Introduction
The need to move liquids from one point to the other is as old as the history of humankind. Such liquids serve such needs as irrigation, domestic purposes, and locomotion among others. Primitive ways of moving liquids from one point to the other existed before the invention of the pump, which has made it easier to move such liquids. This essay seeks to look at the history of pumps, different types of pumps, and their uses.
Typical Applications, their Advantages, and Disadvantages
Single Stage Horizontal Split Centrifugal
The imbibing and suppuration nozzles in a single stage horizontal split centrifugal are integrally built in the lower half of the chamber and on the same horizontal centreline. The aperture configuration is side by side (Ruhrpumpen, 2013).
Single stage horizontal split centrifugal has several advantages. It is easier to set up, examine, maintain and service since its rotor and internals are easier to access. The single stage horizontal split centrifugal works well with several drivers like electric motors and engines (Centrifugal-Pump.org, 2013).
In addition, it comes in of the designs: either overhang, which has low imbibing force service, or between bearing which has high imbibing force service (Centrifugal-Pump.org, 2013). The centrifugal is available in different nozzle types to simplify or match the outside local piping. It is appropriate for the majority of indoor setups (Centrifugal-Pump.org, 2013). The disadvantages of Single stage horizontal split centrifugal include the fact that it has limited applications and needs a larger footprint (Centrifugal-Pump.org, 2013).
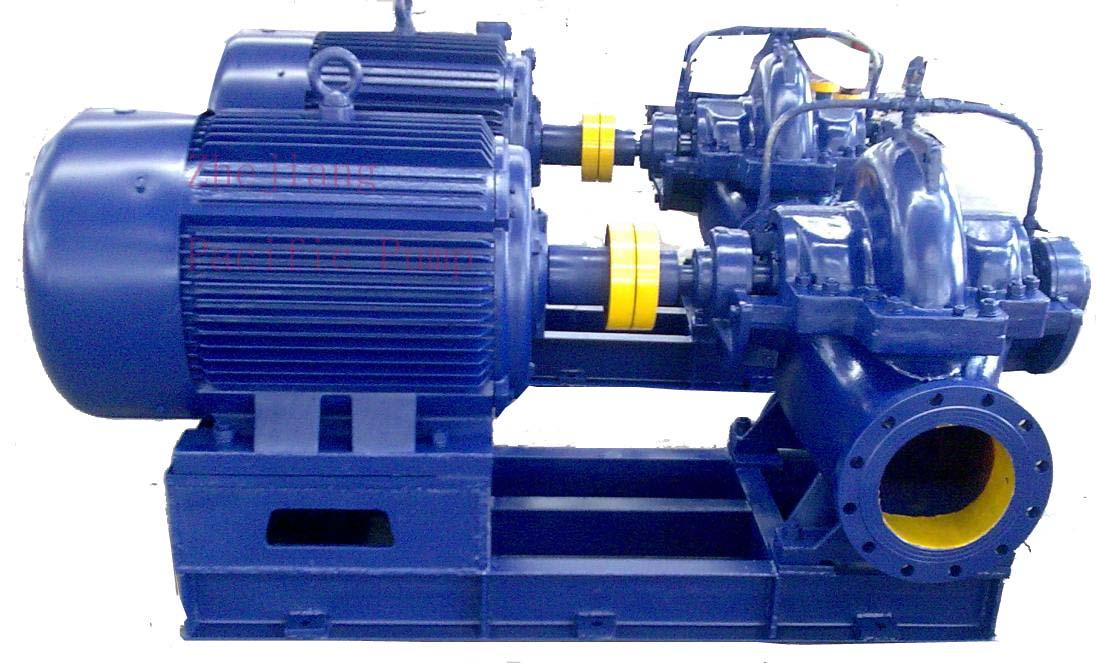
Horizontal Split Double Suction Centrifugal
These are pumps with an axially split casing, which allows the removal of the whole rotor leaving the piping and motor intact (Thinking Buildings Universe, 2013). They have shut impellers with double curved vanes with two bearings on both sides of the pump, which have grease lubricated profound groove circular ball bearings (Thinking Buildings Universe, 2013).
