The city of London has many skyscrapers that stand tall in all streets. They depict London’s rich history of development and evolution of the building culture. However, a discussion of the history of the city of London is incomplete without considering Saint Paul’s Cathedral. The cathedral forms one of the glamorous and famous icons of London.
Its dome that has some framed spires has been a unique skyline feature in the architectural work for over 300 years. Standing at 111.3m, the cathedral was the tallest structure between 1710 and 1962. However, until today, its dome is one of the highest across the world. From the context of area coverage, it takes the second position for all churches in the UK after the Liverpool Cathedral (Campbell 34).
The cathedral constitutes a centerpiece for the English people’s identity. Campbell supports this assertion by adding that many promotional materials deploy it as their main subject, especially its long-standing dome that is surrounded by Blitz fire and smoke (71). The church building has housed important ceremonies, including Sir Churchill and Lord Nelson’s burial services, Peace services to mark the end of 1st and 2nd World Wars, and wedding services for prominent person such as Sir Charles, the Prince of Wales.
The church has also been used as the venue for marking important times in the English history such as Diamond Jubilee, Golden Jubilee, and 80th Birthday (Campbell 83). The structure is an all-time busy building that holds services and prayer sessions on a daily basis. Hence, it is clear that even with modern design solutions, the work of Wren remains an important reflection of the glamour of London and the United Kingdom.
Location of the Building
Saint Paul’s Cathedral functions as the heart of the Anglican Diocese of London. It is located at Ludgate Hill, which is the highest site in London city. Sir Christopher Wren had the honor of designing it in the 17th century. The building process was completed when Wren was still energetic. It was part of a rebuilding program that followed the occurrence of the ‘Greatest Fire of London’ (Tatton-Brown and Crook 103), which destroyed the predecessor building.
The current Saint Paul’s Cathedral in London was built between 1675 and 1710. The church was “the first cathedral to be built after the English Reformation in the sixteenth-century, when Henry VIII removed the Church of England from the jurisdiction of the Pope when the Crown took control of the life of the church” (Tatton-Brown and Crook 19). Wren had begun offering advice on the renovation of the old Saint Paul’s Cathedral in1661.
However, the fire of the Great Britain destroyed it in 1666, thus prompting the need for developing a new design after its demolition in 1670. William Sancroft laid down the anticipated architectural design outcome in 1668. He wrote to Wren informing him that in consensus between London’s bishops and Canterbury Archbishop, he was charged with the responsibility of designing and overseeing construction of a handsome church, which also retained the reputation and glamour of the nation and city of London (Campbell 36).
Designing Saint Paul’s Cathedral took several years. The agreed upon design was attached to the royal warrant. However, provisions were made to permit Wren to make necessary alterations, which he deemed appropriate. The repercussion of the changes was the current cathedral that has one of the most appealing domes across the world. Coal tax was deployed as the main source of finance to build the cathedral. Although the construction process ended on 26 October in 1709, the upper house declared the conclusion of the church on December 1711. However, the construction went on for a number of years. Indeed, statues that are seen on the roof were placed in 1720s. By 1716, the building had used about 1,095,556 sterling pounds, an equivalent of 143 million sterling pounds in 2014.
Culture and Society
The design of city buildings and structures reflects knowledge base and values of the society. This observation suggests that buildings have cultural purposes since they reflect the cultural progression of a society. Hence, the design and construction of Saint Paul’s Cathedral was to be accomplished in a manner that reflected the status of the city of London. This plan implied that the cathedral needed to reflect and/or symbolize the status of the society in which it was erected.
The impacts of the architectural creation of Wren were reflective of the material culture and building technology during its time of construction, but with added innovation and creativity in terms of assembly of materials and appearance of the fully developed architectural work. The fact that Wren was dedicated to design a structure that reflected the caliber of the nation and city suggests the existence of a cultural mentality and belief in excessive and competitive consumption.
Wren was involved in advising on renovation of the old cathedral before the great London fire destroyed it. This situation meant that during the design processes of a new cathedral, he was to ensure that he developed a unique structure in the extent that it could not look like any other cathedral that had been developed on the same site before. Such a motif reflected the culture of competition in developing new skyscrapers. Since the building would be used as an iconic center for many functions of the Anglican Church in London, the design and construction process needed to reflect the English culture of owning the best and the most attractive worship center. Indeed, a look at the cathedral picture in figure 1 evidences Wren’s success in delivering this cultural anticipation.
