Introduction
Job order cost accounting system is often used by companies producing tailored products or services. Companies that use this system characteristically base it on permanent inventory system, which constantly provides an updated record of inventories. The made-to-order products are produced independently and its manufacturing is what is referred to as job order manufacturing (Garrison, Chesley & Carroll, 2010, p. 5). Examples of customized products include men suits, tailored jewelry, and work of art. Boeing is one of the top manufacturers of special-order products. Besides manufacturing customized aircraft, it also specializes in aerospace system’s design, development and integration.
At the point when a job entails delivering more than one unit of special-order products, it normally referred to as job lot. Examples of custom products manufactured as job lots include church seats. Despite the fact that these requests include more than one unit, the volume produced is normally low. Another element of job order manufacturing is the assorted qualities, which is normally referred to as product heterogeneity. To be specific, every client request is likely to vary from another in some aspect. The order difference may be trivial or noteworthy (Garrison et al., 2010, p. 6).The international job order operation begins when a company receives an order for a tailored product from a customer. This prompts the company to start working on a job. Jobs produced on speculation also exist but are less common (Barkowski, 1999, p. 22).
The job order costing follows three steps. The first step entails predicting the cost of the job. This cost is pegged on the product design developed by either the company or the client. The second step entails price negotiation and decision on whether to proceed with the job. Besides cost-plus contracts, the price is dictated by market forces. Manufacturers assess the market price, contrast it with the expense, and figure out if the return is sensible. In the event that the return is not sensible, the manufacturer would decide on the preferred target cost. The third and the last step involve scheduling production process. The schedule should address the client’s needs and match with the manufacturer’s limitations. The individuals preparing the work schedule must also pay attention to workplace facilities, for instance, space, human resource, and supplies. When the schedule is finished, the manufacturer can order for raw materials. Manufacturing takes place as raw materials and work is connected with the job (Walther & Skousen, 2010, p. 14). Figure 1 below shows an example of job order operations.
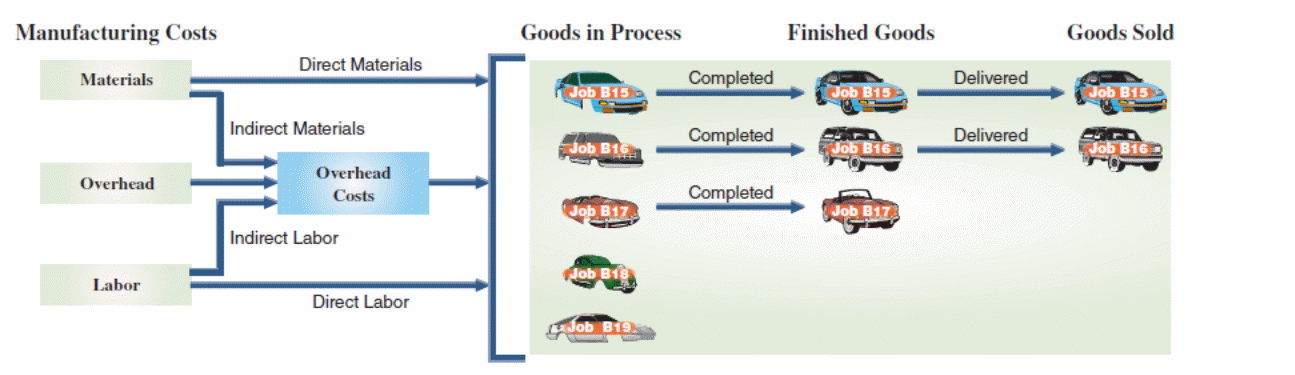
The figure above demonstrates the production operations of a company that installs safety gadgets in autos and trucks. The security gadgets include alarms, fortified exterior, impenetrable glass, and explosive sensors. The company’s clients are individuals who need additional security in their automobile. In order to make this happen, the company requires materials, labor and overhead costs. Remember that direct materials are products utilized in the production process that are distinctly linked to a specific job. Likewise, direct labor is work linked to a specific job. On the other hand, overhead costs are costs that bolster production of more than a single job. Conventional overhead items are depreciation on company facilities, production line supplies, supervision, repairs, cleaning, and other items serving various functions.
