Introduction
Crude oil entails a complex fluid that comprises colloidal particles including asphaltenes and resins spread in a blend of aliphatic and aromatic solvents. The particles mentioned above attribute for the extreme stability of water-in-oil emulsions (Santos, Brinceño, & Loh, 2017). Complete separation of water from crude oil is essential for economic and operational purposes, mainly before transportation and refining. The process aims at reducing the water content of the produced crude oil. It is critical to breaking down the water/oil emulsions, a process referred to as emulsification. Different scholars have attempted to study the numerous mechanisms responsible for the stabilization of water-in-oil emulsions. It is worth noting that emulsions have for a long time been of significant practical interest for the widespread occurrence (Santos et al., 2017).
Notable applications of emulsions include food, cosmetics, pulp and paper, pharmaceutical, and agricultural industries. In recent years, significant advances characterize the crucial stages of emulsions including drilling, production, transportation, and a procession of crude oil (Wen, Zhang, & Wei, 2016). This paper presents a literature survey in the emulsification of heavy crude oil in water.
Heavy oil is exceptionally resourceful. The recent decades have witnessed an increased demand for heavy crude in the wake of the shortfall of conventional oil (Jha, Mahto, & Saxena, 2015). Multiple types of research have studied the emulsion of heavy crude with a central focus on leading a greater understanding of complex systems, which characterize oil composition (Ashrafizadeh, Motaee, & Hoshyargar, 2012). The heavy oil contains surface-active molecules, which cover an extensive range of chemical components, structures, particles, weights, and Hydrophilic-Lipophilic Balance values (Santos et al., 2017).
The complexity of heavy oil emanates from the interactions between the chemical structures at the water/oil interface (Martínez-Palou et al., 2013). It is important to note that transportation of highly viscous hydrocarbon entails dispersing the heavy crude oil in water in the form of droplets stabilized by surfactants (Wen et al., 2016). Heavy oils are made up of large quantities of asphaltenes, which involve high molecular weight polar components that oil explorers describe as natural emulsifiers.
The process of separating heavy crude oil and water is complicated and costly. Jing et al. (2015) demonstrate that heavy crude has higher room temperature viscosity of between 103mPa-s and 105mPa-s. Considering that the desired thickness of heavy oil for easy transportation and processing is typically at 200mPa-s when the temperatures remain at 15°C, it is arguable that heavy crude is more difficult to transport and process compared to the case of light crude. This finding is supported by Kumar and Mahto (2017) in their discovery that carrying heavy crude oil is challenging due to the high viscosity in heavy crude oil emulsions. To address this challenge, players in the petroleum industry engage in several processes meant to reduce friction between crude oil and the interior of pipelines and lower the viscosity of crude oil (Wen et al., 2016). These drag force-reduction measures can take place in situ or along the pipeline or even in intermediary pumping and storage facilities.
Mainly, the emulsification of heavy crude oil in water has been considered as a cost-efficient method (Keleşoğlu, Pettersen, & Sjöblom, 2012). Proponents argue that the emulsification of heavy crude oil in water helps to lower the viscosity of heavy crude since water is a continuous phase while the oil molecules are the dispersed phase. For example, Kumar and Mahto (2016) argue that the use of suitable surfactants can help stabilize and transport heavy crude oil over long distances. Wen et al. attribute such a possibility to the continuous water phase reduces the chances of corrosion of pipelines, clogging of pipelines, and deposition of wax along pipeline walls (2016). Arguably, the cost and efficiency implications that emerge from the emulsification of heavy crude oil in water warrant scrutiny to establish its application in the massive oil extraction, storage, transportation, and refinery (Santos et al., 2017). This immediate need forms the basis of this literature survey.
