Introduction
The global market of the 21st century is characterized by the gradual elimination of trading borders, increased deregulation, a greater diversity of products available, and decreased costs in communication, which lead to a more competitive environment (Forman & Elias, 2016). With the majority of markets already explored and classified as Red, the producers must engage one another not only by increasing the quality of the product but also by decreasing the costs associated with the enterprise (Forman & Elias, 2016). Companies in the domestic market have to face not only local competition but also that presented by multinational corporations located abroad. As a result, there is a dire need for better and sophisticated costing systems.
Costing systems serve as important decision-making tools in an organization, as they help in placing of new products, influence the choices to reduce or even terminate products and services, and define the selling prices by providing reliable information regarding their industrial costs and profitability ratings (Altawati, Kim-Soon, Ahmad, & Elmabrok, 2018). In addition, costing systems can accurately predict and monetize customer satisfaction as an important factor for the viability of companies and their products. As meeting customer expectations for the product is key, there is strong pressure for all organizations to increase productivity while reducing prices. Thus, obtaining a way to more accurately estimate the costs of every operation has become a strategic objective. Activity-Based Costing (ABC) has emerged from the need to do so and serves as a viable alternative to the traditional costing methods implemented today (Altawati et al., 2018). The purpose of the system is to accommodate the new management systems in place, such as Just-in-Time (JIT), Total Quality Management (TQM), and other frameworks that have become increasingly popular in many companies (Altawati et al., 2018).
The company of choice that uses ABC is Illycaffee. It is an Italian-based coffee company that has recently expanded to include wines in its product line, with both lines of products providing a relatively equal profit. The company employs over 1,100 workers and largely focuses on the Italian market, though its products are also exported to the rest of Europe as well as America and East-Asian countries (Illy, 2017). The purpose of this paper is to evaluate the implementation of the ABC system in their manufacturing of coffee and wine.
Illycaffee Profile
Illy coffee is an Italian coffee-roasting brand with a specialization in producing coffee known as espresso (Illy, 2017). In addition to coffee, the company started manufacturing wine after purchasing wineries in Montalcino and Barolo, in order to complement the line of products offered to the HORECA (Hotels, Restaurants, and Cafes) segment of the market (Illy, 2017). The company was founded in 1933 and is still run as a family company, with members of the Illy family presiding over as members of the directorial board (Illy, 2017). The company’s revenues have seen impressive growth in the last 5 years, with the dynamics showing a 5% yearly increase, with a total of 460 million euros as of 2016 (Illy, 2017). As it stands, the company employs over 1,100 workers in both areas of production. The company does not grow its own coffee, instead preferring to import single-origin arabica beans from Brazil, Guatemala, Colombia, Costa Rica, Ethiopia, and India (Illy, 2017). Thus, the manufacturing component of the company revolves around working with coffee beans as well as a growing, seasoning, and bottling wine.
Although the expansion into wine and other related products happened around 2016, the company started adopting advanced methods of accounting, quality control, and supply in 2008, in the wake of the world economic crisis, when dropping sales and increased competition landed a hit on Illy’s profits (Illy, 2017). The adoption of JIT, TQM, and ABC was a complex measure that lasted between 2009 and 2010, when the company underwent a reorganization of its production values, streamlining processes, and investing in corporate training (Illy, 2017). As a result, some positions were cut, others were replaced, and all processes in coffee production were streamlined. The same reorganization of wineries occurred in 2016, after Illy acquired businesses in Montalcino and Barolo, in order to identify the products that had to be kept and ones that could be safely discarded due to low sales.
Definition of ABC
Activity-based costing is a method that involves the assignation of specific components of manufacturing, which includes activities, tasks, acquisitions, services, materials, and products (Altawati et al., 2018). It is based on several parameters, which include the following (Altawati et al., 2018):
- The activities necessary for performing a certain manufacturing process;
- Resources consumed by these activities (raw resources, human resources, instruments, equipment, etc.).
The differences between ABC and traditional cost accounting lie in the precision regarding the need for said allocation (Altawati et al., 2018). Traditional accounting often utilizes arbitrary percentages to cover indirect and overhead costs. As a result, certain processes and activities receive more than they require or are worth, while key processes remain undermanned and underfunded (Altawati et al., 2018). Since both ABC and traditional accounting are meant to estimate the costs of sold goods and the gross margins, the results may differ drastically one from another. This creates major discrepancies, especially in companies where it is necessary to know the exact costs of production in order to determine which products are profitable and which ones are less successful (Altawati et al., 2018).