Gauging and monitoring product costs
Product costs are costs that are straightforwardly and circuitously linked to the production of goods or services. Product costs include the cost of materials and labor directly linked to the production of goods and services. It also includes overhead costs linked to the production process. The overhead costs are costs associated with the production facility, for example, devaluation of equipment and insurance cost. However, product cost disregards operational costs that are not linked to the manufacturing process, such as administrative and advertising costs (Horngren, 1996, p. 113).
The simplicity with which manufacturing costs are tracked to specific good or service relies on the level of customization. Some products and services can be singled out and some are identical. On the other hand, some goods call for a hybrid process, in which the majority of the goods are identical but a few components are tailored. For example, most private jets pass through a hybrid process. Most of these aircraft are identical in terms of design, but their inner fittings and external decorations are tailored (Garrison et al., 2010, p. 8).
One of the reasons behind measuring present and previous product costs is to provide information for financial statements. As per the conventional accounting principle, the product costs should be allotted to inventory. When the products are sold, the cost is reassigned to the cost of sales. This exercise permits stocks to be reported at cost on the balance sheet, and cost of sales to be compared with returns on the income statement. Therefore, job order costing in a production company involves allocating costs to inventory and after that cost of sales when the job is finished. To estimate the cost of specific jobs, job costing system characteristically incorporates a secondary ledger (Walther & Skousen, 2010, p. 33). As illustrated in figure 2, direct costs are drawn and overhead costs are assigned to individual jobs. Aggregate work in process is matched against aggregate accumulated costs for each job in the secondary ledger.
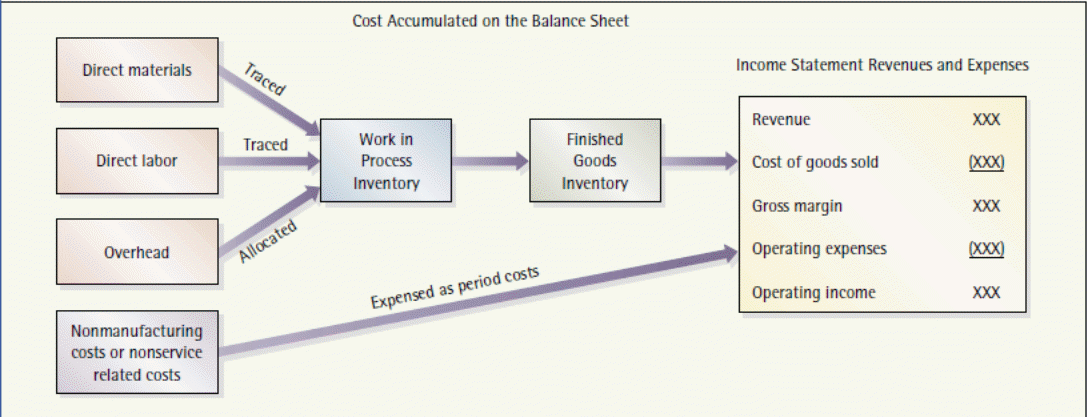
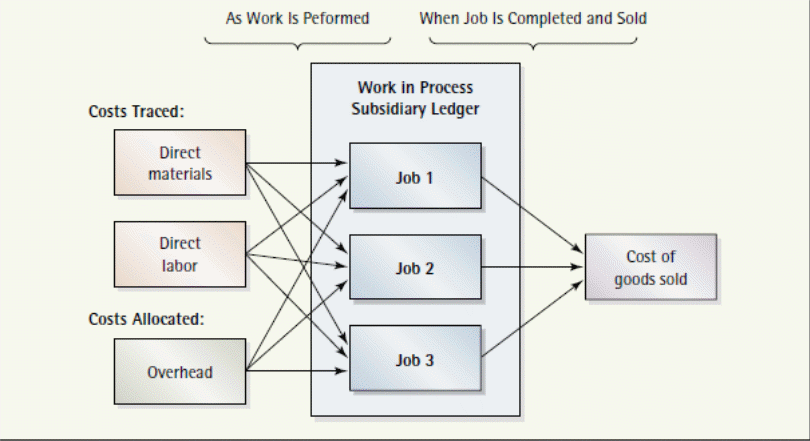
Allotting direct costs
The cost of direct materials and labor for all jobs can be traced from the accounting records. For instance, a company producing steel vents can use information from their manual or electronic records to trace direct materials and labor for each job. These records can be used to calculate employee pay from the direct labor hours, as well as the material cost for each job. The materials costs are normally traced from the existing accounting records using material request form. The information gathered from the source documents are used to assign costs in the secondary ledger for all jobs.
