Leadership can be defined as the conditions for the formation, manifestation and the development of the leader’s authority as well as the recognition of the leader’s merits, qualifications, experiences and favorable human qualities. In that regard, it can be stated that among the aspects expected form the leader quality decisions takes the most important position, followed by the perception of the followers toward such decisions. Considering the aforementioned, this paper analyzes the process of making a decision based on the case study, in which a decision should be made on whether to use the existing outdated equipment to monitor pollution emissions, or buying a new piece of equipment, an Emission Systems Monitoring Instrument (ESMI), which is capable of making precise measurements, but costs money and might lead to fail the deadline (Denhardt & Denhardt, 2009, p. 362). The decision will be analyzed based on the Vroom-Yetton model, stating that the consultative leadership style will suit the described situation the best.
The Vroom-Yetton model is oriented toward a single aspect of leadership behavior, which is the involvement of the followers to participate in the process of making a decision. In that regard, the situation should be assed in accordance with several criteria, after which a model of behavior will be selected, which will establish the appropriate level and pattern of delegation.
In assessing the situation, the vital aspects are: the quality of the decision, the commitment of the subordinates, the knowledge of the leader, the structure of the problem, the probability of subordinates’ commitment, sharing the organizational goal, the likelihood of a conflict between subordinates, and subordinates knowledge. Thus, following such factors, it can be stated that the decision quality is of vital importance in this decision, where the collected data will be used in a presidential decision making process.
In terms of commitment, it can be stated that the commitment of the subordinate to the decision is also of importance, where their experience will help in working with the obtained information in either cases. Nevertheless, it can be stated that it is of high probability that the subordinates will follow the decision and be committed to it, even if it is made only by the leader. At the same time, the leader does not have sufficient information to make the decision on his/her own, as he/she is not familiar with the new equipment, does not have knowledge of the necessary degree or precision, or the precision that the outdated equipment can provide. The latter can contribute to the problem being not well structured, where there are many vague aspects in the problem, such as the economic reasonability of buying the new equipment, with the only information being available from the rest of the team. Thus, it can be stated that not all of the problem’s aspects are clear.
Describing the subordinates, it can be stated that they share the organizational goals, when solving the problem, and as indicated in the case they are highly committed to the goals of the agency. Moreover, the conflict is not likely among them as they all agreed in the opinion that they provided. At the same time it can be stated that they have sufficient information to make a high quality decision, being the more experienced in that field.
Thus, the aforementioned description will imply that the factors of the decision will be structured as follows:
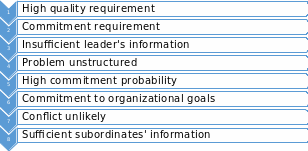
Such description implies that the best pattern of delegation is CII, which sharing the problem with the subordinates in a group meeting, obtaining their ideas and suggestions, and making the decision alone (Denhardt & Denhardt, 2009, p. 355). Such decision reflects a consultative leadership style, following, which it can be assumed that the leader will have better information regarding all the available options.
It can be concluded that the Vroom-Yetton model is a helpful tool to decide, which style to adopt when making a decision, specifically in terms of the degree of the subordinates involvement in such process. According to the model, it was found out that the best style suitable for the situation described in the paper is the consultative leadership style. This style implies that the leader will consult the subordinates in a group meeting, while the decision will be made alone, which might or might not reflect the subordinates’ influence.
References
Denhardt, R. B., & Denhardt, J. V. (2009). Public administration : an action orientation (6th ed.). Belmont, CA: Thomson/Wadsworth.