Bucket Elevator
For several years, the company has been using a bucket elevator made from steel. Steel bucket elevator was chosen because of the cost advantage. They can resist rapid wear and abrasion. Besides, they can tolerate extremely high temperatures during operations. However, a steel bucket elevator could be expensive, especially if it is made from stainless steel material. The company also opted for the steel bucket elevator because of its non-stick qualities and suitability for handling food bulk materials.
The company however faced problems with steel when the grains loaded on Bucket Elevator caused a spark, which led to a fire. The bucket elevator consists of three major parts that can generate heat. The heat can ignite dust in the elevator or atmosphere and cause an explosion. Notably, it was observed that the heat that caused the fire could have originated from a slipping belt connected to the pulley head, the heat created by friction when the belt and the elevator casing get into contact, or heat that emanated from bearing fault. Thus, an alternative replacement was required for the bucket elevator to function normally without threats of explosion and fire from accumulated dust.
The plastic component was used to replace the steel. Specifically, a high-quality plastic bucket elevator was used (Golden Machinery Store Company 1). Polyurethane bucket was chosen for its top quality, enhanced ability to resist wear and resist impacts and, thus, avoiding dust explosion and fire. The plastic bucket is however costly because of its qualities.
The fire resulted from sparks caused by impacts of steel bucket elevator (Hoeganaes Corporation 2). Thus, it was necessary to replace them. At the same time, the company also introduced hazard monitoring and detecting systems to ensure the utmost efficiency and safety of the bucket elevator. These systems would detect any hazards, which may cause explosion and fire.
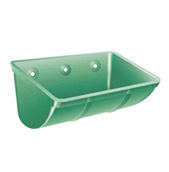
Rust or Corrosion in the Air Lines
The company noted the presence of condensed water in the Air Lines. Consequently, related problems such as corrosion were observed. Atmospheric corrosion or simply rust was noted in the Air Lines because of uncontrolled oxidation of the metallic components. A thin protective coating developed on the surface of the metal because of oxidation of the stainless steel used in the casing. Oxidation is responsible for creating stainless qualities of metal.
Copper and aluminum have protective qualities. Unfortunately, the Air Line is made of steel that creates a loose oxide, which easily comes apart from the metal component. The loose oxide elements eventually drop off and expose inner parts of the Air Line for further oxidization (Elovitz 79). This process normally continues until the Air Line rusts away.
It was noted that the increase in corrosion of the Air Line was intense with high-levels of humidity. It was attributed to an enhanced electrical conductivity of the condition of contact of the metallic surface of the Air Lines. It is imperative to recognize that any rust is electrolytic and thus, the enhanced conductivity may accelerate rusting. However, moisture content does not impact environmental air electrical conductivity (Elovitz 79). Thus, any notable increment in conductivity may only be associated with elevated levels of moisture that interact with contents in the air. The static electricity in the Air Lines could ignite a fire with dust in the air.
The company noted different impacts of corrosion on the surface conditions of the Air Lines. For instance, corrosion was more severe in specific parts with small pores at reduced humidity relative to parts with large pores. Small pores were most likely to draw in more moisture from the air because of variations in vapor pressure. Vapor pressure and the subsequent condensation of moisture in the Air Line are responsible for rapid corrosion of the metallic parts.
Corrosion was not regular in the Air Lines. Some sections had more rust than other parts. Thus, it was noted that the surface finishing of the Air Line was responsible for the intensity of corrosion in specific parts of the Line. Smoother sections of the Air Lines had limited rust. At the same time, it was observed that when the temperatures were high, the humidity was low in the Air Lines. However, a drop in the temperature resulted in more corrosion because of increased humidity in the Air Lines.
To overcome the problem of corrosion-related to humid conditions in the Air Lines, the company installed a compressed air dryer system. The advanced air dryer system had three components, namely pre-refrigeration, evaporation, and air and moisture separation (Harbor Freight Tools 1). The system could extract up to 90 percent of moisture in the Air Lines. This installation prevented too much moisture in the compressed Air Lines. Consequently, challenges associated with corrosion and possible freezing were avoided.
