reactions.
The diffusion mechanism of phenolic (resol) polymer during curing process
Phenolic resin is the oldest synthetic polymer that needs high temperature and high pressure for the curing process. There are two types of phenolic resin – resole phenolic resin and novolac phenolic resin. Scanning calorimetry is one of the methods used to find the curing behaviour of the resol phenolic resins. And the curing behaviour is identified by analyzing the structure of the phenolic resin. Moreover, the reaction mechanism is detected by the dependence of activation energy.
The curing mechanism of core phenolic resin and face phenolic resin will be dissimilar because the curing of the core phenolic resin is quicker than the face phenolic resin. Water plays a main role in the curing process. In the preliminary stages of the curing process, water will dilute the system and delay the curing reaction and during the higher level of conversion, water will reduce the cause of diffusion on the curing reaction to complete the curing reaction.
Resol type phenolic resins are prepared by using different layered silicates like sodium montmorillonite and ω-amino acid modified montmorillonites. The hydrophilic MMT is widely used for phenolic resin curing. The hydrophilicity of phenolic resin is present due to methylol groups. Phenolic resins lose hydrophilicity by eliminating methylol groups. Due to this curing process, the water content present in the phenolic polymer reduces. ω-amino acid modified montmorillonites like C6M is used for the entire stage of phenolic resin curing.
The reaction product of these two has excellent mechanical properties because of the end-tethered structure produced by the reaction among the carboxylic acid of C6M and the methylol group of phenolic resin. The excellent dispersion of silicate layers is also caused for the best mechanical property of the reaction product. The dissolution of phenolic polymers is observed through a new term called the average degree of ionization. It will determine the rate of dissolution rather than the diffusion rate. The phenolic polymer dissolution rate in an aqueous base is considered as the main basis for the functioning of the photoresist materials.
When a difunctional group and a trifunctional group are reacted together, a network structure results. Phenol formaldehyde resin is one example of this type.
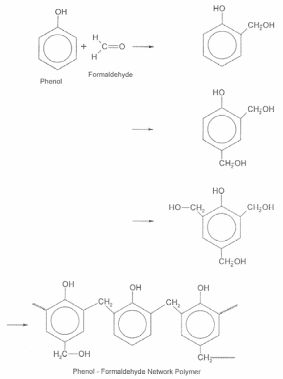
For the best extraction of phenolic compounds various studies are conducted. During these studies, we can find out the effective diffusion rate and mass transfer coefficient for better diffusivity. These values are calculated during the solid-liquid extraction process. The extraction of phenolic compounds can be done by using surface response methodology. These methods are carried out by considering the amount of ethyl alcohol or concentration of sulphured water, respective temperature, the ratio of solvent and the solid in the curing process.
Factors that affect the water reduction
Water is an important diluting agent in phenolic resins. It helps in reducing the viscosity of the resin. During the curing process, there is the evaporation of water from resin. This may sometimes cause voids in the resin which is formed after curing. Sometimes the physical properties are affected by these voids. Some evolution of water takes place in the curing process.
To study the curing nature of the core resin and face resin, Differential Scanning Calorimetry (DSC) is applied. The characteristic of these two resins is differentiated by their activation energy, peak temperature, and peak shape. The result of the wood on the curing process will speed up the rate of addition reaction of the core resin and face resin. The high pH value of the resins leads to the formation of two peaks in the DSC curves.
When the value of the pH lessens the two peaks in the DSC curves combines or overlaps. By adding wood in the curing of the face and core resin leads to a decrease in the activation energy by reducing the pH value of these two curing systems. The colour of the phenolic resin will alter over time which has a high degree of transparency, luminousness and stability as it is very tough and stiff. The phenolic resins include a small quantity of water to make the ultimate resin transparent to control the water at a correct level. If the water in phenolic resin rises it will result in opaque. The cure rate of phenol-aldehyde resins is increased by the combined use of cyclic carbonate and amine and also by the use of a resorcinol source.
The effect of catalyst is the main factor while considering the diffusion process of phenolic polymers. The catalyst is added along with the phenolic polymers during the process of impregnation. By adding catalysts into phenolic polymers, the conductive nature of the substance may change. Resol type phenolic resin is used for adhesion, moulding, lamination, binder for inorganic aggregate etc. The curing of resol type phenolic resin can be done at low temperature also, with the help of curing accelerators which requires a small number of additives. An example of these compositions is resol-type phenol resin, an alkali earth metal oxide and/or an alkali earth metal hydroxide, and a salt.