In the scope of Illy, the need for ABC in comparison to traditional costing is obvious – the company has a myriad of products, ranging from different coffee brands to wines (Illy, 2017). This differentiation of similar offerings to the market requires close supervision of their performance in relation to production costs. Since the company also was planning to move to JIT and TQM at the same time, the provided data could also be used for ABC. For the sake of focusing the paper on the specific line of manufacturing processes, only the coffee-roasting branch of Illy’s production undergo review and analysis. The process of implementation of the system is explained in greater detail in the following chapters.
ABC and its Implementation in Illy
Identification of Processes
Initially, Illy was a company that produced roasted coffee from imported raw material, with a greater focus on coffee capsules, which are either plastic or metallic packages that seal ground or roasted coffee in a vacuum, thus preserving its qualities while protecting it from the outside elements (Gregori, 2018). This sector of activity is comprised of various aspects of labor, including the procurement of industrial equipment, the manufacturing processes, the acquiring of raw materials and subsidiary products, contracted and direct labor, as well as many other subprocesses (Gregori, 2018). In addition, the company produces a variety of alcoholic beverages, which include wines, port wines, champagne, and other varieties (Bendeich & Landini, 2018). The sales volumes for the company are relatively equal in both directions, meaning that no one area has a direct priority over the other. Marketing and distribution are, at the moment, aimed at the Italian peninsula and neighboring countries, while also exploring larger markets, such as those found in China, Russia, and the US (Illy, 2017). Being a premium coffee brand, Illy naturally aims at the upper-middle class of customers as well as the high-end restaurants, clubs, bars, and cafes that can afford to buy coffee in greater volumes.
The company does not exert direct control over its production, as all industrial components are located in facilities separate from its HQ in Trieste, Italy (Illy, 2017). At the same time, the terminal part of the process, which includes the dispatch of merchandise, is a combination process in terms of the use of facilities, employment, and equipment. Thus, the marketing, distribution, and dispatch departments are conjoined. The production of coffee is commercialized via several formats, which follow roughly the same parameters both in the domestic and foreign markets (Illy, 2017). The two channels of distribution include HORECA and modern distribution through retail companies and shops (Illy, 2017). Abroad, Illy completely relies on foreign distributors in order to promote its brand. Although the production of coffee was initially focused on capsules, it is not the only activity developed by the company, as resources are being shared not only between different activities located in the same area but also by different business units. Such conditions vouch for the adoption of ABC, as activities related to the production of any given product have to be evaluated both with the associated costs and the impact they make within the organization.
The ABC framework identifies the list of main and secondary activities that enter the cost evaluation process. Main activities (MA) are critical for the production of the main product of Illy, which is capsules. They have a linear direct relationship with the product, which is verified not only on the cost levels but also affects the quality and the intrinsic constitution of the final product. These activities are as follows (Gregori, 2018):
- Green coffee reception. Conducted at the second coffee warehouse (CW2);
- Green coffee storage. Facilities utilized for this stage are CW1 and CW2;
- Densiometric treatment. Conducted in the densiometric treatment room;
- Blending and roasting. Conducted in the roasting room;
- Grinding. Facilitated in the grinding room;
- Degassing. Conducted in the ground coffee-room;
- Packaging and encapsulation. Organized in the capsules packaging room.
- Semi-finished packaging, placement in cardboard, and final packaging. Also happens in the capsules packaging room.
- Expedition. Conducted in the final product warehouse.
The majority of these activities are contained to a singular industrial building within the company, physically separated into different activity sites. These activities are common to all coffee companies and products, ranging from activities 1 (reception) to 5 (roasting). The roasting stage is what separates most products by allowing the coffee beans to acquire different tasting qualities (Bottazzi, Farina, Milani, & Montorsi, 2012). Illy has 6 groups of products, which constitute complementary activities to the main processes (Gregori, 2018):
- Bulk coffee packaging. Is utilized for HORECA, domestic, and export channels.
- Coffee packaging for HORECA. Utilized in HORECA and vending machines.
- Coffee POD packaging. Domestic and export channels.
- Coffee 250g bag packaging. Domestic and export channels.
- Coffee sachets packaging. HORECA and export channels.
- Coffee capsule packaging. Domestic and export channels.
Thus, it is possible to see that the process and activities used to create different types of coffee products are similar at stages 1-5, with the first differentiation occurring during the packaging state. They use the same resources at the level of facilities, equipment, and labor. At the same time, there is a set of activities common to several organization processes that influences the production process. These activities include the purchasing and receiving of raw materials, equipment, and facility maintenance, as well as quality control. These actions constitute secondary activities to be included in the ABC process, and are listed below (Gregori, 2018):
- Purchasing of green coffee. The coffee is procured from external suppliers in Brazil, Guatemala, Colombia, Costa Rica, Ethiopia, and India;
- Purchasing of subsidiary products. These include packaging materials, capsules, tools, and miscellaneous items.
