Executive Summary
The performance of machines and electronic devices in industries is dependent on the prevailing temperatures. To control machines and electronic devices within the optimal temperature requires automatic temperature controllers. Digital controller is a suitable temperature controller because it is a three-relay system, which connects to the heater, the cooler, and the alarm. The illustration of its effectiveness in temperature regulation was evident when it was set at the control temperature of 80°F and a difference of 1°F, which gave 79°F lower control limit and 81°F upper control limit. The digital controller also responded to alarm temperature limit that was set at 85°F.
Background
Temperature control is central to functioning of machines and electronic devices, including computers. Engineers have designed air cooling and liquid cooling systems to regulate temperate of machines in industries (Zhang, 2010). To enhance effectiveness of these cooling systems, the engineers have come up with digital controllers.
Scope
The project focused on demonstrating the effectiveness of digital controller in regulating the temperature of machines and electronic devices in industries. Specifically, the project demonstrated the ability of digital controller to regulate temperate at 80±1°F. Moreover, the project demonstrated how digital controller gives warnings when temperature exceeds 85°F or goes below 79°F.
Design Summary
The project used the experimental design in demonstrating the effectiveness of digital controller in regulating temperature of machines and electronic devices. The three-relay system is the heart of the digital controller because it comprises the alarm, the cooler, and heater, which the control system uses in regulating temperature.
Introduction
Machines and electronic devices constantly generate heat when they combust fuel or consume electric power respectively. Excessive generation of heat has damaging effects on machines and electronic devices because it causes expansion of thermo-sensitive materials leading to the reduction in performance. According to Zhang (2010), high temperatures reduce durability of machines and electronic devices because they are thermo-sensitive appliances. Moreover, low temperatures has negative effects because they cause contraction of thermo-sensitive materials that make up industrial equipment. In this view, there is a need to monitor and regulate the temperature of machines and electronic devices within the optimum range.
Description of the Project
The project aims to demonstrate the functioning of the digital temperature controller (Digital Controller Wh7016s), which has the ability to control the temperature of machine and electronic devices in industries. The control temperature of 80°F is appropriate for demonstration because it is within the range of room temperature. The digital controller comprises control system, sensor, heater, cooler, alarm, bulbs, and cables. The control system is an integral part of the digital controller because it receives signals from sensor and switches on or off the heater, the cooler, or the alarm, as illustrated by Figure 1.
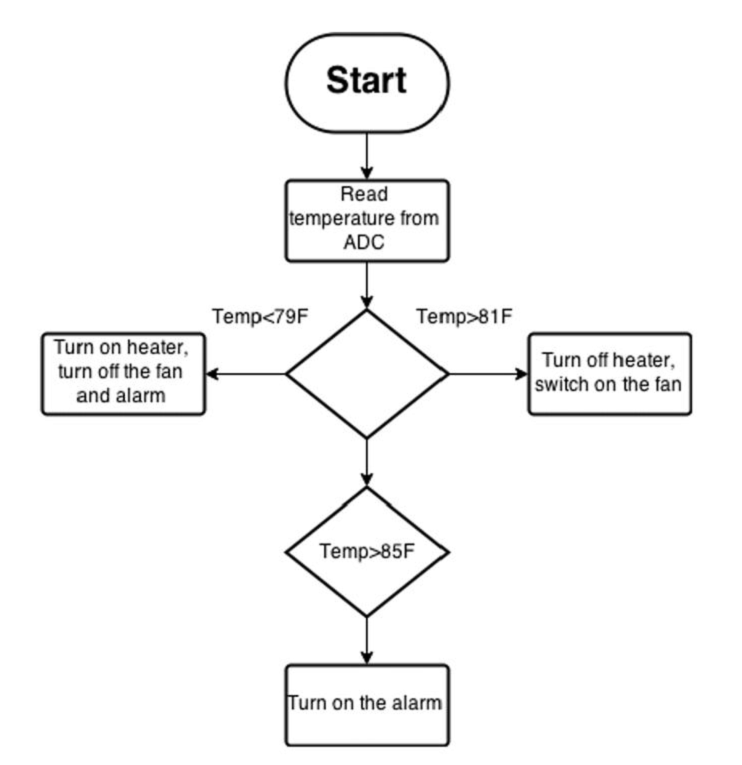
Implementation
Abstracting the Problem
High temperature in industries is a serious problem because it does not only reduce the performance of machines and electronic devices, but also predisposes them to breakdown. Machines and electronic devices operate optimally at room temperatures, which are about 72°F, and they last for a long period (Zhang, 2010). For cooling to be effective and efficient, a sensor is essential to regulate temperature at a desired range. On this basis, machines and electronic devices require stringent control of their temperatures at optimal ranges to enhance their performance and extend their durability.
