Summary
Interlink Express Parcel Delivery is looking for a preventive approach to quality management. This is can be done by understanding the operating process and how it relates to the company’s business operations. Operations should understand the inputs and outputs of the process involved in delivering quality good to customers. It is fundamental to know the suppliers and customers so as operations manger can plan and factor the schedules as well as customer requirements for the supplier and customer respectively.
Having done so, one can easily identify and reduce variable costs in a process. Variations, mistakes, complexities are among the causes of defects in processes (Dale 1999 p. 19). The main objective in the management of a business is to provide high quality goods and services to meet customer demands at the right time, quality and expectations. For this objective to be met, work has to be carried out in an optimal manner. There are variations in time of delivery as well as mistakes made on delivering the wrong parcel to the wrong customer. The company defects mean there is a need for rework, scrap, warranty costs and inspection costs. This may be ineffective for the company in light of increasing competition, which eats up profits. Any additional waste of resources only reduces the company revenues and profits further. In addition, it also helps individuals in an organisation understand the interdependencies in the processes.
Total Quality Management (TQM) consists of a number of principles and techniques employed in the organisation processes and practices in an effort to achieve effective management operations. TQM techniques endeavor to provide the best methods in operating organisation activities (Heizer & Render 2005). It also helps individuals in an organisation understand the interdependencies in the processes.
Introduction
The main objective in the management of a business is to provide high quality goods and services to meet customer demands at the right time, quality and expectations. For this objective to be met, work has to be carried out with utmost optimality. All tasks involved have to be scheduled. A schedule is a detailed plan of operations so that all involved in the process are aware of the tasks, when they are to be carried out done and the individual assigned the task. This is done prior to the commencement and implementation of the scheduled plan. Therefore, the organisation must outline what it intends to achieve within a set time (Burnes 2004).
The objectives could range from cost minimisation, reducing the levels of stock, increasing operational efficiencies, improve cash flow or to maximise the use of resources. A schedule may be simple for example a list of things to do, a checking check out roster or an equipment inventory register. In some instances, a schedule may be more complicated and in consequence requires a more sophisticated operation management system. This system includes GANTT charts, just in time (JIT), network analysis such as program evaluation review techniques (PERT) among others.
Problem Description
The company is faced with a problem in its operations process. There are variations in time of delivery as well as mistakes made on delivering the wrong parcel to the wrong customer. The company defects mean there is a need for rework, scrap, warranty costs and inspection costs. This may not be good for the company since there is competition, which reduces profits. Any additional waste of resources only reduces the company revenues and profits further.
Defects can be caused by the complexities, variance, mistakes or cultural difference. There is a need to look into the operations process and route out the causes of these defects. Variance in production may arise from input materials, the machines, the working environment, operators, methods used and measuring instruments used in the process. As suggested by Marchewka (2003), these are from common causes of variations and management has the power to change systems, processes and infrastructure that cause the differences. There are special variations caused by external sources to a process.
These occur sporadically and disrupt operations. They can be indicated in statistical chart by a big variation from the normal operations or a process out of control as discussed in the methodology and results. Front-line managers and supervisors can easily identify and solve this cause of these variations. Management usually fails to distinguish between special causes of variations and common causes of variations. This leads to fundamental management mistakes (Oakland 1993).
Methodology and Results
Total Quality Management (TQM) consists of a number of principles and techniques employed in the organisation processes and practices in an effort to achieve effective management operations. TQM techniques endeavor to provide the best methods in operating organisation activities (Heizer & Render 2005). However, the level of effectiveness ranges from one company to another, as they do not employ the same TQM methods. History confirms that there is no one recipe for company success, therefore, every organisation employs the best TQM model deemed the best. The contents and contexts of this paper span around the assessment of TQM in an effort to identify one that offers great insight in the improvement process (Heizer & Barry 2010). There are a number of techniques that enable management to reach excellence, and range from joint problem solving, brainstorming, data collection, methods of analysis, planning for just-in-time (JIT).
Having identified the problem face by Interlink Express Parcel Delivery, we look at the statistical approach to solving variations and defects. General tool to achieving zero defects with no mistakes in line with their causes are outlined below:
- Mistakes – use mistake –proofing, Poka-Yoke, Zero defect.
- Complexity – use process mapping tool.
- Variance – use statistical process control, Taguchi methods and Design of experiment.
- Cultural factors – use teams, and management commitment to quality.
