Executive Summary
To produce the three pin plug, the manufacturer first analysed the properties of different materials, the cost-effectiveness of different manufacturing methods, and the cost-effectiveness of the design and assembly line to optimise production and the marketing of the 3 pin plug. Urea formaldehyde was the best material used to manufacture the plug cover and base and brass were suitable for making the pins.
Urea-formaldehyde has good dielectric properties, has good thermal resistance, does not break easily and is cheaper than other resins in the family of amino resins.On the other hand, the weaknesses in the previous manufacturing layout of the process was labour-intensive and very expensive, it was necessary to make a new layout design to substitute the old layout. Automating the new design made it better, cheaper and easier to assemble parts of the plug together to meet the two million plugs per year. The study showed that when the plug came to the end of its life, most of the materials used to produce the plug would be recycled and reused to make new products for other uses.
Introduction and Background
The paper discusses the manufacturing processes and the materials used to manufacture the 3-pin plug. It is important to use relatively cheap materials to manufacture the different components to produce the standard 3-pin power plug to make sure the resulting product is cheap to allow a competitive advantage in the market (Dodiuk & Goodman, 2013). The study recommends the use of thermoset resins, which are plastic materials that are easy to mold into any shape that is suitable for the cover plastic part of the plug.
Styrofoam or foam plastic is a commercial plastic recommended for use because it is light and has good thermal and electrical insulating properties (Wiyaratn & Watanapa, 2010). According to Dodiuk and Goodman (2013), the plastic does not shutter when it drops or falls down. The paper also discusses a new and better manufacturing process to replace the old manufacturing process.
Manufacturing Process
The 3-pin plug is made of three parts, which include the cover, live pin, natural pin, cord grip, base, and grip screws. The discussion about each part and the suggestions about the right materials to use in making the parts are the following.
The Cover
Here, the cover is made of a material that has good insulating properties to protect people from electric shocks. The candidate materials include wood, which cannot be used in its state because if used, it leads to environmental destruction. On the other hand, metals such as copper cannot be used because they are good conductors of electricity. However, plastic, which has excellent insulating properties, is the best material to use.
The recommended plastic includes the family of acetals and acrylics. Acetals are highly inflammable, strong, tough, rigid, resilient, and have good thermal and electrical insulating properties. However, acetals are suitable for making bearings and gears. On the other hand, acrylics are suitable for sunglasses, cameras, and binoculars because they are easily coloured and are susceptible to damage from household chemicals such as gasoline.
The best options to use are thermoset resins that belong to the class of urea formaldehyde. Despite the thermoset resins being not aesthetically appealing, their properties make them suitable for use in making insulating copper cables and for manufacturing the cover and the base of the 3-pin power plug. Resins are polymers with high molecular weight that makes them easy to cast and extrude using the already available moulding and pressing machines. The plastics have cost and chemical advantages and are superior in thermal and electrical resistance. The following is a bill of alternative materials for the plug.
Table 2: Bill of Candidate Materials for Plug Cover and Base.
Design Considerations
The cover should fulfil the following requirements:
- Provide an electrical path for the electrical appliance to the socket.
- Protect the user from an electrical shock.
- Should not fail or break on dropping.
- Resist environmental effects such as moisture.
- Be aesthetically pleasing.
- Fit properly where it is applied.
Manufacturing of Plug Body and Base
Urea formaldehyde, which is a thermoset plastic can easily be extruded, compression molded, cut, milled, and drilled as shown in Figure 2.
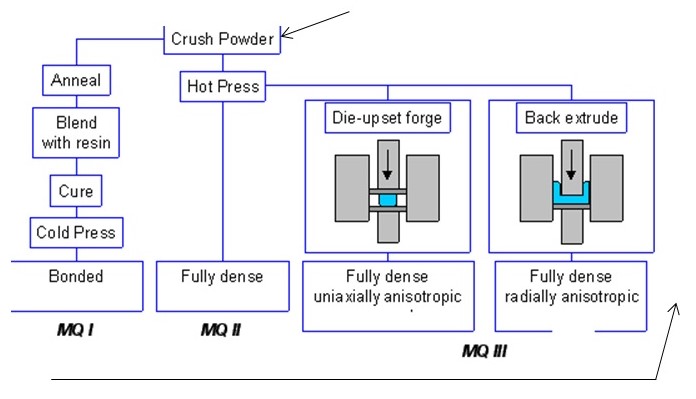
The production process involves crushing the urea formaldehyde into powder and hot pressing the material using the forging machine to produce the cover. The processes are illustrated in Figure 1 and Figure 2.