Definition of Key Concepts
For this literature survey, emulsification will be considered to mean the process of mixing crude oil with water in the presence of suitable surfactants to form stable emulsions that can be easily transported through pipelines with minimal friction and resistance (Santos et al., 2017). Further, separation of heavy crude oil from light crude oil occurs because of its high viscosity. Concepts utilized in this literature survey are context-specific. For this literature survey, emulsification will be considered to mean the process of mixing crude oil with water in the presence of suitable surfactants to form stable emulsions that can be easily transported through pipelines and other petroleum industry installations with minimal friction and resistance. Emulsions must be stabilized to achieve maximum effects.
Emulsifiers are predominately asphaltenes or complex poly-aromatic compounds that are soluble in ethyl acetate, soluble in n-alkenes, and do not have a definite melting point. Asphaltenes are composed of sulfur, nitrogen, oxygen, and trace metals. Stability is the ability of a heavy crude oil emulsion to stick together for a longer period. As evidence adduced by Santos et al., tight emulsions have high viscosity levels and high zeta potential scores (2017). The stabilizing effect is caused by emulsifiers such as asphaltenes which work by way of forming a rigid interfacial film that causes a coalescing effect (Martínez-Palou et al., 2013).
Viscosity implies the ability of crude oil or water’s internal resistance to flow. It is related to the overall thickness of the liquid. According to Keleşoğlu et al. (2012). heavy crude oil has a high viscosity of higher room temperature viscosity of between 103mPa-s and 105mPa-s. Water has relatively lower viscosity at room temperature. This process slows its running speed when passed through a pipeline or other petroleum industry installations. Interfacial viscosity – the viscosity of the fluid at the oil/water interface (Wen et al., 2016). This type of viscosity differs from the normal viscosity of either of the oil and water components in the sense that it only applies to the interface level.
Formation of Heavy Crude Oil Emulsions in Water
Emulsions are classified into three categories depending on the amount of the dispersed phase and the continuous phase (Wen et al., 2016). When heavy crude oil molecules are dispersed in water, the resultant emulsion is referred to as oil-in-water (O/W), when water molecules are dispersed in heavy crude oil molecules the resultant emulsion is referred to as water-in-oil (W/O) (Santos et al., 2017). On its part, when multiple heavy crude oil or water molecules are dispersed in a continuous phase of either component the resultant emulsion is referred to as water-in-oil-in-water or oil-in-water-in-oil (W/O/W or O/W/O) (Hoshyargar, Marjani, Fadaei, & Shirazian, 2015). Figure 1 below captures a graphical representation of the three categories of oil-water emulsions. The formation of a specific type of emulsion is determined by factors such as the amount of water and crude oil molecules, mixture state, and the presence of natural surfactants such as asphaltene (Santos et al., 2017). As shown in the preceding paragraphs, the naturally occurring surfactants work by way of dispersing heavy crude oil particles in water molecules.

W/O emulsions are the most common in many oil fields. Researchers argue that most oil fields feature W/O and W/O/W emulsions with O/W and O/W/O emulsions being considered as reverse and very rare (Keleşoğlu et al., 2012). Identifying the nature of emulsions existing in an oil field entails checking the volume fraction of the dispersed phase. The other stage is known as the continuous phase (Santos et al., 2017). Even so, sometimes it is not easy to determine the smaller period from the other stage, something that calls for the use of other factors such as the size of droplets present in the continuous phase. With the use of the Droplet Size Method, emulsions can either be macro especially when the droplets are more considerable than 0.1um, or micro when the droplets’ size is smaller than 10nm (Keleşoğlu et al., 2012).
Macro-emulsions are typically thermodynamically unstable because the dispersed phase and continuous phase tend to separate over time due to loss of interfacial energy when some droplets coalesce. In contrast, the microemulsions are considered to be thermodynamically stable since they are made up of two immiscible phases and have low interfacial energy (Keleşoğlu et al., 2012). Looking at the formation of macro and microemulsions, it becomes clear that both their composition and stable nature differs significantly. The smaller the droplet size, the more thermodynamically stable an emulsion becomes.
