Introduction
Nuclear fuel is the fissile material used in nuclear power plants to start and sustain nuclear reactions, and to generate power. Some common types of nuclear fuels are radioisotopes of uranium and plutonium, such as U235 and P239. Different types of fuels available are oxide fuels, metal fuels, ceramic fuels, liquid fuels, physical forms, less common types, spent nuclear fuels, radioisotope decay fuels, and fusion fuels. These fuels are characterized by different melting temperatures, densities, and the extent of nuclear flux they create. Nuclear fuel is made by filling zirconium tubes with a mixture of plutonium and natural uranium, or filling the tubes with enriched uranium pellets. Other fuels such as uranium dioxide is made of uranyl nitrate, mixed with ammonia and pressed into pellets. There are many other ways in which uranium fuel is prepared and the fuel composition depends on the type of nuclear reactors. Some categories of nuclear reactors are boiling water reactor, pressurized heavy water reactor, gas-cooled reactor, light water graphite reactor, fast neutron reactor, and others [1].
Irrespective of the type of nuclear reactors, these nuclear fuels have inherent dangers all along the nuclear life cycle made of phases such as ore extraction, refining, processing, casting, use in reactors, storage, transportation, and disposal of the spent fuel. The fuel is highly radioactive and any leaks of the coolant used in the reactors, can render the area for many kilometers from the leak unsafe. The process of nuclear fission can become unstable, leading to a breakdown of the core, causing rapid fallout of radioactive material. Transportation of the spent fuel is difficult since any spills from the container can contaminate the area. Disposal methods are very dangerous since the spent fuel is dumped in deep salt mines, where it continues to pollute the region. There is also an opportunity for rogue nations to divert the spent uranium to make nuclear bombs. Accidents or spills can lead to a radioactive contamination of the area, which has to be abandoned, and this happened in the accidents at Chernobyl, Russia, and in Fukushima, Japan. During the reactor operations, control rods and cooling water along with moderators, control the chain reaction. Any mistiming or wrong step can lead to a continuous chain reaction that would never stop, since the half life of uranium and plutonium is 4.468 x 109 years [2].
The alternate solution to the unstable standard nuclear fuel is Accident Tolerant Fuel (ATF). This fuel has many characteristics and composition that can overcome some of the dangers associated with nuclear reactor accidents [3]. This paper examines details of ATF, the current status, and presents quantitative criteria for ATF.
Current status
ATFs have gained importance after the Fukushima accident and it became clear that the accident was caused by a quick hydrogen explosion that released radionuclides in weak nuclear fuel cladding. Steam in nuclear reactors is under very high pressure and temperature, and this increases the rate of oxidation of UO2-zirconium alloys used in cladding material for uranium pellets. Weakening and rupture of the cladding cause swelling and ballooning of the cladding material, releasing hydrogen that explodes. Therefore, fuel claddings have to maintain their performance characteristics during accident conditions. This has led to the development of ATFs. In ATF systems, new materials are used that can tolerate the loss of coolant for a longer time while giving improved performance during normal operations. ATF has two components, fuel pellets and the fuel cladding. Fuel cladding should have higher thermal conductivity and allow retention of fission products. Increasing the thickness of fuel cladding is not possible, since it would accommodate lesser fuel pellets, and reduce the power generation capacity [3]. This section examines the current status of ATF development in different countries.
Research is underway at General Atomics, US, to study Silicon Carbide (SiC) as a suitable material for ATF. SiC has high temperature strength and it shows high stability under radiation and oxidation, when compared to zirconium alloys. SiC is used as a cutting tool to machine steel at very high cutting parameters. The researchers used SiC and SiC composites for monolithic cladding to provide a tough and hermitically sealed container for improved performance and safety. While initial results are promising, challenges are present in fabricating long and thin walled tubes that meet the functional specifications. The mechanical and thermal characteristics of unirridated SiC structures were examined along with dimensional control and permeability. The conclusions indicate that while the material was structurally sound, it was brittle, there were problems in maintaining the tubular geometry, and development is needed for design and research in several areas of SiC [4].