The curing of the above phenolic resin takes place at a temperature of 10 to 110° C. The examples of the alkali earth metal oxide and alkali earth metal hydroxide are magnesium oxide, calcium hydroxide, barium hydroxide, etc and a salt of a sulphur atom-containing oxoacid and a nitrogen atom-containing base like ammonium thiosulfate. This will act as an accelerator for the curing process. The alkali earth metal oxide and alkali earth metal hydroxide act in this process as a catalyst. Both alkali metal hydroxides and alkaline earth metal hydroxides accelerate the curing of resol. These two are used in this process for activating the curing accelerators.
The barium hydroxides acceleration effect is the maximum. The curing process of resol depends upon the relationship between the type of catalyst and the speed of accelerating effect. That is, the larger ionic radius of the catalyst increases the rate of curing of the phenolic resin. The cure acceleration effect of barium hydroxide is the largest. The curing speed of resol type phenolic resin increases when we add catalysts like sodium hydroxide or barium hydroxide.
The activation energy of the resol cures when we add these catalysts are approximately in the range 17.0-21.3 kcal/mol. Some examples of the conductive substances are carbonaceous milled fibres, carbon black, acetylene black, isotropic graphite powder, and the like. The adding of catalyst is based on some quantity. That is, we have to add catalysts only ten percentages of the total phenolic resins. The usage of the catalyst may cause some disadvantages to the product.
The main disadvantage is that by adding catalyst having conductive nature, its conductivity improves to some extent which may lead to an increase in the price. When we add a lot of catalysts, the condensation time of phenolic polymers will be reduced. The usage of the catalyst may vary several properties of the composite. Sometimes the catalyst progresses the flexibility of the composite. The usage of catalysts also helps to improve the flexibility of the phenolic resins.
The phenolic resins such as biphenyl epoxy (4, 4-diglycidyloxy-3, 3, 5,5-tetramethyl biphenyl) and dicyclopentadiene type are observed by adding several catalysts and the performance of each of the catalysts is observed at constant temperature conditions. According to Chern and Poehlein, we can combine the diffusion factor and the nth-order kinetic model or an auto-catalytic model. By doing this, we can predict the cure kinetics of each catalytic system along with the entire range of conversion. The phenolic resin has been alienated into various groups like moulding resin, laminating resin, casting resin and so on.
The phenolic polymers undergo various phases while it is being post cured and the post-curing temperature affects the diffusion process of phenolic polymers in several ways. Polymer is a long chain made of many molecules. That means it is a combination of small molecules known as monomers.
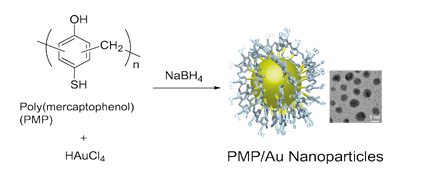
Post cure temperature is more significant than heat duration on the level of phenolic resin cure. The process of preparation of phenolic resin is depending upon the post-curing temperature. That means the resin curing is connected linearly to the post-curing temperature. That is when post-curing temperature increases the extent of cure also increases. “This paper examined the influence of post-cure temperature on the amount of unreacted monomer remaining in a commercial light-cured resin composite restoration following initial light-curing and subsequent post-cure.” (Bagis 2009).
Post curing of phenolic resins is done at 160 degrees Celsius, 230 degrees Celsius and 300 degrees Celsius and it is then carbonized up to 1500 degrees Celsius. The post-curing is done to improve the physical properties of the resin. This process encourages the cross-linking reaction and also causes the evolution of gases. There will be a considerable amount of weight loss in the post-curing process. If post-curing is done at a higher temperature of about 300 degrees Celsius, there will be more loss of weight, low density etc than the other samples. Post curing process also leads to condensation reaction which will help in the forming of long chains, cross-linked chains etc. The density of post-cured samples will have a higher density than not post-cured samples.
Phenolic polymers are synthetic materials that can easily acquire high-temperature stability due to the cross-linking process during manufacturing. It is necessary to consider the thermal and mechanical properties for the high-quality application of phenolic resins. The post-cure process is differentiated by its weight loss. Various studies are conducted to analyze the effect of post-curing temperature on the phenolic polymer diffusion process.