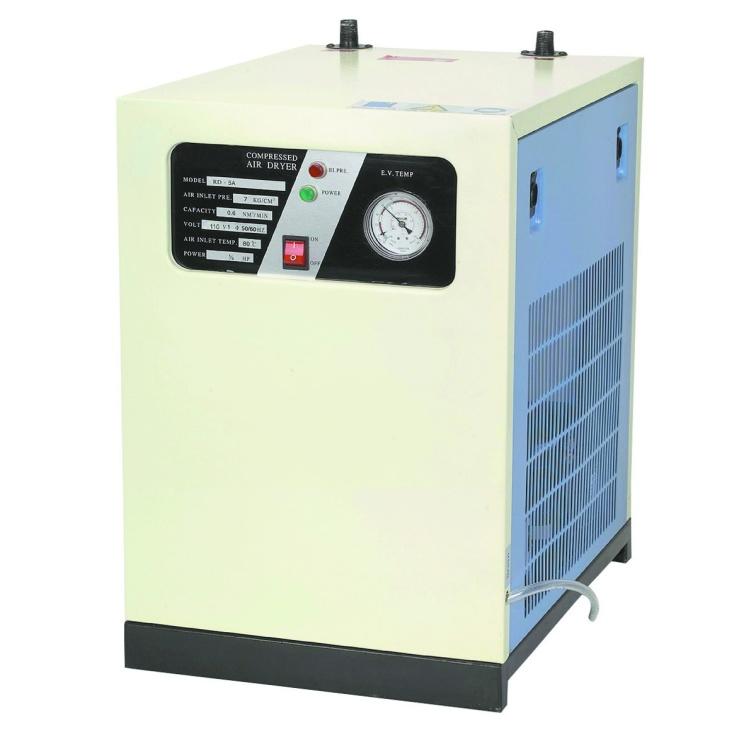
PKC: Highly Flammable and Bad Flow Rate
The company also handles PKC grains, which present several challenges. Their dust, for instance, is highly inflammable. The bad flow rate was also a challenge because grains were expected to flow freely like ‘quicksand’ in the bucket elevator.
Grain dust was associated with the highly inflammable nature of the PKC grains. In most instances, the dust explosions were serious, could lead to deaths and property damage. Figures obtained from OSHA showed that in the last 35 years, more than 500-grain explosions have been noted in different facilities across the US, which have injured and killed many people (OSHA 1). Grain dust was associated with these explosions. PCK grain dust is highly combustible, and it may explode or burst into flames in the presence of adequate dust and any sources of ignition in the bucket elevator.
In this regard, the company realized that it had to control the accumulated PCK grain dust and eliminate possible sources of ignition in the facility to reduce hazards. To achieve these safety measures with PCK grain, the company had to introduce an explosion prevention system outside the warehouse. The facility would offer a cooling system. At the same time, the PCK grains would be stored at the bottom of the warehouse corridors through which cooling machines would be installed to control a potential explosion.
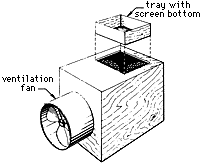
An appropriate cooling system would be installed to ensure maximum airflow into the bottom section of the warehouse to ensure that PCK grain is cooled during storage. The company will only consider a cooling system that can ensure airflow even if the storage chamber is full (University of Minnesota 1).
The company is taking all the necessary steps to ensure that its facilities are safe for employees and systems can operate optimally without posing danger. Such safety measures are, therefore, encouraged in the company.
Works Cited
Elovitz, Kenneth M. “Understanding What Humidity Does and Why.” ASHRAE Journal (1999): 75-81. Print.
Golden Machinery Store Company. Elevator Buckets. 2015. Web.
Harbor Freight Tools. Compressed Air Dryer. 2015. Web.
Hoeganaes Corporation. Metal Dust Flash Fires and Hydrogen Explosion. Gallatin, TN: Hoeganaes Corporation, 2011. Print.
OSHA. Grain Handling. 2015. Web.
University of Minnesota. Dryeration and in-storage cooling for corn drying. 2015. Web.