Researchers in Korea studied the feasibility of surface-coated Zr cladding with metal-ceramic hybrid cladding. The objective was to suppress the production of hydrogen during accidents. Another objective was the development of microcell UO2 pellets to increase retention of radioactive and corrosive substances such as Cesium and I. The concept was to cover the UO2 grains in thin cell walls that would trap the movement of fission products and act as barriers. The research focused on reducing hydrogen production by steam oxidation at high temperatures so that explosions could be prevented. Another focus area was to increase the properties of fission products to retain Cs and I. Two concepts were used in the design. The first was surface modification by using tubes of Zr alloys with external coating, and the second was to have Zr alloys tubes with ceramic composite coating and external metal-ceramic hybrid cladding. Samples were coated with Cr, Si and Al3Ti alloys, and were subjected to high temperature steam oxidation. The results showed that samples with Al3Ti alloys showed very low oxidation at elevated temperatures. Further developments are to manufacture a hybrid cladding with three parts, a Zr inner liner, a composite layer made of Zr, and a surface coating on the outside. This construction allows the matrix to be sealed tight even if the outer layer develops cracks. The outer ceramic layer has a higher safety margin since it can withstand very high temperatures. Challenges remain in developing the ceramic layer [5].
A research was conducted at the Idaho National Laboratory, US, to use uranium silicide pellets as ATF to replace uranium oxide pellets. Powder metallurgy was used to produce uranium silicide and these pellets had the density greater than the theoretical density of 94%. Uranium and silicon form different types of stoichiometric compounds such as USi1, USi2, U3Si2, and others. Among these, U3Si2 has higher uranium silicide content and it can be used to replace UO2. It does not swell under irradiation and is suitable for use as nuclear fuel. U3Si2 has 17 more atoms than UO2 and this gives superior uranium loading, and allows cladding materials such as SiC. The operating temperature is lower, the thermal conductivity is higher, and the lower temperature is useful in nuclear reactors.
The researchers fabricated the fuel in lab conditions in an inert glove box, since uranium is pyrophoric. Uranium silicide was made by combing uranium and silicon powders and a hydride/ dehydride process was used to produce the powder. The resulting powder was compacted and heated in a furnace at 1450 degree centigrade and then in an arc smelter, where tungsten electrode was used to pass an electric current to produce uranium silicide with 97% purity. The samples were turned into pellets and subjected to different tests such as Scanning Electron Microscope, chemical and micro hardness analysis, and ATF-1 irradiation. The last step helped to understand the irradiation performance and to obtain data on possible ATF use. The pellets were pressed into Zr alloy tubes and sent to INL Hot Fuels Examination Facility to run tests that replicate accident like conditions in a reactor. Further research is underway to understand the behavior and swelling characteristics of the pellets and their possible use in reactors as ATF would depend on the test outcomes [6].
While ATFs are a good concept, several factors need to be considered before standard fuels are replaced. These factors include backward compatibility, economics and costs, impact on the fuel cycle and the plant operations, and on the plant safety with design basis and beyond design basis. To develop ATF, researchers selected fully ceramic micro-encapsulated (FCM) fuel. This idea was initially used in high temperature gas cooled reactors, where the particles were dispersed in a graphite matrix. This concept was used to develop cladding for LWR fuel with a SiC matrix that enhances stability under irradiation, acts as a barrier for release of the fission products, and resists proliferation. Cladding materials used were stainless steel of 316 grade, FeCrAl, and SiC.
