A brief explanation of air to fuel ratio
The air-fuel ratio is the volume ratio of air to fuel available in an internal combustion engine of cars or industrial furnaces (Martins, 2012). The stoichiometric mixture ratio (stoic) results from an adequate supply of air to ensure the total combustion of all the fuel in the system. The exact air to fuel ratio (AFR) may be determined by specifying the content of the oxygen in the combustion system and accounting for possible water vapor dilution and any oxygen additions. The ratio is critical for evaluating anti-pollution and engine performance. Usually, richer mixtures have lower AFR. AFR asserts that “for every unit by mass of gasoline, 14.7 units by mass of air must also be present in the combustion chamber during ignition” (Martins, 2012).
In the air-fuel ratio control system for car engines, the engine may operate at a given condition like deceleration and acceleration. The stoich controls the air to fuel ratio in the combustion system. A termination of specified conditions causes the AFR to change from the stoich to a lower ratio. A lower ratio offers the best fuel consumption. This may be changed by specifying the preferred operating conditions for the combustion engine. Any specified operating conditions result in an immediate change from the optimum fuel consumption. A specified period may also control change in optimum fuel consumption and stoich.
Why do we need feedback control?
With effective feedback, one may be able to control events. The fundamental concept in feedback control is that some physical quantities and events require control in a manner that ensures that such activities take on the specified conditions and values. In some cases, the conditions may even assume some pre-determined values during an operation (Mastascusa, n.d).
A feedback control system provides an opportunity to control quantities and determine what may be done. In other words, a feedback control system ensures the effective implementation of any devised concept. For instance, Dubois Van Til, and Zorka (1996) considered the application of the digital feedback control to an automobile engine Air-Fuel (A/F) ratio system in order to develop an inexpensive digital controller, which relied on the existing HEGO sensor. Such a system would enhance efficiency by improving performance, eliminating expensive sensors, and reducing costs of systems in the automotive industry.
An analogue feedback control system in the air to fuel ratio with a block diagram
The analogue control system consists of a linear amplifier (a conventional analogue device and a circuit). The conventional control systems were analogue because of the technology at the time. The analogue feedback system allows for immediate detection of any changes and the amplifier adjusts the changes to the required outputs.
Designs of analogue feedback control systems differ. Generally, they include operational amplifier and other analogue components, which ensure effective integration of control systems and feedback loop.
The analogue system shown in figure 1 consists of the following:
- A throttle angle signal;
- An analogue controller;
- The controlled plant;
- A feedback signal;
- Subtracter for voltage comparison (Martins, 2012).
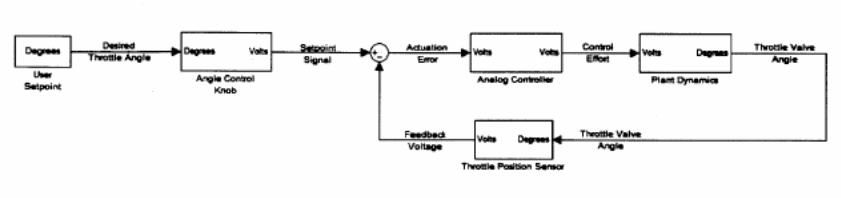
In this case, the designer used a potentiometer to act as a voltage divider with a knob that that worked like the preferred throttle angle. This stage resulted in the conversion signals to voltage.
The potentiometer and the sensing range of the throttle had a similar voltage dividing range to ensure that any turn of the potentiometer would correspond to movements (wide or closed) in both directions.
It was also imperative to note that both the operational voltage range and the throttle position sensor match to ensure that actuation error moves to zero when the throttle achieved the preferred set point angle. This is necessary to avoid actuation error, which is not zero and to reduce any instability of the control system.
It is critical to subtract the gauged feedback signal from the input signal to allow the feedback control system to use the actuation error in effective control of the system. An operation amplifier and few resistors may be used to develop a voltage subtracter with preferred values.
The analogue feedback controller must transmit the actuation error and command signal as required to reduce system errors. A simple control system would require a proportional controller for actuation and control to allow it to function effectively. In other words, a control system can only emit signals that correspond to the error. On the contrary, when there is no actuation error, the control system cannot transmit any signal. Therefore, the analogue feedback control allows for positioning of a steady-state error. The system consists of a return spring for restoring the valve to an idle position when the drive motor system does not create any torque. The torque controls the return spring and ensures that it is at the preferred angle.
