Abstract
Efficient management of resources and activities in an organization is essential for the attainment of the set goals. The conversion of requisite inputs into intended outputs depending on the industry of operation requires materials, decisions, responsibilities, and finances to be managed prudently for the realization of streamlined operations. This paper investigates the management of operations at IKEA UAE, which is a leading company in the furniture industry in the UAE and across the globe. The company has applied various tools of quality management. The research design for this study has taken a descriptive approach that illustrates the different transformational processes at IKEA.
A discussion of the findings based on some theories of operations management further enhances the comprehensiveness of the topic concerning IKEA UAE. The application of quality control systems, flat packing, layout, strategic location, and stylish design of its products underscores the commendable operations management within the company. However, IKEA’s autocratic leadership style poses a threat to the sustainability of its strategic and operational plans. Therefore, it is recommendable for the company to shift to a democratic approach for its leadership in a bid to engage employees in various decisions concerning its operations.
Introduction
The essence of running a business is to satisfy the needs of the public through the provision of goods and services in a bid to make profits. Organizations have systems that facilitate the production of goods and services guided by individual strategies that aim at ensuring efficiency in all the departmental operations. Therefore, “the management of the processes involved in the production of goods and services should be run skillfully for the realization of the organization’s goals” (Kamauff, 2009, p. 104). Operation management (OM) encompasses the decisions, activities, and responsibilities of managing the resources used for the production of goods and services for public utilization (Kamauff, 2009).
One particular company that depicts the various aspects of OM is IKEA UAE. IKEA is a “Swedish company, which was formed in 1943 by Ingvar Kamprad” (Kristofferson, 2014, p. 73). Since then, the company has scaled the heights to become a renowned international retail furniture company that has retail outlets in 38 countries. The company manages its operations out of Sweden through contracts with over 1300 direct suppliers (Kristofferson, 2014).
For this reason, the company has become one of the largest furniture enterprises in the world. The company strives to better the everyday life of the majority. IKEA’s vision is to provide a broad range of home furnishing products that are functional and well-designed (Kristofferson, 2014). The rationality of choosing to investigate the OM strategies for this project is because IKEA has various well-managed processes that foster its growth. IKEA’s principles are concentrated on equity and economy, which necessitates the evaluation of how its processes translate into high-quality furniture products and services.
Topic Statement
This study seeks to analyze how IKEA applies the concepts of operation management to achieve its vision. In this light, all the significant processes that are relevant to the transformation of inputs into outputs at IKEA form the basis for this research. The context of this research will be concerned with materials planning, expenditure management, structural analysis, equipment maintenance, factory management, and other relevant operations. The research will majorly focus IKEA’s operations in the UAE since it has its retail stores in the region. Thus, the study is useful for purposes of comprehending how OM systems work.
Methodology
This research will take a descriptive approach as it seeks to illustrate how IKEA applies its OM strategies. Efforts to determine, identify, and describe what influences the OM at IKEA will be the primary focus of this research. Collection of data will be based on the IKEA case study concerning its conduct of operations. Quality management and improvement tools such as the DMAIC tools will be considered as sources of data for the study. The analysis of OM elements applied at IKEA’s UAE retail stores will be based on evaluation tools such as the Six Sigma and the DMAIC methodology. However, the analysis will be qualitative in most cases since it is based on the managerial strategies involving roles of managers at different levels. Additionally, the assessment of the available data will be based on the company’s application of the tools for the improvement of its operations geared towards the transformation of materials into finished products.
The use of OM concepts at IKEA
The establishment of IKEA retail shops globally has enabled it to display its wide range of furniture items. The affordability of its flat pack furniture that is in line with the company’s economy principle has facilitated the surge of the company to become one of the largest furniture company globally (Dahvig, 2011). For this reason, there is need to comprehend how the application of tools such as the six sigma has facilitated the company’s global impact.