The record of costs assigned to a specific job in customarily referred to as job cost record (Covaleski, 2001, p. 25). Figure 3 shows a job cost record for a steel company. The cost of each unit of direct materials is available in material inventory record. On the other hand, employees’ pay per direct labor hour is available on the payroll record. In some companies, direct material, and labor costs are available in an estimated budget. From the job cost record shown in figure 3, the direct material and labor cost for job 482 is incomplete since only some material and labor have been recorded. The indirect costs have not been apportioned. The steel company measures transitory costs on each cost record. The information in the job cost record is updated, till the job is finished.
Keeping an in-depth job cost record can be laborious and susceptible to bookkeeping errors. As a result, job cost records nowadays come in the form of a computer package. In this case, when the direct costs are entered into their electronic source document, the job cost records, and the general ledger are updated automatically. The electronic job cost record enables the management to instantaneously follow job costs prior to job completion.
These computer packages are often used in large organizations with branches and clients all over the world. They are also used in instances where jobs are intricate or demand a huge amount of resources. However, in small firms, job cost records may be loosely connected to the general ledger system. In such cases, manual job records are used to trace direct material and labor costs for specific jobs. When new costs are incurred, they are recorded on the sheet, which is subsequently recorded in the secondary ledger periodically as jobs are finished or resources are exhausted (Barkowski, 1999, p. 26).
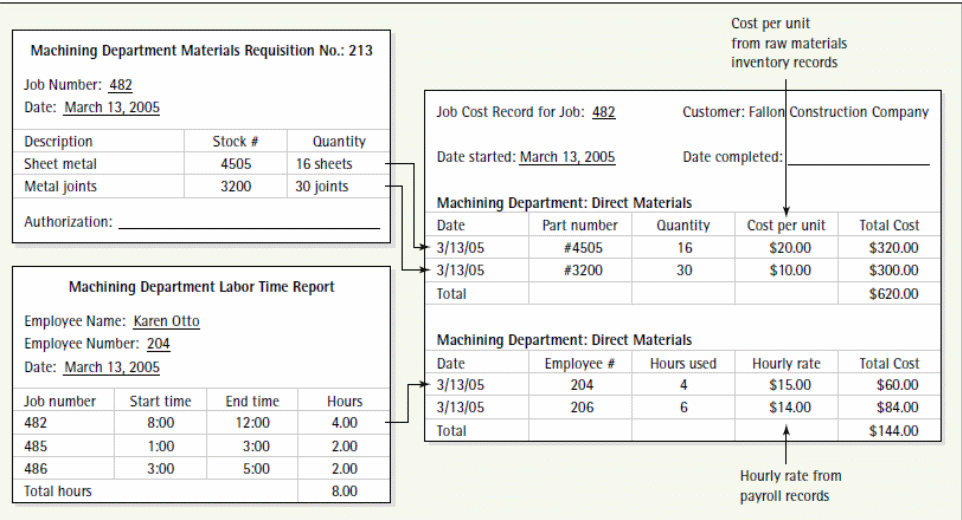
Overhead allocation
Overheads include all costs of productions, excluding direct costs. Overhead allocation is a twofold process. First, various overhead cost is amassed together in an overhead cost pool. An overhead cost pool is an assemblage of specific costs that are accrued for a given purpose. Second, costs amassed in the overhead cost pool are assigned to a specific job. The two processes require the following: identification of pertinent cost objects; identification of overhead cost pools and allotment bases; calculation of overhead allotment rate for each overhead cost pool; and allocation of cost to a specific cost object (Walther & Skousen, 2010, p. 41). In this case, the cost objects are jobs.