- Reception of subsidiary products and coffee. These are delivered to the production facility’s warehouse;
- Equipment maintenance. Is subdivided into two types, one being the routine maintenance provided during specific time periods in exploitation. The other is emergency maintenance, conducted in an event of an accident or breaking;
- Equipment cleaning and sanitation. Conducted in accordance with technical norms and regulations, as well as internal company standards;
- Quality control. In Illy, quality control is done according to the principles of TQM, meaning that there are process owners and intermediary control points at the beginning and the end of each process.
The production of coffee capsules is a complex process that includes a varietyof upstream production subprocesses, which are developed by suppliers. These activities include the creation of plastic capsules using the injection method (Gregori, 2018). The capsules are later being filled with coffee on an industrial scale. Coffee molds used in this activity are designed and provided by the coffee manufacturing company. At the same time, due to the lack of congruent activities related to the production of capsules that could benefit the coffee manufacturing company, it continues to order packages from outside organizations. Therefore, these activities are necessary to be accounted for, with their respective costs entering the ABC system. Due to their reliance on outside suppliers, these activities are called external activities (Gregori, 2018):
- Designing and developing the capsule;
- Protecting property rights for the appearance and functionality of the capsule;
- Producing the capsule for the purposes of coffee packaging.
The Implementation of ABC Methodology in the Company
The implementation of ABC involves two stages, the first one being the allocation of resources and activities, and the second one being the allocation of activities to products based on the definition of industrial costs (Gregori, 2018). As Illy transferred from traditional to ABC methodology, it evaluated all of the main, secondary, and external activities involved in the production of capsulated coffee, as demonstrated above (Illy, 2017). They also highlighted all the tasks performed in each activity. For these tasks, the allocation of industrial facilities, labor, and equipment was performed.
The costs associated with industrial facilities include rental values, electrical payments, maintenance of the facilities, and insurance. Due to the favorable conditions for Illy that allow annual renting, the payments covering these costs were easy to quantify and allocate to the activities pertaining to the building itself as well as in the scope of a more global enterprise (Illy, 2017). The activities behind energy consumption include the lighting, elevators, hoists, and social areas. The energy consumption of the equipment was calculated in accordance with its power on an individual basis and was not included in the building costs (Gregori, 2018). Maintenance costs were largely associated with repairs of the external, internal, and supporting structures. Equipment maintenance was calculated separately, based on the individual piece of equipment.
In regards to insurance, the company has to engage in numerous policies concerning various aspects of coffee production (Gregori, 2018). These include individual employee insurance, business activity, and profits insurance, as well as facilities, stocks, and other related activities. Illy bases its insurance policies on a case-by-case basis, with its allocation reflecting the importance of the insured process or object. The largest expenditures towards object-based insurance are placed on the industrial facilities, as they present the greatest environmental risks, which include gas emissions and waste generation. Civil liabilities are distributed between employees based on the industrial activity they are engaged in. The cost of amenities, such as water, was calculated according to the occupied area since the industrial processes require no water consumption (Gregori, 2018).
The labor costs associated with each task in main and secondary activities were calculated based on the amount of time for each function, as well as taxes, subsidies, social security, and AWT (actual working time) (Gregori, 2018). The working year included 11 months and 20 days, with 10 days allocated for various holidays throughout the year (Illy, 2017). Equipment-related costs were calculated with the expected depreciation of the tools, based on their service expectancy and legal requirements associated with their operation, as well as repair costs and all relevant interventions. Based on these parameters, it was possible to identify the hourly cost for each piece of equipment. The respective costs, thus, would be quantified based on tools and equipment assigned to conduct every activity in the list.
Finally, there are costs associated with external activities, which include the production of capsules. Since they are produced by suppliers, the costs associated directly with Illy include research and development, industrial property patent submission, and maintenance, as well as costs associated with creating molds to be used by the producer (Illy, 2017). All of these costs are fixed and do not absorb the internal resources of the organization, as they are specific to the activity of capsule production. They are also easy to identify and allocate within the ABC framework. Finally, there are costs associated with degassing and expedition of produce, which finish the process of cost identification for processes involving the production of coffee in capsules (Gregori, 2018).
