Cars used in Formula One racing have undergone several modifications since the inception of the racing sports. Nevertheless, they have maintained fundamental elements of physics in designs. Physics plays a critical role in the design of Formula One racing cars. Contemporary Formula One cars have greatly borrowed design elements of aerodynamics. Engineers have ensured that the car is as fast and safe as possible with adequate down force and limited drag.
The engine designs achieve optimization qualities with fuel that can release as much power as possible without affecting the engine functions. The tires are design to withstand prevailing weather conditions. These incorporated elements of physics are what make Formula One cars different from others.
Introduction
Formula One cars have resulted from tremendous efforts of engineers working steadily to understand design concepts that could provide speed and safety simultaneously. Over the last decades, Formula One cars have undergone minor redesign and changes with impressive outcomes, but they have always maintained the basic design of open wheel and a single seat. As technology changes, engineers have seen it necessary to enhance capabilities of cars and drivers.
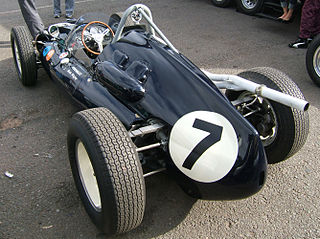
The dynamic structure of the car
Formula One car engineers apply extremely complex aerodynamic approaches in designs. They aim to achieve high efficiency with similar performance of airplanes. The car has rear and front wings, which can easily generate adequate force to propel it off the track. However, these wings are fixed upside down to ensure stability of the car, keep it on the ground, enhance efficiency when negotiating corners and avoid toppling. Hence, the fast laps propel the car, but cannot lift it (Axerio-Cilies and Iaccarino par. 3).
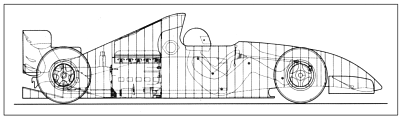
In down force, engineers have applied similar principles used in airplane wings for Formula One cars. In the case of cars, the design achieves down force rather than lift, and Bernoulli’s Principle has been useful. The Principle applies physics to achieve the role of car wings. Air moves at different speeds on both wings and at different distance because of the shape of the wing, which creates pressure difference. The resultant pressure balances the wing and makes it move in the direction of lower pressure (Cook par. 3).
Both wings fixed on Formula One cars have abilities to generate almost 70 percent of the total down force needed. This role makes the wings necessary parts of Formula One cars. Today, designers have ensured that wings are skillfully designed in a complex manner to maximize efficiency.
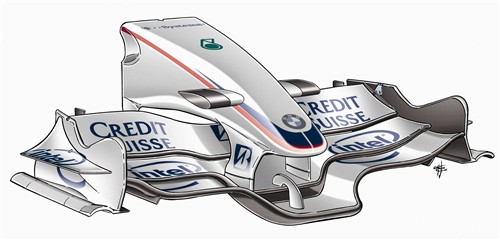
Engineers must determine how to reduce drag in their designs. Drag is a force that opposes the movement of the car. In this case, they must consider all elements of the car and the driver in order to limit drag. Specifically, they consider “the driver’s helmet, linkages for suspension components, external fixtures and hardware, which are all designed to reduce drag on the car” (Cook par. 5).
Engine design
Today, there are stringent regulations to ensure that all Formula One cars have similar engine specifications (Groote, “Formula One engines” par. 3). Car engine is the only source of power for the car in addition to the Kinetic Energy Recovery System (KERS) introduced in 2009. KERS is a component of the chassis that harnesses waste energy generated during braking and changes it to electrical energy for extra power.
The Energy Recovery System (ERS) was unveiled in 2014 Formula One season as an upgrade of the KERS technology (Cook par. 2-3).
There are critical engine optimization requirements that make the design technical. First, engineers must achieve higher volumetric efficiency. They can achieve such optimization because of significantly higher intake manifolds. The turbo chargers used in Formula One cars can exceed the 100% volumetric efficiency found in normal cars. Second, Formula One cars have optimized thermal efficiency. The design of the “chamber, ignition timing, thermal coatings, plug location and chamber design all affect the thermal efficiency” (Groote, “Formula One engines” par. 10). Third, engineers have enhanced mechanical efficiency in Formula One cars. Designers account for rocker and bearing frictions, piston skirt area and other movable components of the car. They restrict internal engine friction to enhance power production.