At times, jobs comprise of specific products, and at times it comprises of a batch of products. Overhead costs are aggregated in one or more cost pools. A number of companies often use organization-wide or factory-wide cost pool for all types of overhead costs, while others use separate cost pools. The overheads can be classified as fixed or variable overheads. Fixed overheads consist of facility managers’ salaries and rental space. On the other, variable overheads consist of all costs that fluctuate with the level of operations, for instance, the cost of power. If a job is carried out by separate units or workstations, then overhead cost pools may well be assigned to each unit or operation. Accountants are free to choose the number and sort of overhead cost pools for a company (Walther & Skousen, 2010, p. 42).
The number and sort of overhead cost pools hinge on the production plan, type of overhead costs, and the suitability of various types of overhead data available to managers. For instance, an organization may decide to have each work area under different managers who are in charge of regulating costs or have multiple work areas under a single manager. The former may decide to separate overhead cost pools for different workstations. The use of distinct overhead cost pools for different work areas would assist the executive to track the performance of station managers.
On the other hand, a single manager overseeing multiple work areas may decide to combine overhead cost pools for different work areas. Allocation base is often used to allocate overhead costs to specific jobs from each overhead cost pool. When a segment of a cost pool differs with the cost drive, the varied segment can be used as the allocation base. The allocation may be based on direct labor hours, direct labor costs and machine hours. An overhead allocation rate is the dollar per unit of allocation base used to assign overhead costs to a specific job (Walther & Skousen, 2010, p. 43). When the aggregate amount of overhead cost and number of allocation base are known, the real overhead allotment rate is computed using the following formula:
Real allotment rate= Real overhead cost/ Real number of allotment base
On the contrary, projected allocation rate is computed using the following formula:
Projected allotment rate=Projected overhead cost/Projected number of allotment base
Suppose the estimated overhead cost for Boeing’s external painting areas is $200000 for the following two months and the total labor hours is 5000. When direct labor hours are used as allotment base, then the allotment rate will be
$200000÷5000= $40 per direct labor hour
Overhead costs are allocated by multiplying allotment rate by the number of allotment base used by each object. For instance, when the allotment rate is $40 per direct labor hour and the external painting job requires 60 direct labor hours, the allocation cost is
60 direct labor hours × 40 direct labor hour = $2400
Case Study: American Louver and Venting Company
American Louver and Venting Company specialize in manufacturing aluminum louvers and vents. The company operates on a global scale and is based in Logan, Utah. American Louver and Venting Company have been utilizing job order costing to screen and regulate direct expenses and overheads. The company has two sections, namely: machining and assembly. Distinct overhead cost pools are used in each section. However, fixed and variable overhead costs are integrated into each overhead cost pool.
In the assembly section, direct work expense is utilized as the allotment benchmark. Additionally, American Louver and Venting Company use the international costing approach to assigning postulated overhead cost to specific objects. In the machine section, next to no immediate work is needed. A huge fraction of the cost in the overhead pool is linked to machine operation and, therefore, machine hour is used as the allotment base. The assembly section depends intensely on direct work and limited machines. The labor varies from skilled to unskilled personnel (ALVC, 2016, p. 3.).
The following estimates were developed for the fiscal year ending December 2015:
This information can be used to compute the allocation rate for each department, which is as follows:
Machining: $1350000÷24000= $56.25 per machine working hour
Assembling: $2420000÷$1200000= 201% of direct labor cost
In order to understand how American Louver and Venting Company job costing system assigns overhead cost, we can use job 482 for various computation. Job 482 was finished a week ago and involved a shipment to an overseas construction site. The following information is available in the job cost record relating to job 482.
Using the above information, we can compute the amount of overhead for job 482 as follows:
- Machining: 100 machine hours × $56.25 per machine working hour = $5625
- Assembly: $10010 direct labor cost × 201% of direct labor cost= $20120.0
It is always beneficial to management when the report incorporates returns and earnings, as well as initial bid. However, it was not possible to directly access such data from the company’s job costing system. Nonetheless, there is always a way of linking the job costing system with returns and job bid information. All these are available in the company’s general ledger. The general ledger normally includes distinct inventory accounts for direct materials, work in progress, finished products. Usually, a number of direct materials cannot be traced to specific objects when utilized, for example, supplies. For this reason, they are relocated to overhead cost pool.
