History
Wastewater is made up of different forms of components. However, the three main types of solids found in wastewater are suspended particles, colloids and dissolved molecules. To start with, suspended particles have a typical dimension of approximately 10 μm. The main types of suspended particles include sand, vegetable matter, and silts. On the other hand, colloids are much smaller in comparison with the suspended particles. Therefore, it is important to first destabilise these small and suspended particles by chemical means in order to help remove colloids from wastewater. This process is necessary as it creates heavier and larger flocks that can easily be removed through conventional physical treatment. The clarification mechanism involves coagulation, flocculation and sedimentation processes.
Coagulation helps to destabilize particles in a process that takes 20 to 30 seconds (Water Rand 1). Zahrim, Tizaoui and Hilal (2010) have observed that coagulation entails “the destabilisation of dye solutions using a coagulant(s), which can be classified into two main categories, namely, metal coagulants and polymers” (p. 624). This technique involves the addition of coagulants to wastewater to remove suspended particles. A rapid mixing process is vital in the coagulation process in order to achieve immediate and full homogenization of the coagulant. This is a spontaneous technique that ensures that destabilisation takes place as a necessary step in the flocculation process.
Flocculation, on the other hand, combines smaller particles to much larger particles in the raw/wastewater. Some of the major coagulants used include Alum: Al2 (SO4)3.14H2O, Aluminium chloride: AlCl3, Ferric chloride: FeCl3, and Ferrous sulphate: FeSO4 (Zahrim et al. 624). The flocculation process takes 10 to 30 minutes, although the maximum flocculation time varies based on the quality of raw water and the dosage used. Lastly, the sedimentation process facilitates the settling of the sediments at the bottom while clear water floats on the top. In most cases, the retention period during the sedimentation process is approximately 4-6 hours. Figure 1 below is a description of the wastewater clarification, which combines the coagulation, flocculation, and sedimentation processes.
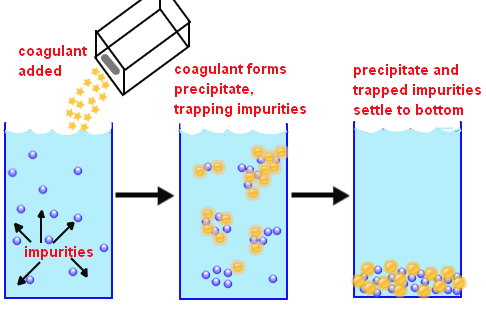
Literature Review
Characteristic of Textile wastewater
The textile industry uses large quantities of water at different stages of textile processing. Moreover, “the major speciality consumption operations are pre-treatment processes (desizing, scouring, bleaching), dyeing, printing, and finishing (Le Marechal and Križanec 34). All these processes consume very large volumes of water. Other processes that require water are “pre-treatment processes are de-sizing, scouring, bleaching, and mercerizing” (Le Marechal and Križanec 34). Table 1 below shows the average water usage and the respective process that consume the water as provided by Correia et al. (1994: 920-923)
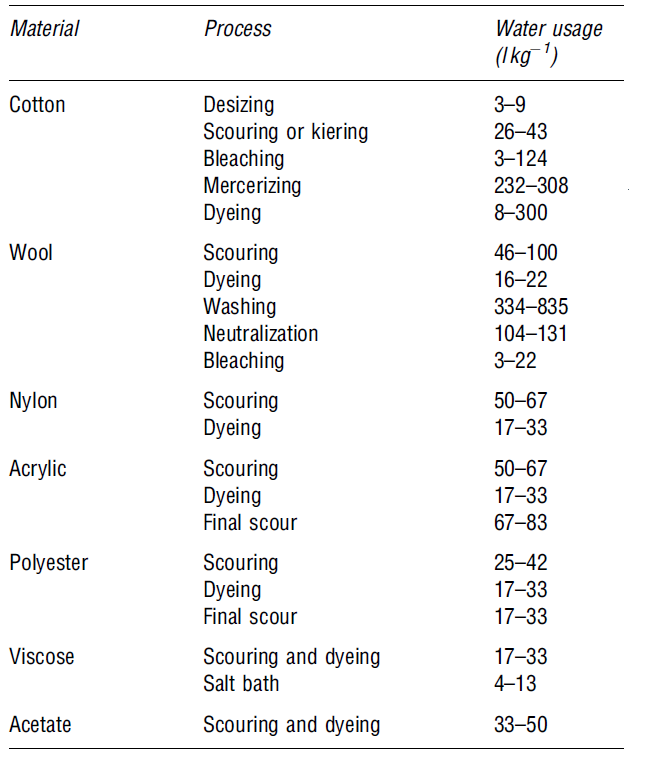
From table 1 above, most of the water is used in the printing, mercerizing, and dyeing processes.

