Abstract
Underwater welding is an area of research where many studies have focused since many challenges are yet to be addressed. This paper seeks to make an overview of underwater welding practices by providing a brief classification, the principals employed, and the merits and demerits of this practice. In the past decades, the safety of the underwater welding practice has been put into question, thus prompting the need to address the issue.
This paper will discuss the Remotely Operated Vehicle (ROV) for welding and show how it is helping to mitigate safety issues. This paper will also explore the flux arc cored welding to demonstrate how it is applied underwater. More evaluation is done to determine newer processes that are considered as convenient and secure. Further discussion is made to evaluate the standard requirements for underwater welding with respect to the American Welding Society Standards. Regarding welding parameters, water depth will be shown to have a greater impact on bead geometry as compared to other underwater welding parameters. Finally, problems and areas for future research are highlighted.
Introduction
Purpose
The purpose of this paper is to provide a detailed report on the current state of the underwater welding practices. In addition, it highlights the viability of the safety measures linked to Remotely Operated Vehicle (ROV), friction-welding mechanism, and flux-cored arc welding. This paper will fulfill the Engineering course requirements to depict the underwater wet welding technology as a fundamental tool for underwater fabrication activities.
Background
The escalating reliance on underwater welding, particularly for general underwater repairs where ground welding is undesirable, has prompted the need to research further to increase efficiency in this activity. According to Verma and Garg (2012), a plethora of techniques is available for on-ground welding, but welding in the presence of water is a major challenge even though the practice is becoming inevitable. The majority of underwater welding activities are undertaken at deep ends to eliminate the probability of ship collisions. In this regard, security challenges are exacerbated by the fact that most of the technologically complex activities involve repairs and maintenance. The possibility of underwater welding was identified over 100 years back, and the British Admiralty was the first to undertake underwater welding for repairs and maintenance of ships below the water surface (Verma & Garg, 2012). However, the evolution of underwater welding has since experienced rapid changes linked to the rising levels of technology.
In 1946, the Netherlands developed unique waterproof electrodes, which boosted the quality of underwater welds since corrosion was eliminated. Apparently, the number of underwater structures such as pipelines, oil, and mineral drilling facilities is being set in large numbers. These structures are subject to mechanical failures and damage from natural occurrences such as storms. However, for continuity, underwater welding becomes inevitable during such repairs. Therefore, ethical and moral considerations regarding human safety cannot be ignored at the time when evaluating the most viable underwater welding technology to adopt. As a result, flux-cored arc welding (FCAW) has been used for underwater welding activities since it is deemed as the most efficient and relatively risk-free (Hi, Zheng & Huang, 2013).
Nonetheless, working towards efficiency, the engineering field has been faced with various emerging challenges, which need to be reevaluated to come up with newer and more effective underwater welding models. According to Hi et al. (2013), FCAW has proved to be very expensive; hence, the need to design low-cost models, which are more compatible with the new technology.
Scope
This paper will review research based on evaluating underwater weldings such as FCAW, ROVs, and alternative possibilities aimed at improving safety. Particularly, the paper will elaborate on the classifications of underwater welding, which include wet and dry underwater welding. The bulk of the paper will focus on underwater wet welding. Even though underwater chamber welding, which entails welding in a dry immersed chamber, has proven to be an alternative solution to the issue, this approach is limited in scope. This assertion holds because dry immersed chamber welding can only be done for regular structures like pipelines, which is very costly and time-consuming. For underwater repairs, welding in the chambers is impractical. Therefore, welding in the wet becomes desirable despite the wide array of dangers associated with this practice.
Discussion
Welding classifications, processes, and terminologies
Underwater welding is classified into two categories that include wet welding and dry welding. Underwater welding is manually conducted just as it happens in the open ground welding, with the only difference being the use of special electrodes for wet welding. The flexibility and scope of wet welding make this approach the most preferable as opposed to dry welding (Jeffus & Bower, 2010). This assertion is because it allows free movement, it is efficient and cost-friendly.
Welding power is sourced from structures installed on the open ground and connected to the welder through cables into the deep water. The principles of operation require expertise in this field since a number of risks are linked to the execution plan following unpredicted failure. The material to be welded is joined to one end of an electric circuit, and a special electrode to the other end. The resulting electric current develops a consistent spark referred to as the arc.