The second phase occurs once all the resources were allocated to the activities involved in the production of coffee capsules. The driver activities involved include the produced roasted coffee, which is measured in kilograms, in relation to the produced coffee capsules that would act as units (Gregori, 2018). Industrial costs are calculated when the product is finalized and the values associated with the bill of materials and products are introduced. The ABC implementation flowchart can be found in Figure 1.
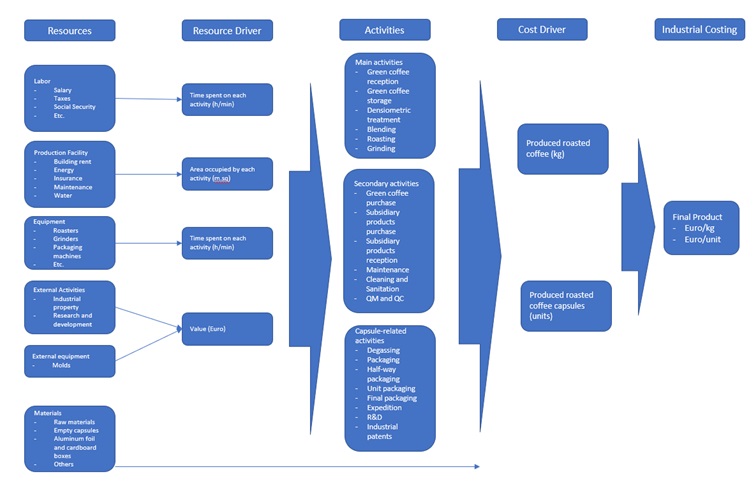
As it is possible to see, all the activities involved in the production of coffee capsules at Illy were successfully identified and attached to resources consumed in these activities. The second phase of the ABC flowchart shows how the activities were attributed through the cost drivers in order to linearly reflect the consumption (Mahal & Hossain, 2015). The total costs of production are calculated by evaluating the prices of materials according to the activities that consume them.
Results of the ABC Framework
Based on the analysis of activities and associated costs in the general manufacturing of the coffee industry by Illy, it is possible to see the distribution of resources based on their relevance in the cost structure of the final product. The highest share of distribution is associated with activities number 8 and 9, which constitute packaging and semi-finished packaging. Their part in the entire process stands for 23.8% for packaging, and 18.5% for semi-finished packaging. The rest of the activities’ percentages vary between 2% for the lowest (densiometric treatment), and 13% for the highest (expedition) (Gregori, 2018).
Using the ABC framework, Illy was capable of obtaining the industrial costs of their coffee products in different variants (Mahal & Hossain, 2015). Because of the similarities of the majority of the steps involved in the production of different variants of coffee, comparative results were possible to obtain by simply adjusting the differences in the final formula for the cost of the industrial product (Mahal & Hossain, 2015). At the same time, the bull of materials helps individuals distinguish the costs of raw material, capsules, and packaging materials. The largest component costs include the coffee itself (raw, green), the capsule, and the packaging materials. Together, they constitute about 82.6% of total material costs (Gregori, 2018). The information was obtained by comparing each individual position’s weight versus the overall costs as well as the relevance of the costs of the capsules, which constitute at least 50% of the total packaging material costs (Gregori, 2018).
Discussion
The results and the process provided above allows for gaining a perspective on the ABC methodology as it was used by Illy in order to gather information of high importance to the organization (Mahal & Hossain, 2015). The company used the framework in order to verify and conduct changes over the past few years and learn more about the development of their industrial activities. As it is possible to see, the ABC costing system provides valuable info that could be used for the decision-making processes in various domains (Mahal & Hossain, 2015). These include the definitions of costs in relation to sales prices and products, the identification of processes that require additional focus and effort, as well as the realities and needs of restructuring in some areas of the industrial unit. For example, the ABC schematic as well as the percentages of work and costs associated with different processes clearly indicate that packaging constitutes the most resource-intensive component in the business, followed by expedition (Mahal & Hossain, 2015).
Thus, Illy could focus on these actions by diverting human resources, material, and equipment from less occupied areas. In addition, the industrial model developed by Illy was then used to develop a list of specific instructions in regards to the distribution of materials, resources, and finances to accommodate each activity. The higher detail allowed for various venues for optimization of the process, broad analysis of the quality of the product during various stages, and the costs necessary to achieve it. Due to the broad range of products provided by Illy, the existing process of resource allocation was often overly complicated and largely ineffective. The implementation of the ABC costing system helped overcome that challenge by streamlining and simplifying the process of decision-making and information-gathering while improving the relevance and usefulness of the data (Mahal & Hossain, 2015). The ABC system, thus, is considered useful and effective by Illy due to its high adaptability to the needs of the company.
