Abstract
The research paper explored how a mechanical pencil, which is a writing or drawing tool equipped with an eraser, is made. Although it serves the general purpose of writing or drawing, the mechanical pencil is considered superior because of its replaceable lead and erasable attribute. It is made up of several components consisting of a plastic body, plastic tube, eraser, and metal. All these materials used in making a mechanical pencil are sourced and processed separately and then transported to the mechanical pencil manufacturers. Manufacturers have developed automated processes for the manufacturing of mechanical pencils.
These processes involve the making of the plastic body, metal parts, the eraser, and the graphite. Shapes and varieties of mechanical pencils have become sophisticated as manufacturers strive for improved better designs. All these components must be assembled to produce a mechanical pencil. The final product is then packed and shipped for distribution to end-users.
Introduction
This research paper covers how a mechanical pencil is made. A mechanical is a writing tool fitted with an erasable lead part for drawing, writing and sketching on papers or woods. The general purpose of a mechanical pencil is to write and draw. It is considered superior to other types of pencils because of replaceable lead and erasable attributes.
Mechanical pencils have special features that have made them popular among writers, artists, and pencil users in general. Unlike the wooden pencil, mechanical pencils are a little bit more sophisticated. In making a mechanical pencil, therefore, a relatively comprehensive procedure must be followed. Globally, there are a considerable huge number of mechanical pencils manufacturers. As such, varieties of designs are engineered by different brands according to user preferences and pricing strategies. The most prominent brands include BIC, Sharpie, and Office Depot among others.
Mechanical pencils have leveraging aspects relative to wooden pencils. Some of the outstanding advantages include writing precisions (clear and consistent lines), do not need sharpening, last longer, comfortable writing, are environmentally friendly due to their synthetic nature, the synthetic rubber is more effective, and are stylish and moderns. Additionally, mechanical pencils can be reused and recycled. Over pens, the advantageous aspect is that they leave erasable marks.
However, mechanical pencils are relatively more expensive and need a constant supply of lead for the refill.
It is imperative to note that the material used and the procedure followed in the manufacturing process will determine the quality of a mechanical pencil.
This research paper comprehensively demonstrates the technical procedure followed when making a mechanical pencil.
Description of Components of a Mechanical Pencil
Plastic Body
The plastic body of a mechanical pencil is mainly made from high–impact ABS plastic. However, there are also metallic bodies. High impact ABS (Acrylonitrile Butadiene Styrene) plastic is considered the best in the collection of styrene plastics (ABS Material, 2012). It is hard, tough, firm, durable and possesses extremely better chemical resistance and dimensional features.
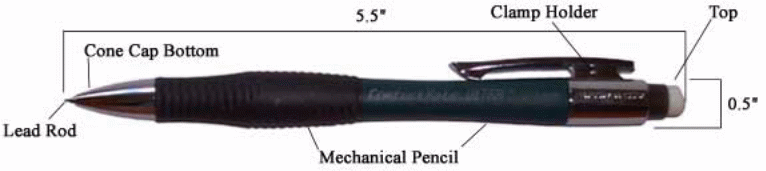
Plastic Tube
The plastic tube found within the mechanical pencil is used to hold leads for a refill once the original tip is exhausted. Some manufacturers used a clear plastic tube to hold lead.
Eraser
An eraser is a detachable part of the pencil made of rubber plug, which is fitted at the lead rod at the back of the mechanical pencil. The eraser is used to remove graphite marks on paper or wood surfaces. The eraser may be white in color.
Metal
The lead advancing mechanism is made from metal that operates on a spring platform. As such, the user can press the pencil button located on the top to ensure that the spring presses the graphite into a locked spot.
Description of Specific Parts of a Mechanical Pencil
The rubber-gripping barrel
This is the part designed as a holding device for the mechanical pencil. It fits between the thumb, middle finger, and the index finger when writing, sketching, or drawing. The rubber-gripping barrel is fitted around the glass barrel. The design allows it to taper at the center and creates a firm grip with the middle finger. This part is also made of a ribbed casing to improve gripping capabilities. The ribbed casing is manufactured from soft rubber made to ensure comfort when the mechanical pencil is held for use for a prolonged time. The measurements can range from 1.7 inches while the diameter is usually 0.5 inches (Dunleavy, 2015).