The advantages of a horizontal split double suction centrifugal include the fact that it does not occupy a lot of space, unlike most other pumps. An inspector can open the lower chamber with interfering with the motor or the pipe system and this enables the technician to detect any problem without necessarily disassembling the pump. The horizontal split double suction centrifugal needs only one individual to repair it as opposed to a team of technicians.
This type of pump is durable and can operate efficiently for over 70 years. The pump is fitted with the double-imbibing impeller to increase its efficiency. (Rishel, 2007)The only known disadvantage is that the impeller suffers from structural weaknesses but in very rare cases (Rishel, 2007).
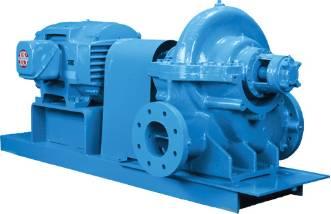
Vertical inline centrifugal
This type of pump has a single stage shut impeller, with double flexure vanes for maximum efficiency and good imbibing performance (Thinking Buildings Universe, 2013). The main advantages of this type of pump include their high efficiency due to the double flexure (Thinking Buildings Universe, 2013). They are offer services, which are free of any vibration. Vertical inline centrifugal pumps also allow the technician to reach the impeller and the technical seal without interfering with the imbibing and the discharge piping (Thinking Buildings Universe, 2013). One disadvantage of this type of pump has to do with the seal or pump. If anything bad happens to the seal or pump, the damage spreads to the motor too (Centrifugal-Pump.org, 2013).
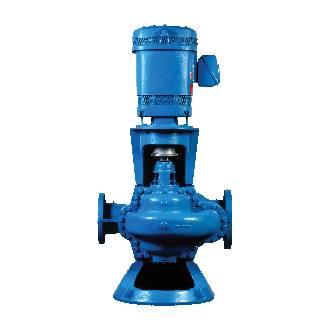
Axial Split Multi-Stage Centrifugal
The impellers in axial split multi-stage centrifugal set up fully symmetrically and have certain hydraulics execution. The outlet and imbibing nozzle are found at the lower half chamber. The pump has the following advantages (Thinking Buildings Universe, 2013). An expert can disassemble the pump without interfering with the pipework. It has anti-thrust bearings, which effectively absorb base thrusts. The only disadvantage is the structural weakness of the impeller (Thinking Buildings Universe, 2013).
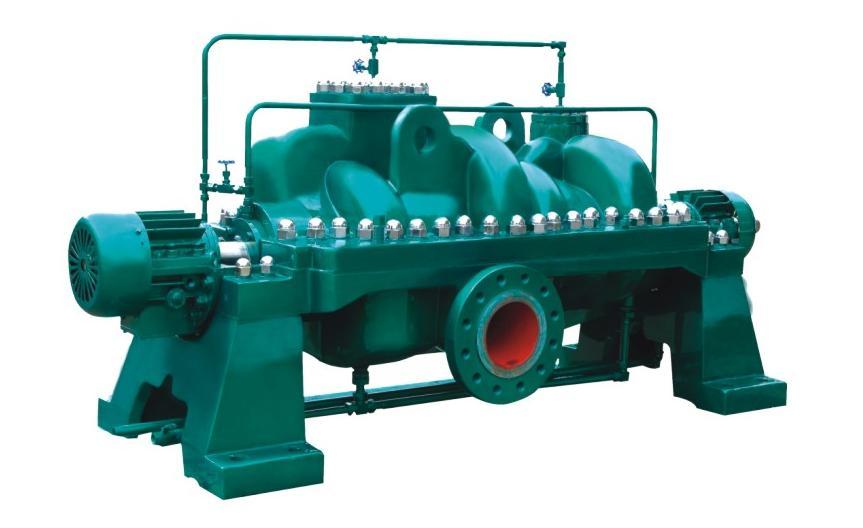
Deep Well Vertical Turbine Centrifugal
This type of pump has three main parts. The bowel assembly, vertical pipes, and shaft work and outlet head. The bowel assembly consists of cast iron while the column pipes and the outlet head have carbon steel and cast iron respectively (Centrifugal-Pump.org, 2013). They are advantageous in that it is easy to add or remove stages from this type of pump. The disadvantage of a deep well vertical turbine pump is the fact that it is hard to inspect it because of its design (Centrifugal-Pump.org, 2013).