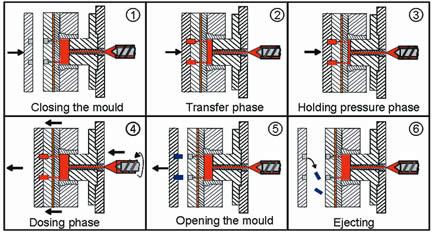
The resulting products are shown in Figure 3 below.
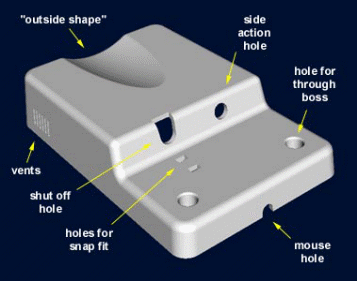
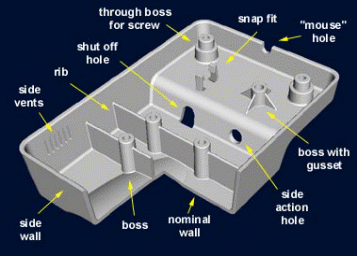
Before the manufacturing process of the 3 plug covers and the base starts, the manufacturer evaluates the quality and performance measurements of the materials to determine their suitability. In addition, the manufacturer asks important design questions such as functional requirements, how the cover works, existing manufacturing methods, and the alternative materials that are available for use (Kalpakjian et al., 2008).
In the present situation, the best material to use is urea formaldehyde because it maintains the required shape and size after it has been worked on. The right decisions of the design of the 3-pin plug are made based on the correct specifications provided by the designer, which includes the ability to satisfy the British standards for manufacturing 3-pin plugs. The assembled 3-pin plug shown in Figure 3 consists of all the parts after the plug has been assembled.
The main geometric concerns used in the design to mold the covers that are shown in Figure 4 include the proper flow of the plastic and the shrinkage of plastics using the sinkholes. To make sure that the plastic cover maintains the necessary strength required to avoid breakages, the cross-sectional thickness is kept to minimum.
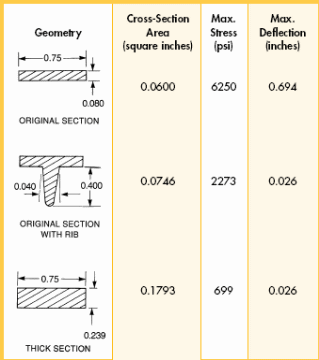
The geometry of the original cross-section of the covers shown in Figure 4 shows how the forces of deflection and stress can be managed to make sure that the plastic does not break.
Cable wires
The wires used to make the cables and clips were imported from other manufacturers because they were relatively cheaper when obtained from the external market rather than to produce them in-house.
Fuse Clips
The fuse clips were bought from other sources because they were cheaper to buy than to manufacture them in-house.
Plug Pins
The production process includes:
- Stamp molding the raw material – because it is easy to use and cheap to install.
- Outline cutting – makes the shape easy to use.
- Plating – prevents corrosion.
- Polishing coloring – improves the aesthetics.
- Cleaning -to remove dirt.
Figure 5 shows the machine used to produce the pins. The material considerations for the plug pins include copper, mild steel and brass. The materials are easy to shape, mill, drill, and draw. However, brass is the best candidate because it is easy to sand-cast, die-cast, and low-wax-cast the brass without breaking.
