Emirate Airlines is one of the three airline companies which integrated Six Sigma in their operations. Such integration supported the company’s efficiency and services’ quality growth, making Emirate Airlines one of the best flight carriers around the world. Nonetheless, the importance of continuous improvement encourages the company to use lean approaches not only in the operational management but also in activities aligned with customer satisfaction rates. Therefore, the study on Six Sigma’s effect on customer satisfaction rates within Emirate Airlines should indicate whether the lean approach stimulates efficiency, quality and personalisation of services provided by the airline.
Literature Review
The concept of Six Sigma dates back to 1981, when, frustrated by the numerous attempts to integrate different quality systems, Motorola and General Electric began to organise them into a network of improvements that would ensure consumer satisfaction and product competitiveness. Motorola’s president has set a tenfold increase in productivity over five years (Juliani & de Oliveira, 2019). The engineer, Bill Smith, has researched this program to determine the correlation between in-service product performance and repair frequency. In 1985, Smith provided the results of his research and suggested measures to reduce product defects (Juliani & de Oliveira, 2019).
These studies formed the basis of the modern concept of Six Sigma. Six Sigma is an approach to business improvement that seeks to identify and eliminate the causes of errors or defects in business processes by focusing on those baseline parameters that are critical to the consumer (Garza-Reyes et al., 2017). Six Sigma is a strategic approach that works across all processes, products and industries. Recently, this concept has been receiving increasing attention due to the significant economic achievements of those organisations that declare their commitment to this area of quality management.
The essence of the Six Sigma method is effortless. Suppose that as a result of the manufacturer’s negotiations with the consumer, they agreed that the tolerance for some critical product characteristics would be, for example, 1 mm. Then the task of the manufacturer, if they share the idea of “Six Sigma,” is straightforward. They need to “drive” the natural dispersion of this indicator in the process of production to such stable limits that it falls within the agreed tolerance limit of 12 times, which, exactly, is ± 6q.
The basis of the Six Sigma strategy is the thoughtful and purposeful application of different methods (mostly statistical ones), the improvement of the quality of processes by specially formed teams of talented specialists, who work in close contact with senior management. These groups solve carefully selected and promising tasks that bring significant economic benefits (Garza-Reyes et al., 2017). The theoretical basis of the Six Sigma methodology is the developed provisions for evaluating the possibility of a statistically controlled process to satisfy the given requirements, taking into account deviations of product characteristics from the mean and centeredness.
In the 20th century, a process was historically acceptable if it was in a statistically controlled state, had scattering within ± 3q and fixed mean value, that is, when 99.73% of all possible characteristics were covered under the ± 3q distribution curve. Therefore, the process capability of ± 3q leads to the production of 0.27% defects, or 2,700 mistakes per million skills (DMM). Assuming that the average may shift by 1.5q, the number of DMM increases to 66 810. The four-sigma processes currently used by many organisations provide 6210 DMM, whereas the operation corresponding to ± 6q is only 3.4 DMM (Morgan, 2018). It means 99.99966% of the production of defective products or the implementation of any services or actions.
The basics of the Six Sigma concept were laid by Motorola. Its approach was based on the classic continuous improvement scheme based on the cyclic model of Schuhart quality management – PDCA (Julianin & de Oliveira, 2019). The first stage – planning – involves formulating goals and objectives, identifying critical parameters for success, improvement plan, project selection and team building. The second stage – implementation – involves training and coaching, plus application. The third stage – verification – involves measuring, evaluating performance, analysing and reviewing projects. The fourth step – corrective action – involves continuous improvement, standardisation, consumer research, benchmarking and redesign.
Subsequently, under the Six Sigma concept, the PDCA model was transformed into the AISM model: Measure, Analyse, Improve, Control. Recently, there has been a tendency to complement this model with several stages. Often the DMAIC variant occurs – a Define (definition) step is added at the beginning of the model. Six Sigma Academy (USA) executives Harry and Schroeder believe that this program consists of four stages: Recognise, DMAIC, Standardise, Integrate (Barboud et al., 2018).
