Summary
Littlefield Technologies is a factory that produces satellite system receivers composed of specific kits of elements. The process of assembling components and making the whole product includes four steps realized at three stations.
Problem Identification
Littlefield aims to maximize the revenues received during the product’s lifetime. To achieve the goal and maximize profits, it is important to resolve such a problem as the necessity to minimize lead time and queues and receive the customer contract with the highest level of payment.
Relevant Information
The first step in resolving the identified problem is the focus on such data as the utilization rates and queue rates. These data are important for forecasting the demand and for deciding on purchasing machines and strategies realized concerning setting up the reorder point and quantity. The average number of orders per day was determined to conclude about the demand. It was calculated that the average number of customer orders was approximately 11 orders per day (Figure 1). The demand was rather stable.
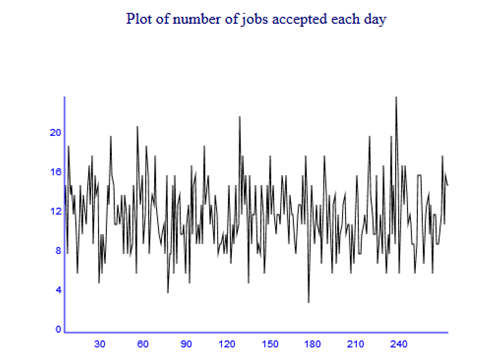
Solutions Developed
- Minimizing queues and purchasing machines. On the fiftieth day of the factory’s work history, Station 2 and Station 3 demonstrated about 100% utilization. If the utilization is nearly 100%, and the demand is increasing or stable, it is possible to decide on purchasing machines. Machines for Station 2 and Station 3 were purchased because of the rather high waiting inventory rate. It was important to identify the cause of the high waiting rate and addressed the problem. Thus, the machines for Station 2 and Station 3 were purchased during the fiftieth day, after deterring the demand and waiting rates.
- Addressing the order quantity. The second step was associated with addressing the order quantity. It is important to change the order quantity to the Economic Order Quantity (EOQ) to minimize not only inventory costs but also ordering costs. For the fifty-sixth day, the achieved reorder quantity was 23,160 kits.
- Choosing contracts. Thus, the team decided to change the current contract to Contract 3. As a result, it was necessary to purchase more machines for Station 1.
- Setting up the reorder point. Changes in the number of machines led to the necessity to set up the reorder point according to the formula dL + ss, where d = daily demand, L= lead time in days, and ss = safety stock. Thus, on the 133rd day, the reorder point was 3,000 kits.
- Necessary adjustments. Having analyzed the speed of getting more profits, the team decided to decrease the number of machines for Station 2, on which the main focus was made during the first days of the operations.
Changes in the numbers of machines at stations led to changes in the utilization rates, queues, and lead times (Figures 2-5). Figures 1 and 2 demonstrate the changes in the utilization rates for Stations 2 and 3 after purchasing machines. Figures 4 and 5 demonstrate the overall changes in the lead times and orders.
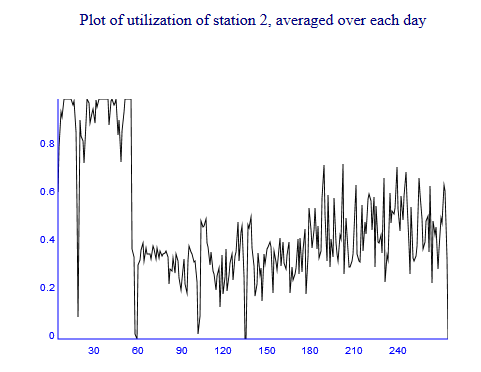
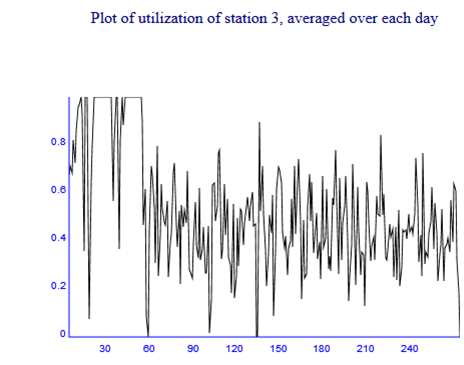
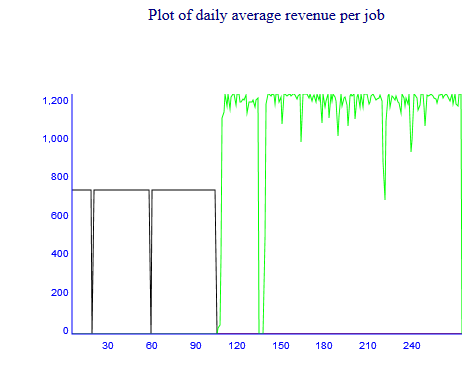
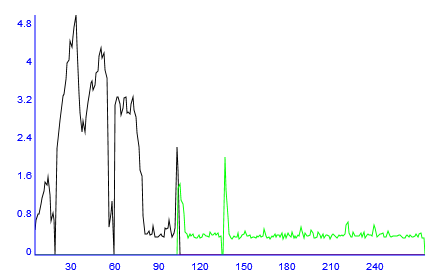
The decisions on purchasing machines at the first stages of the work and decisions of shifting to Contract 3 as the first change were not effective enough because of the associated risks (Appendix 1). Furthermore, the goal associated with minimizing the lead time was achieved through utilizing rather incorrect strategies.
Recommendations
The optimal strategy for Littlefield includes such steps:
- Having examined the utilization and queue rates for the station, it is important to examine the lead time and decide on purchasing machines to support the work at the concrete station. It is also important to set the reorder point rather high. None of these factors can be ignored while deciding on purchasing machines. It is important to manage the reorder point and Economic Order Quantity frequently, to control the process effectively.
- Much attention should be paid to the gradual change of contracts when all the requirements of the contract are followed. Decreased lead times identify the necessity to shift to Contract 2 because of 100% utilization and then to Contract 3 if the lead time numbers decrease. The demand should be stable, and the machine vacancy rate should be high.
Summary of Recommendations (Table)
Appendix 1. Transaction History
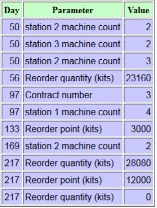