Introduction
Quality is a very vital feature in any undertaking. Whether it is a process or product quality remains one of the most critical characteristic that must be carefully analyzed and controlled in order to add value to the process or product. Tools and techniques are available to ensure that quality management is professionally performed.
This writing is going to summarize a number of these tools with a focus on the Pareto tool.
Quality management tools
Several tools are available that include Pareto chart, control, run charts and flow charts, Ishikawa diagrams (fishbone), scatter plots and check sheets and lists.
Pareto charts
Typically bar charts arranged in descending pattern from the highest bar on the left to the lowest on the right. During the Pareto analysis there are a number of steps followed that include:
- Gathering the raw data.
- Defining the raw data by sorting and ordering.
- Assigning suitable labels to the axes of the chart.
- Deriving the bar chart for every category.
- Calculate the cumulative totals for every category.
- Optionally drawing a cumulative line as an addition to the plotted bar chart.
Scatter plots
This is typically a line graph with no line. This diagram has the Y axis assigned to represent the variable whose behaviour can be predicted.
Control charts
This tool is used as a means of statistical process control. These charts are used to identify if the variables under consideration have consistent measurable characteristics.
Flow charts
This tool shows direction flow. This can be used to model processes, opportunities and decision points within a process. This is an important tool to help us understand process flows.
Run charts
This is a tool used to evaluate processes based on time or order. This tool involves gathering, organizing, charting and interpreting data.
Cause and effect/ Fishbone / Ishikawa diagram
Also called the fishbone or Ishikawa diagram and is used as the initial step in problem solving process.
Check sheets/ List
The check sheet is an interpretive and adaptable data recording form suitable for both qualitative and quantitative data collection. The check list defines all the operational conditions and steps to be taken during a certain process.
The Pareto analysis overview
The basis of this study focuses on the Pareto principle. This is also referred to as the 80-20 rule by Joseph Juran which suggests that 80% effects are a result of 20% causes. The genesis of this suggestion was based on Italian economist Pareto back in 1906.
Pareto tool and the Cause and effect tool / Fish bone tool
The Pareto tool can be used to disintegrate a big problem into smaller pieces. This is aimed at identifying the most significant portions and assigning the necessary attention to these portions.
The fishbone or Ishikawa diagram is a tool that can be used initially prior to using the Pareto tool. The cause and effect tool will identify the main causes that can be identified for the problem. These causes can then be fed into the Pareto tool to identify which ones need the most attention to solve the problem. Below is a general illustration of the fishbone diagram.
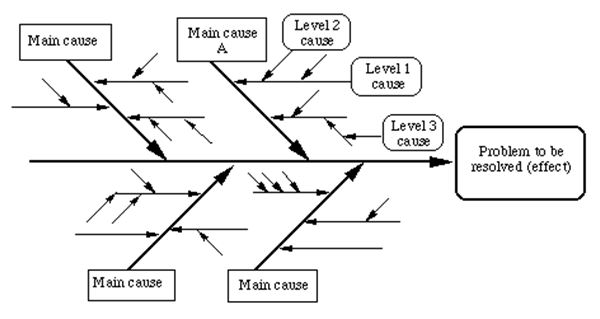
Additionally, because the other tools under study here show process flows and sequences or cause and effect, they can also be used to point out the errors in these processes. For instance using the flow chart can help us to identify error resulting from defective flow, which means the output prior to the defective point may be accurate.
However, output coming after the defective point may have some errors. As such the outcomes after the defective point can be submitted to the Pareto tool for analysis to determine the extend and occurrence of each type of error. This may be necessary in order to address the defective processes involved. Generally the Pareto tool is used with other tools to ensure quality management during certain processes.
Pareto tool uses and benefits
The Pareto tool can be used to identify those components that are responsible for a large proportion of the problems. Since the Pareto chart breaks the problem at hand into smaller portions, effort can then be redirected and focused where it is most needed. This is likely to maximize the achievements. In this way the Pareto tool can be used to prioritize applications or variables within the process being observed. Prioritization ensures that the limited resources are optimally utilized without any wastage.
Pareto charts can be used to address defects occurring during a production process. These defects most likely occur at varying frequencies. This tool can help a manufacturer to tackle the defects either by reducing the defect types that occur more frequently or eliminate those that cause monetary loss.
Toyota the giant Japanese automobile manufacturer does also use Pareto analysis tool to streamline their production with continued success (Poka Yoke, 2011).
Pareto exercise. Six Sigma Work Shop. Case Study – Disk Drive Pareto Analysis
The following tables are a report of the errors reported to the Six-sigma workshop quality engineer is responsible for a diskette drive that is used in the assembly of a personal computer. An analysis using Pareto analysis and a recommendation must be drawn.
Table 1: Error type weekly frequency.
The Table 2 below here shows the data from the different days of the week summarized into one table. The totals of the various error types occurring during the week can then be used in the subsequent calculation that will follow.
Table 2: Weekly count error frequency.
Based on the above data we can derive the following Table 3 below showing the error codes and totals against the respective cumulative percentages.
Table 3: Ordered error code and their cumulating percentages.
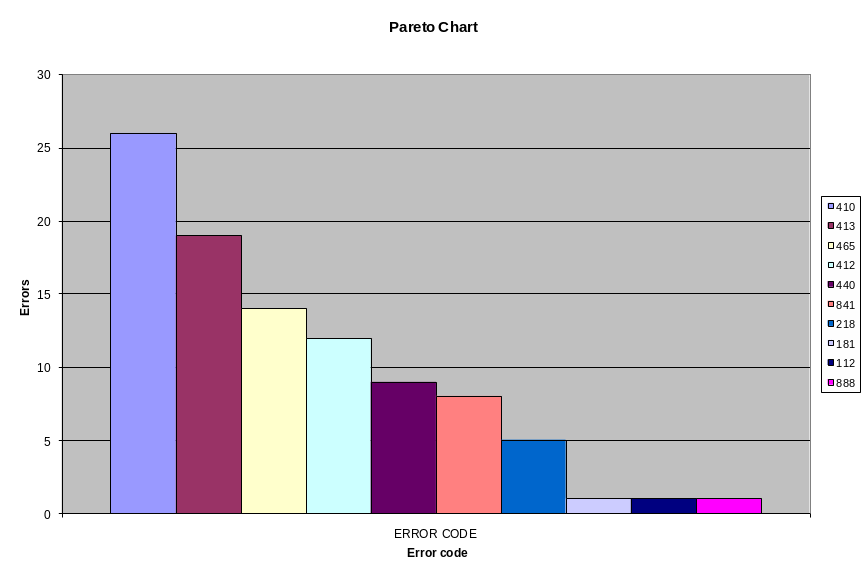
Recommendations
Errors coded as 410, 413, 465 and 412 needs to be addressed urgently in that order. Most priority should be given to error 410, 413 and 465. These errors account for a cumulative percentage of 64%.
The errors coded 181, 112 and 888 are negligible in their occurrence and effect. Accordingly the Pareto principle will hold for this exercise where the first three error types can be addressed to alleviate the other errors from occurring. It is recommended that the quality engineer at Six sigma workshop allocate enough resources and effort towards solving the cause of the error coded 410.
Additionally, the error occurrence rates appear to be higher towards the end of the week rather than at the beginning and if this may be attributed to human intervention or input then it shows reduced human concentration which probably requires introducing working shifts for the workers.
Reference
Poka Yoke. (2011). Poka Yoke or mistake proofing: An overview. Web.