Advantages and Disadvantages of Activity-Based Costing
As illustrated by Illy, which was used as a case study, ABC provides tangible results to companies with long and complex manufacturing process lines. The costs provided to the company as a result of the analysis are both realistic and specific, thus allowing for a more precise pricing strategy for each product line. It also allows evaluating said products based on their cost-efficiency in connection to customer expectations – some products were eliminated from Illy’s line due to being too expensive for the results produced (Mahal & Hossain, 2015). Another strength of the ABC costing system is in the identification of inefficient processes, improvement facilitation, and identification of product margins (Mahal & Hossain, 2015). The elimination of unnecessary processes helps trim and streamline the production, as well as help understand and justify costs when manufacturing overhead. All of these strengths are closely related to the concepts of TQM and JIT, which require significant improvements from the traditional manufacturing that Illy implemented prior to innovations.
Nevertheless, just as any new system utilized in manufacturing, ABC comes with distinctive disadvantages unique to itself. The primary weakness is the time and costs associated with the collection and analysis of information (Altawati et al., 2018). In order to effectively utilize ABC in decision-making, a continuous process of data collection is required. This could only be achieved through automatization and dedication to IT personnel that could help facilitate said data collection. Specialists would also be required to comprise ABC reports, as normal accounting does not necessarily lend the necessary data. In addition, ABC methods are hard to transfer from one company to another, meaning a lack of uniform parameters to be used for external reporting.
One of the significant challenges associated with ABC is management training. Although the framework provides valuable data for decision-making, Illy’s managers and process owners did not have experience with the new systems and had to be retrained or replaced in order to make use of the new system (Altawati et al., 2018). The difference in performance standards, with an aim for improvement, resulted in the company having to adopt a change framework, in order to adapt the systems and people to the principles of JIT, TQM, and ABC (Altawati et al., 2018). It was a difficult task, as utilizing some of these systems without others would have resulted in suboptimal performance. The company had to subscribe to all of them or none. Fortunately, Illy managed to utilize all three, which greatly simplified and reduced the overhead costs for products, which resulted in the impressive 5% revenue growth seen from one year to the other (Illy, 2017).
Conclusions
ABC objectively represents the next step in the evolution of cost accounting, providing a more efficient way of data usage, collection, and cost assignment, based on the resources allocated to each specific process. Unlike traditional accounting, which sometimes allocates resources based on arbitrary views and preferences, ABC helps deliver a closer approximation to what is necessary for a specific process or product line. Illy provides an excellent representation of the utilization of ABC in its product line. The ABC flowchart provided in the paper demonstrates the streamlined allocation of resources based on resource drivers, activities, cost drivers, and industrial costs. The company used ABC for two specific purposes – improving the production processes through prudent resource allocation and removing or improving the products that were not cost-efficient in terms of both sales and production values.
At the same time, as demonstrated by the history of ABC’s implementation, the system is not without its inherent costs. In order to successfully implement ABC, Illy had to retrain its managers, hire external experts to teach the personnel the principles and functions of ABC, JIT, and TQM. In addition, the company was forced to undergo the process of change, which resulted in a degree of internal instability and a brief reduction of sales during the transition phase. Nevertheless, ABC is a must-have for companies that process large volumes of overhead production costs and seek to diversify their portfolios of products. Illy falls into this description perfectly, which is why the framework worked so well for the company, resulting in increased sales, reduced costs, better processes, and overall economic efficiency.
References
Altawati, N. O. M. T., Kim-Soon, N., Ahmad, A. R., & Elmabrok, A. A. (2018). A review of traditional cost system versus activity based costing approaches. Advanced Science Letters, 24(6), 4688-4694.
Bendeich, M., & Landini, F. (2018). Beyond coffee: Illy looks to wine and chocolate for stronger aroma.Reuters. Web.
Bottazzi, D., Farina, S., Milani, M., & Montorsi, L. (2012). A numerical approach for the analysis of the coffee roasting process. Journal of Food Engineering, 112(3), 243-252.
Gregori, G. (2018). Illy sustainability business model. Symphonya. Emerging Issues in Management, 1, 104-109.
Illy. (2017). Social value report. Web.
Mahal, I., & Hossain, M. A. (2015). Activity-Based Costing (ABC)–An Effective Tool for Better Management. Research Journal of Finance and Accounting, 6(4), 66-74.
Forman, C., & Elias, J. (2016). Coffee 2016. New Haven, CT: Yale School of Management.