Mean control charts will be used to monitor the sample parcel from production to establish the control levels in the process. This will aid operations put in place measures to reduce and eventually eliminate these variations. Since discrete measures are not being sought, normal distribution will be used (Robbins, Millett, Cacioppe and Waters-Marsh 1998). These charts will clearly show the operations within a given period and indicate success rate. This data can be linked to other special and normal causes of variations to determine the cause of actions.
The three – sigma control limits of the process are:
- The upper control limit
- The warning limit
- The lower control limit
In some instances, a lower warning limit may be added.
These process limits will be used in the control chart. They will limit the variations about the mean. From the statistics, a sample may fall between the control limits and the warning limits.
Formulas for the control and warning limits
- Upper Control Limit (UCL) = mean x+ 3 σ/√n
- Upper warning Limit (UWL) = mean x +2 σ/√n
- Lower Control Limit (LCL) = mean x -3 σ/√n
- Lower Warning Limit (LWL) = mean x -2 σ/√n
Where
X is the sample means
σ/√n is the standard error of the means (SE)
Control charts
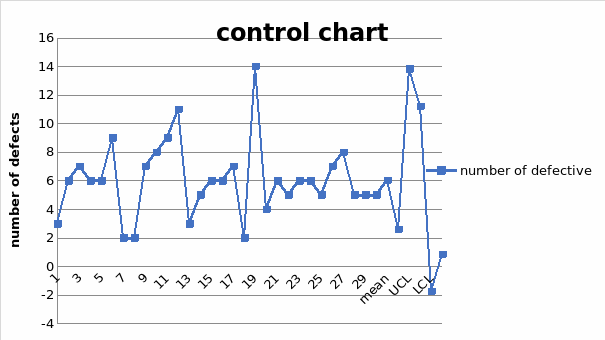
Control chart 1. Data
- Mean = 6.03
- SE= 2.59
- UCL= 13.81
- UWL =11.22
- LCL= -1.75
- LWL= 0.85
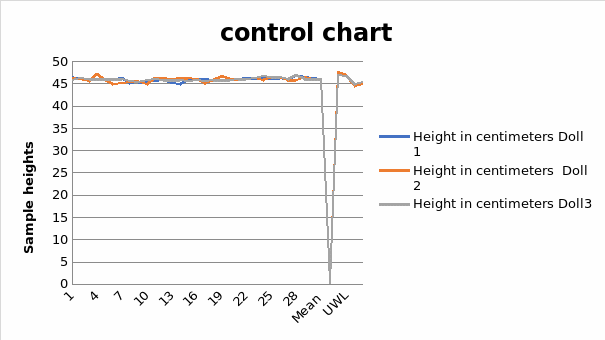
Control chart 2
The two data sets show the results that have been used to plot the control charts. The size variance may be small as shown on the graph but sampled out and plotted in the given range alone there is a large variation in the sizes. Warming zones can be sampled out like in the 19th sample on defects; a record of 19 defects was recorded. After which there is a slight reduction then the defects number increases again.
Questions that need to be answered on chart interpretation on if the process is in control are as follows:
- Are there any values above the upper control limit?
- What are the values between the warning and control limits?
- What is the number of consecutive values on one side of the warning limit?
- What is the rising and falling trend indicated in the chart?
- What is the trend in the warning limits?
The control chart shows that the process is out of control since the chart show the process has been fluctuating between limits and at some point, the process was beyond the upper control limit. In the last three days, there was some level of stability in defects but the percentage does not give the process credit. There is no consistency in the outcomes this shows that the process is unstable. At any point, a random height can be generated. If the height had differing by a margin of plus or minus 0.2, the process would be close to elimination of variances.
The company may consider applying either closed or open systems. Closed systems are systems that do not rely on their environment, they chart their own unique path and do no transact with the outside world (Doss, Wallace & Webber 2006). An example is an astronaut’s life support pack. Open systems interact with the environment. They exhibit characteristics like the use of inputs and discharge of outputs and transacting with the environment. In this paper, we discuss open systems at length. Green Onyx operates an open system. It procures inputs, which are expended in the production of sunglasses. This involves taking the inputs through various production processes before the final product is ready for release in the market. For a smooth transition in the production process, a schedule of the workflow needs to be mapped. This will ensure bottlenecks that would otherwise slow down or ground the process all together are ironed out (Barrien 2000).
In addition, Joint Problem Solving comes as the best technique in organising group tasks in the company within quality circles. Joint Problem solving the focus is on continuous improvement of quality through depersonalizing conflicts, offering logical frameworks as well as integrating organizational objectives with the employees. This is best done through action-oriented problem solving procedure (Barrie 2000). The action-oriented problem solving process begins with problem identification through brainstorming organization operations. The next step is to establish goals that guarantee continuous improvement. The third is putting the plan in order of priorities that endeavor to achieve goals as well as develop group priorities.
