Introduction
Cans are useful containers used in everyday life for packaging and storing beverages. Most manufacturers use aluminum as a raw material to manufacture beer and soft drink cans. For example, 95 percent of the cans manufactured in United States are from aluminum and amounts to 100 billion beverage cans in a single year. However, it is important to note that aluminum cans are not good in storing foodstuffs. In most cases, manufacturers prefer steel in manufacturing food cans. On the other hand, the inimitable properties of aluminum make it the best raw material for manufacturing cans for holding carbonated beverages. Additionally, the shiny aluminum walls make it one of the best decorating materials hence, attracting the attention of many consumers (Hosford & John, 1994, p.48).
History and Technical Description of Aluminum
The identification of aluminum dates back to 1782 as the metal widely recognized with stature in France. History asserts that in 1850s, many people preferred aluminum to gold and silver for manufacturing trinkets and eating utensils such as cups, plates and cooking pots. To crown it all, King Napoleon III became so much enthralled with military lightweight aluminum equipments and immediately sponsored its extraction. In ancient times, aluminum occurred in various places. Nevertheless, due to lack of expertise in the extraction process, aluminum remained elusive for a long period. As the most fascinated metal in 19th century, aluminum became so expensive forcing many people to look for other alternatives. However, the period of technological advancements that started after the Second World War saw a breakthrough in the extraction of aluminum and easy smelting of aluminum. Eventually, exceedingly high prices of aluminum fell considerably paving its industrial exploitation.
Before the Second World War, manufacturers made beverage cans from steel. This is because many manufacturers could not afford the high price of aluminum. Besides, since the extraction of aluminum was limited due to lack of extraction expertise, many manufacturers of cans preferred the very available steel. For instance, during the Second World War, the U.S government used steel cans to transport beer to the soldiers involved in war overseas. This period saw large production of steel pipes, the production that continued even up after the end of the war. However, in 1958, the Adolph Coors Company became the first firm to create aluminum cans amid various difficulties in the manufacturing process. Nevertheless, the produced cans weighed less (198g) as compared to the usual cans that weigh 340g. Ironically, many people preferred the aluminum cans something that incited Coors and other metal companies to develop not only abundant aluminum cans, but also quality aluminum cans (Turner, 2001, pp. 20-27).
Other manufactures created steel cans with an aluminum crown as the new model of cans. It came out that this hybrid model of cans had distinct advantages compared to purely steel cans. For example, the aluminum top distorted the galvanic reaction occurring between beer and steel giving beer twofold shelf life as compared to the one stockpiled in purely steel cans. In addition, consumers found it easier to open the aluminum top by just a simple pull-tab. Most steel cans require a special opener prevalently known as “church opener” to remove the top lid. The struggle to remove this top lid forced firms like Schlitz Brewing Company to introduce aluminum tops making other brewing companies to follow suit. By the end of 1968, at least all brewing companies had their cans sealed with an aluminum top (Smith, 1988, pp. 8-34).
Two-piece drawing and wall ironing
The technique came into limelight in 1963 following Reynolds Metal Company’s successful fabrication. However, it is imperative to note that Coors was the first company to produce hybrid cans with top and bottom aluminum tops through impact-extrusion process. Immediately after their development, giant breweries such as Coca-Cola, PepsiCo, Coors and Hamms opted to store their beverages in these cans thus becoming the first beneficiaries. According to statistics, the number of aluminum cans used in United States increased from 500 million in 1965 to 8.5 billion in 1972 and the figure continued to swell even as many brewery firms opted for aluminum cans for storing carbonated beverages. Noticeably, the modern aluminum cans have very many disadvantages as compared to the old steel or steel-and-aluminum cans. For example, aluminum cans do not rust and lengthens shelf life. Moreover, aluminum cans chills speedily, are easy to salvage and its lustrous surface is quite arresting (Hosford & John, 1994, pp.48-53).