Cone Cap
This is a hollowed cast casing made to offer protection to the mechanical graphite holder found inside. It also aligns the other graphite rods with the lead rod outlet. The cone cap is normally manufactured from high-quality impact plastic, usually coated with silver chrome. The cone cap screwed in the right direction on the barrel. They usually measure 0.75 inches with a diameter of about 0.375 inches to 0.125 inches in diameter.
The lead rod outlet
This hollow cast casing is made to hold lead rods. It also strengthens the graphite and protects them from breakage when in use. The lead rod outlet, just like other parts of the mechanical pencil made of plastic, is also manufactured from High impact ABS plastic. It is then coated with silver chrome for aesthetic. A plastic fitting is used to join the cone cap with the rest of the component. The cone cap is about “0.086 inches for the length while the diameter ranges between 0.078 and 0.0313 inches” (Dunleavy, 2015, p. 5).
The Assembly Barrel
This component of the mechanical pencil is a hollow plastic casing made to cover the internal systems of the pencil. It holds the lead rods and eraser. The barrel part also has a pocket clamp holder. It is made to lie on the index finger for balancing the mechanical pencil during drawing or writing. It also a part of the gripping barrel measures about 2.75 inches in length with a diameter of 0.5 inches. The barrel has four main parts, including the pocket clamp holder, the hourglass barrel, the lead rod ejector, and the detachable eraser.
The hourglass barrel
This is also a hollowed cast casing made to hold “0.02-inch graphite rods and to sustain the balancing position of the mechanical pencil on the index finger or the knuckle during drawing or writing” (Dunleavy, 2015, p. 8). It also manufactured from high impact plastic. Except for the graphite rod outlet and the detachable eraser, all other parts of the mechanical pencil join the hourglass barrel. In fact, the hourglass barrel is “the main component or body of the mechanical pencil” (Dunleavy, 2015, p. 8). The length of the hourglass is usually about 1.75 inches with a diameter range of 0.5 inches to 0.375 inches.
The pocket clamp holder
This part fastens the mechanical pencil to the pocket by clamping it. It has a cap that is attached to the top of the hourglass barrel. The device is also fitted with an elastic-plastic clamp to allow it to lengthen from the cap.
This component allows the mechanical pencil to clamp around the pocket when it slides between the stretchable plastic clamp and the hourglass barrel. This component is also made of high impact ABS plastic and may be coated with a silver chrome for aesthetic. It is about 1.75 inches in length and 0.5 inches in diameter.
The lead rod projector
The retracting component of the mechanical pencil holds the eraser and ejects the graphite rod via the graphite rod outlet found at the rear of the mechanical pencil. It is also made from high impact plastic while fitted with internal features to connect with the hourglass barrel. This component measures 0.25 inches in length and a diameter of 0.375 inches.
The removable eraser
The detachable eraser, usually made of rubber, is a rubber plug that is inserted at the rear end of the mechanical pencil. It is used to erase graphite particles on the paper. The normal length for the eraser is about 0.375 inches in length with a diameter of 0.25 inches.
The Plastic Body
Type of Plastic Used
Although some mechanical pencils have metal body parts, plastic is widely used on most body parts of mechanical pencils. Specifically, durable high impact ABS plastic is commonly used. ABS is a thermoplastic resin that meets specific quality requirements for a mechanical pencil plastic body.
Resource Gathering and Processing
All materials for the manufacturing of mechanical pencils are sourced from different sources. Plastic materials are made from polymer after several chemical and mechanical processes. The metal parts, for instance, are mainly extracted from iron ore from the Earth.
Plastic
Mechanical pencil manufacturers commonly use the high impact Acrylonitrile Butadiene Styrene (ABS) plastic for the plastic components of the pencil.
The initial raw material for High impact ABS plastic is hydrocarbon products obtained from oil. Crude oil is extracted from the earth’s crust and pumped to factories where it is refined. Through fractional distillation, different products are obtained from crude oil, including propane and ethane. Propane and ethane are chemically treated and transformed into monomers acrylonitrile, butadiene, and styrene used in the manufacturing of high–impact ABS plastic. Monomers are then polymerized through subjection to additional condensational reaction processes. The processes are hastened by the use of catalysts (American Chemistry Council, Inc., 2015).
For variation in plastic property, certain monomers are combined to form a specific plastic with preferred features. The rigidity or flexibility of a specific plastic depends on the level of temperatures and chemical treatment that plastic is subjected to during processing. Additionally, modification can be applied to improve impact resistance, heat, and enhance the toughness of the ABS plastic (American Chemistry Council, Inc., 2015).