Tests were run for the fuel, UO2 and Zr alloy cladding. Simulations of accidents were performed with the MELCOR severe accident code, to evaluate the different cladding performance. Results showed that the standard UO2-Zr system faced quick oxidation when the reactor water level fell, releasing hydrogen and heat within 4 hours. The new cladding system of UO2-FeCrAl on the other hand, remained steady and released half the amount of hydrogen after 8.5 hours. Similar results were seen for FCM-FeCrAl combination, and the core remained almost intact after relocation. These effects are due to the high melting temperature of the new cladding. In the simulation, the UO2-Cr system shows rapid heating of upper structures and it relocates to the bottom, releasing more hydrogen and steam. For the new cladding, since cladding oxidation did not take place, the core remained intact. The researchers conclude that simulations indicate that the UO2-FeCrAl and FCM-FeCrAl systems can be considered for reactors. However, other factors such as cost, economics, compatibility, and reliability need to be examined [7].
The previous sections presented research on ATF and several materials and methods were tested. The physical preparation of samples and preparing tests appears to be a tedious task. If the research does not meet the objectives, then the whole set of experiments is wasted. UK is at the forefront of nuclear reactor research and it has set up the Integral Inherently Safe LWR design (I2S-LWR), 2850 MW integral PWR, for research and testing. Researchers in UK have developed a lab simulation where it is possible to create simulations using different lab code such as ANSWER reactor physics code, WIMS and EDF energy core simulator PANTHER. The objective of the research was to study the performance of uranium nitride and cladding material FeCrAl and silicon carbide. In the study, I2S-LWR was designed with U3Si2 and stainless steel. The reactor has an integrated feature that allows cooling to be removed and simulate accidents. In the experiment, the reactor was tested for the fuel and steel alloy cladding using a two stage approach. Macroscopic cross sections were simulated with WIMS and used for a 3D core design with PANTHER. The results from this simulation were compared with Monte Carlo code, and the results examined. The results indicate that there was a high co-relation between the reactor physics code and the WIMS code, showing that the simulations have a high reliability level. This study is important since researchers can use simulations of the planned research and then proceed if the results are satisfactory [8].
Quantitative criteria for accident tolerant fuel
Discussions from the previous section show that ATF needs to have certain properties that make them tougher in accident conditions. Desired functions are that they should withstand loss of active cooling for a much longer duration than existing fuels with the result that the existing safety margins will increase. This should help to enhance performance of the fuel for a longer time. ATFs should be adaptable to existing nuclear plants and allow for licensing for future reactors. They should also reduce maintenance and operational costs. This section presents important quantitative criteria for performance of ATFs in severe accident conditions. An important point is that a number of cladding systems and materials were discussed and these systems have their own properties and features, and it may not be possible to obtain common quantitative criteria for them [9]. However, efforts are taken to bring the best possible fit criteria.
Steam Oxidation temperatures: This parameter refers to the temperature at which steam oxidation of the cladding begins. Fig 3.1 presents data on this temperature for different cladding systems.

As seen in the Fig 3.1, the standard or conventional Zr alloy starts oxidation at a temperature of 1273-1773 degree centigrade. In section 3 [3, 4] SiC has emerged as an important source for cladding system. SiC system has a cladding oxidation temperature of 1473-1873 degree centigrade. Hence, the first assessment is that the oxidation temperature range for ATF of SiC should be at a middle value of 1763 degree centigrade. However, one should also consider APMT system with Ti2AlC system [5, 7]. It is seen that this system has an oxidation temperature resistance of 1323-1748 degree centigrade. The mean temperature of this system can be considered as 1535 degree centigrade.
Oxidation time and film formation: These parameters indicate the exposure duration when oxidation starts, and the amount of oxidation is measured by the film formation on the substrate. Materials with lower oxidation temperatures show weight gain due to oxidation film formation. The objective is to prolong this duration to the maximum value and delay film formation with weight gain. Fig 3.2 shows the results of samples tested for weight gain when placed in a steam environment at 1200 degree centigrade [11].