Division of Tasks
Input, switch control, and output are three major tasks of digital controller. The sensor performs the input task by sensing temperature of machines and electronic devices, and relaying the appropriate digital signal to the control system. The sensor has data acquisition card, which transforms analogue signals of temperature into digital signals. The control system has a switch control, which construes the digital signal from the sensor and turns on the right switch as a response. The output task can be to turn on the heater, the alarm, or the cooler, when temperature goes above 81°F, above 85°F or below 79°F respectively.
Problems Faced
Since the digital controller is a three-relay system, connection of cables to respective devices, namely, the cooler, the heater, and the alarm was tricky. Moreover, connecting digital device to power was tricky because it requires connection of both AC power and AC/DC power. To set the digital controller to maintain temperature was difficult for it involved adjustments of the desired control temperature to 80°F, temperature difference to 1°F, and alarm limit to 85°F. Another problem faced was in selecting the site, where the sensor would accurately detect the temperature changes and relay relevant signal.
Sensor Selection
Identification of the Sensor Type
The type of sensor that is in the digital controller is thermistor. In temperature controllers, thermistor is the common type of sensor that is incorporated in thermostat to regulate temperature. The advantage of thermistor is that it has high resistance and is very sensitive to slight changes in temperature (Du, 2014). The high resistance is a property that makes thermistor sense a wide range of temperatures. Given that the digital controller aims to regulate temperature within the narrow range of 3°F between 79°F to 81°F, the sensitivity of thermistor enables it to detect slight changes in temperature. Therefore, thermistor is the appropriate type of sensor, which has the capacity to detect changes in temperature and relay relevant signals to the control system to effect temperature changes. The functionality of the control system is solely dependent on the sensitivity of thermistor and integrity of thermostat.
Performance Test of the Sensor
The digital controller was assembled by connecting the heater, the cooler, the alarm, the power, and the sensor to the control system. The bulbs and alarm are indicators, which depict functioning of the digital controller in different temperatures. In the digital controller, the control temperature at 80°F and the temperature control limits was set at 79°F and 81°F for lower and upper limits respectively. Additionally, the alarm limit was set at 85°F. The hand represented heating stimuli, while the cold water represented the cooling stimuli. To examine whether the sensor would trigger the heater, the sensor was placed in cold water in a beaker and the temperature dropped below 79°F and turned on the bulb, the heater, and alarm. Moreover, to examine if the sensor would trigger the cooler, the sensor was held by hand and the temperature rose above 81°F and turned on the bulb and the cooler. When the temperature rose beyond 85°F, the alarm gave a warning.
Measurement System Implementation
Hardware Configuration
Given that the digital controller consists of the control system, heater, cooler, sensor, bulbs, alarm, AC power, AC/DC power, and cables, hardware configuration was necessary. The first procedure involved the connection of the control system directly to AC power and indirectly to the AC/DC power via bulbs using five cables. The first cable connects control system to the heater, the second one to the cooler, the third one to the alarm, the fourth one to the AC/DC power, and the fifth one to the AC power. Each cable connected to the heater, the cooler, the alarm was connected to bulb, which indicates the connectivity of the control system. When the temperature went below 79°F, the bulb for the heater turned on and the alarm rang, whereas when the temperature went above 81°F, the bulb for cooler turned on and the fan started cooling. When the temperature increased beyond 85°F, the alarm gave a warning.
Software Configuration
For digital controller to regulate temperature of machines and electronic devices effectively, it required software configuration. Software configuration involved resetting the digital controller to allow entry of new settings to regulate the temperature at 80°F. The temperature control limit of the digital controller was set at 1°F, which is the difference value (d) of the control temperature. The difference value permits the digital controller to regulate the temperature between 79°F and 81°F, which are lower control limit and upper control limit respectively. At the lower control limit, the control system turns on the heater, while at the upper control limit, the control system turns on the heater (eBay Seller, 2014). In setting the alarm, the difference for upper alarm limit is 5°F and for the lower alarm limit is 1°F. In essence, the upper alarm limit becomes 85°F and the lower alarm limit becomes 79°F.
Conclusion
Machines and electronic devices in industries require temperature control because high and low temperatures affect their performance and longevity. Digital controller is a suitable temperature controller for it is a three-relay system, which permits connection of the heater, the cooler, and the alarm. The sensor used is very sensitive to slight changes in temperature, and thus, suitable for detecting changes in temperature by 1°F. The data acquisition card effectively translates the analogue signal from the thermistor into a digital signal, which the control system recognizes and makes respective changes on output devices, namely, the heater, the cooler, and alarm.
References
Du, W. (2014). Resistive, Capacitive, Inductive, and Magnetic Sensor Technologies. New York: CRC Press.
eBay Seller. (2014). AC 110V Fahrenheit 3 Relays Digital Temperature Controller Set up demo [Video File]. Web.
Zhang, P. (2010). Advanced industrial control technology. Amsterdam: William Andrew/Elsevier.