It should be highlighted that in the concept of “Six Sigma,” the emphasis is not so much on the number of defects per million possibilities, but on the methodology of systematic reduction of process scattering (Marshall et al., 2020). The urgent need to move away from the traditional three-sigma approach is easy to see if to imagine the output of a process consisting of, for example, 20 consecutive operations, each of which provides a given percentage of output. If this percentage corresponds to the “three-sigma” approach, then at the output it is (0,9973) 20 == 0,947, that means, about 5% of the deficit, whereas at the “Six Sigma” approach, we have (0,999 996 6) 20 = 0,999 93 that is, only 70 defects per million.
The base of the Six Sigma concept is formulated by Motorola as follows:
- Defining the number of defects per million capabilities (DMM) as a standard measure to various aspects of the activity of any organisation (computerisation, programming, production development, administrative management);
- Introduction of intensive training of teams implementing projects to improve profitability, reduce unforeseen losses and shorten the work cycle;
- Concentrating the leadership of the organisation to support the activities of the groups: guidance helps teams overcome resistance to change, provides them with additional resources and retains groups within the strategic goals of the organisation;
- Training highly qualified business process improvement experts who can use quantitative and qualitative improvement tools to meet the strategic objectives of the organisation;
- Ensuring that appropriate evaluation is carried out before and after process improvement to determine business results and their compliance with strategic goals;
- Appointing trained and certified experts to improve the business process to lead project teams for one to three years.
The application of the Six Sigma method involves the following steps.
- Step 1. Measurement. One or more quality-critical characteristics are selected, necessary measures are made, results are recorded and short-term and long-term changes in processes are evaluated.
- Step 2. Analysis. Benchmarking of crucial production characteristics, analysis of breaks is carried out and it is found out what conditions contribute to the best performance. Sometimes it becomes apparent that radically changing the product or its manufacturing process is required.
- Step 3. Improvement. Specific product features are being improved to meet quality assurance goals and financial performance. Then the characteristics are diagnosed and the primary sources of change are identified. The critical process variables are then determined using experiment planning methods. The quality requirements are set for each of them.
- Step 4. Management. The developed process is documented and monitored using statistical methods of analysis. Depending on the results of the investigation, it is sometimes necessary to return to the previous steps.
The Six Sigma toolkit uses both simple quality improvement and more sophisticated tools: statistical process control (SPC), scheduling of types and consequences of potential failures (FMEA), measurement systems analysis (MSA), experiment planning (DOE). Besides, softer technologies are used to solve problems: team formation, project management, conflict resolution and cross-functional problem-solving techniques (Syltevik et al., 2018). Some of these tools have been in use for 20 years. Considering that the quality of customer service comes first, the concept of Six Sigma has a set of tools to improve the quality of service, design and production, will not only improve the profitability of the organisation but also increase its market share.
Research Methodology
For the study on quality improvement within Emirate Airlines, the secondary data analysis is selected. In this qualitative research, it is decided to collect reports and industry data on how airlines integrate Six Sigma in their customer services to improve customer satisfaction rates. As a result, the secondary data analysis should provide comprehensive and consistent findings on whether the integration of the lean approaches triggers changes in this critical for the airlines’ operational field.
The study of secondary sources, despite their classification, is the starting point for the creation of any research programs. Costly and time-consuming field research is irrelevant when the solution to the problem can be found in literature, statistics, company reports, or other available materials (Sadik, 2018). The study of secondary information is the simplest way of research that can be carried out on its own to make the necessary current management decisions (Ahmad et al., 2019). They use materials that come from external and internal sources. External sources provide, first of all, information about the environment of the enterprise, internal sources – about the status and ways of using the funds.
The choice of data collection methods depends on the purpose of the study, the ratio of the costs involved and the expected results. The experience of many businesses in different industries shows that secondary research allows to achieve lower cost goals than the primary ones. The advantages of the secondary research are in the fact that the cost of conducting secondary research is lower than obtaining the same results through primary research and in most cases, secondary information is sufficient to make decisions regarding the innovation of research (Mohamad et al., 2017). Data collection by secondary methods allows creating a basis for activity analysis and identification of tendencies of development of the bank itself, its place in a competitive environment, the most critical areas of innovation activity.