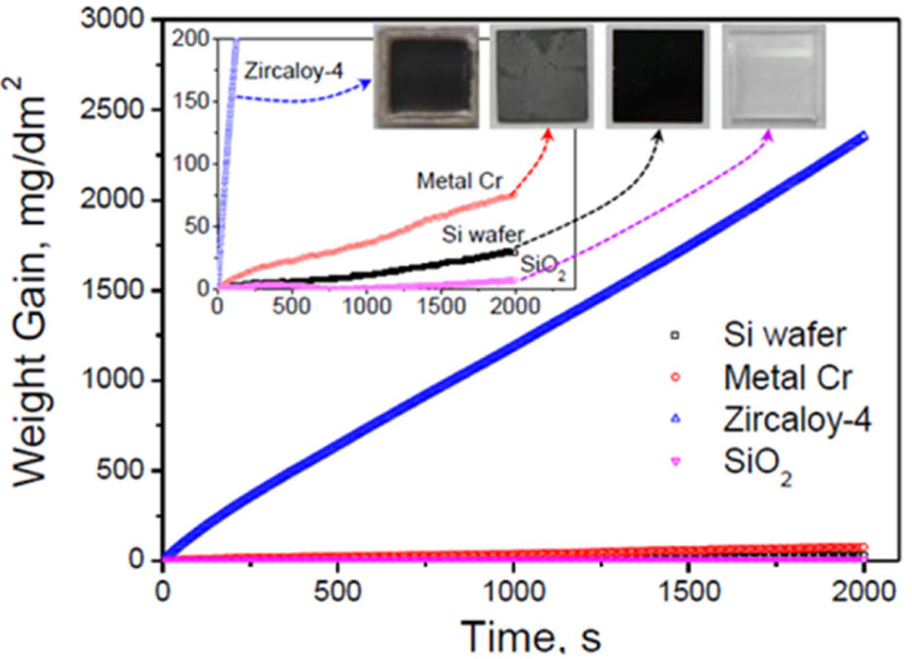
Samples that were tested are Si, Cr, Zr4 alloy, and SiO2. From the graph, it is seen that Zr4 alloy starts to gain weight steadily from 0 seconds, and this linear weight gain continues for the full duration of the test that ran for 2000 seconds. Therefore, it is clear that Zr4 alloy is perhaps not suitable for temperatures above 1200 degree centigrade. The other alloys showed very little weight gain indicating that oxidation does not occur and film does not precipitate for the full duration of 2000 seconds. As seen in Fig 3.2, Si, Cr, and SiO2 showed marginal weight gain. Hence, the quantitative data for ATF is that samples should have less than 5 mg/ dm2 weight gain when exposed to a steam environment for 2000 seconds.
Young’s Modulus: The Young’s Modulus is important in understanding the elastic properties of materials. It gives the ratio of stress to strain and the value defines the behavior under different load conditions. Materials with higher values are less tensile, and they can resist deformation better. Young’s modulus varies with the temperature and at higher temperatures, the material is more tensile and the value reduces. This aspect is important in ATF since they operate at elevated temperatures. In a test, FeCrAl alloys were prepared and tested. These alloys had compositions in weight % of Fe ranging from 83.98 to 77.86, Cr from 12.99 to 16.06, and different compositions for Al, Mo. Si, Nb, etc [12]. Fig 3.3 presents the graph of elastic modulus to temperature for these metals.
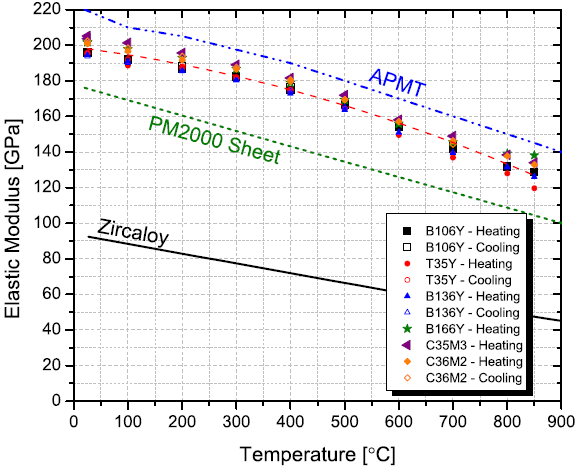
From Fig 3.3, it is clear that Zr alloy shows a sharply decreasing Young’s modulus at 900 degrees centigrade, where the value is 45 Giga Pascals. APMT alloy samples show the highest value of 140 GPa, while PM2000 sheet shows a value of 100 GPa.