The exhaust in Formula One cars is also designed to ensure maximum efficiency. For instance, its length matches horsepower requirements. Moreover, it can withstand extreme temperatures of over 1200°C.
Most Formula One car engines have three various methods of engine designs with regard to the position of the cylinder. Inline engines are no longer used in Formula One cars because they are longer and need heavy crankshaft. Boxer engines have cylinders that are placed opposite each other. They are the best approaches for building car engines. Finally, V-type engines are the most common in today’s Formula One cars. The regulatory authority allows engines to be placed at 90° in V8 models. V-types engines are difficult to build and require careful consideration because of possible combustion issues. Therefore, its basic balance at the right angle is mandatory.
Crankshaft design depends on the type of the engine on a Formula One car. A complex engine design like the V8 requires equally different crankshaft design.
Formula One cars could have low thermal efficiency and therefore require an effective method of cooling internal combustion engines. While Formula One cars have similar cooling systems like ordinary cars, the spacing and aerodynamic requirements for racing cars have totally different positions (Groote, “Formula One engines” par. 10).
A transmission system for cars is the transitional point from gears, car systems, rotating engine power to wheels. It, however, focuses on the gearbox and differential within the gearbox system. The transmission system is made of carbon fiber and mounted firmly on the rear part of the car engine.
Fuel
Formula One cars use “gasoline as a fuel for their engines” (Groote, “Fuel” par. 1). The fuel is mixed with air within the cylinder to produce combustion, which creates potent force. The design of the combustion system enhances fuel distribution within the chamber to produce explosive for maximum power. At the same time, the design of the combustion chamber ensures fuel efficiency. The design must ensure maximum power production without interfering with the system durability and fuel economy.
Formula One cars have “deformable fuel tanks manufacture from puncture-proof Kevlar to dramatically limit the risk of any fire during an accident” (Groote, “Fuel” par. 12).
Tires
There are three different types of Formula One car tires. There is a tire for dry surfaces (F1- Country par. 1). It consists of “660 mm in external diameter and 350 mm wide with four longitudinal grooves of at least 2.5 mm reinforced with the Depth Regulations” (F1- Country par. 1). Tires have symmetrical grooves that run at the center with a gap of 50 mm. The dry tire for Formula One cars is a new concept. The dry tire concept has achieved limited ground contact and ensured firm grip from the rubber grooves and the track. The focus on tires aims to ensure safety of Formula One cars, especially when negotiating corners (F1- Country par. 1).
There are conditions such as moderate rain that do not necessarily require the use of wet tires and therefore intermediate tires are needed. Such tires are used in a wide range of conditions and tracks. For instance, they must remove water film on a drying track and remain stable on a dry track without wearing fast. For this reason, intermediate tires have sculptures (F1- Country par. 2).
There are also wet tires for Formula One cars. Wet tires are designed for rainy tracks and wet surfaces. They have greater constraints on compound. Wet tires are designed to “evacuate the film of water which infiltrates between the tire contact area and the track” (F1- Country par. 3). Too much water film may cause the tire to “lose grip, which could result in aquaplaning” (F1- Country par. 3). All different types of tires can be used in the race. While one tire is intermediate, the rest are suitable for soaked tracks. However, the race director must declare the track wet for such tires to be used in the race.
Additionally, most Formula One tires are filled with nitrogen-rich gas without moisture to maintain constant pressure irrespective of the prevailing temperature. Nitrogen is also used because it can hold tire pressure for relatively longer time than air (F1- Country par. 3).
Conclusion
Physics continues to play critical roles in the design of Formula One cars. Concepts of physics are incorporated in the dynamic structure of the car, engine design, tires and fuel to enhance efficiency and safety at optimized performance.
Works Cited
Axerio-Cilies, John and Gianluca Iaccarino. Grip or Aerodynamics: The Fluid Mechanics of Formula 1 Wheels. n.d. Web.
Cook, Brian. The Physics of Formula One. 2014. Web.
Groote, Steven De. Formula One engines. 2009. Web.
—. Fuel. 2006. Web.