This model of welding has been highly adopted for many years due to its benefits, which include flexibility, time efficiency, and affordability. When structures are already immersed in water, it becomes hard and expensive to move them to the open surface for repairs. Even moving them to welding chambers inside water is impractical. Therefore, only wet welding can be used in repairs and maintenance for underwater mechanical structures. In addition, the speed of operation is important since the majority of the laid pipelines or drilling structures prompt emergency repairs to prevent oil spills into water bodies. Wet welding is the most suitable when handling these emergencies. Additionally, offshore structures can only be reached directly through wet welding, and the equipment needed to facilitate repairs and maintenance is minimal as opposed to dry welding.
According to Rodriguez-Sanchez, Perez-Guerrero, Liu, Rodriguez-Castellanos, and Albiter- Hernandez (2014), fatigue repairs and cracks on offshore structures can only be done appropriately using wet welding procedures such as FCAW, ROV, friction welding, and gas tungsten arc. Although wet welding is highly desirable for underwater welding, it faces several disadvantages; for instance, the process entails fast quenching of the welding material by the wet environment. This action reduces the stability of connectedness and raises porosity. Hydrogen accumulation increases the formation of fatigue cracks on structures. The unintentional introduction of hydrogen in the Heat Affected Zone (HAZ) and the weld material cause lines of weakness, hence reducing the ductility (Verma & Garg, 2012). In addition, due to poor visibility issues, the welder might not be capable of welding effectively.
On the other hand, dry underwater welding is done in various ways that involve welding in a chamber. In a dry chamber habitat, water is displaced to create a water-free environment, which is referred to as a splash zone where operations take place. Dry spot welding is another method whereby a transparent chamber filled with gas is used, but the welder remains in water with only the arms in the enclosure to facilitate the welding process. The principles of operation entail the size of the chamber as well as the geometry of the area under operation. Although it is not one of the most desired approaches, dry underwater welding has several advantages, which include its own environmental control systems (ECS).
This aspect improves the welders’ safety since the chamber is free from marine animals, and it is clearly illuminated. Since hydrogen concentration is low, the quality of the welds is relatively high as the quenching of the weld occurs at a low rate. The demerits of dry underwater welding include high costs since with greater depths, the arc shrinks and higher voltage is needed. In addition, one chamber cannot be used to do different weld tasks. Complex and large structures are needed to make the chambers and support structures on the surface.
The American Welding Society (AWS) code for underwater welding
The AWS was established in 1919 as a nonprofit entity seeking to pursue the science and technology behind underwater welding processes with the aim of advancing it globally (Jeffus & Bower, 2010).
With the evolving technology, researchers are often generating a passion for the arc, thus prompting the need to create uniformity for application via the use of standards. The AWS code is a document used concurringly as a guideline, and it is regularly updated under the watch of a committee of professionals working within the major areas of underwater welding to ensure that the standards are comprehensive. The AWS ensures that the demand for highly sophisticated equipment and mechanisms is met, and the set standards for operation are met for all marine infrastructure development and maintenance. The standards focus on human safety and healthy, material quality, industrial applications, among others, through updating standards of operation, advanced training, and certification towards attaining the leading-edge underwater welding knowledge. As transcribed in the AWS code of practice, a welder-diver must be a certified welder with the capability to weld with regard to the AWS D3.6M (Rodriguez-Sanchez et al., 2014).
The standards require a welder-diver to be fully qualified based on a predetermined procedure. All connections should be strictly insulated to avoid direct water contact. All the materials used must conform to the AWS standards. Up to date, the AWS continues to offer support for welding education and technology advancement to promote firm, competitive, and fascinating experiences in the welding field.
The Remotely Operated Vehicle (ROV)
The ROV is a widely used underwater welding device, particularly in deep-water activities like offshore oil extraction. The ROVs do not have humans aboard, but a skilled crew monitoring from a ship operates them. The crew is linked to the ROV by immersed tether system, which may include a load to reduce the effects of underwater currents when working in adverse environments. The electrical motor “operates a hydraulic pump, which propels and powers welding equipment like the torque device and artificial arms to facilitate welding where electrical motors would be impractical to use offshore” (Ximin et al., 2014, p. 685). ROVs assume different designs for specified tasks, and they are fitted with cameras to monitor operations from the vessels or the surface.