True emulsions are typical representations of small droplets that are always in Brownian motion. Ashrafizadeh et al. argue that an actual emulsion must have tiny droplets that move regularly, and therefore hard to settle (2012). Such movement is referred to as Brownian motion and is caused by the thermal collisions among molecules in the continuous phase. In the event a pure emulsion lacks small moving droplets, then natural surfactants, as well as suspended solids, must be introduced to reduce the coalescing effect of the free energy present in the interfacial surfaces. While acknowledging that emulsions have dynamic characterizes that change over time, it becomes clear that the characteristics exhibited at the instance of formation differ with those presented at the instant when they reach a complete resolution (Keleşoğlu et al., 2012). The situation stems from the presence of different types of absorbable materials in heavy oil extracts. It is worth noting that some emulsifiers have more extended adsorption rates and persistence than others. Also, the subjection of heavy crude to varying temperature, pressure, and agitation may occasion changes in emulsion characteristics (Santos et al., 2017). These three factors are introduced interchangeably to derive desirable components during the process of extracting, storing, transporting, and processing crude oil (Jha et al., 2015).
The emulsification process is a function of several factors. Figure 1 above demonstrates that the emulsification of heavy crude oil in water is affected by some water molecules present (Keleşoğlu et al., 2012). When more water molecules are present, then the emulsion is considered to be either W/O or W/O/W, and when heavy crude oil molecules are present, then the emulsion is found to be O/W (Santos et al., 2017). Additional factors include the volume of the fraction at the dispersed phase, temperature, droplet size, distribution of droplets, and interfacial tension. When volume fraction is increased then heavy, crude oil droplets become more compact hence occasioning more friction amongst the droplets (Hoshyargar et al., 2015). In effect, increased resistance heightens the viscosity of the emulsion. Also, when a substantial crude oil extract is subjected to high temperature, its stickiness and interfacial tension properties are altered.
High interfacial tension tends to break the droplets’ integrity at the continuous phase, occasioning increased movement and coalescing. As expected, such increased change affects the overall stability of the emulsion (Hoshyargar et al., 2015). The opposite is true.
The emulsification of heavy crude oil takes place in the presence of an emulsifying agent. The authors argue that emulsification occurs when heavy crude comes sufficiently mixes with water in the presence of an emulsifying agent. The argument is based on the assumption that crude oil must mix with water at some point of extraction, storage, transportation, and processing. Also, the argument assumes that there are sufficient emulsifying agents to facilitate the emulsification process. The mixing process can occur naturally especially when heavy crude oil is exposed to water for an extended period (Hoshyargar et al., 2015). Alternatively, crude oil production exposes the crude oil to sufficient mixing with water molecules by the increasing amount of shear as the crude oil extract flows through pipelines and reservoir rock, stored in reservoirs, and processed through refineries’ equipment (Jha et al., 2015).
The core idea here is to subject the crude oil to maximum mixing to reduce the sizes of droplets of water and therefore reduce the viscosity of the emulsion (Ashrafizadeh et al., 2012). While acknowledging that the specific characteristics of the emulsifying agent such as its nature, amount, and presence have a direct impact on the viscosity of an emulsion, the mixing process is equally important because it determines the type of emulsion present. Typically, most heavy crude oil extracts have natural emulsifiers as denoted by their high viscosity (Ashrafizadeh et al., 2012).
Emulsification of dense crude oil forms emulsions in water occurs in different stages of extraction, refinement, and transportation (Hoshyargar et al., 2015). According to evidence adduced by the authors, a typical emulsion of heavy crude oil in water occurs when droplets of oil become suspended in water particles to form a stable mixture that requires separation during refinement. Some water particles present in the emulsion may differ from one oil field to another, with some crude oil emulsions having as high as 80% water particles. Heavy crude oil or water molecules in an emulsion result in a water-oil or oil-water interface depending on the percentage of the respective components of each of the two significant liquids.