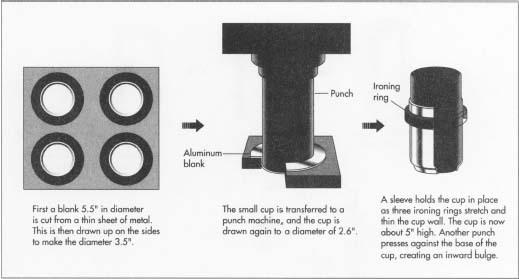
Raw Materials
As discussed in the sections above, aluminum is the main raw material for manufacturing cans. Nevertheless, aluminum occurs naturally as bauxite. After extraction, bauxite undergoes refinement in the factory and later on smelted to produce molten aluminum and cast into ingots. Manufacturers also mix small percentages of other metals to make aluminum cans. For instance, the bottom part of the aluminum can contain small amounts of other metals such as silicon, magnesium, manganese and copper. In most cases, manufacturers use recycled aluminum to manufacture aluminum cans. The ability to recycle aluminum easily makes it easier for manufacturing companies to recycle the used cans hence, sustainable development. In addition, the amount of energy used in smelting can is less as compared to the one of smelting bauxite (Alcoa Rigid Packaging, 2010, p.1).
Manufacturing Process
In most cases, the ordinary process of making aluminum beverage cans is drawing and ironing. The following procedure analyses all steps involved in manufacturing cans beginning with the cutting of blanks.
Cutting the blank
This procedure starts with the casted aluminum ingots. The casted aluminum ingots measures 76cm of 30 inches in thickness and appear as sheets of uniform thickness. Manufacturers will cut the sheet into circles (14 cm in diameter) popularly known as blanks, which will build the bottom and sides of the can. The top part of the can will form later due to the crystalline condition of the aluminum pane. It is important to note that during the cutting process, some pieces of aluminum sheet go to waste. Thus in order to minimize losses, manufacturers should make wide ingots that can produce two spread out rows, each comprising of seven blanks. By doing this, only 12 to 14 percent of the material goes to waste, and they can recycle later. Following the separation of blanks is to fold them to form a small cup that measure 4.45cm in radius.
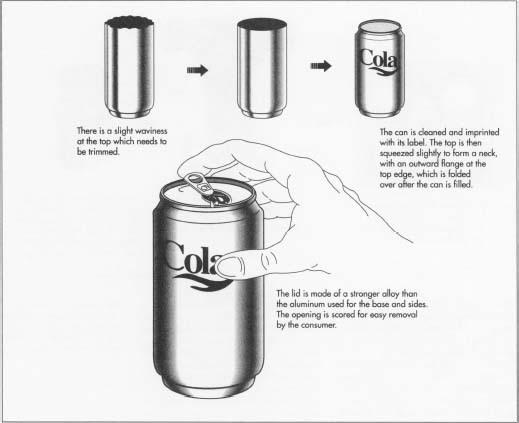
Redrawing the cup
The succeeding step is to move the pinched diminutive cup into a subsequent device to continue the procedure. The sleeve of the second machine puts the cup in position such that immediately the punch lowers; it forms circular cups of diameter 6.6 cm. on the same note, the height of the cup roses from 3.3cm to 5.7cm. Next, the ironing rings will elongate and slender the cup walls to form the desired shape. After slandering and thinning, the cup now measures 5 inches or 13cm in height. Next, knock the bottom to bend inside in order to counteract the pressure exerted by the carbonated beverage. In addition, the manufacturer designs the bottom part in such a way that it appears thicker than the top part due to the pressure exerted by the carbonated beverage.
Trimming the ears
The third procedure of can manufacturing is trimming the ears. You realize that after successful drawing and ironing, the top of the cup appears wavy characterized by small ripples or “ears”. However, in a move aimed at controlling the development of “ears”, diverse aluminum companies who have studied this incident expansively control the rolling of aluminum sheet in order to manipulate the height of the ears. Nevertheless, due to trimming of the ears, some pieces of aluminum go to waste.
Embellishment
The producers do not need auxiliary concluding of the can for example, buffing up since the cup is shimmering and smooth following the above procedures. Habitually, after the cup has undergone trimming, the producers will clean and label it and then squeeze the top to form a neck and an out-ward flange where the lid will rest (Alcoa Rigid Packaging, 2010, p.1).
