Introduction
A ship’s steering gear operated by fluid power incorporates two fluid systems each constituting a pump-fed from its supply tank and a thruster unit with an isolating the pair. The tanks have mechanisms that close the isolating valve in case the fluid level drops. If the fluid drops beyond a set limit, the pump-fed from that reservoir is stopped and the pump in the other system started.
Hydraulic and pneumatic systems are used for the transmission of power. In Hydraulic and pneumatic systems, a force is applied on a piston and transmitted to the next through oil and air respectively. The fluid in hydraulic systems is oil while air is used in pneumatic systems. A typical fluid diagram is shown below.
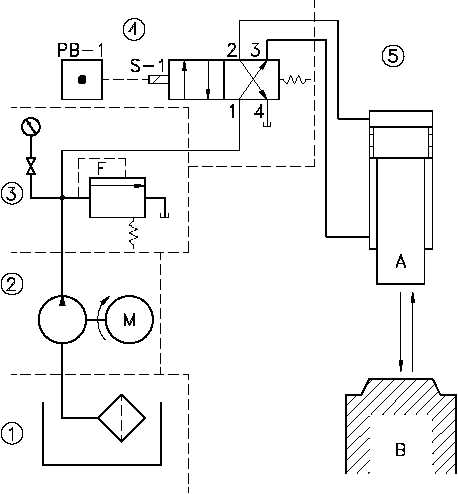
Engineering Fluid Diagrams and Prints DOE-HDBK-1016/1-93 FLUID POWER P&IDs.
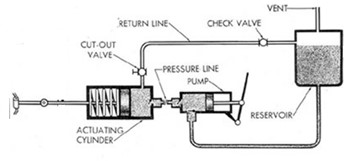
Advantages of hydraulic and pneumatic systems
These systems are widely used for power transmission because they have several notable advantages. The use of these systems results in much less complicated systems as parts like gears and cams are eliminated and fluids used in the transmission of power instead of solid parts. This guarantees minimal breakdowns as the fluids are not subject to breakages. Fluid transmission is convenient because it allows easy remote operation; the power can be transmitted to remote locations very easily by use of tubes with very few losses. Properly adapted pneumatic and hydraulic systems deliver smooth quiet operation with no vibration and variations in loads do not affect the system. These systems are also very economical to use because the cost of maintenance is pretty low. Hydraulic systems allow flexible power distribution over tubes or pipes and also allow for force multiplication increasing flexibility. They are very sensitive and are ideal in cases where high precision is required. These systems operate with oil and therefore are self-lubricated eliminating the cost of additional lubrication and cutting down the rate of wear. Quiet operation that is characteristic of hydraulic systems is vital especially in marine vessels where enemy detection is to be minimized. Structural advantages of these systems include few moving parts, low losses, and reduced wear. In terms of operation, forces can be distributed equally in many directions. The systems are also relatively safe and reliable and have an impressive response.
Suitability of hydraulic and pneumatic systems to different requirements
Despite their similarities, pneumatic and hydraulic systems vary in their suitability for various applications. Pneumatic systems are preferred in applications that require speed, average pressure, and fairly accurate control. Hydraulic systems on the other hand are ideal for systems that require very high pressure and exceedingly accurate control. The two systems are sometimes combined in cases where medium pressure and a bit more accuracy than as is possible in pneumatic systems are required.
Disadvantages of hydraulic and pneumatic systems
Pneumatic and hydraulic systems do have their disadvantages besides the discussed advantages. The use of fluids as power transmission agents poses several challenges. These fluids must be properly confined in the system and the structural integrity of the system parts must not be compromised at all. Leaks of any kind must be avoided at all costs to ensure minimal energy losses. These systems require constant checks as impurities or foreign material must be avoided as they could clog valves and other small orifices that are common in these systems. This then necessitates the use of fine filters to ensure smooth and uninterrupted operation. They also require that anyone working on the systems have some knowledge of their components and operation. The high pressure in hydraulic and pneumatic systems can pose a danger to the personnel operating the systems especially in the event of ruptures. Also, air compressors are expensive because they require constant maintenance and are fairly inefficient.