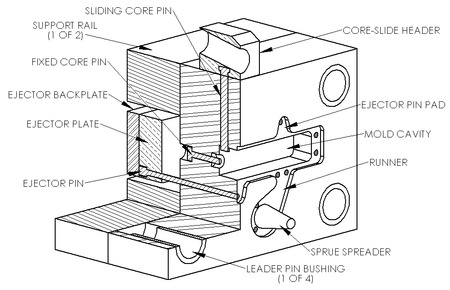
Brass is cheaper than iron and copper and it does not rust when exposed to moisture or water. Brass is easily milled, ground, cut, and drilled that makes it easy to weld, fasten, and solder. The plug pins are made of brass, which is an alloy of zinc and copper that are mixed in varying amounts. Each alloy has a different melting point because of the different composition ratios of the materials, and in general, the melting temperatures of the alloys vary between 700°C and 1000°C.
The pins are ferrous in nature and have an intermediate weight because they are made of brass. The pins are made of good conductors of electricity that makes them have good thermal and electrical conductivity. In addition, brass is good because it has some of the important technical properties of the materials, which include high ductility, resistance to wear, abrasion, and corrosion. Another quality that makes bras a good material is that it is easy to solder and braze when making the pins (Wiyaratn & Watanapa, 2010).
Alloying silver with copper makes it cheaper, but not as cheap as brass, which has a melting point of 992°C. Silver is suitable for use because it “has an intermediate weight. Silver can be soldered, welded, cast, rolled, forged, machined (cut), spun, bent, pressed and extruded. The material finishes well increasing the aesthetics” (Dodiuk & Goodman, 2013, p.2).
Screws
Screws are vital because they are used to join the components together. Different methods are used to manufacture the screws and the most recommended is the cold thread rolling method. Typically, the cold-working process enables the manufacture to use a special taping attachment machine.
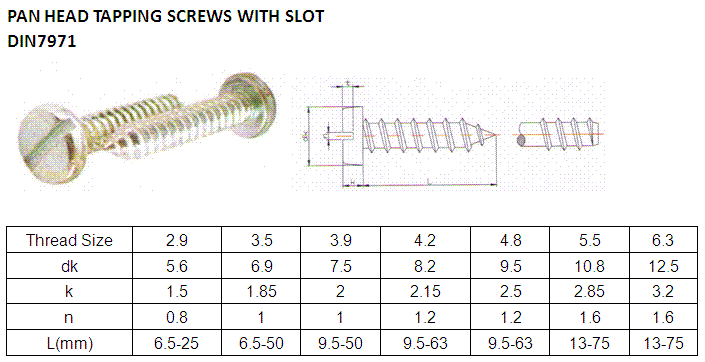
The process does not cause loss of materials, but it the right method for making cheaper screws with short threads used to assemble the 3-pin plug. The thread rolling process is done between two dies, which consist of one fixed die and the other one that rolls on the fixed die (Jahangirian et al., 2010). The screw made this way allows the plug to be dismantled and reassembled to ensure the components do not make a permanent joint. The skills and machines to make the components are important capital requirements for the manufacturing process if the process is to be done locally instead of importing the screws.
End-of-Life Disposal
The copper wires used to make the conductors and the brass for making the pins can be recycled for other uses when the plug reaches the end of its life. However, the plastic used to make the covers and base should carefully be disposed because of the health effects it can cause on human beings when released into the environment. Typically, the plastic cannot be reformed or recycled and that makes proper disposal very important. In addition, the plastics have additives that should be avoided because they can adversely affect the environment. Additives are necessary because they improve the properties of plastics such as reducing the cost of production and improving the working properties to assist in the processing of the plastic covers.
Analysis of the Cost Issues
The manufacturing process consumes resources that makes the issue of cost-effectiveness an important factor. In addition, the right process enables the manufacturer to produce large quantities of plug pins at a relatively cheaper price. In comparison with extrusion, machining is expensive because it makes a poor return on investment (ROI). However, other options that are available to manufacture pins include die-casting, forging and extrusion. However, a comparative analysis of the costs of manufacturing the pins to determine the most suitable manufacturing technology is done as follows.
Here, the manufacturing process consists of the running costs, materials, and startup costs. Here, manufacturing data can be used to compare the production processes to determine the best option in manufacturing the pins shown in Table 2.
