Introduction
Laser devices are very instrumental in industrial applications. This is mainly because of its unique characteristics such as collimation and congruence, among others. Its creation involves optical amplification of photons through stimulated emission. Moreover, it is known for temporal and spatial coherence, this cannot be attained through other technologies. Laser light can be manipulated for use in various industrial sectors.
These include precise measurements, cutting and moldings, welding, sensors and eye treatment, among others. Laser is therefore vital in measurements and instrumentation. This report will deal with use of laser in measurements and instrumentation. In this regard, the paper will explore laser sensors, their design, theory, process, cost and limitations. It will also endeavor to explore its application in modern technologies (Weschler 1).
Laser Sensors
Laser sensors are devices that use laser beams to sense and measure dimensions. These may range from height, thickness, 3-D point clouds, distance from objects, position and surface profile, among others. One important characteristic of laser sensor devices is their accuracy and precision.
This has enabled them to be used in highly definitive measurement applications with innovative technology. Products from laser sensors are important for various industrial applications such as advanced research, home applications and industrial appliances, among others. It is also quite important to note that there are numerous laser sensor products. In this regard, they are classified in accordance with application needs.
For instance, home appliances such DVD players use laser sensor for conversion of tracks into electrical signals. In addition, other laser sensors are utilized for various industrial purposes. These include displacement and confocal sensors, among others. As has been noted above, there are numerous types of laser sensors, which range from household to industrial appliances (Sens2B International 1).
In this regard, this paper will focus on laser displacement sensors, which are utilized in measurements and instrumentation. The paper will cover design, theory, process, cost and limitations of laser displacement sensors. In essence, this will cover laser triangulation sensors.
Laser triangulation sensors are one of displacement sensors utilized to define position of any given target. This is usually achieved through measurement of reflected beams from the targeted surface. In such cases, a laser diode, which works as a transmitter is normally utilized to project spot of light from the laser to the target. Similarly, the reflected beam is usually focused on a receiver (light sensitive device). An optical lens does this.
In order to sense changes in displacement, a reflection of the new spot is made and this effectively changes. In order to linearize the results, as series of conditionings are made. These include linearization, analogue and digital conditioning. The target position is then got from the output results of signal conditioning. Moreover, this output is usually proportional to the displacement made by the targeted object (Sens2B International 1).
Design
A laser sensor is designed to give precise measurements of displacements of objects. The device is designed to provide measurements for targets. Its design consist of a laser diode, (CCD) charged coupled or (PSD) position sensitive device.
The two elements, CCD or PSD can also be called receivers. Moreover, it is also quite important to note that only one of the two elements can be utilized at a time. However, this depends on the function intended for the device. Moreover, it is important to note that PSD sensors perform to expectation in normal (perfect) conditions.
Nature of targets is also an important factor that determines the kind of output received. For instance, when these conditions favor texture or tilt change of the target, shape of the light spot also varies. This alters center of distribution of light, which ultimately alters the output of the receiver. However, it is important to note that the position of target does not change. The figure below shows the schematic design of laser triangulation sensors (Sens2B International 1).
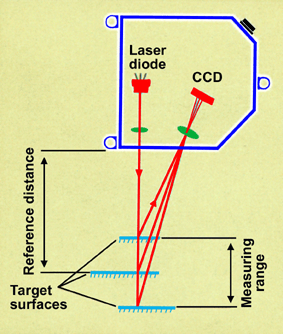
The figure above shows the components of a displacement laser sensor. It consists of the laser diode, target surfaces which are made of optical lenses and the receiver. The figure below shows a displacement lasor sensor with its componenets in place to focus on a target. In order to producce results, it is focused on an object which can be moved to give results.
It is also impotant to note that while PSD receivers are sensitive to light intensity, this is not the case with CCD receivers which are magnificient irrespective of texture or color of the target object. In fact, the latest element of CCD is important as it reacts instinctively to change in surface conditions of the target. In esence, the device is designed to overcome complications attributted to PSD in the past (Micro-Epsilon Messtechnik Corp. 1).
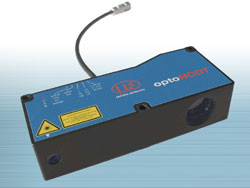
Theory
The invention of HeNe was a revolution in making of laser sensors. This is mainly because laser could make alignment systems. Moreover, it was the only way of making a continuous wave. Its ability to be collimated made it much easer to be utilized in long-range measurements. Furthermore, this enabled sensing over long distances. Collimation was further improved when the diameter of HeNe laser was increased to 6mm and then to 12mm.