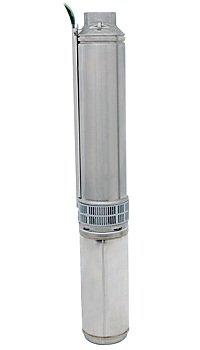
Gear Type Positive Displacement
This type of pump displaces a certain amount of liquid with each cycle of the pumping systems by trapping the liquid between the pumping systems and a static chamber. The following are the advantages of this type of pump (Centrifugal-Pump.org, 2013). A positive displacement pump can work at high pressure, are relatively small and are very effective. The only disadvantage, which is rare, is leakages from these pumps (Centrifugal-Pump.org, 2013).
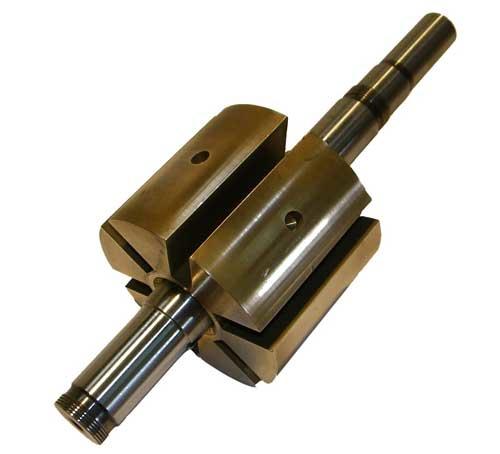
Reciprocation Injection Positive Displacement
This type of pump transfers an amount of liquid by a crankshaft, central cam or an alternating liquid in a reciprocating movement (Centrifugal-Pump.org, 2013). This type of pump carries with it the advantage of working under high pressure and with high speed (Centrifugal-Pump.org, 2013). It is disadvantageous in that in the event of mechanical breakdowns pressure imbalances occur (Centrifugal-Pump.org, 2013).
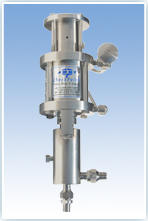
Principles of Operation of a Centrifugal Pump
This type of pump depends on centrifugal pressure to operate. Centrifugal pressure causes an object to move in a circular design by making it pull a distance from the middle axis as seen in the diagram below.
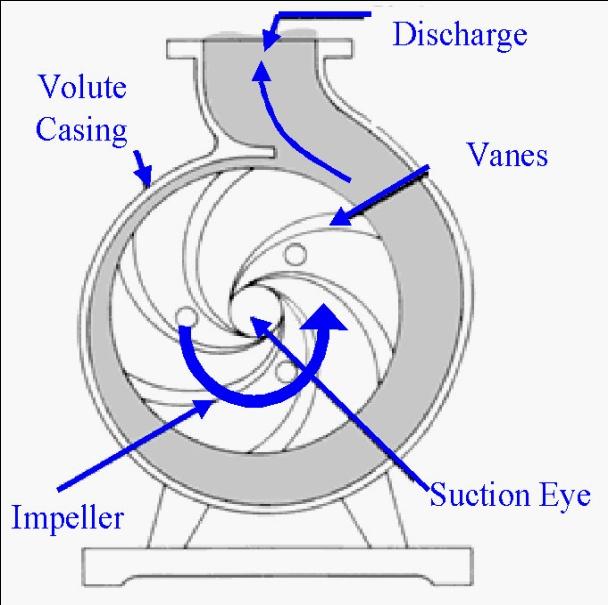
Horizontal Overhung Centrifugal Refinery Pump
This type of pump has three basic components: casing, impeller, and the shaft, which are made of stainless steel.