The lid
So far, we have discussed how aluminum builds the bottom and sides of aluminum beverage cans. The only remaining part is the lid, which covers the beverage stored in the can. Additionally, the procedure has also elaborated why we need a thicker material and an in-ward bulge at the bottom, that is, to contain the pressure exerted by carbonated beverages. Likewise, the lid ought to be strong and stiff, and even stronger and stiffer than the base. Thus, in order to make a stronger and stiffer lid, manufacturers mix aluminum with some alloys of magnesium and manganese, which results into a strong and stiff metal. In addition, the lid is normally thicker than the sides or bottom of the can. Next, the designers will cut the lid into circular pieces of diameter 5.3cm (2.1 inches). Clearly, we notice that the lid appears smaller as compared to the diameter of the walls (6.6cm or 2.6 inches). Subsequently, the manufacturers will then stretch the middle of the lid vaguely upwards before moving it to another machine for riveting. Up to this point, we have a riveted lid. The manufacturer will then bring in another piece of metal called a pull tub and insert it beneath the rivet. The next step is to score the lid so that when opening, the consumer will only pull the tab and leave the can open. The process of manufacturing an aluminum lead is almost over. The quality control division will have to check whether the cans have cracks or pinholes. Any can with pinholes or cracks becomes defective (Singh, 1993, 129-131).
Filling and seaming
The final stage of can manufacturing is filling and seaming. At this particular stage, we have a can with a neck and a complete lid. Next, the manufacturer will move the aluminum can, fix it tightly against the bench of the filling device, and pour the carbonated beverage inside. After filling, next is adding the lid and then bending the upper flange towards the lid completely seaming the aluminum can. We now have a complete aluminum beverage can ready for the market.
Byproducts and Alternatives
It goes without saying that during the drawing and ironing can manufacturing process, some aluminum materials get lost on the way. For instance, during the cutting of the blanks and trimming of the ears, several pieces of aluminum remain unused. Nevertheless, through recycling, manufacturers can join the small pieces together for the next process. In addition, used aluminum cans also undergo recycling for use in the next manufacturing process. Noticeably, the recycling of aluminum is vital to any can manufacturing industry, as the factory is able to save up to 95 percent of energy. This is on one of the advantages that make aluminum the best material for manufacturing cans as compared to steel or all-steel-and-aluminum cans, which seem hard to recycle.
Nevertheless, manufacturers have also come up with mechanisms of saving waste during the can manufacturing process for example, developing rigid sheets circumspectly managing the whole process to ensure minimal loses during cutting of “ears”. Furthermore, the reason why manufacturers design a smaller lid as compared to the sides is to minimize the huge loss of aluminum. Following the continued rising demand of aluminum cans, many manufacturers are studying ways of reducing the lid further to conserve more aluminum (Larson, 1993, pp. 30-31).
Conclusion
The rising demand of cans has forced manufacturers to increase the production of aluminum cans in order to curb this demand. Today, aluminum companies all over the world produce several billion cans each year for various uses such as storage of carbonated beverages (beer and soft drinks), and foodstuffs. Thus, in the wake of this growing demand of cans, the future production of cans chiefly depends on the designs that save energy, money and materials. Other incidents include designing cans with smaller lids and neck diameters to minimize losses. So far, aluminum cans enjoy much preference as compared to other cans as it doubles shelf life, does not rust, and is recyclable.
Reference List
Alcoa Rigid Packing. (2010). How aluminum cans are made. Web.
Hosford, F. & John, L. (1994). The Aluminum Beverage Can. Scientific American, 48-53
Larson, M. (1993). New Ideas Come In Cans. Packaging, 30-31.
Singh, S. (1993). Internal Gas Pressure on the Compression Strength of Beverage Cans and Plastic Bottles. Journal of Testing and Evaluation, 21(2), 129-131.
Smith, G. (1988). From Monopoly to Competition: The Transformations of Alcoa, 1888-1986. Cambridge University Press.
Turner, T. (2001). Can making for Can Fillers. Boca Raton: CRC Press.