Application of Six -Sigma at IKEA
The Six Sigma approach to business operations is an excellent move towards enhancing the quality of the products and processes in an organization. In this case, operation management becomes efficient since the quality management tool only allows 3.4 defects for a million processes (Braunscheidel, Hamister, Suresh & Star, 2011).
The application of the Six Sigma tool is aimed at identifying errors and eliminating them from the streamlined processes. Various steps are usually followed when implementing the tool whereby aspects such as cost reduction, profits maximization, customer satisfaction, and environmental pollution are considered. In a bid to secure efficiency in the steps, statistical methods of data collection using tools such as the Pareto charts and Ishikawa diagrams could be used to analyze the collected information. For this reason, the use of the Six Sigma to evaluate IKEA’s OM is essential since the company is focused on offering quality furniture products to its globally situated customers (Hansegard, 2013).
The use of the Six Sigma tools is enhanced by IKEA’s application of the DMAIC model in its operations. This methodology entails defining, measuring, analyzing, improving, and controlling the transformation of inputs into outputs ready for the market (Dahvig, 2011). Additionally, the application of research techniques based on the Six Sigma at IKEA is appropriate since the company has conducted some projects based on the methodology. For instance, the “IKEA Group and SSD Global, Inc. Lean Six Sigma Project was implemented on September 2010 to enhance the company’s online customer experience” (Kristofferson, 2014, p. 103). The grading of employees at IKEA in different categories including green belts, yellow belts, and champions is another aspect of the six-sigma application, which is relevant to this study (Dahvig, 2011).
IKEA’s transformation process
Since IKEA’s vision is to provide quality furniture items at affordable rates, the company bases its strategies along these lines. This aspect is evident in the quality of its products, affordability, attractiveness, self-assembly, catalogs, self-service at its stores, and cheap product marketing strategies. In so doing, IKEA enhances its efficiency in various ways. For instance, the self-service aspect of its operations ensures that the company minimizes its personnel and delivery costs since individuals and small families can select items, purchase, and use their transportation.
The company’s focus on quality products has improved its relationships with suppliers due to the expected standardization requirements. Efficiencies in space and transportation of furniture to the designated locations have been enhanced due to the flat packaging process (Kristofferson, 2014). Consequently, this move has enabled the improvement of operations in warehousing and transportation, thus streamlining logistics and supply chain management. The figure below shows how IKEA’s operations management flows.
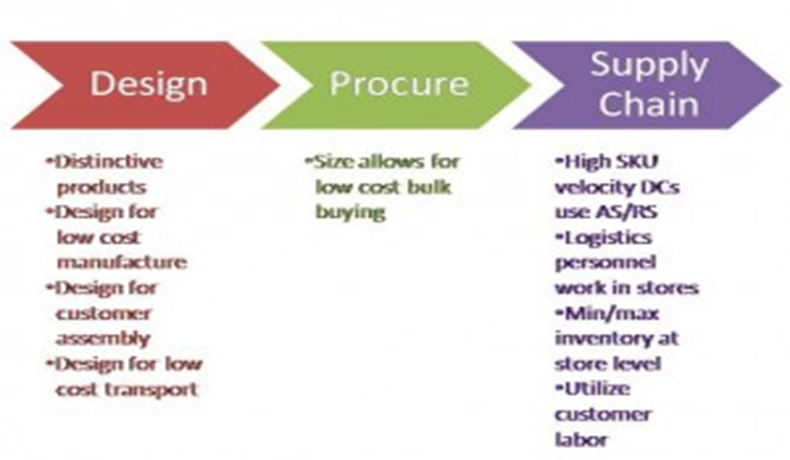
IKEA’s strategic location in the UAE has also been attributed to its commendable operations management team. The large size of its stores minimizes its expenses while allowing clear visibility of the displayed furniture. The movement of customers and staff in the spacious stores improves the customers’ experience in the shops and the workers’ working environment (Kristofferson, 2014). Therefore, the management of operations in the stores portrays the effectiveness of the processes behind the finished products.