Textile wastewater processes
There are different textile wastewater processes that are relevant to textile processing. These processes are described in the sections below.
Sizing
This is the first phase of the pre-treatment processes in which the fibres are made stronger and uniform after the removal of unwanted materials. At this stage, sizing agents such as carboxymethyl cellulose, polyvinyl alcohol (PVA) and starch are added to ensure strength and reduce breakages (Snowden-Swan1).
Desizing
This entails the removal of size-chemicals materials from used textile before weaving (Snowden-Swan 1). According to Le Marechal and Križanec, “the washing water from desizing may contain up to 70 % of the total COD in the final effluent. Synthetic esters’ oils are less problematic because they are emulsified or soluble in water and easily biodegraded “(34). The removal of chemicals depends on the size of chemicals, chemical compounds in the wastewater, and recipes used. This process is hindered by the presence of pollutants such as alkalis, surfactants, enzymes and additives (Puzyn and Mostrag-Szlichtyng 34)
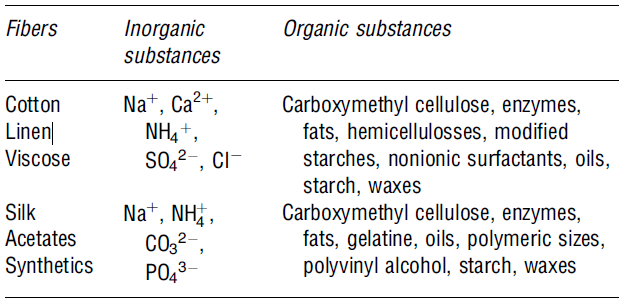
Scouring
This is the “cleaning process for removing impurities from both natural and synthetic materials” (Le Marechal et al. 34). Here, an alkali solution is added to break down natural oils, surfactants, waxes, and fats. During the scouring process, impurities are emulsified and suspended in the scouring bath (Snowden-Swan, 4). Table 4 presents some of the possible pollutants found during the scouring effluents process.
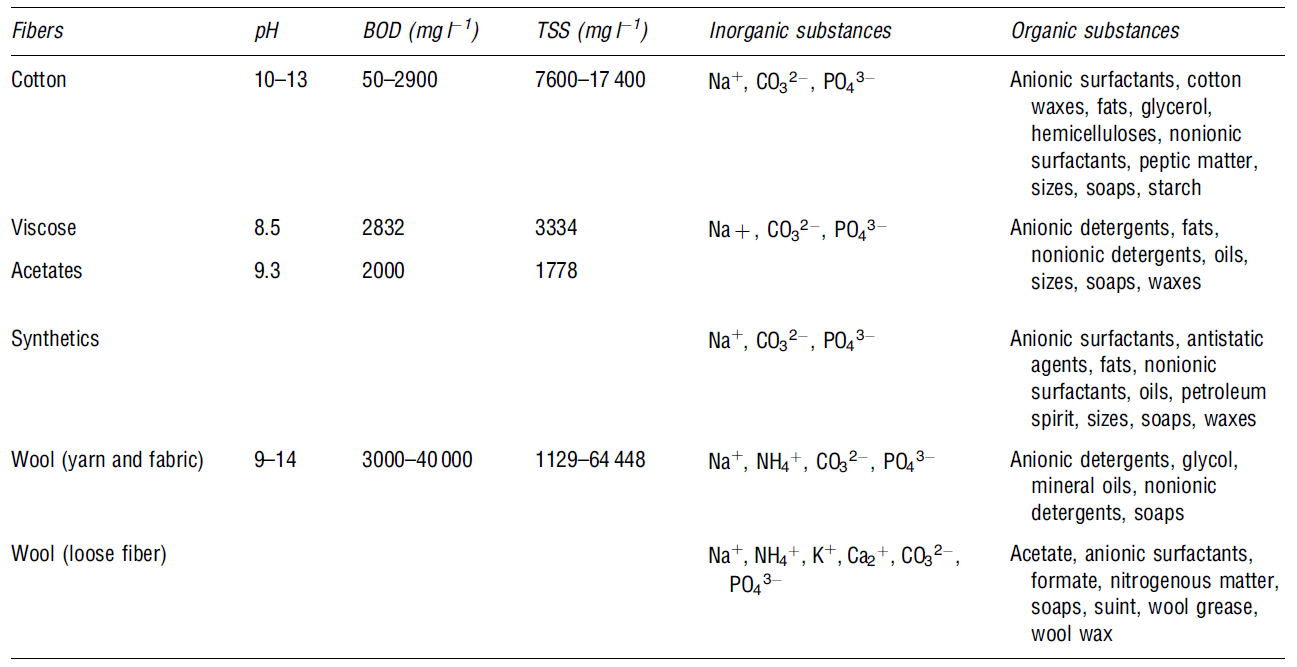
Bleaching