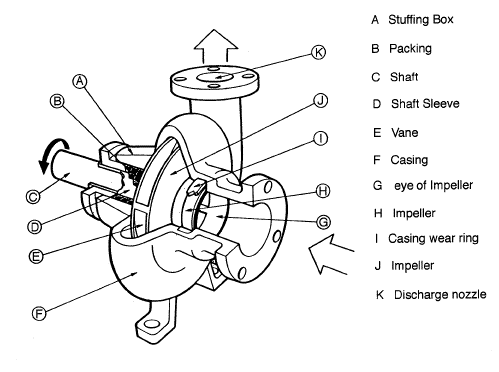
Typical Centrifugal Pump System Installation
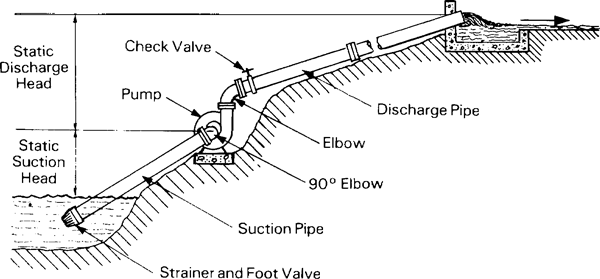
Construction and Operating Principles of a Reciprocating Pump

Key Elements of a Typical Reciprocating Positive Displacement Pump
The pump is made of stainless steel on the casing and cast iron in the inside
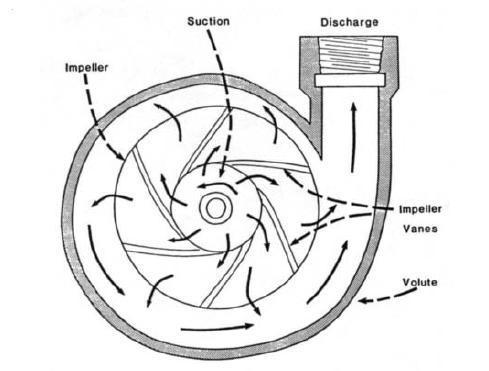
Construction and Operating Principles of a Rotary Positive Displacement Pump
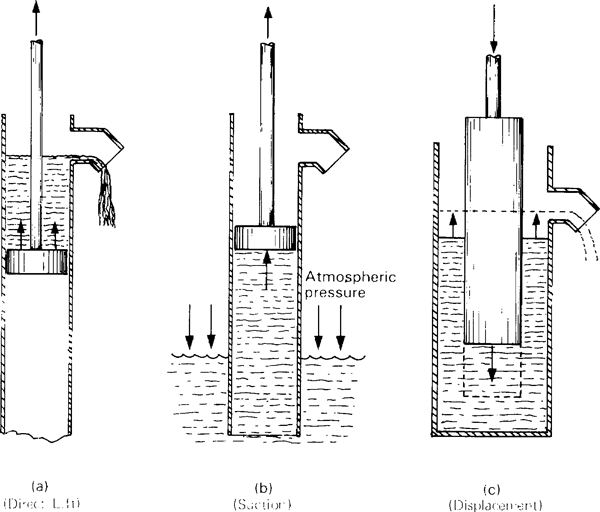
Key Elements of a Typical Rotary Positive Displacement Pump
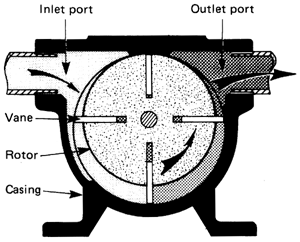
Six Common Types of Positive Displacement Pumps Found in the Chemical Process Industries
The six types of positive displacement pumps include the rotary type, which moves liquid using the tenets of rotation (Pump, n.d.). The second type, reciprocating type, works by allowing fluid to flow into it as the cavity on the imbibing side expands and the fluid moves out of the outlet as the cavity caves in (Pump, n.d.). The third type, the gear pump, utilizes two meshed levers rotating in a compact chamber and pumps out fluids by capturing it in the tooth gaps (Pump, n.d.). The fourth type, progressing cavity pump, has a piston that enters a heavy rubber channel and as the piston rotates, the liquid rises up the rubber channel (Pump, n.d.).