Alternatively, manufacturers for mechanical pencil can use recycled high-impact ABS plastic since the plastic is highly recyclable. Typically, there are two recycling procedures adopted by manufacturers of high-impact ABS plastic. The two reprocessing methods include mechanical recycling and the use of solvents. Precisely, the solvent-based method is used in the recycling of highly painted high-impact ABS plastic to ensure that the loss of butadiene is as minimal as possible. Notably, empirical experiments have revealed that reprocessing of the high-impact ABS plastic does not alter its microstructure (Hotes, 2015). During recycling, nonetheless, specific conditions must be put in place and purification must be done optimally for high-quality ABS plastic.
Once the raw materials for high-impact ABS plastic are gathered and the plastic processed, the plastic is compressed into plastic pellets that are then shipped to the mechanical pencil manufactures.
Synthetic rubber
Rubber is majorly obtained from latex, which is extracted from the back of the rubber plant, Ficus elastic that either grows naturally or is cultivated. The extraction process involves cutting slanted strips of the back and requires some expertise. The thickness of the cut determines the latex flow and if done haphazardly, the cut can damage the tree. Once the cut is made, latex is collected with containers that are placed at the bottom part of the cut.
The collected latex is then transported to the factory using tank tracts. At the factory, the latex is put in a centrifuge machine that reduces the water concentration in the sap. As a result, the rubber content in the sap increases to approximately 60%. The next step involves treating the sap with acid to get rid of a larger amount of water.
Alternatively, synthetic rubber can be manufactured from synthetic latex. The two elementary components used to obtain synthetic latex are butadiene and sterol. While butadiene is acquired from oil in gaseous form, the sterol is removed from oil and coal. The two substances are chemically treated, by soap solutions, aiding the creation of rubber. Further, processes are employed to enhance the formation of colors. Later, when the latex is properly standardized, stopping reacting inhibitors are added. To shorten the latex, it is put in acidic solutions. Once the latex is curtailed, it is thoroughly washed to get rid of unwanted chemical substances. The latex is then subjected to regulated heat and pressure to obtain granules.
Metal
The metallic raw material used in making mechanical pencils originates from the earth’s crust. Fundamentally, all pure metals are extracted from ores (minerals). In most cases, iron appears naturally as compounds of rocks and not pure metals. The rocks containing the metal ores are made of different minerals formed through the cooling of liquid magma by pressure, temperature and other physical effects. It is imperative to note that the properties of pure metals can be improved by making alloys, which are commonly used in making mechanical pencils (Zimmerman & Weindorf, 2010).
The iron ores are located beneath the earth’s surface and, therefore, the process of excavation requires the use of heavy machinery such as bulldozers, drills, trucks, and lifters. Essentially, the machine helps in removing the layer of the earth’s surface, breaking hard rocks, recovering and transporting the ores and reclaiming the land after the mining process. Further, rather complex processes are followed to remove slag from the ore. This involves physical-chemical and electrical procedures that ensure that the level of slag is as less as necessary (Zimmerman & Weindorf, 2010).
After the extracted ore is relatively slag free, it is melted, and mixed with carbon and other substances to make a harder iron alloy, steel, which is shipped to mechanical pencil manufacturers.
Graphite
Majorly, graphite occurs in metamorphic rocks like marble, gneisses, and schist. Graphite molecular structure enhances writing. The non-metal is made of six carbon atoms that are tightly held together in extensively spread out strata with weak bonds (amid the strata) and strong bonds (inside the strata) (University of Waterloo, 2006).
The extraction of graphite is dependent on either the degree of rock (containing the graphite ore) weathering or the graphite ores nearness to the earth’s surface. As such, the underground method is used for rocks that are relatively far from the earth’s surface. On the other hand, the open-pit method is used when the ore is near the earth’s surface (University of Waterloo, 2006).