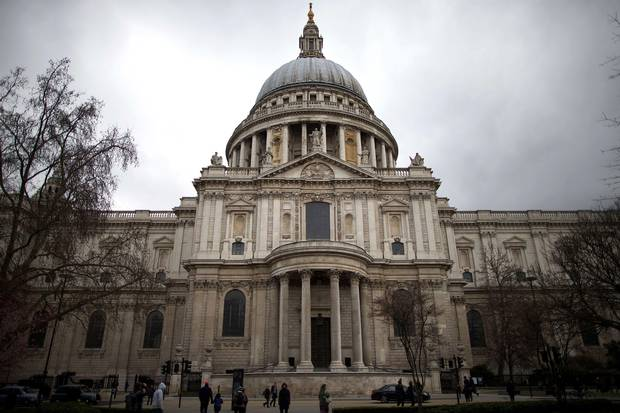
Many design aspects of Saint Paul’s Cathedral reflect the building culture for worship centers across the globe at its time of construction. When Wren was given the authority to make changes on the design during the construction process, he took an immense advantage of it. One of the major changes was done on the dome. Wren raised an additional mega feature over the original cupola or the brick cone. This change was done in a bid to support a stone-made light, which formed an elegant feature.
He also covered a “brick-made cone with wood and lead cupola” (Campbell 59). These features were borrowed from the design of St Peter’s Basilica that is located in Rome, Italy. The culture of designs for worship centers is also reflected in the Saucer Domes that are located at Nave. The original idea in its design was borrowed from the Val-de-Grace church, which forms part of Francois’ work, which Saint Paul’s Cathedral designer saw when he visited Paris in 1665 (Sankey 78).
The design of Saint Paul’s Cathedral was highly influenced by the Baroque styles. This resemblance depicted the capacity of its designer to rationalize various building cultural traditions in the English world and other places such as the work of Polladio and Mansart (Tatton-Brown and Crook 89). Medieval influences are evident on the transepts of the church.
Construction of the Building
The main challenge in the construction process was building a large building on a weak ground (clay soil). The building also has one of the largest crypts across the world. Although it is huge enough, piers occupy most of its (crypt) space. They (piers) absorb the weight of smaller piers (Tatton-Brown and Crook 90). In the construction of other cathedrals across the world, four main piers support most of the weights. However, Wren’s building has incorporated eight piers. This plan has the effect of enhancing better weight distribution in the foundation. During the construction process, changes occurred on the building ground akin to its relative weakness, although Wren responded by making the appropriate structural alterations.
The critical challenge that Wren faced in the design process and subsequently in the construction process was making not only visually satisfying architectural work, but also replacing the lost cultural significance of the old St Paul’s Cathedral following the occurrence of the London fire in1666. Wren had to address the problem of visual impression since it constituted one of the most important anticipated building characteristics.
One of smart ways of accomplishing this mission was to divide and extend the external and interior heights for the church’s pitch above the level that had been reached by the designer of St Peter’s Cathedral through utilization of curves. To achieve this goal, he inserted a brick- made cone, which supported the outer domes, which were covered with lead. Stone lantern was made to rise at great heights above it as shown on figure 2.
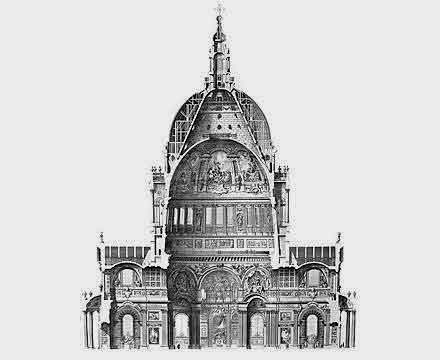
The inner dome and the cone have a thickness of 18 inches. They are supported using iron shackles. The design has some buttresses that are placed superficially at the ground floor. Before the commencement of the construction, Wren altered the elements, which did not comprise a classical aspect of the design. Instead, he constructed a thick wall to eliminate the buttresses. However, flying buttresses were deployed in the reinforcement of clerestory and the vault. This feature was only incorporated in much late stages of the design with the aim of providing extra strength.
Materials
Without materials, Wren’s design would not have been physically actualized. The main building material for the cathedral was Portland stone. Indeed, the church was one of the very first buildings to deploy this kind of stone. Large quantities of it were required in the construction, which made King Charles II issue special orders that no Portland stone would be mined for any other purpose without Wren’s consent (Tatton-Brown and Crook 161). Other major materials were lead, timber, marble, and wrought iron. Stone and timber formed the subject on which the engraving and sculpture works were done. Wrought iron was mainly deployed in fencing, although it was not Wren’s deliberate choice. He had preferred hammered iron since it could be made more decorative compared to wrought iron.