Figure 2 below explains this relationship. Due to the high viscosity nature of heavy crude oil, the emulsification process can take place at various stages of heavy oil production. Notably, the phases involve extraction from ground reservoirs, inside wellbores and storage reservoirs, during transportation, during separation plants, and the final refinery phase (Hoshyargar et al., 2015). The complex nature of extraction, refinement, storage, and transportation of heavy crude oil makes it almost inevitable to avoid emulsification effects. For example, some oil-producing countries usually transport their heavy crude oil to far away refinery plants increasing the chances of emulsification as the high water content is required to reduce the high resistance exerted to pipelines by the high viscosity characters of emulsified heavy crude oil.
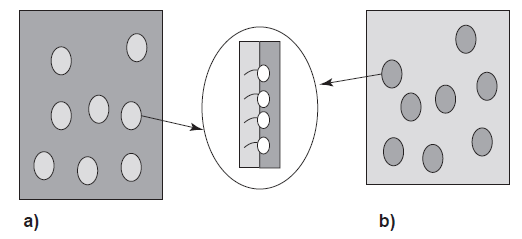
Heavy crude oil has high surface-active molecules, gases, and solids that make emulsification more complex. Jha et al. argue that the oil/water interface created in an emulsion is more complicated to separate because of the complex chemical structures of heavy crude oil (2015). Unlike light crude oil, heavy crude oil is made up of surface-active molecules such as asphaltenes that contain high molecular weight to enhance the emulsification process (Jha et al., 2015). While other components such as resins, acids, and crystals do not possess emulsification processes on their own, they work closely with the asphaltenes to enhance the emulsification process. The rule of thumb here is that the more the concentration of asphaltenes in heavy crude oil, the more the stability of oil-water emulsions (Ashrafizadeh et al., 2012). Sometimes heavy crude oil exists in multiple emulsions such as oil-water-oil or water-oil-water emulsions. Again, this is determined by the emulsification technique and the specific components forming the heavy crude oil.
Core Emulsification Techniques
The two most common emulsification techniques are mechanical homogenization, use of membranes, and ultrasonic waves. For example, the ultrasonic wave technique works by way of causing strong physical and chemical reactions that create a vibration effect, allowing immiscible liquids to be well mixed (Keleşoğlu et al., 2012). This procedure is a more desirable approach because it reduces the length of time required to stir and emulsify heavy crude oil hence eliminating the risk of precipitation. Also, this technique results in the effortless melting of wax crystals by residual heat. This effectively creates small-sized droplets and efficiently stabilizing the emulsion in ways that would not be possible using other methods.
The application of this technique is made possible by different chemicals such as PEG 200 and involves determining the density and purity levels of the heavy crude oil (Kumar & Mahto, 2016). The accessed heavy crude oil is also taken through the SARA procedure where saturates, aromatics, resin, and asphaltenes are separated. Other rigorous methods are also undertaken before stabilization and viscosity tests are conducted. On its part, the mechanical homogenization approach results in the stretching of the formed interfaces, increasing the surface area for coalescing and other stabilizing actions. For example, turbulent is formed in low shear mixers. The emerging trend here is that each emulsification technique should result in stable emulsions that have little or moderate viscosity for easy transportation through pipelines and other oil processing installations.
Looking at all the techniques discussed above, it is clear that the emulsification of heavy crude oil in water must adhere to core requirements. Jing et al. (2015) observe that the significant element for emulsification to take place include mixing, emulsification, and stabilization. Further evidence presented by shows that heavy crude oil must be mixed vigorously to form a highly stabilized emulsion. The mixing process usually begins at the oil reservoir during the squeezing or crude oil and water through narrow pores and into the production tubing until it reaches the manifold of the wellhead. This squeezing results in lowered pressure as the oil/water mixtures go through the several chokes and valves set up to allow for maximum mixing (Ashrafizadeh et al., 2012).
