History: Case Studies
The cyclic steam injection process was first implemented in 1959. By this time, the steam injector wells were already in place and had begun production. Soon after the technique was being deployed for extraction of oil, many oil exploration companies started using this method despite being considered old-fashioned. However, owing to its operational efficiency the method was used without a scientifically established basis or precedent. There was very little literature evidence available regarding its potential uses and cost efficiencies as weighed against other methods on oil exploration companies across the CSI was deployed after successful trials and subsequently refined to be used for commercial scale oil extraction in rigs where other methods had failed or were seemingly ineffective.
The Russian Case Study
After this initial period, there has been substantial advances in the oil extraction process. However, it was established by scientific research that CSI was far superior than any other method for the extraction of vicious crude oil from horizontal wells. Chemical additives further enhance its capacity and potential to extract oil and the repeated steam injection results in extraction of large volumes of oil. The efficiency of this method also increased with time as a result of improvement in underlying technology and steam producing equipment.
Co-injection of steam with surfactants and foams reduce water production and consequently increases the oil production. For instance, in Russia, oil exploration companies use foams and gels to maximize efficiency. In this case, this resulted in a 33% decrease in the amount of water used and a corresponding increase of 25% in the oil rate of production (Sheng 2013). The number of stimulation cycles also increased with advancement in technology. It started with only 3 cycles which grew to 30 cycles as a result of a greater understanding of steam usage, its properties and injection conditions (Alvarez & Han, 2013).
The Canadian Case Study
Canada also deployed this system with certain changes to improve the overall efficiency of the process. The Canadian oil exploration sector worked extensively to improve upon the steam distribution mechanism to improve efficiency. Screen sections were used to improve contact between the well and the reservoir (Alvarez & Han, 2013). Additionally, small flow vents were used to control flow of water and enhance oil production.
Liquid has also been added to steam in order to increase the recovery factor. It has been noted that the recovery factor increases by 3-6% (Alvarez & Han, 2013). Other methods have also been deployed to increase efficiency of CSI process which include air injection, and use of biodiesel. Both methods have shown to result in greater efficiency and approximately 20% increase in recovery. (Abidin, Puspasari & Nugroho 2012).
The Chinese and American Case Studies
China uses state of the art and novel techniques to ensure maximum efficiency while using CSI for oil extraction. A few of the parameters include controlled steam generation, insulating surface pipeline, multi-zone steam injection and use of chemical additives (Alvarez & Han, 2013). Other measures such as use of process control systems have also served to maximize output (Haiyan et al., 2005). Furthermore, the process of steam injection has been improved by the using separated-zone injection methods (Sheng 2013). Primarily, these techniques have been observed to increase to up to 70% of the steam zone (Alvarez & Han, 2013).
Field tests in the Henan Oil Field in China depict the benefits of carbamide use. The use of carbmide resulted in an improved recovery of oil by an approximate 7-8%. Residual oil saturation also decreased slightly (Zhang et al, 2009). Similar results were obtained in Venezuela where the technique was replicated to enhance steam distribution in the wells. The technique resulted in the improvement of production by 40%. (Abidin, Puspasari & Nugroho 2012). Furthermore, solvents were employed to improve the injectivity of steam by eliminating organic deposits from rocks. Another measure adopted in China was tubing and annulus of the well achieve maximum efficiency.
In addition to the measures taken above, some other methodologies were adopted to improve efficiency of CSI technique. Subtle variations in temperatures and pressure has been found to be useful depending upon the region and type of well. In the US, calculated reservoir heating has been used instead of the more traditional approach in which each of the wells are heated separately. This technique was employed in the Cold Lake field and Potter sands of California, through a method involving sequential steaming process to enhance oil production (Sheng 2013). In the Cold Lake field, high pressure injection is used to fracture the formation. This method increased production of oil by 30% (Alvarez & Han, 2013).
Economic Viability of CSI
For any method to be practical for industrial extraction scale, it needs to be evaluated for efficiency. It can be noted that CSI has been an important method for enhanced oil extraction. However, it still remains a solution for oil extraction from wells where other conventional techniques cannot be employed with effect. Therefore, considerable improvements need to be made for CSI to be effective. Moreover, further research is warranted to provide engineers with state of the art cost effective solutions. This can be done by understanding the underlying phenomenon of wettability, relative permeability, temperatures, and pressures changes to increase the oil recovery process (Wang et al. 2017).
One of the most viable qualities provided by the CSI is its usefulness in extracting heavy oil. Until relatively recently, heavy oil excavation was not considered economically viable. Heavy oil stands for with 20 degree API gravity or lower. It is significantly easier to find and develop, but harder to extract and process. The operating costs of producing heavy oil were incomparably high and unable to keep up with the oil prices remaining in the 30$/bbl range (Sun et al., 2017). However, since the 2000s, there has been an ongoing campaign of investments in the heavy oil projects, for which CSI has proven to be an economically effective way of extraction.
Californian Midway-Sunset field presents an excellent economic opportunity for extracting heavy oil using CSI, as it already implements two steam injection wells in the area. Other potential areas of investment include Kern River, which has projected deposits of 1.57 billion bbl, and South Belridge, with 1.06 billion bbl in estimated deposits (Sun et al., 2017). CSI, also known as CSS, or cyclic steam stimulation, is known for producing large yields in the first few years of excavation, with the output gradually dropping over the next several decades.