Open-pit method
In the open-pit method, the minerals are extracted from open quarries. For this technique to be used efficiently, graphite ores have to be in close proximity to the earth’s surface. Additionally, the earth layer covering the ores must be reasonably thin. In such conditions, miners use drills or dynamite explosives to break the rocks. Moreover, water and air are forced into the cracks further splitting the rocks. Once the ore is freed from the rocks, it is floated. The method of bringing the graphite to the surface depends on the sophistication of the mining country. For instance, the developing countries using less sophisticated methods like using a pick, shovel, and laborer pushed vehicles (University of Waterloo, 2006)
When the graphite ores are situated far in excessive depth from the earth’s surface, the underground technique is employed. Underground mining is further divided according to the positioning of the ore underground to include drift, hard rock, and shaft techniques. In the shaft mining method, tunnels are constructed to be used by miners and mining tools. Additional shafts are used to move graphite ores over to the surface using rather heavy equipment. The third category of tunnels is used for ventilation. For ore that is situated parallel to the earth’s surface, the slanted shaft method is employed. For mountainous areas, tunnels are dug lower than the ore stratum to use gravitational pull during extraction (University of Waterloo, 2006).
Alternatively, graphite can be manufactured artificially by subjecting amorphous carbon to extremely high but monitored temperature. Amorphous carbon used in the manufacturing of synthetic graphite can be obtained from petroleum, coal, among other artificial or natural substances. Additionally, synthetic graphite can be produced by direct precipitation of special carbon (graphitic) from pyrolysis of gases like acetylene. Since graphite is a carbon, only carbonaceous materials are used to make artificial graphite (Asbury Graphite Mills, Inc., 2006).
Precisely, petroleum coke is commonly used in the extraction of synthetic graphite. However, the selection of the carbon must be done prudently to produce the most appropriate graphite to be used in the mechanical pencil. Once proper carbon is selected, it is subjected to varied and complex processes to manufacture graphite (Asbury Graphite Mills, Inc., 2006).
Processed graphite is then transported to the mechanical pencil manufacturer where it is mixed with clay to manufacture lead shots.
Mechanical Pencil Manufacturing Step
Several steps are involved in the manufacturing of a mechanical pencil. The initial steps involving sourcing and processing of raw materials to make distinct components, including plastic, metal, and rubber. All these components of a mechanical pencil are assembled into a final single product and then shipped for distribution to users (Gershenson, Prasad, & Allamneni, 1999).
Mechanical pencils are designed in different shapes and sizes to meet various purposes (Poole, 2014). Thus, the major factor that influences the design and shape is the purpose and to some extent user preferences.
The plastic consists of a hollow barrel, lead control mechanism and removable eraser held at the top. The eraser is normally removed to insert the graphite.
The production processes involve grouping different components of mechanical pencils together based on their manufacturing stages and then every production process is increased to account for various tasks and other minor tasks of every stage (Gershenson, Prasad, & Allamneni, 1999). Components such as the tip or cone, hollow plastic barrel, plastic cap, and plastic lug unit are made from injection-molded plastic. In addition, further tasks are noted during the injection of the molding process, which include dyeing, determining the ejector pin and using the attached cylinder to melt the plastic (Gershenson et al., 1999).
As previously noted, many processes are involved in the production of a mechanical pencil, and they usually start with the manufacturing of each component separately.
The Making of the Shaft (plastic parts)
Once polymers have been created, they are then sent to the manufacturers in the form of compressed plastic pellets.
Once the pellets have been received, the manufacturer then melts them down and starts the process of injection molding.
By subjecting the melted polymer through injection molding, mechanical pencil manufacturers can manipulate the shape of the plastic to meet various shapes and sizes required for different components. The barrel is made to hold at least five pieces of lead graphite.
Every barrel of a mechanical pencil is produced in a specific diameter big enough to accommodate between five and ten pencil lead steadily. The hollow barrel is made from metal, rubber, or plastic.
The pencil tip of a mechanical pencil is “made with screw grooves” (Jet Pens, 2015, p. 1). Manufacturers have noted that screw grooves are the most secure technique to hold the tip of the pencil to the barrel.
The plastic part is manipulated to produce the desired shape such as a cone for the tip. These shapes are mainly for aesthetics. Further, it is narrow at the end to ensure that the tip can only accommodate single graphite at a given moment.
The Making of the Metal Parts
This part of the mechanical pencil is made from manufactured steel obtained from suppliers. The steel is mainly high carbon metal, which must be further processed into the thin wire to make springs. The springs are heat-treated to ensure that metal is relaxed and ensure that they can retain their shape every time they are flexed.
The thin wire is passed through an automated machine that winds it at a given point to make highly elastic compression springs.