Other types of phenolic resins are Phenol formaldehyde resins. They are prepared by using phenol and formaldehyde in the molar ratios 1.2 and 1.8. Phenol to formaldehyde molar ratio is denoted by FP. The succeeding slashing of ethers in the 1.8 system may lead them more complex compared to FP=1.2 systems.
“The structural changes in each resole after heating was observed by 13C CP-MAS NMR up to 500°C, and their surface areas after carbonization at 1000°C were measured using N2 and CO2 gas adsorption. The FP=1.2 material was found to possess narrower micropores than the FP=1.8 material. These results are significant for those industries where the high-temperature behaviour of phenol-formaldehyde materials is important.” (Lenghaus, Qiao & Solomon 2001).
Effect of temperature
When the curing temperature increases, it will lead to speed up the reaction.
The phenolic resins require temperatures above 10°C for their curing. Then the phenol-formaldehyde resins are post-cured at a certain temperature and their samples are carbonized. This increases the mechanical property of the phenolic resin. The increase in temperature and time will lead to the reduction of the contraction of phenolic resins during carbonization. Due to the post-curing in phenolic resins, its weight will lose to a great amount, then there is an increase in the contraction and lesser density of the sample.
The phenolic polymers undergo various phases while they are being post cured and the post-curing temperature affects the diffusion process of phenolic polymers in several ways. Phenolic resin requires a certain temperature for the curing process. Post cure temperature is more significant than heat duration on the level of phenolic resin cure. The process of preparation of phenolic resin is depending upon the post-curing temperature. That means the resin curing is connected linearly to the post-curing temperature. That is when the post-curing temperature rises, the rate of curing also increases. At temperatures below 130° F curing does not occur.
Temperature above 200° F. (95° C.) favours curing. But the process is slow. Therefore, the setting of resins requires a long time. The thermal stability is depending on the structure of the curing agents. The temperature required for the extraction process will affect the rate, time and diffusivity of the extraction. If the temperature required for extraction is increased, it leads to an increase in the extraction rate. The increase in diffusivity may cause a decrease in extraction time. If the concentration of sulphuric acid is more in the solvent mixture, diffusivity increases up to the maximum level and decreases when we add additional ethyl alcohol in the reaction mixture.
To identify the limitation of diffusion in the processing of thermosetting polymers, various methods are used. The main thing to identify the limitation of the diffusion is that first, we have to find out the average diffusion coefficient of the molecular species in the curing systems. The diffusion coefficient is an important term while considering the diffusion process. The method is in connection with mobility-related properties like ionic conductivity and dipole relaxation time. That means Dielectric measurement is considered as the main factor.
But various studies regarding the diffusion process in thermosetting polymers reveal that ionic conductivity is the dominant factor in the diffusion model at the first stage of the diffusion process whereas the dipole relaxation time is considered as an important factor at the postal stage of the diffusion process of polymers. These studies give an idea about the structural property relationships in thermosetting polymer systems.
Reference List
Bagis, Y 2009, “The effect of post-cure heating on residual, unreacted monomer in a commercial resin composite: Abstract: definition”, Dental Material, vol.16, no.4, p.244-247, Elsevier. Web.
Chapter 5 methods for studying diffusion in polymers: series of activated jumps n.d. Web.
Diffusion coefficient: definition 1989, About.com: Composites/Plastics. Web.
Dominquez, JC, Alonso, MV, Oliet, M & Rodriguez, F 2009, “Chemorheological study of the curing kinetics of a phenolic resole resin gelled: Graphical abstract”, European Polymer Journal, Science Direct. Web.
Engineering studies: polymer structures 2003, NSW HSC Online. Web.
Fick’s first law of diffusion: definition 2009, About.com: Composites/Plastics. Web.
Fick’s second law of diffusion n.d. Web.
Lenghaus, K, Qiao, GG & Solomon, DH 2001, “The effect formaldehyde to phenol ratio on the curing and carbonization behaviour of resole resins: abstract”, Polymer, vol.42, no.8, p.3355-3362, Science Direct. Web.
Ogoshi, T, Umeda, K, Yamagishi & Nakamoto, Y 2008, “Synthesis of phenolic polymer-coated gold nanoparticles”, Polymer Journal, vol.40, no.10. Web.
Phenol- formaldehyde network polymer n.d. Web.
Polymer diffusion n.d., Oxford material: Polymer and Bio-Material Group. Web.
Stoye, D, Freitag, W & Beuschel, G 1996, Resins for coatings: chemistry, properties, and applications: modified phenolic resins, Hanser Verlag.