Table 2: Hourly Production Rate.
As shown in Table 2 above, the number of pins manufactured depends on different factors such as the length and size of the pins. To make 2000,000 pins measuring 10 millimetres each per an hour, 20,000 meters of material have to be extruded to yield a production capacity of 2000,000 pins. However, an analysis of the data on the cost of each pin shown in Table 2 provides the best figures for decision-making.
Table 3: Running Costs.
Table 4: Cost Comparisons.
Table 4 shows that the total cost of in-house manufacturing of the pins using the forging method is 57.5p and the total cost for manufacturing the pins using the extrusion method is 61.1p for the same number of units, however, the cost of importing the pin is 71.3p. The cheapest process can also be determined by drawing a graph of the total cost for each process against the batch size 7. Figure 7 shows the graph comparing the total cost of each process for different batches and the quantities of the pins.
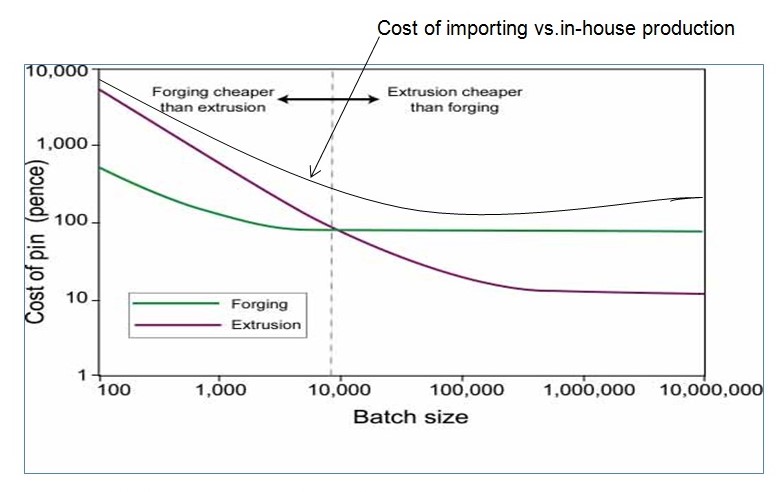
As shown in Figure 7 above, the cost-effective process of manufacturing more than 10,000 pins is extrusion. On the other hand, the cost of importing 10,000 pins is still higher compared with the least-cost of manufacturing the pins. For this study, the aim was to produce a large volume of pins using the most effective production method.
According to Wiyaratn and Watanapa (2010), the extrusion process is the right one to use when the cost of production per unit is compared with the cost of buying the pins. In addition, because the machinery has already been installed for manufacturing the pins, buying them from other sources could simply make the machinery redundant. However, some of the factors that are to consider when deciding the best process to use include: environmental protection, finding skilled technicians, the demand from the customers, and the availability of machinery.
Other Parts’ Costing
The fuse clip, cord grip, and fuse can be bought from other sources because the machinery to make them is not available within the manufacturing firm. The cost of installing the production machines and the lifespan of the machines are analysed in Table 4 below.
Table 4: Cost Analysis.
The total cost per fuse clip, cord grip, and fuse assuming a constant value has been used to calculate the labor required to work on the parts is 5.7p for the pins manufactured in-house and 4.5p per an outsourced pin, which makes the outsourced pin cheaper.
Quality Assurance
Quality is a fundamental component that is factored when designing to sell in a competitive market. Quality assurance is guaranteed in each manufacturing step to make sure the product meets the customer’s needs and expectations by implementing quality control measures at all manufacturing levels. Quality assurance is implemented by:
- Putting in place systematic production processes to ensure fit-for-purpose and error-free plugs.
- Materials were inspected for quality to check if they were compliant to quality standards.
- Testing of the plugs for conformance to standards such as checking the size of the casing and implementing quality control procedures for the casting machines.
- Ensuring that quality control regulations were observed such as designing the plug so that it can be recycled at the end of its lifespan to ensure sustainable resource management.