Summary: The recommended specifications for ATF, based on [10, 11, 12] are as follows.
Operating temperature range: 1535 degree centigrade
Weight gain from oxidation and film formation: 5 mg/ dm2 when exposed to a steam environment for 2000 seconds.
Young’ Modulus: 140 GPa at 900 degree centigrade.
Summary
The paper examined the significance and need for ATF and discussed the current status of research. The findings indicate that cladding materials made from SiC, coatings of Cr, Si and Al3Ti alloys, composite matrix of Zr and ceramic layers, micro-pellets of UO2-FeCrAl and FCM-FeCrAl systems, are under trials. Clear specifications of materials and specifications are not yet available. The paper also presented quantitative criteria for important parameters such as minimum steam oxidation temperature and weight gain from oxidation, and the Young’s Modulus. These specifications need rigorous testing before they are approved and their impact on costs, compatibility, reliability, and other factors must be considers. The opinion and feelings formed from the research is that the subject of ATF is very critical and extensive research with live trails needs to be undertaken. Suggestions are to increase funding and provide researchers with adequate facilities to take up urgent research and development. Nuclear accidents in the past few years show that the cleanup costs and damages are very high. These costs and human suffering can be avoided with ATF.
References
Per Peterson, “Spent nuclear fuel is not the problem,” Proceedings of the IEEE, 106 (2017) 411-414.
Xing Yan, Hino Ryutaro, Nuclear hydrogen production handbook, CRC Press, 2016.
Zeses Karoutas, Jeffery Brown, Andrew Atwood, Lars Hallstadius, Edward Lahoda, Sumit Ray, Jeffrey Bradfute, “The maturing of nuclear fuel: past to accident tolerant fuel,” Progress in Nuclear Energy 102 (2018) 68-78.
Deck Christian, Shapovalov Jacobsen, Jonathan Sheeder, Oscar Gutierrez, Joe Zhang, Jim Stone, Hussain Khalifa, Christina Back, “Characterization of SiC–SiC composites for accident tolerant fuel cladding,” Journal of Nuclear Materials 466 (2015) 667-681.
Yang-Hyun Koo, Jae-Ho Yang, Jeong-Ying Park, Keon-Sik Kim, “KAERIS development of LWR accident-tolerant fuel,” Nuclear Technology 186 (2014) 295-304.
Jason Harp, Paul Lessing, Rita Hoggan, “Uranium silicide pellet fabrication by powder metallurgy for accident tolerant fuel evaluation and irradiation,” Journal of Nuclear Materials 15 (2015) 1-18.
Larry Ott, Kevin Robb, Dean Wang, “Preliminary assessment of accident-tolerant fuels on LWR performance during normal operation and under DB and BDB accident conditions.” Journal of Nuclear Materials 448 (2014) 520-533.
Benjamin Lindley, Dan Kotlyar, Geoffrey Parks, John Lillington, Bojan Petrovic, “Reactor physics modeling of accident tolerant fuel for LWRs using ANSWERS codes,” EPJ Nuclear Science Technology 2 (2016) 1-9.
Jon Carmack, Frank Goldner, Shannon Bragg-Sitton, Lance Snead, “Overview of the US DOE accident tolerant fuel development program,” Idaho National Laboratory INL/CON-13-29288 (2013) 1-10.
Bruce Pint, “Material selection for accident tolerant fuel cladding.” Metallurgical and Materials Transactions, E2.3 (2015)190-196.
Hyun-Gil Kim, Jae-Ho Yang, Weon-Ju Kim, Yang-Hyun Koo, “Development status of accident-tolerant fuel for light water reactors in Korea,’ Nuclear Engineering and Technology 48 (2016) 1-15.
Zachary Thompson, Kurt Terrani, “Elastic modulus measurement of ORNL ATF FeCrAl alloys,” Oak Ridge National Laboratory. Web.