For instance, if there is a problem in the production process. It could be emanating from common causes and special causes. On the defects problem, it could be that the machines are faulty or there are human errors that are being made in the process. It does not single out the inputs but considering the defects the inputs are placed lower on the causes.
Brainstorming is a technique that enables the management gets many ideas on faced problems within the shortest time possible. It is very effective when it involves a team of people concentrating on problems and ideas without any criticisms. Brainstorming endeavors to have the present conditions of a problem known as well as try to establish the main cause. This will also call for data evaluation after gathering statistical data (Lientz & Rea 2002). The company should look into the identified areas machinery, human resource among and other causes and seek corrective action. These may mean management will buy new machinery or repairs the existing ones to improve effectiveness. There may be a need for employee re-training on the processes involved (Oakland 2007).
Just in time (JIT) focuses on strategic methods to achieve effectiveness and efficiency in company acquisition and management of company inventory and raw material when dealing with vendors. This specifically involves the acquisition of right quantities at the right time with zero waste. There is a need to look into the manufacturing process and route out the causes of these defects. For example, variation in production may arise from input materials, the machines, the working environment, operators, methods used and measuring instruments used in the process.
Discussions and Recommendation
There is a problem in the operation process. It could be emanating from common causes and special causes. On the defects problem, it could be that the machines are faulty or there are human errors that are being made in the process. It does not single out the inputs but considering the defects the inputs are placed lower on the causes. Some common human mistakes identified are:
- Lack of experience
- Wrong identification
- Slowliness
- Lack of standardisation of inputs
- Unexpected machine operations
- Intentional errors
- Misunderstanding
The company should look into the identified areas of operations, human resource among and other causes and seek corrective action. These may mean management will buy new vehicles with computerised systems or repairs the existing ones to improve effectiveness. There may be a need for employee re-training on the processes involved. Much more important on the size of the parcels: the measurement tools used in there machinery need to be checked.
- Order receipt by the sales department.
- Order analysis and approval by the credit section
- Order receipt by stores for quantity allocation
- Goods send to dispatch and packaging
- Invoicing of order by the invoicing department for record and payment
This is a general view of the ordering process at the company. The sales department does not need to duplicate the order in five copies on receipt. The data is input online saved and mailed to the credit section. The section performs an online analysis on credit credibility, mails back the reply, and stores the approval in the central data system. On receipt the sells person mails the approval to the customer and notifies stores to quantify and release the goods to dispatch. Invoicing department can get the information on the dispatch and invoice the client. Integration of the system saves resources in terms of time, people and funds (Kast & Rosenzweig 1985).
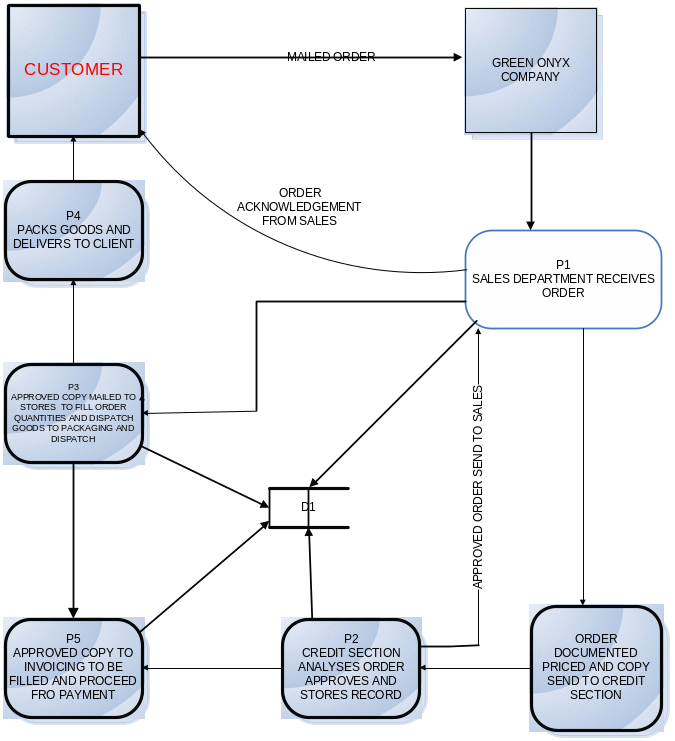
The processes explodes are the sales department’s receipt of order, credit department’s receipt of order and order receipt by stores. This is the child diagram of the data flow diagram of level zero. It contains parts of the DFD level 0 and additional elements of the operational processes.