The steps followed in ensuring the three-pin plug was of the desired quality include:
- Doing a quality check of the raw materials;
- Ensuring quality control checks were followed to avoid production problems;
- Using efficient assembly processes with minimal problems;
- Automating the manufacturing process where it is possible.
3.0 Possible Redesign to Allow Cost Reduction and Automated Production
The production and assembling of the 3-pin plug are heavily reliant on labor-intensive machines, which is a very important factor of production because it contributes to the increase of the production cost and time, which causes the final product to be expensive.
In comparison with the previous design, it is easy to assemble some components such as the cable sheath, cold grip, pins, and the fuse body into to the base of the plug. The new design allows the pins to be made in such a way that they allow other parts to be slid into the base of the body to avoid using many parts such as screws. In addition, the design can be altered in such a way that most of the parts simply slide into each other to make the whole assembly without using screws.
In addition, the cover can be designed to accommodate other parts by sliding them into the base using the machine instead of having them joined together by hand. The new design shows that some of the components are no longer needed and can be removed from the assembly line, which includes the pin screws, plug screws, and the cord pin screws.
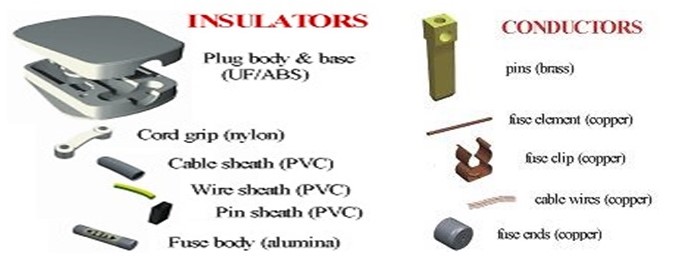
The new design, which is shown in Figure 10, shows some of the parts that have been removed because they are not necessary to make the entire assembly of the pin. 3.1 New Assembly Design
The layout in Figure 9, which is the old manufacturing method for the pin, has significant weaknesses. For instance, the reception and the quality control offices are situated behind the processing area, which makes it inconvenient for the customer when walking into the office to make inquiries. In addition, a cold storage area should be removed to create more space because it is no longer needed as some of the components that required machines that used the coolant when being produced were not needed here.
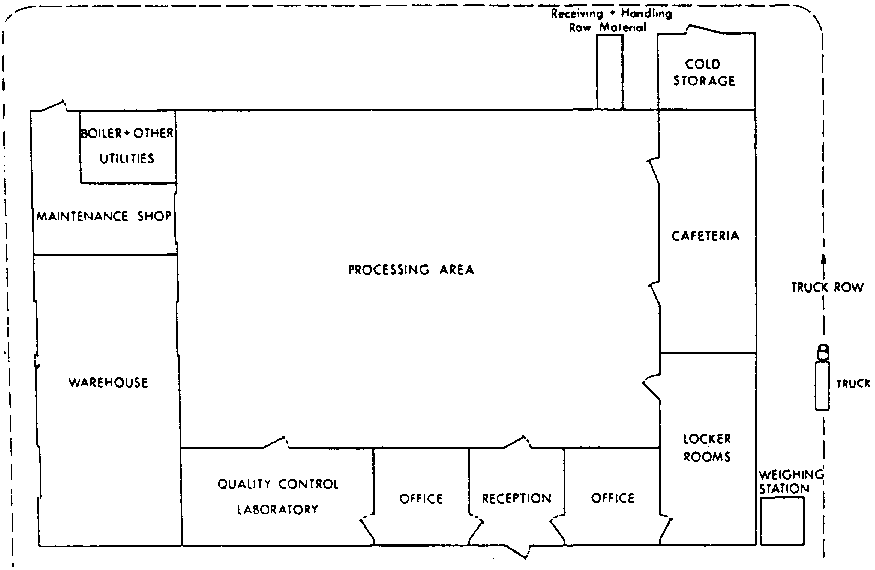
Adopted from Dodiuk and Goodman (2013).
However, the proposed design, which is shown in Figure 10, is used to overcome the weaknesses inherent in Figure 9.