The analogue feedback control consists of an error integration unit to restrict the steady-state error and enhance valve actuation. A control effort may be used in the valve motor when the actuation error is combined in other specifications even if its zero.
The analogue Proportional-Integral (PI) controller cannot work directly with the throttle body DC motor due to higher current flows within the motor from its sensing and amplification circuit parts.
Generally, processes are analogue in nature, and such processes consume time as they move from one position to another (Kilian, 2000). Hence, the normal feedback control systems are analogue. This implies that, in most cases, the digital feedback control must first change the actual analogue signal into digital form for subsequent transmission. Conversely, any output from “a digital control system must also be changed into analogue form” (Kilian, 2000).
A digital feedback control system in air to fuel ratio with a block diagram
The digital feedback control consists of a digital circuit, which could be a computer microprocessor or microcontroller-based circuit (Kilian, 2000).
Car engines use an electronic engine control system to regulate the amount of fuel that goes into the engine (Dubois et al, 1996). This relies on the output of the sensor of the exhaust oxygen gas as elements of a feedback control system of the air to fuel ratio. Many modern cars rely on digital controllers. The design could be a discrete or continuous time model with the pole placement or PID technique (Lee and Haddad, 2002). Another technique involves a highly complex heuristic process in which conversions of output signals take place from Analogue-to-Digital (A/D) and Digital-to-Analogue (D/A). Control constraints are also evaluated in this process.
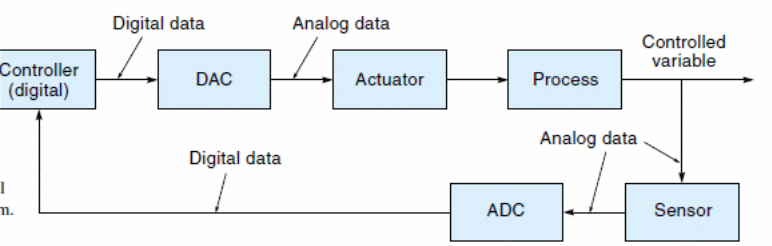
Car combustion inventions may differ. However, the common models may use two exhaust gas oxygen sensors (HEGO) to apply the digital feedback control. Both sensors are located at the upstream and downstream to provide feedback signals. A system for controlling signals from both ends is necessary.
In the digital feedback control, the major design goal is to enhance the steady-state performance of the controlled PI system. The physical AFR system may only receive signals from the HEGO sensor output and other control inputs. The digital feedback system should have high capabilities relative to the set point in order to receive the signals from the HEGO sensor.
The design of the digital feedback system must account for the value of the HEGO sensor output (Dubois et al, 1996). In addition, it must be able to recognise any changes in the output based on the pre-determined or defined operation conditions. The feedback system may also account for the values of the previous input.

Advantages of a digital feedback control
A feedback control system monitors changes that can affect a process due to constant changes in its environment. An open-loop system may allow alterations and inaccurate data to create imprecise outputs and unreliable data (Kilian, 2000). Conversely, the closed-loop system detects any alterations and strives to restore outputs in their correct forms (Kilian, 2000). Thus, a feedback control system should be sensitive to changes in processes (Kilian, 2000).
The digital feedback control can be changed to provide the desired outputs by modifying the feedback loop components. The system can partially reduce impacts of signal interference. Signal disturbance could result into inaccurate output.
References
Dubois, M. J., Van Til, R. P., and Zorka, N. G. (1996). Digital Control of an Automobile Engine Air-Fuel Ratio System. Proceedings of the 1996 IEEE International Conference on Control Applications (pp. 792-797). Dearborn, MI: IEEE. Web.
Kilian, C. T. (2000). Modern Control Technology: Components and Systems (2nd ed.). Connecticut: Delmar Thomson Learning. Web.
Lee, K-S., and Haddad, A.H. (2002). Stabilization of discrete-time quantized control systems. American Control Conference, 5, 3506 – 3511. Web.
Martins, T. V. (2012). Analog and Digital Control of an Electronic Throttle Valve. Boston: MIT Department of Mechanical Engineering. Web.
Mastascusa, E. J. (n.d). An Introduction To Control Systems. Web.