This is a chemical process that removes unwanted colours from the materials used. The process eliminates natural colours using chemicals like hydrogen peroxide and sodium hypochlorite. In addition, bleaching wastewater from textile contains high levels of solid content characterised by low-to-moderate biochemical oxygen demand levels. The table below shows some of the organic and inorganic materials present in wastewater after bleaching (Correia et al. 923).
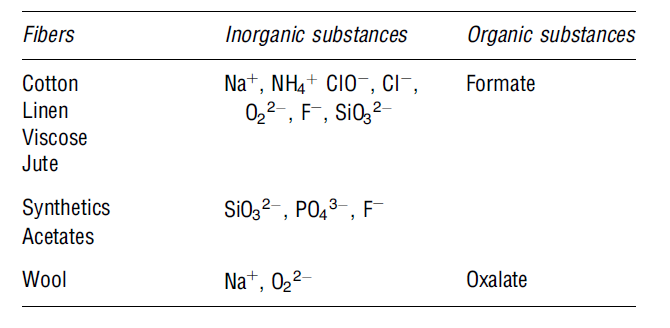
Mercerising
This is a “chemical process that improves the strength, lustre and affinity of dyes (Alenka et al. 35). The mercerising process helps to improve the appearance of fibre, its lustre, and dye-ability. Before the dying process starts, the concentrated alkaline solution is usually added. Next, the fibres are washed in an acidic solution prior to the dyeing step (Snowden-Swan 1). The wastewater effluents produced during the mercerising process have lower biochemical oxygen demand and high PH levels. The table below shows some of the possible contaminants observed in the mercerising process.

Dyeing
The process adds colour to the fibres. Large volumes of water are required to make a dye bath. Water is also used in the rinsing process after soaking the fibres in the dye. Chemicals such as formaldehyde, sulphide, organic processing assistants, surfactants, salts, and metals are added to improve dye adsorption (Snowden-Swa 1; dos Santos, Cervantes and van Lier 2379). The compounds added to increase the levels of pollution in wastewater because they are toxic in nature. The table blow shows some of the possible contaminants in the dyeing process.