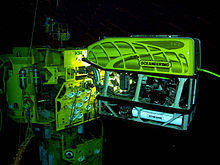
Underwater friction welding technology
Friction welding entails rotating one workpiece against another to create friction heat at the revolving point (Verma & Garg, 2012). This type of welding occurs in a solid-state, which generates coalescence of parts due to the heat sourced from mechanically instigated rotating movements. The pressure is used to ensure that the work parts do not lose contact. There are two types of friction welding techniques. In the first process, one part is clamped to avoid any movement, and the other part is made to rotate at a constant rotational pace by the use of a motor. When the desired temperature is attained, the rotational force is reduced to cease motion, and more pressure is exerted to ensure a stable weld when the rotating part stops. The benefit of this method is that it produces a strong weld in a short time, provided the process is monitored accurately to ensure precise regulation of pressure, speed, and duration (Majumdar, 2006).
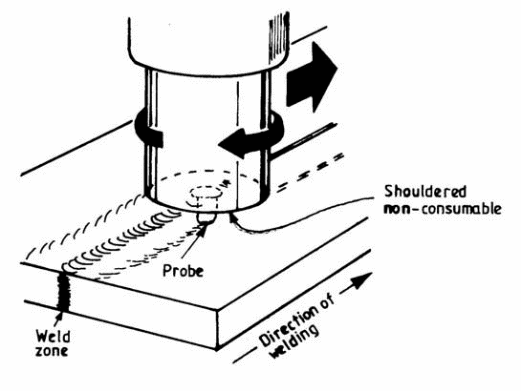
The other variation is referred to as inertia welding, whereby a flywheel is rotated using a motor to attain the desired speed. It circumvolves one of the pieces to be joined against the weld zone, after which the flywheel is brought to halt when the desired speed is attained, and more pressure is incorporated to strengthen the weld. Both procedures use friction heat to provide high-quality weld, and no filler metal is needed. Since there is no molten weld pool, the dangers of hydrogen weakening are alleviated. The friction welding process has the ability to join most of the common metals and develop combinations of different metals, such as aluminum to ceramics (Majumdar, 2006). Therefore, it is cost-effective since it takes a short time, and fewer inputs are used given that filler materials are not necessary.
In a bid to examine the effectiveness of the friction welding procedure in underwater welding, Farrokhi, Heidarzadeh, and Saeid (2013) compared the mechanical properties of joints welded at air and underwater environments. The authors identify that the underwater friction welding regulates the heat input in the course of welding, thus resulting in a regular and quality structure as opposed to friction welding in the air environment. Structures joined in underwater environments form the hardest joints as opposed to those joined in air conditions. In addition, the tensile strength and stability of joints increase in underwater welding, but a decline in air environment (Gao, Jiao, Xu, & Zhou, 2014).
Bead geometry in underwater FCAW welding
Flux-Cored Arc Welding is a widely utilized high deposition rate welding process. FCAW produces a smooth and uniform weld appearance. It is flexible while operating; simplified operator skills are some of the benefits of FCAW.
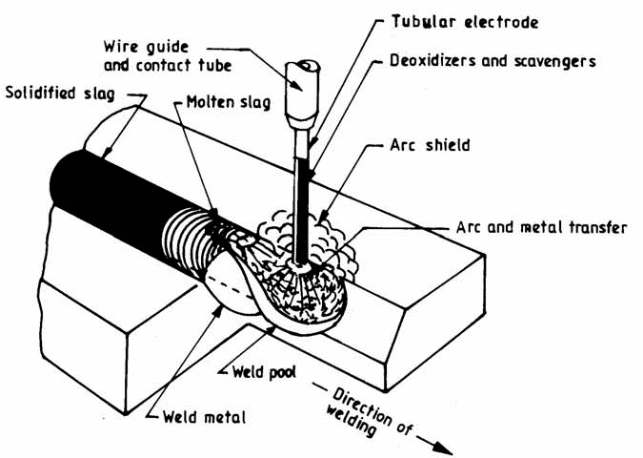
Several parameters must be considered when planning to execute an underwater welding task regardless of the method used. The main parameters are “water depth, arc current, arc voltage, and travel speed” (Hi et al., 2013, p. 1980). According to Hi et al. (2013), the bead geometry entails the bead height, width, and depth, which are essential physical characteristics of a weld joint. Water depth and travel speed are the most influential welding parameters that affect the bead geometry. The effective maximization of the welding parameter in underwater wet welding possesses the capability to weld with maximum heat input and optimal arc length, which increases arc strength. The application of optimized procedure parameters improve the attainment of quality weld-bead geometry, hence the formation of strong underwater structures.