Later, the mixture is channeled through a series of separators set up in a train to remove excess water then channeled through electro-coalescer to remove more excess water to levels below 0.5% of the emulsion. Ashrafizadeh et al. (2012) show that depending on the density of the heavy crude oil, intense mixing can continue to take place in pumps artificial lifts. The actual emulsification process can only take place once emulsifiers such as resins, asphaltenes, and acids are present in the mixing process. The emulsification process takes place when emulsifiers form interfacial films at the oil and water interface. In effect, the interfacial films reduce the interfacial tension (IFT) which in turn increases the dispersal level of oil molecules within the water medium. Figure 3 below shows the emulsification process. It depicts a rapidly adsorbing emulsifier (right side) and slowly adsorbing emulsifier on the left side.
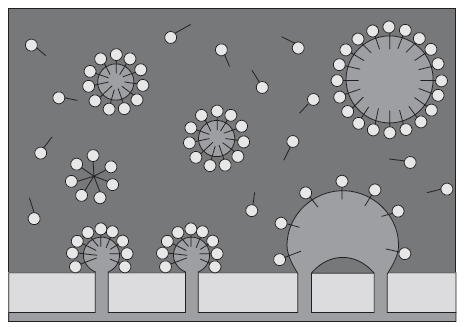
Along the way, the stability and viscosity of the emulsion must be tested and the necessary measures deployed to realize optimal levels as may be desired. For example, heavy crude oil processing that is done in situ may require low levels of viscosity and stability since it does not require transportation using the pipeline. On the other hand, petroleum companies should ensure that heavy crude oil that is transported via pipelines for lengthy distances in adverse weather conditions has optimal stability and viscosity to minimize cases of clogged pipelines (Kumar & Mahto, 2016). The stabilization of heavy crude oil emulsion is crucial as it helps to put a check on the overall viscosity of the emulsion, ensuring that there is a free flow along pipelines and other processing installations.
Stability of Emulsions
The stability of the emulsification of heavy crude oil in water is affected by the presence of solid particles such as silica and clay. Langevin et al. (2004) argue that while solid particles such as silica and clay negatively affect the stability of heavy crude oil emulsion in water due to their hydrophilic nature. As a consequence, they can become oil-wet especially when they are exposed to crude oil for far longer periods in the absence of water (Santos et al., 2017). It is important to note that when there is a decrease in the size of oil-wet particles such as silica and clay results in a more stable water-oil emulsion due to the obvious hydrophobic effect (Keleşoğlu et al., 2012). Also, a perfect combination of stabilizing surfactants such as asphaltenes and the oil-wet particles result in more stable emulsions as opposed to situations where asphaltenes are used as the stabilizing agent alone (Hoshyargar et al., 2015). This situation is however subject to the presence of sufficient asphaltenes to cover all the possible adsorption sites. As Figure 2 below shows, the asphaltenes stabilizes a water-oil emulsion by forming a heptanes molecular structure to cover resins and other particles such as naphthenic acid.
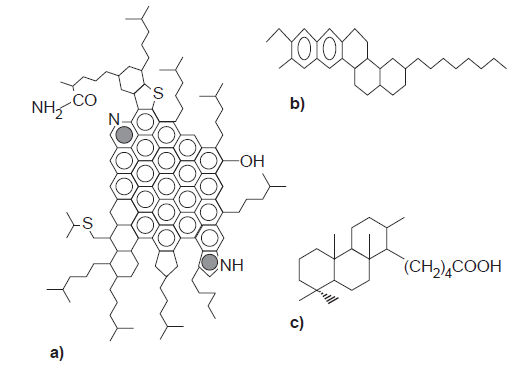
The concentration of O/W an emulsion affects its stability. In their recent study, Kumar and Mahto (2017) argue that the concentration of O/W molecules and other factors influence the stability of emulsions. Notable factors include water phase viscosity, pH, the surfactant used, dispersed droplet size, temperature, emulsification method, and density difference between oil and water molecules. As Figure 4 below demonstrates, a reduction in temperature and an increase in the content of crude oil and surfactant concentration in an emulsion tend to increase stability. Specifically, the figure demonstrates that when the oil content is increased from 40% to 60% and the surfactant is maintained at 2wt% the stability of the observed emulsion grew from 51.7% to 85% (p. 379).