Sales department on receipt of order documents the order by in putting the customer package information in the system. This includes the name, the order number, the items codes, quantity, date, time house number, street and weight of the package. This storage of information will aid any employee of sales access the information on recent orders or customer data. It does not limit the data to order number or customer information. The order is priced and sent to the credit section. Sales department inputs the prices depending on the item codes. This pricing is different from one listed in stores. Sales department issue prices according to the market prices that will generate profits for the company.
The credit section receives the order copy by mail and values the order. If it is a current customer, the value is added to the outstanding balance and it is established if the credit limit has been exceeded or it’s within the limit (Lientz & Rea 2002). After the analysis, an approval is made and data sent to the central database. A copy is mailed back to the sales department, which acknowledges the order to the buyer and sends to stores. Thereafter, the journey for delivery to the main customer is begun.
In addition, the Company can re-design its ordering process to a more efficient system. From the duplicated copies of the order forms sent across the departments and filled, it can be assumed its operating a manual system. At the process, time cycle duplication is considered as a non-value adding activity. More effort and resources can be channeled to value adding activities. Time is one of the most important resources and it determines wealth to be created though efficient processes. Process boundaries should be established and activities planned to manage time. Those activities that involve reworking mean that resources are waste even though the rework was adding value.
Rework, movement, delays can be eliminated. A computerised integrated system will aid the company design a more efficient ordering process. Storage of data in a central database improves the communication and access to information. Using selected tools in project planning and scheduling the company ordering process will be designed to serve customers better and create a competitive advantage for the company. Control charts can be drawn to establish if the process is in control in so doing improve on the quality of the system. These charts can act as a problem solving tool as they will indicate the limits in processes and avoid out of control activities (Dunning 1981).
Conclusion
The quality management tool identified by Heizer and Render (2009 p.13) includes Just in time technique, benchmarking, use of Taguchi methods, employee involvement continuous improvement. Other statistical tools include flow charts, Pareto principle, checklists, scatter plots and check sheets. Having identified the problem areas the company has to focus on improving its processes towards quality improvement. It has to start by laying out clear quality objectives then lay out a strategy of implementation. This, accompanied by employee participation, will see the company improve quality processes attain zero defect process (Heizer and Render 2005 p. 32).
The production and operation process up to the delivery point of products run without hitches. Bottlenecks that would otherwise slow down the process are alleviated because a clear path of how tasks follow each other is laid down ahead of the process. It also makes it easier for a new employee to pick up the process in case a key resource was to be laid off (Dwyer, 2005). This storage of information will aid any employee of sales access the information on recent orders or customer data. It does not limit the data to order number or customer information. The order is priced and sent to the credit section. Sales department inputs the prices depending on the item codes. This pricing is different from the one listed in stores. Sales department issues prices according to the market prices that will generate profits for the company (Barrien 2000). It also helps individuals in the organisation to understand the interdependencies of such operational processes.
References
Barrie, D 2000, Managing quality, Blackwell Publishing, Oxford.
Barrien, K F 2000, A general systems approach, Rand Millay College Publishing company, Chicago.
Burnes, B 2004, Managing change: a strategic approach to organization dynamics, NY, Prentice Hall.
Dale, B 1999, Managing quality, Blackwell Publishing, Oxford.
Doss, G, Wallace, M & Webber, L 2006, IS Project Management Handbook, Aspen Publishers, Aspen
Dunning, H 1981, International Production and Multinational Enterprise, George Allen and Union Publishers, London.
Dwyer, J 2003, The Business Communication Handbook, 6th Edition, Prentice Hall, Australia.
Heizer, J & Barry, R 2010, Operations management, Pearson Publishing Limited, London.
Heizer, J & Render, B 2009, Operations management, Pearson Publishing Limited, London.
Heizer, JH, Render, B 2005, Operations management, Pearson/Prentice Hall, Pennsylvania.
Kast, F & Rosenzweig, E 1985, Organization and management, McGraw Hill, Inc., Singapore.
Lientz BP, Rea KP 2002, Project Management for the 21st Century, Academic Press, Chicago
Marchewka, JT 2003, Information Technology Project Management, Wiley Hoboken, Pinkerton.
Oakland, S 1993, Total quality management, Butterworth publishers, Bradford.
Oakland, S 2007, Total quality management, Butterworth publishers, Bradford.
Robbins, SP, Millett, B, Cacioppe, R & Waters-Marsh, T 1998, Organisational Behaviour: Leading and Managing in Australia and New Zealand, 2nd Edition, Prentice-Hall, Australia.