Findings
Operation managers at IKEA including those situated in the UAE retail stores ensure that the conversion of inputs into desirable outputs follows steps that are in line with its vision. IKEA safeguards its competitiveness in the market by cutting its production costs and at the same time not compromising quality. Added quality services have given IKEA and edge over its competitors since customers prefer shopping in environments that observe the best customer service opportunities. According to Banker (2009), quality services at IKEA are manifested by the provision of catalogs to customers with staff equipped with items such as tape measures, notebooks, and pens, ready to meet their specifications.
The transformation process at IKEA if further fostered by the services that it provides through the sale of quality furniture at affordable prices. For instance, “the company has a special section for children to play as their parents shop” (Kristofferson, 2014, p. 142). This aspect portrays how IKEA is sensitive to the particular needs of different customers. Shops and bars offering affordable Swedish products make the shopping experience at IKEA friendly to customers.
IKEA manages its production operations by partnering with subcontractors located in various parts of the world since it does not have a manufacturing plant. However, research for quality improvement is based in Sweden where the company is headquartered (Kristofferson, 2014). The connotation of this aspect is that the enterprise can minimize the cost of production and ensure that suppliers maintain quality through constant research.
IKEA approaches the transformation of materials into designs that have the Scandinavian identity. The management of operations at the production levels ensures that the use of natural wood and new materials of attractive colors are used together with high technology to spread the Scandinavian culture to the outside world. Kristofferson (2014) argues that the company’s ability to display the Scandinavian modernity to other regions has facilitated the company’s competitiveness in terms of identity and quality.
Discussion
The application of the Six Sigma metric in the management of operations at IKEA handles its efficiency in improving quality through economic means. IKEA has minimized defective products through research at its Swedish headquarters. In so doing, the company has managed to enhance the development of it furniture products. Therefore, reducing errors that would cost the reputation of IKEA in the UAE has facilitated its competitiveness in the furniture industry. The unceasing research that focuses on the production of furniture that identifies with the Scandinavian identity has handled the distinctive products that fit well with the middle-class as well as the upper class. In this light, the company has been in a position to satisfy the needs of customers from different social classes around the UAE.
The application of the DMAIC methodology at IKEA underscores its efficient operations management. The Six Sigma tool has been applied severally to the processes at IKEA to enhance customer experiences and foster competitiveness. For instance, in 2010, the company came up with the “IKEA Group and SSD Global, Inc. Lean Six Sigma Project” aimed at reinforcing its online platforms for a better customer service. The project portrayed the essence of the application of the DMAIC model since a definition of how the customers ought to be served was laid down. Measuring its viability led to the analysis of its customer needs found out that an improvement of the online services was essential for the management of its operations (Dahvig, 2011).
In this case, the transformation of inputs in terms of materials, decisions, and responsibilities could be streamlined in agreement with the needs of the clients. The online platform also ensured that IKEA is not erratic in its strategies towards embracing technological advancement, which is an important aspect of the 21st Century society. For this reason, IKEA explored wider markets for its outputs through online engagements with potential customers, thus staying competitive.
Since IKEA does not have a factory to supply its UAE outlets directly, suppliers from the region have been contracted to fill the production gaps. The Theory of Swift, Even Flow clarifies that production operations should be streamlined evenly and swiftly (Stevenson, 2008). This aspect implies that materials necessary for the production of the high-quality furniture need to be at the assembly point in time for a transformation process. Value addition of the products at the UAE outlets ensures that the theory of operation management is fostered in the processes involved in the creation of well-designed furniture.
According to Stevenson (2008), the swift movement aspect of the theory holds that impediments need to be removed for the minimum time to be spent for materials to reach their destination. In this light, IKEA’s collaboration with worldwide suppliers improves its logistics and supply chain operations that are geared towards the provision of quality and affordable furniture items. For this reason, the company has been in a position to operate profitably in the UAE and other 37 nations. Additionally, speedy and timely operations to meet the needs of customers attributes for the IKEA’s position in the furniture industry.