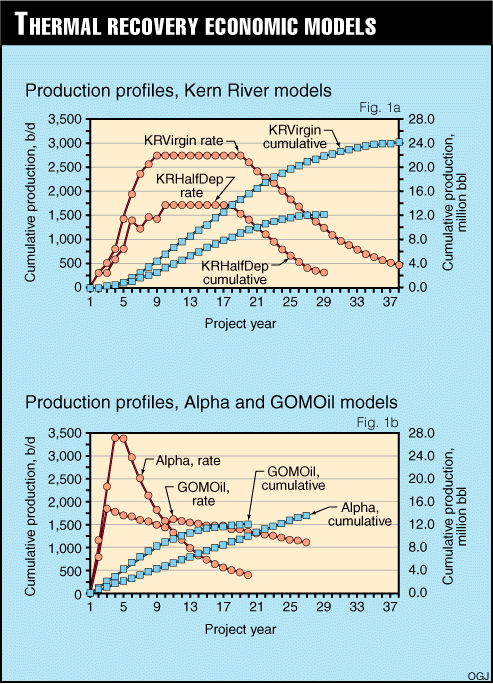
Figure 1 demonstrates comparative economic output for four avenues for potential investment. The first three, including two projected models for Kern River excavation and one for Alpha, which is an existing older CSI platform, are compared with a standard investment into the Mexican gulf shore oil (Sun et al., 2017). As it is possible to see, CSI excavation offers a substantially higher yield during the first decade for the Alpha venture, and for two decades for the Kern River excavation projects. Although the extraction rates fall down substantially after that, it is possible to see that the overall output is comparable if not higher than that of an average shoal oil venture in the Mexican Gulf.
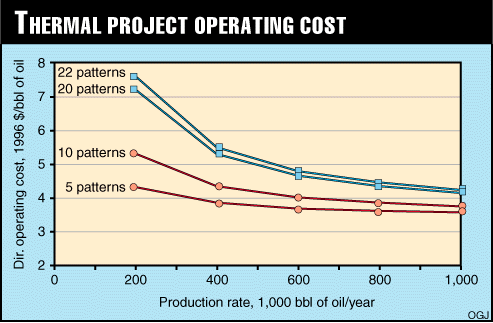
As it was already mentioned, CSI oil extraction processes have relatively high project operation costs. These costs are expanded by the number of patterns included in the excavation. The more patterns there are – the higher are the expenses for operating them. However, it must also be noted that the expenses during the first years of production are associated with the construction of oil platforms that use CSI as its primary oil stimulation process. It is the same for every venture. As demonstrated in Figure 2, the costs associated with the extraction of 1000 bbl of oil per year are dropping significantly as the production output grows. At its peak, the operational costs for 22 patterns are comparable with five patterns, but lending a significantly higher output potential (Sun et al., 2017).
As it was exemplified by Alpha project as well as the estimations for two Kern River projects in California, SCI-based developments for heavy oil present a new and economically-viable prospective avenue for the petroleum industry. The initial high costs of extraction are offset by rapidly rising excavation outputs. By the time the venture reaches its peak production, these costs are significantly lowered, enabling to use economy of scale.
The overall amounts of oil extracted are comparable to shoal light oil ventures. Due to high yields in the first two decades and subsequently lower returns later, SCI-based heavy oil excavation projects are relatively short-term, when compared to standard practices. Given the similar amounts of oil extracted during the 40-year old period, they are arguably less risky, as they repay the investments much sooner.
Although Enhanced Oil Recovery (EOR) is one of the most frequently applied techniques, CSI is still not the most commonly used technique. Gas injection is a methodology of choice. CSI is only used for horizontal wells with crude oil with high viscosity. Simple steam injection is also used frequently since it is much safer and does not pose serious environmental risks. Other EOR methods are much hazardous and pose considerable risks to the environment.
This is the reason why more research is being directed towards pilot studies to improve steam injection techniques. Many countries are now encouraging the use of steam injection techniques as against gas injection. In these countries, the underlying regulations do not allow for use of some cheaper methods of extraction that are otherwise environmentally hazardous. In these countries, CSI as a viable mode of enhanced oil recovery has been encouraged.
References
Abidin, Z., Puspasari, T., & Nugroho, W. 2012. Polymers for enhanced oil recovery technology. Procedia Chemistry, 4, 11-16.
Alvarez, J. & Han, S. (2013). Current Overview of Cyclic Steam Injection. Journal of Petroleum Science Research, 2 (1). 116-127.
Haiyan, H., Shuhong, W., Yitang, Z., Dingmin, W., and Zhong, G. 2005. “State‐of‐the‐Art of Heavy‐Oil Development in China and Its Technology Challenges.” SPE 10617‐MS.
Sheng, J. 2013. Enhanced oil recovery field case studies. Gulf Professional Publishing.
Sun, F., Yao, Y., Chen, M., Li, X., Zhao, L., Meng, Y., … Feng, D. (2017). Performance analysis of superheated steam injection for heavy oil recovery and modeling of wellbore heat efficiency. Energy, 125, 795-804.
Wang, Y., Zhang, L., Deng, J., Wang, Y., Ren, S., & Hu, C. 2017. An innovative air assisted cyclic steam stimulation technique for enhanced heavy oil recovery. Journal of Petroleum Science and Engineering, 151, 254-263.