The study on customer satisfaction rates’ improvement via lean approaches integration should answer the research question (RQ) whether the Six Sigma approach increases customer satisfaction from the airlines’ services. To answer this question, the following hypotheses are developed:
- H0: The Six Sigma approach does not affect the customer satisfaction rates.
- H1: The Six Sigma approach increases customer satisfaction rates.
Data Analysis and Results
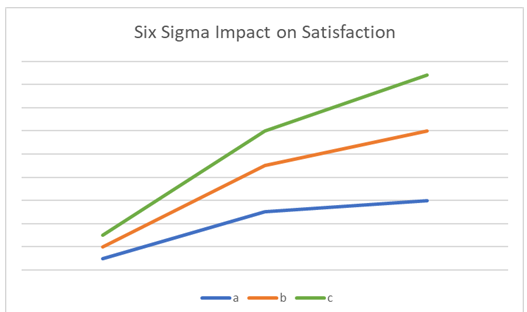
The analysis of Emirate Airlines’ annual reports and corporate social responsibility reveals that the integration of Six Sigma supports the increase in customer satisfaction rates. The conducted review and analysis of four crucial areas in customer services indicate that
- waiting time on the registration desk has a significant impact on clients in 38% of all cases;
- the accuracy and efficiency of the solutions matter in 23% of all cases; and
- the quality and personalisation of services affect customer satisfaction rates in 35% of all cases.
What is more, the dependence of customer satisfaction on these three characteristics has a statistically significant impact on the overall satisfaction rates. The p-value is.01, which is less than the test standard p<.05. In this case, the changes in any of the selected and tested service features may cause disruptions and a decline in customer satisfaction rates (Mohamad et al., 2017). The H1 is confirmed by the test and analysis, as there is Six Sigma’s impact on customer satisfaction rates if the methodology is integrated into operations or personnel responsibilities.
Nonetheless, the comparison between the Six Sigma approach and traditional customer-oriented approach is needed to understand whether the lean methodology stimulates satisfaction rates’ growth, or whether this parameter dependence on other variables within airlines’ operations.
Discussion
The obtained results from the statistical evaluation indicate that the integration of a lean approach within customer services positively affected customer satisfaction rates. It can be admitted that such strong dependence is due to the customers’ sensitivity to how airlines behave with clients and proceed with their requests (Sweis et al., 2019). In this instance, the waiting time variable depicts the importance of accuracy within personnel actions, as the high velocity of requests proceeding increases satisfaction rates and quality of the provided reports (Hussain, 2016).
Moreover, the accuracy and quality of the provided assistance contribute to the mitigation of the number of returning requests, as clients obtain exclusive information or help regarding their inquiries (Lasrado, 2018). In this case, the first and second variables show interdependence and significant reliance on the lean approaches, as the quality tool and mechanism.
Recommendations
In the UAE, the Transportation Security Administration (TSA) used new technology to quickly search for items in baggage, reducing the waiting time for passengers on the security control line (Al-Aomar et al., 2016). TSA has invested millions of dollars in finding ways to use process improvement to improve passenger service without compromising safety. Given many processes associated, there are several to integrate Six Sigma and enhance the internal operations within the airport.
Emirate Airlines can also implement a lean manufacturing system to optimise airport security. After examining the data, the airport can integrate Six Sigma into the security process, which included the placement of an “intermediary for passengers” at the beginning of the inspection strip and the installation of a support agent at the end of the line. The idea is to find someone who would help passengers prepare for check-in and help them return their belongings when they are ready. The airport can train employees with this lean approach. The satisfaction level of passengers passing through the new security lines may reach 95%.
Further, another project may aim the efficiency of baggage handling increase, allowing the company to achieve high results and saved many travellers from problems. Emirate Airlines should apply the Lean Six Sigma strategy to solve problems associated with baggage handling on connecting flights, which often leads to flight delays, as aircraft are waiting for baggage to be loaded (Alsyouf et al., 2018). The use of DMAIC methodology will provide a continuous improvement cycle to baggage handling on connecting flights. The goal is to reduce delays in aircraft turnover, by keeping the baggage handling delays less than 30%.