The finished springs are then inserted to the right part of the mechanical pencil as a distinct component.
The Making of Eraser
Once the rubber has been delivered at the eraser factory using a tank truck, it is mixed with other materials, including pigments, sulfur, pumice, vegetable oil, and other chemicals that change properties of the final substance.
Truck tanks normally deliver the synthetic rubber as a liquid or powder. As such, it is easier to mix. Natural rubber is delivered in bales and normally requires pulverization to form a powder. Alternatively, it can be dissolved to make a solvent prior to the mixing process.
During the heating process, sulfur hardens the mixture to make it more stable. An extrusion process is applied to make plugs that are attached to the pencil once the product is complete. The heating process results in a soft solid mixture, which is passed through a die to produce a long cylinder. The long cylinder is cut several times as it comes out of the die. This process results in the formation of plugs.
Flats are made from an injection molding. These flats are usually not attached to the pencil. At this point, the mixture is usually a warm liquid that forms molds and then cools to create a solid. Flats are then obtained from the molds.
Once the plugs have been made, they are transported directly to the pencil manufacturer. The ferrules – small cylindrical metal cases, are used to attach plugs to the pencils. Aluminum is normally used for manufacture ferrule, particularly for relatively cheaper pencils. Alternatively, pencils that are expensive use painted brass as ferrules. Glue or little metal prongs are used to attach ferrules to the pencil while the inserted plug in the ferrule is normally clamped around the pencil.
Mechanical pencil manufacturers can mark their names on the pencil flats through stamping. Stamping involves pressing a stamp with ink on the pencil eraser. Other manufacturers use screen printing to mark their products. An ink roller moves over the patterned piece of silk or any other piece of materials used to conceal the eraser. Embossing is applied in three-dimensional pencil markings as the eraser is chopped with a sharp die. Once the process is complete, the flats are packed for shipping to distributors and end-users.
Manufacturing of eraser requires quality control. The processes are highly automated to produce the best products in large numbers. Today, experienced manufacturers have automated several processes using various techniques to eliminate multiple inspection stages.
Eraser manufacturers have learned to source their products from the best raw materials and suppliers. New products or substances are subjected to thorough quality checks before they can be used just to ensure they meet quality standards.
The manufacturers only assess a small number of erasers to establish their quality standards, including physical properties. All flats must have the same size to ensure they fit into the boxes while plugs must maintain the right measurements to fit into ferrules. Erasers should be sufficiently hard, but not too hard or too soft to ensure they work well.
The Making of the Graphite
Powdered graphite and fine clay are usually mixed with water and stirred to ensure a uniform mixture. It is imperative to recognize that the ratio of the clay and graphite are responsible for determining the hardness of the resulting lead and finally the pencil.
The next process involves pressing the mixture of graphite to produce long strings, which are then chopped to specific lengths and then collected. These lead components are still soft and easily bend and, therefore, must be kept straight during handling.
The cut lead pieces are kilned to harden them for about 24 hours to ensure that the mixture is dry and properly fused. The lead is then immersed in wax to ensure fine, smooth and strong lead. Once the lead cores are ready, they are prepared for subsequent assembling.
Graphite Variations
It is imperative to note that modern mechanical pencils do not have the toxic lead because they are manufactured from graphite and clay or plastic polymer materials. Relative to other regular pencils, mechanical pencils are made to produce small marking types. It is possible to refill mechanical pencils once the lead is exhausted. However, inexpensive types can be disposed of and recycled once they are empty.
Diameter
These types of pencils only have one lead diameter. However, some models of mechanical pencils have many mechanisms located inside the same barrel housing to ensure that a greater or varied thickness can be attained ranging from 0.3 mm to 0.7 mm. In some instances, 1.00 mm may also be found, they are not common.
Mechanical pencils are built with different lead diameters to ensure that they accommodate the diverse needs and preferences of users, as well as account for the type of pencil model. Diameters of 0.5 mm and 0.7 mm are the most common because their widths ensure that users can achieve exact writing and sketching. Other limited diameter leads include 0.2 mm and extremely rare leads of 0.1 mm from specific manufacturers like Pentel.
Mechanical pencils with small millimeter leads can carry several leads in the barrel. These models are made to minimize refill frequencies. However, there are few exceptions, which can only hold a single lead, Pentel 350 E. refilling the pencil involves inserting the lead tube into the barrel once the original one is worn out or fully consumed.