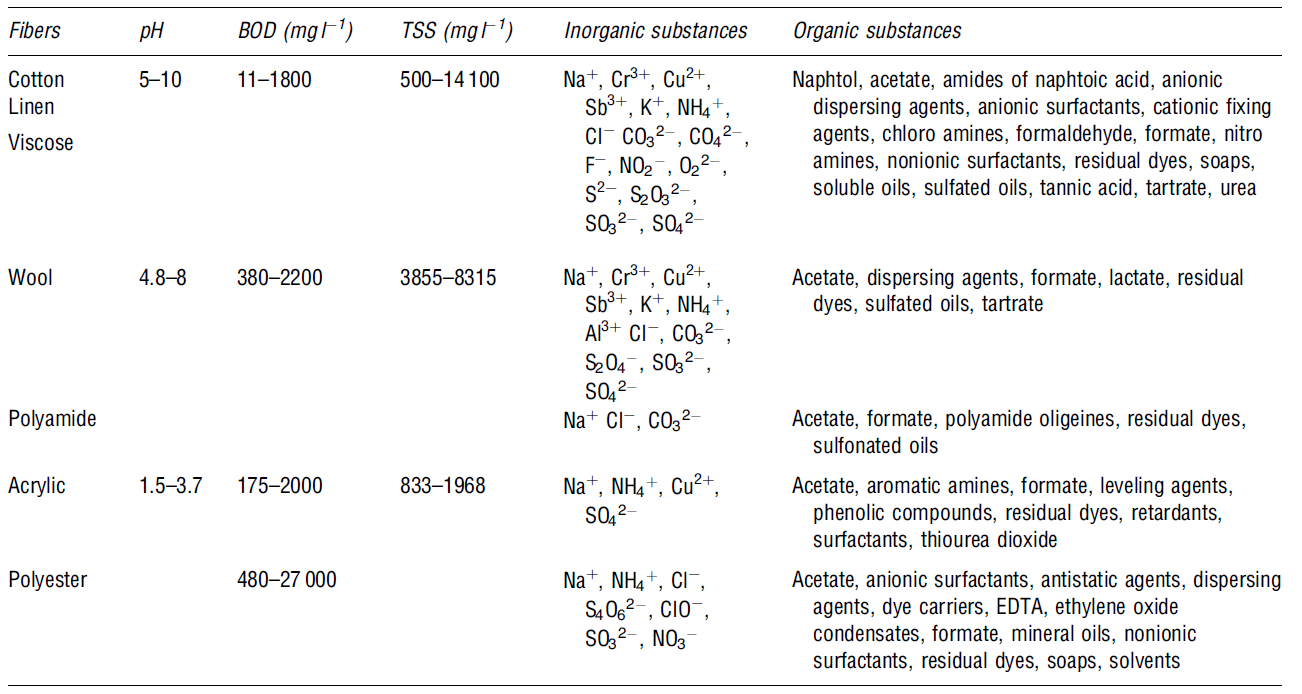
Printing
This process entails the addition of colour to the textile material. The major printing methods are “rotary screen, direct, discharge, resist, flat screen, and roller printing (Le Marechal et al. p. 36). These techniques are mainly used for commercial purposes. Le Marechal et al. have noted that “pigments cover about 75-85 % of all printing operations, do not require washing steps and generate a small amount of waste” (p. 36). This means that less water is required in the printing process because most of the pigments used have high affinity and are insoluble by nature. The key constituent of textile printing is a print paste, and it comprises water, dyes, urea, thickeners and other chemicals like organic solvents and surfactants (Volmajer Vale et al. 687).
Finishing
This process “involves those mechanical/physical and chemical treatments performed on fibre, yarn, or fabric, in order to improve appearance, texture, or performance” (Le Marechal et al. p. 36). These treatments are used to improve the serviceability and properties of the fibre. Wastewater from the finishing process contains polyvinyl alcohol, CMC derivates, stearate, acetate. Waxes, resins, and waxes, among other toxic organic compounds (Volmajer Valh et al. 688).
General characteristics of textile wastewater
Wastewater from textile industries is composed of hazardous organics such as dyes, persistent organic pollutants, salts, surfactants, and metals. These are discussed in the following table below:
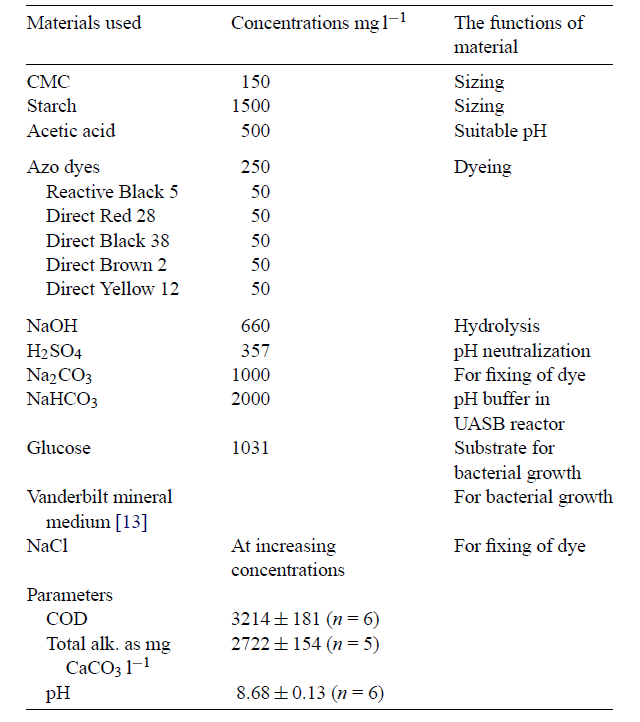
Dyes
Dyes and pigments used in different processes of textile manufacturing form wastewater compounds. In most cases, these pigments and dyes are produced in the printing and dyeing processes (Volmajer Valh et al. 688). Moreover, the dyeing process has large amounts of contaminated wastewater, particularly after bathing and washing the fabric. The wastewater effluent also contains by-products, auxiliary chemicals, and residual dyes, in addition to pollutants such as cleaning solvents (e.g. oxalic acid). Over 700,000 tons of dyes are produced annually around the globe Verma, Dash and Bhunia 155). The main methods used to remove dyes are adsorption, photocatalysis, advanced oxidation, biodegradation, electrolysis, foam flotation, chemical coagulation, chemical and biological oxidation ( Papic et al., 294-295; Lee et al. 215).