This comes from the principle of laser, which states that propagating lasers do so with little spreading when the diameter is larger. In essence, laser sensors work on a simple principle that relies heavily on the fact that light travels in a straight line. In this regard, position-sensing targets can be detected when the beam of laser intercepts them. This can then be digitized to be given out as the measurements.
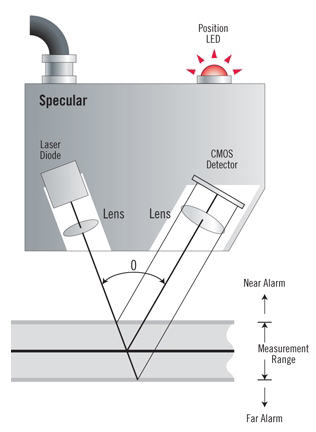
Laser sensors have come a long way in measurement and instrumentation. Moreover, their uses have increased to determine perfect squares, flatness, straight lines and vertical references. In this regard, they are capable of improving precision of sensors in displacement measurements. The figure below shows a laser beam, which is focused on a position target.
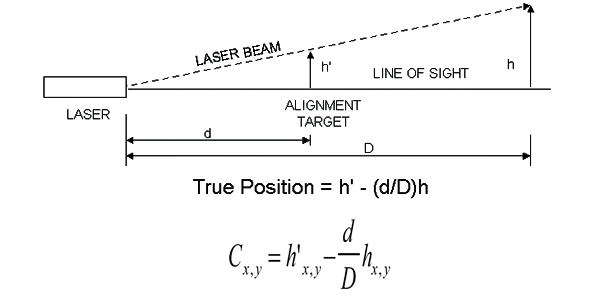
Tooling methods have varied throughout centuries. However, advancements in technology have brought about innovations that have transformed measurements, instrumentation and metrology. This has replaced the tiresome work employed by personnel to determine measurements using telescopes.
In this regard, laser creates planes of reference. This is then converted to electrical signals to give an output from the receiver. Laser beams are very important in establishing a line of reference. This is mainly because light travels in a straight line. Moreover, this comes as a relief since complicated methods utilized to make straight lines were inaccurate. In addition, laser has also improved determination of flatness.to thousands of an inch (Sens2B International 1).
Procedure/process
The process of measuring target positions using a laser sensor has improved over the years with advancements in technology. Using the set up below, determination of true position of objects is possible. However, innovations have made this process quite simple as works previously employed are currently carried out by digital means, which simply give out the readings. The figure below shows measurement principle.
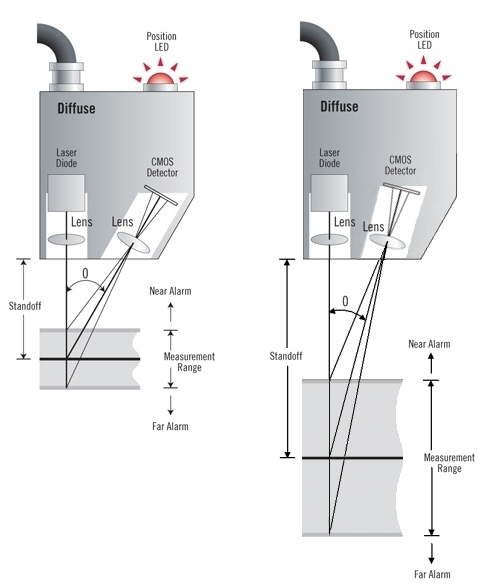
Laser sensors have the advantage of combining both alignment and sensing range to provide quality results. Laser sensors are in different forms. These include ultrasonic, fiber optics, part sensing, clear object detection, slot and measuring array sensors, among others. The process involves the following: Placing a target object in focus through the lens of a laser sensor. This involves finding the right alignment for reflection to be achieved. The procedure can be illustrated as shown below.