IKEA’s stores layout complements its strategies towards the enhancement of its operations in the UAE, which can also be attributed to its success. The design of its retail shops favors pleasant shopping experience, thus adding value to the furniture products. The availability of snack joints, restaurants, toddlers’ section, and other complementary services improves the customer experience since different customers have varying needs (Kristofferson, 2014).
Basing this perspective on the Theory of Swift, Even flow, value addition of the finished products is facilitated by the provision of complementary services and products available in the UAE retail stores. The layout of the retail stores is planned in a way that it is friendly for smooth operations since it incorporates a warehouse and the showroom. Customers are provided with ample parking space, thus facilitating movement and loading of purchased furniture to their vehicles. Company trucks can also access the warehouse for delivery of new items. The spacious nature of the IKEA’s stores in the UAE makes it easy for customers to move in, make orders, receive their goods, and make payments in the shortest time possible.
The discussion above clearly unmasks IKEA’s priority in promoting effectiveness and efficiency in operations management. The application of OM strategies based on theories and quality improvement models in every aspect of its operations highlights the company’s features of a working and efficient OM system.
Recommendations
Despite the efficient management of IKEA’s operations in the UAE, there is room for proposals that aim at enhancing its mechanism. The recommendations are geared towards the elimination of challenges that inhibit the realization of the company’s vision. This aspect implies that factors that pose threats to the attainment of quality furniture at affordable prices need to be evaluated for proper action.
The organizational structure at IKEA tends to adopt an autocratic style of leadership. Ingvar Kamprad, the founder of IKEA, used the authoritarian style of leadership to manage the operations of all the company’s departments. Despite his resignation in 1986, Kamprad still influences the management of the company. Reports indicate that he applies his autocratic leadership techniques that have negative implications for the employees’ motivation (Kristofferson, 2014).
Therefore, the organizational culture is biased towards the autocratic style of leadership, which is incompatible with the modern democratic style of leadership. For this reason, external agencies tend to criticize the organization’s leadership mechanisms. In spite the effective operations management, the company risks losing its competitive advantage if increased criticism on its style of leadership prevails.
IKEA needs to embrace a democratic style of leadership. In so doing, the workers would be motivated to take part in decision-making on matters of improving the company’s operations. Valuable insights would emerge, as employee engagement would provide new strategies for developing areas such as the inventory systems. Representative and participatory leadership styles invite innovations for the company to enhance the quality of its furniture towards the attainment of quality products at affordable rates.
Therefore, a rationalized improvement plan is necessary for the restructuring of the leadership style from autocratic to a democratic one. The plan considers the effectiveness of the operation management so that it does not interfere with the already well-functioning processes. In a bid to execute the intended changes in the organization, different models can be applied. However, the Burke-Litwin model is the best option for this case.
The model holds that organizational change on leadership navigates from the top (external environment) to the bottom levels (performance) (Stevenson, 2008). In this light, the top management has the greatest implications for the external environment that monitors the operations of a particular organization and it is always ready to criticize it when discriminative processes exist. On the other hand, the transformational processes in the internal environment have the greatest impact on the organization’s performance. The following flow chart indicates how leadership style changes would strengthen operations management at IKEA.