Challenges and mitigation measures for underwater welding
Several dangers are linked to the welder, such as electric shock. Welding done “while exposed to direct contact with the wet environment is highly vulnerable to electric-related fatalities” (Jeffus & Bower, 2010, p. 111). Mitigation measures include ensuring sufficient or rather complete electrical insulation of the welding tools and disconnecting the power supply when the arc is extinguished. Secondly, meeting the AWS standards for structures welded by underwater welding may prove very difficult because doing inspections after welding is problematic, and integrity is highly compromised. As a result, the probability of failing to detect defects is high. This aspect does affect not only human life but also aquatic life, particularly for cases such as oil leaks. Precautions entail often conducting an evaluation for welders to ensure they have up to date skills regarding underwater welding (Jeffus & Bower, 2010).
Due to the persisting challenges facing underwater welding practices, substantial research has done an upgrade process performance. The automation of underwater welding and inspection has been actualized, and efforts are being made to eliminate emerging drawbacks (Majumdar, 2006). Apparently, the use of robots in the field has emerged as an alternative technique for application, improving quality, and output in this industry. Robotic welding involves welding that is done by robotic equipment. Mechanical advancements are being made to ensure the efficiency of the robot application to realize the expected returns. The key benefit of the robotic welders is that they eliminate human risks and increase the speed of welding, which translates into reduced costs. In addition, recent improvements have introduced nickel-based flux cored filler that offers advanced wet welds and halogen-free flux due to the use of the stainless steel flux cored cables.
Conclusion
As shown, the technology in underwater welding has undergone significant growth, and relentless efforts are being directed to research on this field. In particular, wet welding has been a common practice. Its significance has escalated with the current acceleration in the making of underwater structures. Despite this progress, more research is needed to provide alternative and more effective wet welding procedures. Wet welding technology is an acceptable method that covers a wider scope of application due to its flexibility as opposed to underwater welding in dry chambers. Even though most cases highlighted in this paper have existed for a while, they are yet to make a tremendous promise in the offshore welding activities. This aspect brings forth the need to develop high-potential technologies to meet the demand and standards in the international realm. This progress has always been in line with the AWS regulations to ensure improved quality and output.
References
Farrokhi, H., Heidarzadeh, A., & Saeid, T. (2013). Frictions stir welding of copper under different welding parameters and media. Science and Technology of Welding and Joining, 18(8), 697-702. Web.
Gao, G., JIao, X., Xu, Y., & Zhou, C. (2014). Study of Underwater Friction Welding Technology. Welding Journal, 93(9), 54-58. Web.
Hi, Y., Zheng, Z., & Huang, J. (2013). Sensitivity model for prediction of bead geometry in underwater wet flux cored arc welding. Transactions of Nonferrous Metals Society of China, 23, 1977-84. Web.
Jeffus, F., & Bower, L. (2010). Welding: skills, processes and practices for entry- level welders. Clifton Park, NY: Cengage Learning. Web.
Majumdar, D. (2006). Underwater welding-present status and future scope. Journal of Naval Architecture and Marine Engineering, 3(6) 39-48. Web.
Rodriguez-Sanchez, J., Perez-Guerrero, F., Liu, S., Rodriguez-Castellanos, A., & Albiter- Hernandez, A. (2014). Underwater repair of fatigue cracks by gas tungsten arc welding process. Fatigue & Fracture of Engineering Materials & Structures, 37(6), 637-644. Web.
Verma, K., & Garg, H. K. (2012). Underwater welding-recent trends and future scope. International Journal on Emerging Technologies, 3(2), 115-120. Web.
Ximin, L., Yufei, L., Haibo, G., Liang, D., Jianguo, T., Kerui, X., & Zongquan, D. (2014). Design of underwater welding robot used in nuclear plant. Key Engineering Materials, 6(20), 484-489. Web.