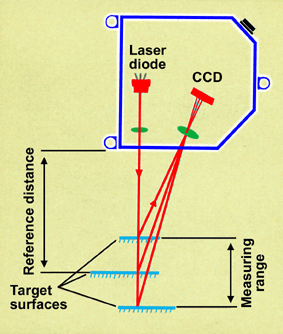
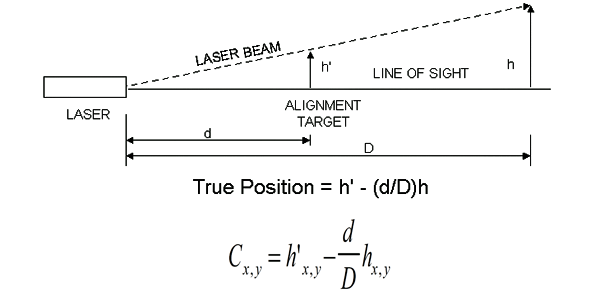
Laser sensors used light beams to scan dimensions of an object. This allows for three-dimensional scanning of objects since it applies optical properties of light. The method can be applied on fragile objects since no contact is required for measurement of sensing. The process of measuring displacement using Laser triangulation sensor is normally achieved in light sensors in the following manner.
When an object is placed within the sensing range of a laser sensor, its position is measured by conditioning of reflected beams of laser from the object. His process involves a transmitter, which is also known as the laser diode. The diode transmits light spot towards the object. When the spot of light reaches the sensing object, this is reflected to the receiver through an optical lens. The reflected light is then focused on the light sensitive receiver, which converts information into electrical signals that can be read (On-Trak Photonics, Inc. 1).
Limitations
As much as Laser sensors provide various advantages to uses, they have several limitations that impede their use. These include their range of usage as well as the number of targets they can work on successfully. Limitations include maintenance due to the fragility of its elements.
For instance, foreign debris or dirt has the capability of not only affecting accuracy but also distorting its functionalities. In addition, laser sensors have electronic components, which are very sensitive and therefore cannot be utilized under a wide range of temperatures (0 degrees Celsius to 40 degrees Celsius). For instance, their use in high temperature conditions may be impeded. Furthermore, at very high temperatures, some elements such as lenses and diodes, among others may break.
Moreover, their use in vacuum conditions is limited, as they must be cooled in order to function properly. As had been noted above, PSD are quite limited in reaction to texture and color, this affects its accuracy and thus affect laser sensors. It is also quite necessary to note that laser sensors can only measure a limited displacement. For instance, they cannot be utilized for very long distances (Laser Technology, Inc. 1).
Cost of Equipment
Cost is a very important factor to consider when choosing the right equipment to purchase. Laser sensors are numerous and vary in costs. This depends mainly on the kind so application they are utilized in, for instance, large-scale industries that deal with robotics use powerful lasers that cost thousands of dollars. On the other hand, lasers sensors made for home applications are usually cheaper and can cost as little as thirty dollars.
For example, LDS (laser distance sensor) laser sensor can be purchase for just under $ 30. Moreover, CMOS laser sensors are quite cheap and can be bought for less than $100. In essence, the kind of application required for a given laser sensor determines its cost. Therefore, consideration for purchasing laser sensors should be focused on the functions and efficiency before narrowing down to cost (MTI Instruments Inc. 1).
Conclusion
Lasers are of great importance in an increasingly globalized market. This is mainly because laser applications have diversified over the years. For instance, its use in motion detection, collision avoidance and security as well as sensing applications has improved quality of life. Laser sensors are therefore very instrumental in industrial world. This is mainly because they have eased the work of measurements, cutting, welding, as well as precision of the same. Various types of laser sensors apply a wide range of techniques in target detection.
These include laser displacement sensors, ultrasonic, fiber optics, part sensing, clear object detection, slot and measuring array sensors, among others. Laser displacement sensors include laser triangulation sensor, among others. These are used for measuring displacements and sensing object positions. It is important to note that the cost of laser equipment varies with intended function. However, their use is divers and very instrumental in a technologically advanced world (Banner Engineering Corp 1).
Works Cited
Banner Engineering Corp. Products & Applications: Laser Sensors. 2012. Web.
Laser Technology, Inc. The Smallest, Most Powerful, Lowest Cost Laser Sensors in the Market. 2012. Web.
Micro-Epsilon Messtechnik Corp. Laser Triangulation up to a distance of 2m. 2012. Web.
MTI Instruments Inc. Laser triangulation Systems. 2012. Web.
On-Trak Photonics, Inc. Laser Alignment Theory. 2012. Web.
Sens2B International. How they work: Laser Triangulation Sensors. 2012. Web.
Weschler, Matthew. How Lasers Work. 2012. Web.