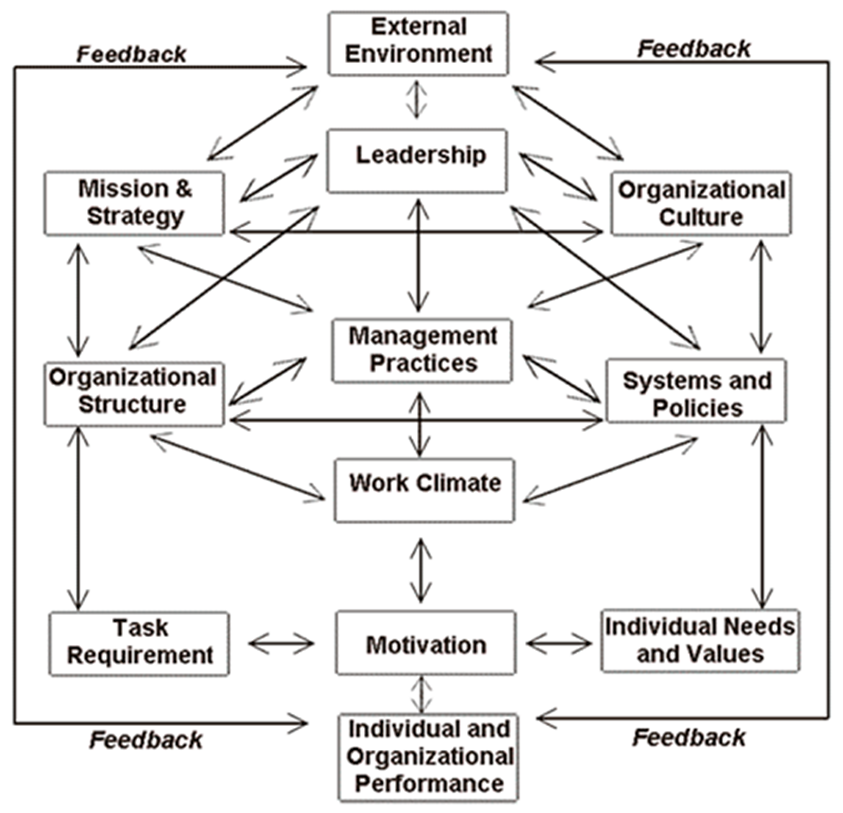
The flow chart shows how the Burke Litwin model would change the transformational processes if a democratic system of leaderships were adopted. Leadership changes at IKEA would improve motivation, which is in line with the company’s mission strategy. Consequently, transformational changes within the organization would be achieved through the adoption of democratic systems of leadership.
Conclusion
Operational management strives for the transformation of inputs into meaningful outputs. This aspect entails the management of material, decisions, responsibilities, and control of costs to achieve the predetermined goals. IKEA is one of the companies that portray the different attributes of OM that have been implemented effectively and efficiently. The company has been in a position to harmonize its operations per its vision of providing quality and affordable furniture to the public. Thus, its exemplary performance offers an opportunity to investigate the underlying factors responsible for its success.
The application of the Six Sigma methodology uncovers the various factors responsible for the effective operations management. Cutting production cost through contacting suppliers, designing the retail outlets to meet the customers’ needs, and sophisticating its online platform are some of the operational strategies accountable for the company’s success. However, its leadership style poses a threat to the company’s image since it is autocratic in nature. A recommendation to adopt the democratic style of leadership tends to suit the enhancement of operations management at IKEA.
References
Banker, S. (2009). In-Store Logistics at IKEA. Web.
Braunscheidel, M., Hamister, J., Suresh, N., & Star, H. (2011). An institutional theory perspective on Six Sigma adoption. International Journal of Operations & Production Management, 31(4), 423 – 451. Web.
Dahvig, A. (2011). The IKEA Edge: Building Global Growth and Social Good at the World’s Most Iconic Home Store. New York, NY: McGraw-Hill. Web.
Hansegard, J. (2013). The Long, Slow Process of IKEA Design. The Wall Street Journal. Web.
Kamauff, J. (2009). Manager’s Guide to Operations Management. New York, NY: McGraw-Hill. Web.
Kristofferson, S. (2014). Design by IKEA: A Cultural History. London, UK: Bloomsbury Academic. Web.
Stevenson, W. (2008). Operations Management. New York, NY: McGraw-Hill. Web.