Conclusion
The conducted study on Six Sigma’s effect on Emirate Airlines’ customer satisfaction rates reveals that the lean approaches support the quality and accuracy of customer services within the company. What is more, the analysis of secondary data from the company and industry reveals that Six Sigma’s philosophy has significance in managing high quality, accurate and personalised services when dealing with customers’ requests, claims and inquiries.
In this instance, the integration of Six Sigma in all customer-related services and operations should stimulate the continuous advancement of Emirate Airlines’ services and their efficiency regarding proceeding with clients’ needs and issues. The proposed areas for further Six Sigma’s integration should create the aligned process in all services related to clients’ needs so that Emirate Airlines may continue to expand and advance its values and products based on the customer-oriented and quality assurance principles.
References
The selected reference style is APA due to its convenience in use and editing.
Ahmad, S. Z., Ahmad, N., & Papastathopoulos, A. (2019). Measuring service quality and customer satisfaction of the small-and medium-sized hotels (SMSHs) industry: Lessons from United Arab Emirates (UAE). Tourism Review.
Al-Aomar, R., Aljeneibi, S., & Almazroui, S. (2016). Reducing Operational Downtime in Service Processes: A Six Sigma Case Study. 2016 International Conference on Industrial Engineering, Management Science and Application (ICIMSA), 1-5.
Alsyouf, I., Kumar, U., Al-Ashi, L., & Al-Hammadi, M. (2018). Improving baggage flow in the baggage handling system at a UAE-based airline using lean Six Sigma tools. Quality Engineering, 30(3), 432-452.
Barboud, O. S., Abdulaal, R. M., & Kabli, M. R. (2018). Utilizing quality tools: Enhance the productivity at aircraft maintenance sector of Saudi Airlines. Journal of King Abdulaziz University, 29(1), 3-19.
Garza-Reyes, J. A., Kumar, V., Martinez-Covarrubias, J. L., & Lim, M. K. (2017). Managing Innovation and Operations in the 21st Century. Boca Raton. Productivity Press.
Hussain, R. (2016). The mediating role of customer satisfaction: Evidence from the airline industry. Asia Pacific Journal of Marketing and Logistics, 28(2), 234-255. Web.
Juliani, F., & de Oliveira, O. J. (2019). Lean Six Sigma principles and practices under a management perspective. Production Planning & Control, 1-22.
Lasrado, F. (2018). Legacy of Excellence: The Case of the United Arab Emirates (UAE). Management for Professionals, 37-56. Web.
Marshall, A. J., Ojiako, U., Williams, T., Al-Mazrooie, J. R., Lin, F., & Chipulu, M. (2020). Risk management as knowledge production: Application to fast-tracked complex multi-stakeholder airport projects. In Entrepreneurial Innovation and Economic Development in Dubai and Comparisons to Its Sister Cities (pp. 33-66). IGI Global.
Mohamad, H. A. D., Ab Yazid, M. S., Khatibi, A., & Azam, S. F. (2017). Service quality, customer satisfaction and customer loyalty of the hotel industry in United Arab Emirates (UAE): A measurement model. European Journal of Management and Marketing Studies.
Morgan, J. (2018). An evidence-based model for agile organizational change. Available at SSRN 3306206.
Sadik, R. M. (2018). Implementation of total quality management in airline (case study Emirates Airline). International Journal, 7(5).
Sweis, R. J., Asma’a, S. I., Amayreh, I., & Al-Sayyed, N. (2019). The relationship between total quality management (TQM) implementation and organizational performance: Evidence from the airlines’ companies in UAE. International Journal of Information, Business and Management, 11(1), 58.
Syltevik, S., Karamperidis, S., Antony, J., & Taheri, B. (2018). Lean for airport services: A systematic literature review and agenda for future research. International Journal of Quality & Reliability Management.