Exterior Design
The most outstanding feature from outer side of the cathedral is the dome. It rises about 111 meters, thus making it the dominant mark of the London’s sky space. Unlike the domes of the Val-de-Grace and the St Peter’s Cathedral in Rome, Wren’s dome rises in two-story masonry. Looking at the building from a distance, one clearly sees the columned porch. This design element anchors the interior pitch and the conduits. The conduit provides the necessary support for the long-standing illumination.
On top of the columned porch, Wren positioned a stone gallery, which is elegantly decorated. The dome, which is covered by lead, rises above the columned porch below the lantern. Eight luminous gadgets penetrate, although they are not clearly visible. West front transepts have a half-circle portico in the entrance. Windows are located between pilasters. The underside openings possess patterns that take after the Roman artistic work. Gibbon’s stone carvings appear beneath the windows. The pulpit rises 110 feet above the ground level.
Interior Design
From inside of the cathedral, one clearly sees the central part of the building that is meant to accommodate bands of singers. A domed narthex that takes the shape of a square forms the entrance of the cathedral from the west portico. St George, St Dustan, and St Michael chapels are flaked on its either side. The central part that is designed to house bands is raised 28m high. Passageways have been designed using special structures (cloisters berths). The cathedral has a section, which provides anchorage to the church’s organs and pulpit team among others. The interior view of the dome represents a particularity impressive artistic creation of the 17th century as shown in figure 3 below. Along the width of the choir is the apse that has mosaic decorations.
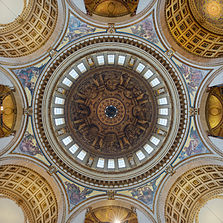
Labor Force
Throughout the design process, Wren worked with Nicholas Hawksmoor as a personal helper while Dickinson functioned as a measuring clerk. Marshall, Edward, and Strong were employed as chief masons. After the demise of Marshall in 1678, the two brothers worked to the finishing point of the cathedral. Langland operated as a chief carpenter all through the construction process. Grinling operated as a chief sculptor.
He took active roles in the North Portal construction in addition to supervising internal wooden fittings. However, Caius Gabriel sculptured the southern pediment transept (Tatton-Brown and Crook 113). Francis Bird was engaged in making the relief on west pediment and various other statues that appeared on the west front of the cathedral. In 1709, William Dickson took up the responsibility of laying concrete on the cathedral base with sandstone. This task was accomplished in 1710. However, there lacks evidence on the exact number of people who were employed to complete the project.
If it were Today
People’s artistic creativity develops as time progresses. This claim is perhaps true with reference to the construction of St Paul’s Cathedral. If the construction could be done today, tools that were used in the construction would also be different. The construction would probably involve a heavy use of equipment and different materials, rather than just stones, lead, iron, and timber. For example, instead of stones and wooden fittings that formed part of the structural components that provided strength in the building, pre-stressed concrete would most be appropriate to minimize time that would be required to complete the construction from over 30 years to about five or three years. Pre-stressing is one of the methodologies that are deployed by modern structural engineers to mitigate natural drawbacks of steel concrete structures.
The methodology is employed to produce various commercial structures. Pre-stressing is done on floors, bridges, and beams. Concrete withstands more loads while subjected to compressive loads than while subjected to tensile loads. This behaviour implies that it can withstand more loads when used to produce columns that are to be subjected to compressive loads relative to when it supports loads that subject it to tension.
A similar scenario is experienced when concrete is deployed to produce a beam. For instance, when a beam is simply supported and loaded, the dead load (load due to the weight of the beam) and the applied load subject the upper portion of the beam to compressive deformation. The lower side is subjected to tensile strain, which induces tensile stress. Since non-reinforced concrete is stronger in compression than in tension, the beam can only support a limited amount of load in tension.
When the span of a beam is increased, the supportable load reduces because longer spans buckle more than shorter spans. One way of dealing with this challenge is by providing more support to the beam. However, this strategy is inconvenient, especially when a large floor area is required such as the case of St Paul’s Cathedral. The amount of concrete used to make a beam to support a given amount of load will be higher than in the case of a reinforced beam. Hence, the cost of constructing beams for supporting loads in a multi-storey building such as St Paul’s Cathedral using plain concrete becomes prohibitive. Hence, reinforcing becomes necessary.