The fifth type, roots pumps, produce a non-interrupted flow of liquid by imbibing at the outlet (Pump, n.d.). The sixth type, peristaltic pump, has a flexible cylinder in it. As the rotor moves, it pressures the liquid to move through the cylinder (Pump, n.d.).
Two Basic Types of Seals Used in Centrifugal Pumps
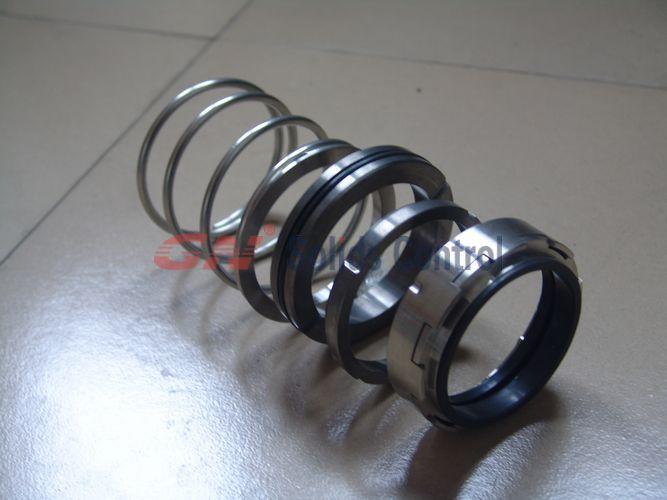
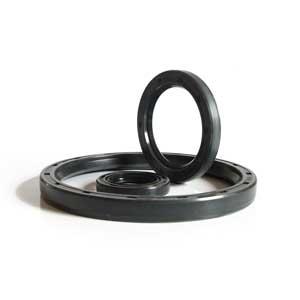
Manufacturer’s Performance Curves
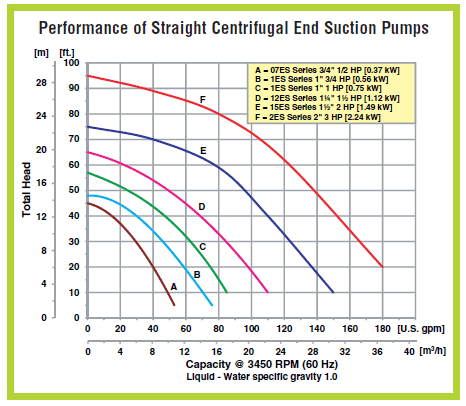
References
Centrifugal-Pump.org. (2013). Horizontal vs. Vertical Design. Web.
Engineering Tutorials. (2013). Lab Manual: Working Principle of Reciprocating Pump. Web.
Mud Solids Control Equipment. (2013). Mechanical Seal in Centrifugal Pump. Web.
Pump. (n.d.). Web.
Rishel, J. B. (2007). Horizontal Split-Case Centrifugal Pumps: Five advantages help achieve efficiency, quality, and low first costs. Applications and Resources , 2-3. Web.
Ruhrpumpen. (2013). Single Stage Horizontal Split Case Pumps. Web.
Thinking Buildings Universe. (2013). Grundfos PACO Double Suction Split Case Pumps – Horizontal and Vertically Mounted. Web.