Hardness
Mechanical pencils are made with varying degrees of hardness just like some non-mechanical pencils. However, the hardness of the pencil is influenced by user preferences on durability and darkness. Manufacturers generally use a lead with similar density except in some pencils with greater thickness.
Pigments
Colored lead mechanical pencils are not common, but they are available. Twistable mechanical pencils manufactured by Crayola, for instance, are some examples of colored mechanical pencils with both erasable and non-erasable features. They also possess a mechanical feed system, but they lack refill leads. In the recent past, however, many companies such as Pilot, Pentel, and Uni-ball have ventured into the manufacturing of colored mechanical pencils. However, they offer a limited variety of diameters from 0.5 mm, 0.7 mm or two mm. Other companies, such as Koh-i-Noor, currently produce colored mechanical pencils with several diameters and replaceable leads.
The Advancing Mechanism
The lead advancing mechanism is made from metal that operates on a spring platform. As such, the user can press the pencil button located on the top to ensure that the spring presses the graphite into a locked spot.
The subsequent process involves the transportation of the spring platform component to an assembly factory for additional advance processes in the production of the mechanical pencil.
It is imperative to recognize that mechanical pencils can be different based on their mechanical systems. First, the system can hold the graphite and effectively move it forward. The second type of mechanical system can only hold the graphite in a fixed position.
A screw-based mechanical pencil moves the graphite by moving and twisting the screw – a process that results in the movement of the slider down the barrel. This type of mechanical pencil was the most common in the early 20th century. Most of these mechanical pencils had a one-way locking system to ensure that the lead can move back into the barrel.
Mechanical pencils with lead holder or clutch usually have thicker leads measuring between 2 mm and 5.6 mm. In addition, they normally hold only a single piece of graphite at any given moment. An ordinary clutch pencil is triggered through a push on the eraser cap at the top of the pencil. The jaws located inside the barrel open to allow the graphite end to move freely via within the barrel, or to move back into the barrel.
The lead drops out without resistance when the pencil is pressed and the jaws are released. During this process, it is impossible to control the forward movement except by an external mechanism. This mechanism can be attained by maintaining the tip of the pencil slightly above hand palm or on the surface of work. Some mechanical pencils are fitted with systems that incrementally move the lead. Alvin Tech-Matic lead holder, for instance, is such a mechanical pencil. However, such pencils are not always categorized as other mechanical pencils with propelling systems.
Mechanical pencils are also ratchet-based. These are generally clutch pencils, which have about two to three minor jaws within to hold the lead with a ring found at the tip. These jaws are manipulated by “a knob found on the end or at the side of the pencil” (Veley, 2011, p. 36). A push on the button results in movement of the jaws forward and separation and consequently the graphite advances.
A mechanical movement is noted when the button is released causing the jaws to move back. The lead retainer, which is a small device made of rubber, is used to maintain the lead at the right position and stops it from falling freely out of the barrel or moving back into the barrel as the jaw movements to retain the grip. In other mechanical pencils, a perfectly fitted metal sleeve is used to control and support the graphite, and they do not necessarily require a rubber retainer. In a single kind of a ratchet-designed pencil, shaking the pencil normally causes the load within to cause mechanical movement in the cap.
Further, such pencils may be fitted with a button at the top or side to ensure that the user can control the lead when required. Another mechanism is used to move the lead automatically. In this pencil, a ratchet is used to move the lead, but a minimal amount of friction is applied to prevent the lead from sliding back into the barrel. The nib consists of a spring collar that is pressed when the lead is finished at the top to extend it after the pressure is applied and released (Veley, 2011).
In other complex designs, the ratchet mechanical pencil can rotate the lead to 60 in the clockwise direction each time the lead is put on the paper to ensure that it wears out in an even manner. As such, the lead is normally narrower at 50 percent relative to other regular moving mechanical pencils. Thus, they have a more uniform thickness of written lines. This design emanated from Mitsubishi.
Assemblage
In this process, all barrels are attached to the advancing mechanism and then the tip of the pencil is then screwed at the lower end of the barrel while the pencil eraser is attached at the upper end of the barrel.
In producing mechanical pencils, some factories can conduct all their processes in-house using their specialized plants. Conversely, other manufacturers may sub-contract specific components for manufacturing. For instance, a company may choose to mold its own plastic barrels, fix the metal parts, tips among others or the plant may be specifically for assembly operations.