Metals
Organic metals are also used in textile processing, and some of these metals are discharged through wastewater effluents. These effluents contain toxic heavy metals components that are known to cause fatal health problems. The dyeing and finishing processes produce substantial amounts of contamination characterised by fluctuating pH, high chemical oxygen demand, and intense colour (Belkacem, Khodir and Abdelkrim 2456-256)
Salts
An inorganic salt is used in textile manufacturing processes to add and enhance dye uptake by the material. The major inorganic salts used in textile manufacturing include sodium chloride (NaCl), sodium sulphate (Na2SO4), sodium carbonate (Na2CO3), and sodium hydroxide (NaOH). The major environmental effect of the waste effluents is soil salination (Lau and Ismail 322).
Others
The table below shows some of the other components that form wastewater in the dyeing and finishing processes. The components have different concentrations rates, as shown in Table 9 below.
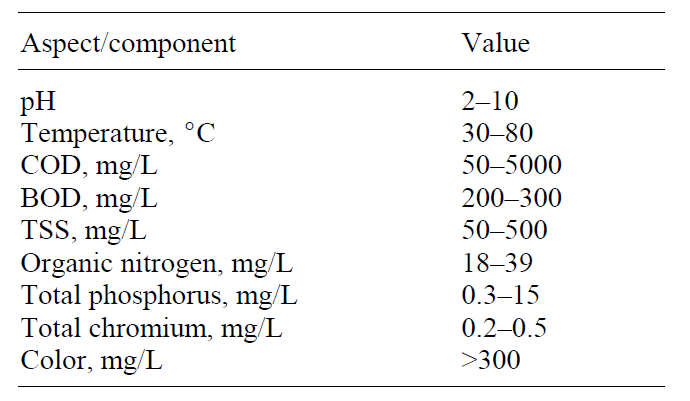
Effect of coagulants type
Metal Coagulants
The most frequently used metal coagulants are classified into two categories: (1) aluminium based and iron based coagulants (Bratby 32). The aluminium coagulants comprise “aluminium sulfate, aluminium chloride, sodium aluminate, aluminium chlorohydrate, poly aluminium chloride, polyaluminum sulfate chloride, polyaluminum silicate chloride, and other forms of poly aluminium chloride with organic polymers” (Bratby 32). On the other hand, the iron coagulants consist of “ferric sulfate, ferrous sulfate, ferric chloride, ferric chloride sulphate, poly ferric sulphate, and ferric salts with organic polymers” (Bratby 32). Other metal coagulants used in water treatment are magnesium carbonate and hydrated lime.
Iron and aluminium coagulants are the most popular forms of coagulants because of their effectiveness, in addition to their lower cost and availability (MacPhee, Cornwell, and Brown 27). The efficacy of aluminium and iron coagulants is due to their “ability to form multi charged polynuclear complexes in solution with enhanced adsorption characteristics” (Bratby 32). These coagulants have higher adsorption rates when in solution form. The table below shows some of the frequently used coagulants. A summary of their physical and chemical properties is also given:
Table 10: Physical and Chemical Properties of commonly used coagulants (Bratby 32).