Over-applied and under-applied overhead costs
Under international job order costing, constant alterations need to be made so as to harmonize the factual overhead with the quantity of overhead that has been assigned to a specific object. When computing overhead allotment rate, overhead cost and allotment base are used. At the end of the period, the quantity of overhead in the inventory account may be too small or in excess, hence harmonization has to take place. Over-applied overhead arise when real costs are less than the aggregate amount of overheads assigned to inventory account. Conversely, under-applied overheads arise when real costs are more than the aggregate quantity of overheads assigned to inventory account (Polimeni, Handy & Cashin, 1994, p. 144).
In order to rectify the two situations, the quantity of overheads assigned to real overhead costs has to be compared first. For example, suppose the machine section total overhead costs were $1620000, whereas cost assigned to a specific object were $1350000 (24000 machine hours × 56.25 per machine working hour). The total overheads for the assembly section were $2420000, whereas the cost assigned to a specific object were objects were $2412000($1200000 direct labor cost ×201% of direct labor cost). The collective amounts of over-applied and under-applied overhead costs are as follows:
Pros and cons of job order costing system
Assume a client approached a law firm in order to handle a lawsuit against an individual he feels plagiarized his work. The company’s accountant predicts the case will take 400 hours of expert labor. He also projects the following direct costs:
In the previous year, the company’s total overhead costs were $400000 and the partners worked for approximately 4000 expert labor hours. As a result, the projected allotment rate was $100 per direct labor hour (400000÷4000). Therefore, projected overhead cost for this case is $100×400 hours=$40000 and the sum of the projected cost is $152000($40000+$112000). The company’s strategy is to markup cost by 15% for the projected cost hence, the projected revenue for this case is 22800 ($152000×15%). Given the above information, the customer’s service price will be:
Assume a rival company considers the direct expert labor hours as the only direct cost and regard other costs as overheads. The allotment rate is $150 per expert labor hour. The rival accountant projects the case to cost $70000+ $60000(150×400) = $130000. Given the above information, the customer’s service price will be:
It is obvious that the prices projected by the two companies are very close. The costs that are utilized to project the price are also utilized to evaluate cost in the company. The company independently accounts for directs costs, whereas the rival incorporates these costs in overhead. Each approach has its own advantage and disadvantage. For example, the company’s system incurs extra costs in accumulating and allocating outlying benefits, photocopying, and phone charges to a specific job.
Each of these costs is amassed in a distinct cost pool. The accuracy of records for these costs hinges on the capacity and desire of the staff to keep splendid records. Separating and allocating additional direct costs helps to enhance cost evaluation. The overhead cost pool is relatively small and incorporates lesser kind of costs. As the proportion of costs that can be directly tracked to a specific object increase, the precision of the costing system enhances. For this reason, systems with the lower proportion of overhead highly portray the flow of resources to specific objects.
The information available in the job order costing system can be used for numerous purposes, namely: reporting the value of inventory and cost of sales on the financial reports and revenue tax returns; creating cost projections to help in bidding on prospective jobs; comparing actual costs with projected costs; and developing cost projections for provisional and long-haul decision (Walther & Skousen, 2010, p. 37). According to Horngren (1996, p. 88), job order costing provides a comprehensive breakdown of direct materials and overheads by purpose and characteristic. As a result, it makes it very easy to assess the viability of a job based on cost projections. The overheads are allotted based on the scheduled rate. In addition, through the job order costing system, it is easy to detect wastages and flaws.
Last but not least, it monitors the efficiency of various jobs based on scientific methods (Horngren, 1996, p. 88). However, job costing system is susceptible to uncertainties and is based on individual discretion. Accountants are free to choose the amount and sort of overhead cost pools for a company. Uncertainty often surrounds the assignment of direct costs to specific objects since these costs are traced to each object. The decision on which direct cost are traced to specific objects is based on individual judgment. At times, direct costs are fairly small, and the cost of developing a framework to trace them is higher than the benefit. Furthermore, keeping an in-depth job cost record can be laborious and susceptible to bookkeeping errors. Polimeni et al. (1994, p. 145) also points to the fact that strict regulation of costs linked to specific objects under the job order costing system is an uphill task since overhead allotments are based on projected figures.