Some manufacturers mode their barrels and tips outside the factory and import other components, such as metal parts. At the same time, components that advance the lead may be assembled and fixed into the tip by specialized, automated machines found in the plant. They also do the final assembly by hand to ensure that the quality of mechanical pencils is maintained because the assemblers physically assess the pencils. As such, they ensure that all mechanical pencils distributed to end-users are perfect quality products.
The Tip Assembly Machine works on the shank and put them on the tip cone while applying pressure to create a grip on the tip.
Influences on the design
For several centuries, manufacturers and designers of mechanical pencils have found ways to improve their products and ergonomically fit (Petroski, 2010). As such, designers have introduced new features that are more advance to mechanical pencils. Today, there are mechanical pencils for students, executives, everyday carry, ergonomic, high precision, lead guarding, shaker, and mini mechanical pencils.
Retractable Tip
New designs of mechanical pencils have retractable tips to ensure that they are safe for users and pockets.
Lead Protection
Sleeves are designed to protect the pencil leads from “breaking, specifically the part of the lead-covered” (Jet Pens, 2015, p. 1). The sliding lead sleeve allows the paper surface to restrict the lead sleeve back into the tip of the mechanical pencil when the lead is used. Consequently, users can continue using the sharp tip while the lead is protected. Other forms of mechanical pencil designs have even more advanced protection systems. The platinum OLEeNu, for instance, is designed with “in-built spring to protect the pencil tip from the pressure that emanates from writing” (Jet Pens, 2015, p. 1).
Some mechanical pencils such as “ZeroShin and Platinum OLEeNU have dual-clutch” (Jet Pens, 2015, p. 1). This special component is designed to allow users to use up all the lead until the last bit. The dual-clutch mechanical pencil is designed to ensure that the user exhausts virtually the whole lead rather than waste about 15 percent (Jet Pens, 2015).
Auto Lead Rotation
It ensures that the lead remains sharp and consistent in Uni Kuru Toga mechanical pencils with this feature (Jet Pens, 2015). A ratchet mechanism allows the lead to rotate narrowly each time the lead is in use. Consequently, lead uniformly wears out on every side, resulting in a uniform, consistent writing.
Conclusion
These research papers have explored how a mechanical pencil is made. It covers initial activities, including sourcing and extraction of raw materials such as plastic barrel, plastic tube for the graphite, eraser and other mechanical systems.
Several components are produced in the process of manufacturing mechanical pencils. It is preferred because of the solid marking core made of graphite referred to as lead. Various assortment of colors is also available. These pencils have the ability to produce consistent lines in the required thickness without the need to sharpen them. Consequently, they are available for a wide range of purposes, including regular writing and technical drawing. Mechanical pencils are considered the best alternatives to wooden pencils and pens because they do not require sharpening, are erasable, and considered comfortable and durable among other benefits.
It is also imperative to recognize that manufacturers and designers of mechanical pencils have consistently focused on innovation and refinement to make better products that cater to diverse purposes and user preferences.
References
ABS Material. (2012). ABS Material. Web.
American Chemistry Council, Inc. (2015). How Plastics Are Made. Web.
Asbury Graphite Mills, Inc. (2006). An Introduction to Synthetic Graphite. Web.
Dunleavy, B. (2015). Technical Description of the Mechanical Pencil. Web.
Gershenson, J. K., Prasad, G. J., & Allamneni, S. (1999). Modular Product Design: A Life-cycle View. Journal of Integrated Design and Process Science, 3(4), 1-9. Web.
Hotes, T. (2015). ABS Resin Plastic – Features, Limitations and Variations. Web.
Jet Pens. (2015). Guide to Mechanical Pencils. Web.
Petroski, H. (2010). The Pencil: A History of Design and Circumstance. New York: Alfred A. Knopf, Inc.
Poole, S. (2014). I Can Never Have Too Many Mechanical Pencils. Web.
The University of Waterloo. (2006). Earth Sciences Museum. Web.
Veley, J. A. (2011). The Catalogue of American Mechanical Pencils. Dayton, OH: Greyden Press. Web.
Zimmerman, A. J., & Weindorf, D. C. (2010). Heavy Metal and Trace Metal Analysis in Soil by Sequential Extraction: A Review of Procedures. International Journal of Analytical Chemistry, 2010(387803), 1-7. Web.