Jar Test apparatus
After the effluent wastewater was collected, an experiment was conducted using the jar test apparatus. To complete the various tests, different coagulant solutions were prepared (Vanerkar, Satyanarayan and Satyanarayan 65). Under the jar test apparatus, the designed samples were cautiously mixed for 60 seconds at 100 RPM and afterwards flashed mixed at 40 RPM for 1 hour (Vanerkar et al. 65). The solution was allowed to settle for 30 minutes. The supernatant liquid was later collected, and the settling sludgevrecorded.
Table 11: ‘Physicochemical Treatability of Wastewater from Food Processing Industry Using Coagulant Ferrous Sulphate’ (Vanerkar et al. 65).
From table 11 above, the coagulant used (ferrous sulphate) resulted in a 72.52 per cent of the suspended solids removed at an optimal dosage of 175 mg/L, while that of BOD removal was 58.2 per cent. Sludge production after adding ferrous sulphate was considerably less in terms of volume compared to Alum. The colour of the sludge/effluent was dark at the maximum addition of ferrous sulphate dosage.
At the lowest dosage of 50 mg/L, the suspended solids removal was recorded at 48 per cent, while the biochemical oxygen demand and chemical oxygen demand reductions were 30 per cent and 32.59 per cent, respectively. In regards to the general efficiency and optimal Ferrous Sulphate (FeSO4) dosage of 125 mg/L was found to be most effective as the biochemical oxygen demand, chemical oxygen demand, and suspended solids removals rates were at 51.21 per cent, 46.21 per cent, and 65.65 per cent, respectively.
Table 12: Table 5: (Physicochemical Treatability of Wastewater from Food Processing Industry Using Coagulant Ferric Chloride) as adopted from (Vanerkar et al. 65).
With regards to ferric chloride, the results indicated that its removal was considerably lower in comparison with ferrous sulphate (Vanerkar et al. 65). To begin with, biochemical oxygen demand, chemical oxygen demand, and suspended solids reductions were at 40.0 per cent, 35.02 per cent, and 64.12 per cent, respectively, at a minimal dosage of 125 m/L. This is has been depicted in table 12 above. At the optimal dose of 175 mg/L, the reductions showed an increasing trend, albeit marginally. Additionally, the effluent’s colour was considerably dark, which made it aesthetically unsuitable. At the optimal dosage of 175 mg/L, the removals indicated an increased trend although secondary. In addition, the effluent’s colour was considerably dark, which made it aesthetically unsuitable.
At 125 mg/L, the optimal dosage for ferric chloride and ferrous sulphate removals was achieved. Moreover, the treated effluent using ferric chloride reported the colour change, which yellow but intensified as more doses were used. Compared to the ferrous sulphate, the level of sludge production was higher in the case of ferric chloride. We can therefore safely conclude that both coagulants are not congenial when used for wastewater treatment because they add iron content, change the colour of the effluent, and are costly.
Organic polymer coagulant
The two figures below represent the impact of polymer dosage when used on turbidity and colour removal.
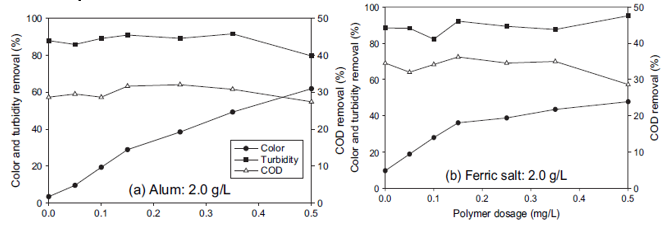
Variation in the dosage of the polymer on turbidity and colour was carried out at the p-0.5g/L range. On the other hand, the inorganic coagulants were maintained at a fixed level of 2.0g/L (Joo and Shin et al. 63). As reflected in figure 2, there was a gradual increase in colour removal as the polymer dosage was raised. In regards to the alum/polymer treatment, there was a steady efficiency increase of colour removal to 62 per cent when polymer dosage was raised to a level of 0.5 g/L (Joo and Shin et al. 63).
Nonetheless, the speedy increase in regards to colour removal was experienced in ferric salt to a level of 0.15g/L. In figure 2b, the rate of increase gradually becomes smaller after passing 0.15g/L of the ferric salt/polymer. In general, compared to ferric salt/polymer, alum/polymer was considerably more efficient in colour removal. However, an additional polymer of the polymer showed no significant effect in COD and turbidity removal (Joo and Shin et al. 63).