Personal reflection
When products and services are tailored, numerous costs can be simply be traced to a specific product. For instance, the interior of most private jets is tailored to match the needs of clients. Direct materials costs, for example, covering expenses can be tracked to a specific aircraft. This also applies to direct labor. Other production costs, for instance, office director’s income and insurance expenses are backhanded and relegated as a major aspect of overhead to a particular item. A request or an order from a client constitutes a job. A job can also constitute a consignment of products or services. Job order costing is the procedure of allocating costs to tailor-made products or services. Direct materials and work expenses are allocated to specific jobs, as well as the manufacturing overheads. Job allotment depends on the overhead costs, allotment base, and the allotment rate.
The three are very beneficial when the management wants to arrange for new jobs. Once the labor hours are projected for a bid, the projected allotment rates can be utilized to guesstimate overhead costs. When a computer package is used, overhead costs can be estimated automatically. As the labor cost is keyed in the computer, overhead costs are assigned to specific objects instantaneously. All things considered, source document must unite distribution base information required to allocate overhead expenses. As already been stated, direct labor hours and costs can be retrieved from the payroll. However, exact details regarding usage of labor or machine hours by each object should be recorded in a job costing system. Suitable information on machine use may not be reachable unless particular records are kept.
The accounting department can create an online system where such information can be recorded by the operators. Since managers usually need cost data before job completion, projected allotment base is used to assign overhead. When the projected allotment rate and real allotment base are used to assign overhead, then this is known as normal costing. Normal costing is often used to create provisional income statements, control costs, and guesstimate costs for bids. In other words, the management essentially measures historical costs when generating financial statements and different reports related to the company’s returns.
The stakeholders use profitability to assess the organization’s performance and to settle on speculation and different choices. Historical cost data is additionally utilized by the management to screen operations, estimate costs, and once in a while settle on long haul choices, for example, whether to present another item. To facilitate various uses of cost data, we have to acknowledge costs that are related to a product and cost that are not specifically identified with production.
Conclusion
Job order costing is suitable for companies that produce heterogeneous products and services. The customization principle is pertinent to both manufacturers and companies providing services. Many companies providing services address clients’ needs by offering tailored services for each client. Cases of such services include a bookkeeper assessing a customer’s financial reports, an interior designer redesigning an office, a wedding advisor arranging and overseeing an entourage, and an advocate defending a client.
Whether the setting is assembling or administration, job order operations entail addressing the requirements of clients or carrying out custom jobs. Job order costing is the procedure of allocating costs to tailored products or services. Direct materials and labor costs are allocated to specific jobs, as well as the production overheads. Job allotment depends on the overhead costs, allotment base, and the allotment rate. The information available in the job order costing system can be used for numerous purposes, namely: reporting the value of inventory and cost of sales on the financial reports; creating cost projections to help in bidding on prospective jobs; comparing actual costs with projected costs; and developing cost projections for provisional and long-haul decision
References
ALVC. (2016). American Louver and Venting Company: About Us. Web.
Barkowski, L. (1999). Intranets for Projects and Cost Management in Manufacturing. Cost Engineering, 1, 21-33.
Covaleski, J. (2001). Manufacturing Niche May Be Too Hairy for CPAs. Accounting Today, 1, 22-28.
Garrison, R., Chesley, G., & Carroll, R. (2010). Solutions Manual to Accompany Managerial Accounting. New York: McGraw Hill.
Horngren, C. (1996). Cost Accounting. New York: Prentice Hall.
Polimeni, R., Handy, S., & Cashin, J. (1994). Schaum’s Outline of Theory and Problems of Cost Accounting. New York: McGraw-Hill Irwin.
Walther, L., & Skousen, C. (2010). Job Costing: Managerial and Cost Accounting. London: London Business School.