Traditionally, reinforcing was done using steel bars, which provided the required strength in tension. With a reinforced beam, the span, which can support an equivalent load with a non-reinforced concrete beam that has equal cross-sectional dimensions, is higher. The need to increase such spans even higher gives rise to the need for a pre-stressed concrete, which will be most applicable in the construction of flying buttresses, landings for cones and domes, and piers in case of St Paul’s Cathedral if it were to be done today.
Constructing the cone for the cathedral would not make use of stones as one of the material selection alternatives. Concrete is the prime material that is deployed today in the construction of structures that carry loads of overriding components. Building St Paul’s Cathedral today would require significant implications in terms of cost, strength requirements, and material availability. This situation would create the necessity for the deployment of pre-stressed concrete instead of precast concrete. Wren would definitely consider Freyssinet’s plan to improve the cathedral’s building technology.
From 1928 to 1933, Freyssinet made the most significant achievement in the development of pre-stressed concrete. These achievements were due to the discovery of double-actuated hydraulic jacks that were deployed to stress concrete’s high tensile wires. The accomplishments also followed the discovery of vibration methodology that was deployed in producing high-strength steel (Raju 2). These discoveries marked the beginning of the intensive spread of the practical applicability of pre-stressed steel since 1935.
Upon their realization of the effectiveness of Freyssinet’s methodology of pre-stressing concrete, civil engineers in the US and Europe began constructing long-span beams from 1945 to 1950. A good example of such a beam was deployed in the construction of Tamins-Reichenau Bridge in Switzerland. Building St. Paul’s Cathedral in London using the pre-stressed concrete today requires Wren to manufacture pre-stressed beams just as he sourced stones, timber, lead, and wood among other materials. Manufacturing of pre-stressed concrete is done at a pre-stressing concrete plant.
Since beams would be required in the cathedral’s construction, setting such a plant would make the cost of construction prohibitive. The best alternative entails contracting the manufacturing of beams to support the domes, cones, and other components of the cathedral. During the manufacturing of the pre-stressed concrete, the contracted civil engineers need to apply two ways of inducing compressive stresses in pre-stressed concrete. The first approach encompasses pre-tensioning while the second approach entails post-tensioning. In the pre-tensioning process, the concrete has to be placed after stretching of tendons.
Force that is used to pre-stress concrete has to be transferred to the concrete via a bond. In the pre-tensioning method, concrete is placed on the stretching steel. Mutsuyoshi and Hai suggest, “To strengthen the beam, steel tendons with high strength are put in between two abutments to be tensioned to around 70 to 80 percent of their overall strength” (167). Tendons are held in their respective positions by means of a tensioning force before the introduction of concrete into a mould.
Time would then be provided for the concrete to cure for it to gain the necessary strength. Tensioning forces would then be released. Steel produces a reaction after attaining the required strength from the concrete, thus making it gain the length that it had before. Consequently, tensile stresses are converted into compressive stresses, which upon complete curing of the concrete become very firm.
If they were to build the church today, manufacturers of the beams that were used to build St Paul’s Cathedral would consider using post-tensioning methodology to induce the necessary strength in the concrete. In this approach, the concrete would be put after the tensioning and hardening of tendons before the steel is stretched. The resulting forces that characterize the pre-stressing would then be moved along the concrete supports (Mutsuyoshi and Hai 171).
Building the cathedral today would require the deployment of modern-day advanced lifting machineries such as hoist cranes. The building ground would be prepared using heavy earthmovers. With modern lifting machineries, the cone and even the dome would be cast and lifted into place while the decorations would also be moulded in place instead of being sculptured. Nevertheless, the painting of the dome, marble floor finishing, statues, various decorations on the window, altars, and the pulpit among other places would be done in the same way it was done in the 17th century.
Works Cited
Blundy, Rachel. Construction Secrets for St Paul’s Cathedral to Be Exposed in New Television Series, 2014. Web.
Campbell, James. Building St Paul’s. London: Themes and Hudson, 2007. Print.
Mutsuyoshi, Haiyu, and Nier Hai. Recent Technology of Pre-Stressed Concrete Bridges in Japan. Tokyo: Saitama University, 2010. Print.
Raju, Kingston. Pre-Stressed Concrete. New York, NY: McGraw Hill, 2009. Print.
Sankey, Douglas. “Cathedrals, granaries and urban vitality in late Roman London.” RI: Journal of Roman Archaeology 3.1(1998): 78–82. Print.
Tatton-Brown, Tim, and John Crook. The English Cathedral. London: New Holland Publishers, 2002. Print.