Theoretical Evidence
In today’s marketplace, optimization of resources, their adequate use, and cost reduction are the key attributes of a successfully developing company capable of competing effectively. For the qualitative analysis of available resources and the possibility of their optimal use in business practice, there is a large number of methods and models used depending on specific tasks. One of them is Economic Order Quantity (EOQ), which is a model used to determine the optimal quantity of goods or materials to be ordered at a given time in order to minimize the total cost of inventory. The point of minimizing inventory is to save costs since unsold goods take up space, to reduce risks since inventories can become obsolete or physically obsolete, which is especially true in the food industry, and to increase efficiency since excessive inventory can make it difficult to account for them. Thus, EOQ seeks to eliminate situations in which inventory builds up and instead offers tactics and methods to calculate and predict these quantities.
The fundamental idea behind EOQ is based on the premise that trade-offs exist between the cost of placing an order and the cost of holding inventory. From an economic perspective, the basic structure of EOQ is represented by three components, namely, the cost of storing inventory, the cost of placing an order, and the demand for products. Demand should be understood as the number of units of a product that are expected to be sold in a given period of time. High demand is a favorable sign for business because it responds to increased consumer popularity of the products. The cost of product placement includes the cost of processing the order, transportation costs, and any other costs associated with placing the order. Ideally, companies should strive to keep placement costs as low as possible to increase margins. Finally, the third component of EOQ is inventory holding costs, which should be defined as the physical cost of holding inventory, insurance costs, and other opportunity costs associated with not being able to use the capital for other investments. It follows that these costs should also be reduced in order to increase profit margins in the company. Thus, the three-component EOQ is based on finding equilibrium points at which there is an optimal number of orders by minimizing the total cost of inventory equal to the sum of the cost of placing the order and the cost of holding the inventory.
To use the EOQ model to solve real-world problems, companies need to have information about product demand (D), order placement cost (S), and inventory holding cost (H). When this information is known, the following formula can be used.
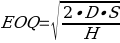
The formula will determine the optimal economic number of orders that a company should operate on in order to minimize inventory costs. In doing so, information about the optimal number can then be used to determine the necessary frequency of ordering and quantify how many items the company needs to order each time to ensure that unnecessary costs are minimized (Tarver, 2021). Among other things, the EOQ model can determine the number of orders that a company needs to place in order to ensure that there is no surplus or shortage of inventory, which means that the goods ordered in quantity are close to the goods sold.
The disadvantage of using such a model is the assumption that the demand function is constant, which means that customers must consume the same number of products throughout the year. Obviously, not all products fit this description, and demand will not be constant for seasonal products associated, for example, with the Christmas holidays. In addition, ordering costs should also be constant according to EOQ logic, but this paradigm does not take into account the probability of unforeseen business events and the impact of geopolitical and natural crises on economic well-being.
The EOQ model also includes the term total cost (TC), which, as shown in Figure 1 below, is a non-variable value. In general, TC should be understood as the sum of fixed costs of order placement (order placement cost) and variable costs of inventory storage (inventory storage cost).
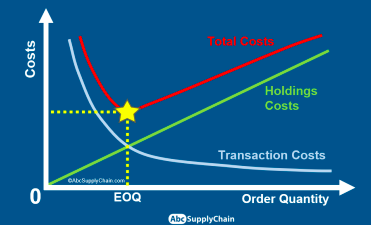
In the discussion of the EOQ model, one should additionally point out its fundamental differences from the Just-in-Time (JiT) model. JiT is a production and inventory management model in which raw material components are supplied, and production processes are performed only as needed (Banton, 2022). Thus, the primary difference between the two models is the different philosophies: while EOQ seeks to determine the optimal number of orders, JiT seeks to reduce unnecessary inventory. Moreover, EOQ seeks to maintain order quantities unchanged over time, whereas JiT focuses on satisfying only the number of orders that have been placed by customers.
The Practical Case
The above reflections can easily be applied to solving the case study on a company selling Ultamyacin at Smitheford. The annual demand (D) is 400,000 units, the annual storage cost rate is 15% of the product cost, the cost of purchasing the product is $48 per unit, and the cost of ordering the product is $28.00. These data are sufficient to calculate the optimum number of orders for the company, viz.:
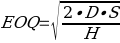

This formula uses the cost of purchasing the product instead of H is $48 per unit, multiplied by 15 percent. This decision was not accidental because the original formula includes the cost of storing inventory, which, according to the terms, is 15% of the cost of the product. The remaining steps are to simplify the expression.

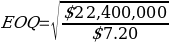


In other words, applying the formula showed that the optimal number of orders for the company (rounded) should be 1,764. In this case, the company will be able to manage its inventory in an optimized way, as expected, it will not be in excess, and the company will be able to minimize the cost of maintaining it. To calculate TC for the available data, one must remember that TC is the sum of the fixed costs of placing the order and the variable costs of keeping the inventory. In general, the formula will look like this:
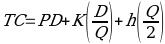
The formula uses quantities such as the unit purchase price (P), the amount of annual demand (D), the fixed ordering cost (K) and the annual unit storage cost (h), and the order quantity (Q). Substituting the known values, the total cost can be calculated.



Hence, the TC for this company is approximately $19 million. It is interesting to observe how the TC changes if the quantity is 1,000. It is important to note that it is talking about the optimal quantity, then in this case, there is a decrease in the calculated equilibrium value by 763.83 units. Then:


That is, when the optimal quantity is reduced, the TC is also reduced by about $8,000. But if one disregard the cost of goods per unit, the total cost is $14,800 for 1,000 items versus $12699.61 for 1,763.83 items, which means the difference is $2,100.39. As a consequence, without considering the total cost of goods, the TC increases when the number of items is reduced, which may be evidence of reduced stocking costs.
References
Banton, C. (2022). Just-in-Time (JIT): Definition, example, and pros & cons. Investopedia. Web.
Tarver, E. (2021). How is the economic order quantity model used in inventory management? Investopedia. Web.
Thieuleux, E. (2022). EOQ formula with examples in Excel (Economic Order Quanntity). ABC Supply Chain. Web.