Alternative systems
Alternative systems that could be used in marine steering are mechanical and electromechanical. Mechanical steering systems (cable systems) come in two main forms; rotary and rack and pinion. These systems employ the use of gears, cams, and many other solid parts. This gives these systems quite a several disadvantages over the hydraulic system. The solid components of mechanical systems are prone to wear off due to the constant motion of the steering system. Friction between the moving parts is the chief cause of this wear. Expenses in lubrication are inevitable if any attempts to reduce this are to be employed. Mechanical systems are also limited as sometimes their low capacity is limited. Large marine vessels that require large forces to steer would need alternative systems because if used, mechanical steering would be prone to rapid wear due to the large forces involved; this would mean reduced durability. Relative to hydraulic steering, mechanical steering systems have large space requirements due to the many solid parts of the drive train involved including gears, shafts, and housings which take up a lot of space. Mechanical systems using rack and pinion require long rack housings that take up a lot of space and offer little flexibility in mounting. All mechanical systems have a backlash by their design. This factor leads to instability in high-performance boats at speeds exceeding 50 miles per hour (Teleflex marine steering). Dual cable steering is normally recommended for these types of boats. Mechanical steering also displays many losses as the forces are transmitted over many solid parts.
Cable systems on the other hand have the advantage of durability and reliability if properly adapted for the particular vessel. They are also fairly simple to operate.
Another alternative steering system would be the electromechanical system. In this system, electric motors and mechanical drive trains are employed. The motors give the required energy which is then transmitted via the mechanical drive train (Payne par.3). All the challenges outlined above due to the mechanical drive train apply to the electromechanical systems as well. Additionally, the electromechanical system necessitates the need for a source of electric power. This as anticipated has economic implications as the electric power comes at some extra cost. Electric motors used also have the disadvantage that they are not ideal in cases where instantaneous or abrupt stopping is required as they tend to ‘over travel’. This weakness of electric motors makes them unsuitable for applications that require high levels of accuracy. Furthermore, electromechanical systems are noisier during operation than the quiet hydraulic systems
The advantage of this system on the other hand is that it eliminates any form of drudgery that may have been associated with the mechanical system because the operator does not have to use energy turning the steering wheel; this is done by the motors. The operator only has to push a button.
The table below was used in the review of the several available systems before deciding to choose the hydraulic system as the most ideal for this application
Table 1
Safety
The safety of life at sea (SOLAS) convention is one of the most important treaties ever signed about safety at sea. It seeks to ensure the safety of crew and passengers on every vessel at sea. The SOLAS has a technical provision that specifies minimum standards for the manufacture, instrumentation, and operation of ships about their safety. Flag states are charged with the responsibility of seeing to it that ships in their territory do comply with SOLAS’ requirements. In the convention, certificates are issued as confirmation that all rules have been followed. (SOLAS par.6).
Everyone who manufactures supplies or modifies machinery must devise ways and means of detecting hazards and a means of risk analysis. Hazards that come about while working with fluid power cannot be eliminated but appropriate engineering control methods must be employed to ensure safety. In the proposed system, if the fault is detected and cannot be automatically countered, then the further operation of the machinery can be halted until the operation problem is diagnosed and safety affirmed. Additionally, the proposed control system is designed such that one fault in it does not disable the safety function; the safety function, therefore, remains active even after one or two components fail (Shead par.4). Monitored safety valve systems, safety pressure switches, monitored rod blocks and trapped keyboard valve interlocks are some safety features used in modern-day hydraulic and pneumatic systems.
Steering of any kind of vessel is very important because it could either save lives or lead to loss of lives. Fluid systems like described above operate well when the fluid doesn’t leak. However, in the case that the fluid leaks, then the whole steering system may fail to expose people on board to great danger. The proposed steering system seeks to counter this problem by providing a steering gear that acts in the event of a leak in the system to counter failure and allow the steering to continue. This system is such that the gear only becomes operational in the event of a leak but is otherwise not. This would ensure safety because of assured steering.
Conclusion
Many systems are available and viable for use in marine steering systems. All of the systems can perform well if properly adapted for the particular application. However, after careful review, Hydraulic systems were found to have been the most suitable for this application. Their relative advantages over mechanical, electromechanical, and electric systems gave them the upper hand In this application. They are therefore hereby recommended.
Works cited
International Convention for the Safety of Life at Sea (SOLAS), 1974. Web.
Payne, John. The marine electrical and electronics bible. New York. Google Books., 1998.
Shead, David. Machinery Safety and Control Systems. 2009. Web.
Teleflex marine steering.An introduction to mechanical and hydraulic steering, 2006. Web.