At the same time, when the temperature is kept at 35_C, stability increases to 83.3% from 51.7% when the concentration of oil is 40% in the emulsion. Also, the stability of 100% is achieved at the same temperature level but increased oil concentration of more than 40% (p. 379). In explanation, stability tends to increase at reduced temperature levels because of the obvious reduction of the interfacial tension that exists between oil and water molecules in the emulsion (Jing et al., 2015). Since reduced interfacial tension also reduces internal energy and pressure of the emulsion molecules (Ashrafizadeh et al., 2012), the coalescence time is increased hence building more stability.
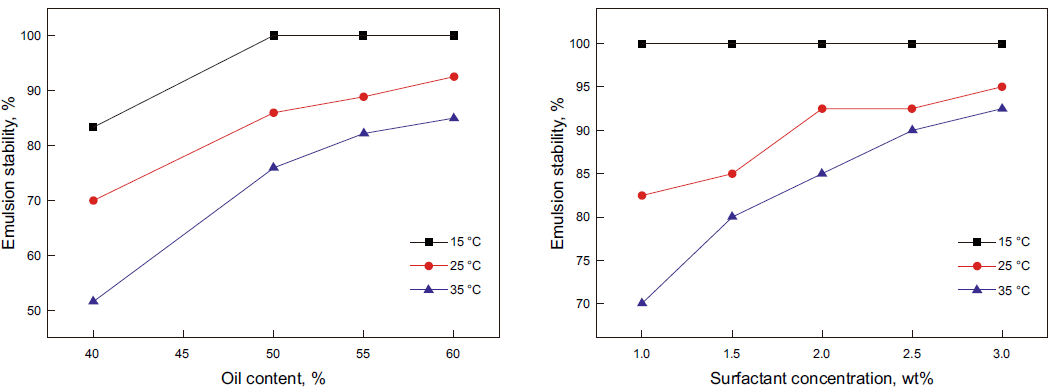
Figure 4 above shows that stability can be increased at high temperatures by increasing surfactant concentration. Kumar and Mahto (2017) find that when temperatures increase during summer as is the case in some oil-rich countries such as Kuwait and Saudi Arabia, the stability of oil/water emulsion goes down. Luckily, the challenge can be quickly addressed by increasing the amount of surfactant concentration (Roodbari, Badiei, Soleimani, & Khaniani, 2016). The logic here is that improved surfactant molecules prevent the coalescence of dispersed oil molecules. Arguably, this finding waters down efforts by some industry players to heat pipelines focus on reducing the viscosity of heavy crude oil (Keleşoğlu et al., 2012).
The concept of heating pipelines is not only a costly affair for petroleum companies, but it also lowers the stability of emulsion created hence forcing players to add more crude oil concentration and surfactant to the emulsion. Such efforts may increase the overall viscosity of the emulsion thus doing little to address the challenge of clogged pipelines (Jing et al., 2015). However, considering that most oil-rich regions experience hot climatic conditions exceeding the 15°C mark, Kumar and Mahto (2017) found such temperatures as optimal for stabilization. From the second chart of figure 4 above, it is arguable that the surfactant concentration should be kept at up to 3wt% and oil concentration at 60%.
Droplet size distribution also affects the stability and rheology of an oil/water emulsion. Ashrafizadeh et al. (2012) find that the oil/water ratio in an emulsion, the type, and concentration of surfactant and the technique used to form an emulsion determine the droplet size distribution and hence the stability of the emulsion. Kumar and Mahto (2017) support this argument by showing that some emulsification techniques such as ultrasonic waves have been noted to be more effective than others such as mechanical homogenizing techniques because they tend to produce relatively small dispersed phase droplets (Hoshyargar et al., 2015).