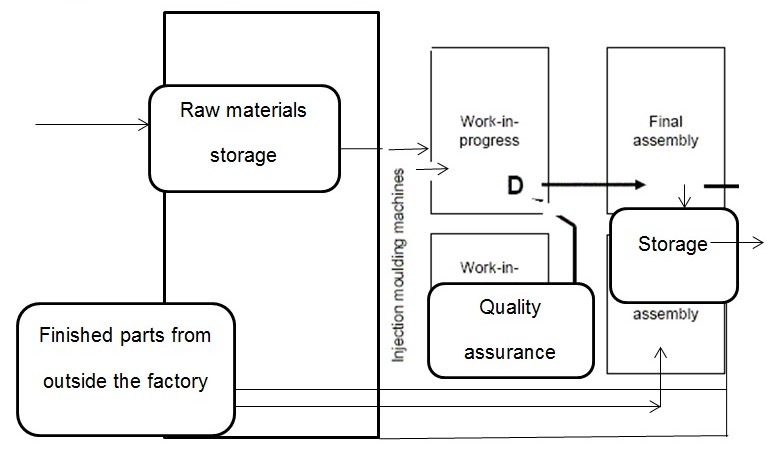
The factors that were put into account to justify the layout in Figure 11 include:
- Production volume of 2 million plugs per year;
- Ensuring effective material handling strategies;
- Ability to efficiently utilise the available space;
- The proximity of the moulding machine to the product assembly points;
- The storage space for the finished product;
- In conclusion, the proposed design will be cost-effective and will enable the manufacturer to optimise the available space.
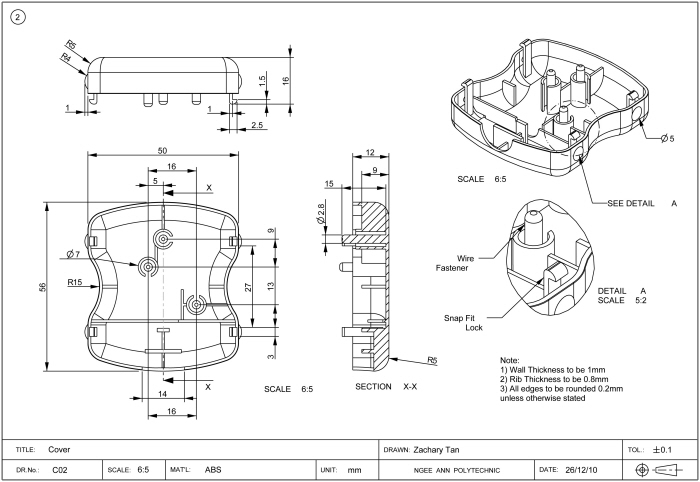
Conclusion
In conclusion, multiple methods are used to make the 3-pin plug because different processes are applied to manufacture different parts of the plug. Brass is a good candidate for making the pins, but the wire clips are outsourced to reduce the cost of investing in a new machinery and hiring skilled people to start a new production process. Urea formaldehyde is the best thermoset plastic to use because of the properties such as easiness to work on, resistance to abrasion and wear, excellent thermal and dielectric properties, and lower costs to produce in comparison with other plastics.
The manufacturer used a special taping attachment machine to cut the screws. By analysing the cost and quality issues, it is easy to determine the best production methods that are cost-effective and efficient. However, the author recommends further research to determine the cheaper methods and materials to use in manufacturing cheaper but high-quality plugs.
References
Dodiuk, H., & Goodman, S. H. (2013). Handbook of thermoset plastics. London: William Andrew.
Jahangirian, M., Eldabi, T., Naseer, A., Stergioulas, L. K., & Young, T. (2010). Simulation in manufacturing and business: A review. European Journal of Operational Research, 203(1), 1-13.
Kalpakjian, S., Schmid, S. R., & Kok, C. W. (2008). Manufacturing processes for engineering materials. London, UK: Pearson-Prentice Hall.
Wiyaratn, W., & Watanapa, A. (2010). Improvement plant layout using systematic layout planning (SLP) for increased productivity. World Academy of Science, Engineering and Technology, 72(36), 269-273.