In both treatments, the removal of turbidity was 90 per cent, while COD removal was only 30 and 35 per cent for alum/polymer and ferric salt/polymer, respectively (Joo and Shin et al. 63). This suggests that the inorganic coagulant is not an effective dosage when used in isolation. However, the addition of polymer increases the rate of dye removal from real wastewater by 62 per cent.
Works Cited
Belkacem, Merzouk. Khodir, Madani and Abdelkrim, Sekki. “Treatment characteristics of textile wastewater and removal of heavy metals using the electroflotation technique.” Desalination, 228.1-3 (2008): 245-254. Print.
Bratby, John. Coagulation and Flocculation in Water and Wastewater Treatment. London: IWA Publ, 2006. Print.
Correia, Venceslau, Tom, Stephenson and Simon, Judd. “Characterization of textile wastewaters – a review.” Environmental Technology, 15.10 (1994): 917-929. Print.
dos Santos, Andres, Francisco, Cervantes and Jules, van Lier. “Review paper on current technologies for decolourisation of textile wastewaters: perspectives for anaerobic biotechnology.” Bioresource Technology, 98. 12 (2007):2369-2385. Print.
Joo, Duk Jong, Won, Sik Shin, Jeong-Hak, Choi, Sang June, Choi, and Myung-Chul, Kim. “Decolorization of reactive dyes using inorganic coagulants and synthetic polymer.” Dyes and Pigments , 73 (2007) :59e64. Print.
Lau, Woei-Jye and Afauzi, Ismail. “Polymeric nanofiltration membranes for textile dye wastewater treatment: Preparation, performance evaluation, transport modelling, and fouling control- a review.” Desalination, 245.1-3 (2009): 321-348. Print.
Lee, In-Seok., Lee, Sung Hee and Lee, Jeung-Eun. “ Occurrence and fate of synthetic musk compounds in water environment.” Water Res. 44.1(2010): 214–222. Print.
Le Marechal, Alenka Majcen and Boštjan, Križanec. Textile Finishing Industry as an Important Source of Organic Pollutants. 2014. Web.
MacPhee, Michael, David, Cornwell and Richard, Brown. Trace Contaminants in Drinking Water Chemicals. Denver, CO: AWWA Research Foundation and American Water Works Association, 2002. Print.
Papic´ Sanja, Natarija, Koprivanac, Ana Boži and Azra, Meteš. “ A removal of some reactive dyes from synthetic wastewater by combined Al(III) coagulation/carbon adsorption process.” Dyes Pigments 62 (2004): 293–300. Print.
Puzyn , Tomasz and Aleksandra, Mostrag-Szlichtyng. Organic Pollutants Ten Years after the Stockholm Convention – Environmental and Analytical Update. 2014. Web.
Snowden–Swan, Lesley. Pollution Prevention in the Textile Industries, In, Freeman, H. M. (Ed.), Industrial Pollution Prevention Handbook. New York: McGraw-Hill, 1995. Print.
Vanerkar, Arya, Njeev, Satyanarayan and Shanta, Satyanarayan. “Treatment of Food Processing Industry Wastewater by a Coagulation/ Flocculation Process.” International Journal of Chemical and Physical Sciences, 2.1 (2013): 63-72. Print.
Verma, Akshaya Kuma, Rajesh, Roshan Dash, and Puspendu, Bhunia. “A review on chemical coagulation/flocculation technologies for removal of colour from textile wastewaters.” Journal of Environmental Management, 93.1 (2012): 154-168. Print.
Volmajer, Valh, Majcen, Le Marechal, Arya, Vajnhandl. S and Jerič, Šimon. Water in the Textile Industry. In: Peter Wilderer (ed.) Treatise on Water Science. Oxford: Academic Press, 2011. Print.
Water Rand. Water Purification. n.d. Web.
Zahrim, Abu, Chedly,Tizaoui and Nidal, Hilal. “Evaluation of several commercial synthetic polymers as flocculant aids for removal of highly concentrated C.I. Acid Black 210 dye.” Journal of Hazardous Materials, 182.3 (2010): 624-630. Print.