Figure 5 below expounds more on this finding. The chart shows that smaller droplet size distribution results in more stable emulsions. While going back to the argument made by Ashrafizadeh et al. (2012) to the effect that increasing surfactant increases stability in an emulsion, it is arguable that a higher surfactant concentration leads to the production of small size oil droplets. This finding is supported by Figure 5 below showing that an emulsion with 1wt% surfactant has oil droplet sizes between 164 and 396 nm while the emulsion with 3wt% surfactant concentration had droplet sizes of between 105 and 255 nm (Kumar & Mahto, 2017). In effect, this finding summarises the reality that the stability of a heavy crude oil emulsion is a function of oil/water concentration, temperature, droplet size distribution, and surfactant concentration.
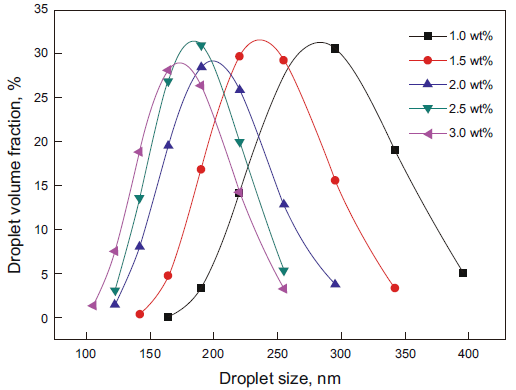
Finally, more surfactant concentration increases the zeta potential value. Kumar and Mahto (2017) found that oil/emulsions with higher levels of surfactant concentration had higher zeta likely score leading to increased stability. While using the zeta possible analysis technique to measure and predict the likelihood of an emulsion to coalesce, the authors found out that emulsions with a higher concentration of surfactant tend to register the relatively high level of electric charge on the surfaces of droplets (Jing et al., 2015). Figure 6 summarises these findings. While drawing on the reality that high electric charge indicates that the droplets tend to repel each other (Jha et al., 2015), it is arguable that petroleum companies should strive to increase the concentration of surfactants to increase the electric charge or droplets. Again, while going back to Ashrafizadeh et al. (2012) finding that more surfactant concentration results into small size droplets, it is arguable that petroleum companies can create more stable heavy crude oil emulsions by monitoring the zeta potential scores of their heavy crude oil emulsions in various stages of processing.
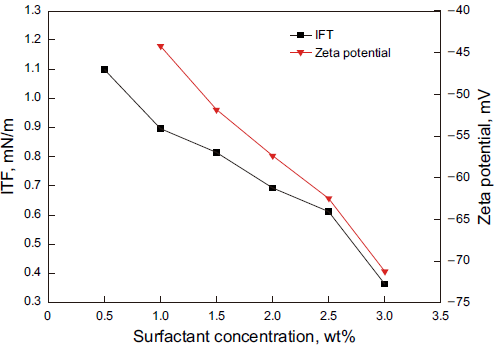
Viscosity of Emulsions
The viscosity of emulsions can be higher than that of the oil/water components. Jing et al. (2015) claim that emulsions demonstrate a non-Newtonian behavior as a result of the crowding effect and the structural viscosity of its droplets (Jing et al., 2015). The shear rate of an emulsions’ thickness is influenced by shear rate earning it the non-Newtonian tag – as the shear rate grows, the viscosity drops, making it relatively easier for heavy crude oil emulsion to flow through pipelines without occasioning clogging effect along the course. Heavy crude oil with high viscosity flowing at 175°F has been observed to exhibit Newtonian behavior up to 40% water concentration (Jing et al., 2015).
However, when the water cut goes beyond the 40% level, the emulsion exhibits a Newtonian behavior. Such a non-Newtonian response occurs as a result of shear-thinning and increases exponentially when the water cut level goes up to 80%. At this level, the emulsion reverts from W/O to O/W, with the displaced water becoming the continuous phase (Keleşoğlu et al., 2012). At high water concentrations of 95% and above, a W/O/W type of emulsion is created. In interpretation, it can be argued that a high density of water reduces the viscosity of heavy crude oil allowing free flow along with processing installations. Keleşoğlu et al. (2012). the show, these factors include the respective viscosities of constituent components (heavy crude oil and water), temperature, shear rate, solids present in crude oil, and droplet size distribution. These factors are more or less the same as the stability of the case of the emulsion.
Conclusion
Emulsification of heavy crude oil in water involves a rigorous mixing process in the presence of emulsifiers such as asphaltenes. This literature survey has shown that the emulsification process of heavy crude oil entails dispersing oil molecules in water medium through techniques such as mechanical homogenization and ultrasonic wave and use of membranes. Three core processes are involved. These are mixing, emulsification, and stabilization. While mixing helps to thoroughly stir heavy crude oil molecules with water molecules and emulsification helps to reduce the high viscosity of the heavy crude oil. On its part, the stabilization process helps to strengthen the water/oil interface.
Specifically, the emulsification process helps to lower the viscosity of the heavy crude oil, causing it to flow smoothly through pipelines and other petroleum industry processing installations. It has been found that stability can be built by increasing oil and surfactant concentration and reducing emulsion temperature (Roodbari et al., 2016). These three actions can decrease the droplet size distribution of oil molecules in the emulsion. Also, these measures can increase the zeta potential score of an emulsion. From a different perspective, the heavy crude oil extracts have a high viscosity that petroleum companies must reduce through emulsification to allow free flow through pipelines and other installations. The actual viscosity of heavy coarse oil emulsion is determined by several factors including the respective viscosities of constituent components (heavy crude oil and water), temperature, shear rate, solids present in the heavy crude oil, and droplet size distribution.
References
Ashrafizadeh, S., Motaee, E., & Hoshyargar, V. (2012). Emulsification of heavy crude oil in water by natural surfactants. Journal of Petroleum Science and Engineering, 86(87), 137-143.
Hoshyargar, V., Marjani, A., Fadaei, F. & Shirazian, S. (2015). Prediction of Flow Behaviour of Crude Oil-in-Water Emulsion through the Pipe by Using Rheological Properties. Oriental Journal of Chemistry, 28(1), 109-113.
Jha, P.K., Mahto, V. & Saxena, V.K. (2015). Effects of carboxymethyl cellulose and tragacanth gum on the properties of emulsion-based drilling fluids. Canadian Journal of Chemical Engineering, 93(9), 1577–87.
Jing, J., Sun, J., Zhou, J., Shen, X., Tan, J., Li, X., & Zhang, L. (2016). Dynamic stability of heavy crude oil in water emulsions. Journal of Dispersion Science and Technology, 37(7), 980 – 990.
Keleşoğlu, S., Pettersen, B. H., & Sjöblom, J. (2012). Flow properties of water-in-North Sea heavy crude oil emulsions. Journal of Petroleum Science and Engineering, 100(11), 14-23.
Kumar, S. & Mahto, V. (2016). Emulsification of Indian heavy crude oil in water for its efficient transportation through offshore pipelines. Chemical Engineering Research and Design, 115(Part A), 34 – 43.
Kumar, S. & Mahto, V. (2017). Emulsification of Indian heavy crude oil using a novel surfactant for pipeline transportation. Petroleum Science, 14(2), 372 – 382.
Martínez-Palou, R., Cerón-Camacho, R., Chávez, B., Vallejo, A. A., Villanueva-Negrete, D., Castellanos, J., &… Aburto, J. (2013). Demulsification of heavy crude oil-in-water emulsions: A comparative study between microwave and thermal heating. Fuel, 11(3), 407-414.
Roodbari, N. H., Badiei, A., Soleimani, E., & Khaniani, Y. (2016). Tweens demulsification effects on heavy crude oil/water emulsion. Arabian Journal of Chemistry, 9(Supplement 1), S806-S811.
Santos, R. d., Brinceño, M. I., & Loh, W. (2017). Laminar pipeline flow of heavy oil–in–water emulsions produced by continuous in-line emulsification. Journal of Petroleum Science and Engineering, 156, 827-834.
Wen, J., Zhang, J., & Wei, M. (2016). Effective viscosity prediction of crude oil-water mixtures with high water fraction. Journal of Petroleum Science and Engineering, 147, 60-770.