Background
One of seven comprising the United Arab Emirates, Dubai is no longer reliant solely on oil wealth since it has moved aggressively to transform itself into a financial services hub for the Middle East on a par with London, New York, Singapore and Hong Kong. Combined with a secondary thrust into high-profile sporting events, such a national development tack has necessitated large numbers of expatriate workers, in turn fuelling a real estate boom and road congestion. The need for a mass-transit system has also been spotlighted by the superb outcome of tourist marketing based on positioning Dubai as both convenient stopover and a shopping destination in itself.
The pressure on vehicles and road infrastructure would likely come from both the resident population, already the largest among all the emirates, and from continued robust growth in tourist numbers. Population in the middle of the decade stood at 1.5 million. On the back of 6.4% annual growth, this reached 2.26 million in 2008 and was projected to reach 5.5 million people by the year 2020. In turn, the influx of tourists was forecast to rise to no less than 15 million as early as 2010. By mid-2005, therefore, Dubai Municipality (also, the “Dubai state”) had finalized plans and resources for a railway system as the better way of easing traffic congestion.
Plans were laid to eventually construct four railway lines with a total of 57 stations. Groundwork began in early 2006 for the Red Line, with a planned length of 52.1 kilometres and 29 stations. By August that year, the government also awarded contracts for the Green Line, rather shorter at 17.6 kilometers (later upgraded to 23) and just 18 stations, but covering the highly important Airport and Healthcare City. Targeted completion was 2010 for both lines. It is testimony to the priority given this infrastructure project, however, that the Red Line commenced operation in September 2009 when ten stations had become operational. When complete, the Dubai Metro may be the longest completely automated (because driverless) mass transit system anywhere in the world, certainly a comfortable three kilometres longer than the previous record-holder, the Vancouver Skytrain.
This paper analyses the case of the Purchasing function within Serco Gulf, the operator that was to take over the built-up system in the first quarter of 2007. The analysis spans such key planning issues as stakeholder requirements, the cost and revenue outlook, structural and process matters within the department, supply chain management topics and a timeline for supporting the Dubai RTA goal of moving forward inauguration form 2010 to September 9, 2009.
Key Planning Issues
Stakeholders
The primary stakeholders of the Dubai Metro are government, employers both public and private, foreign direct investors, tourists, the commuting public, car owners, and freight service operators. Also involved, though perhaps neither avidly interested nor standing to benefit directly, are media, the rest of the United Arab Emirates, and environmentalists. (This last group is addressed in section II-B below.)
Government
For government, the Dubai Metro project is a showcase of economic development because mass transit has been proven over and over again as a rational solution to urbanization and the grievous inner-city congestion it brings. By itself, this fully-automated system is singular and bolsters the status and leadership of Dubai, not only within the UAE federation (the Metro is the first urban rail transit anywhere in the Arabian peninsula) but all over the Gulf and South Asia as a whole.
Since Dubai Metro is publicly-owned, the government of Sheikh Mohammed bin Rashid al Maktoum, via the Roads and Transport Authority (RTA), is also the sole stockholder. So far, the initial investment for engineering design and construction has already more than doubled from the initial estimate of AED 12.45 billion (US$ 3.4 billion) to AED 28 billion (US$ 7.6 billion) by the time the first Red Line segment opened in September this year. While the cost escalation was justified by significant scope and design alterations introduced by the RTA, sunk cost does negate revenue projections of AED 18 billion (US$ 4.9 billion) over the first ten years of the project.
This presents Serco with a dilemma:
- Adjust fares in order to realise an economic profit from operating the two lines?
- Or maintain the original policy of subsidising fares at affordable levels and derive operating profit from some combination of direct government subsidy, food concession fees and transit advertising?
The Riding Public
By sheer headcount, the 15 million tourists visiting the city annually are supremely important stakeholders since the free independent travellers (FIT’s) among them can be expected to value an efficient mode of getting around the city when sightseeing or shopping.
From day to day, of course, the resident population of employees without means is the single most vital stakeholder in the Dubai Metro project. Frequency of need/patronage is the critical determinant for this passenger segment. Which means that unreliable service caused by defective materials or shoddy suppliers will trigger the most complaints from this stakeholder class.
The Dubai Municipality Public Transport Department projected a passenger load factor of 27,000 per hour and an average of 1.2 million per day for the Red and Green Lines when the system is completely built. This is equivalent to 355 million passengers annually (Baxter 1).
Employers and Foreign Direct Investors
Both state-owned and private businesses stand to reap the most gains as stakeholders in the Dubai Metro. This is based, first of all, on the principle that all urban infrastructure is necessary for boosting commercial activity and hence, the economic diversification and growth of the emirate. More directly, the second benefit for present and prospective investors is that mass transit makes travel times more predictable, thus reducing tardiness among the carless rank and file and improving the predictability of courier times.
Thirdly, mass transit makes distant housing tracts a possibility now. This is necessary to decongest the city centre and suburbs, where apartments are already shared and which threaten to degenerate into crowded slums that may well be breeding places for urban crime. An orderly civic life is, of course, a prerequisite for a favourable business climate.
All in all, the active participation of shop owners, hotels and other businesses in ensuring that the project succeeds will boost their lives because it is an economic activity. All this will lead to sustainable economic development of the main urban center and satellite “cities” being developed all the time.
With increased gross domestic product and commercial activity, the government stands to earn more from import duties (up to 10%), a 5% residential tax on rental rates, and a 5% tax on hotel services and entertainment.
Expatriates, Sportsmen and the Dubai Upper Crust
Part of the promotional campaign touting Dubai as a regional hub has been sponsoring such events as the Dubai Sevens (Rugby), a Women’s Tennis Association tournament, golf events and regular horse racing. Such events naturally attract sports-minded expatriate workers, native Arabs and Emirati, as well as enthusiasts who fly in mainly to be spectators at high-profile events. All residents who own cars and visitors who avail of rental units naturally have a stake in the success of the Metro at decongesting the road system. And the carless sporting public will of course benefit from a reliable mass transit system that has stations near the event venues.
The Dubai Serco Organisation
The Hampshire, UK-based Serco Group plc earned the nod of the Dubai Municipality for being a highly diversified, £ 3.1 billion contract-service company that is not only publicly-listed but also derives over 90% of revenues from public service contracts. The sheer diversification of its business base – spanning defence, mass transport as In Dubai, outsourced or privatised local area government services such as prisons, health care, welfare and education to work, business process outsourcing, information and communications technology (ICT), nuclear and environmental services. If nothing else, such diversity protects Serco from business downturns in one or two market sectors pulling down bottom lines for the company. That turnover doubled from £ 1.6 billion in 2004 to £ 3.1 billion in 2008 (Serco Five-Year Summary 1) vividly demonstrates how a strategy of diversification ensures steady growth.
Besides the London Docklands project, Serco brings to the RTA contract in Dubai experience operating mass transit systems elsewhere in the UK, in Denmark and Australia.
Investment and Financing
Both the Finance and Purchasing functions of Serco Dubai are guided by the Serco Management System, the relevant core values of which are:
- Adhere to a business strategy that meets business objectives;
- Achieve the sustainability of the business;
In addition, the Finance function responds directly to the mandate to maintain sound systems of financial control to prudently protect value for shareholders and preserve assets that Serco manages in trust for its principals.
In March 2007, when the hypothetical time scale for this case commences, the RTA had a signed a ten-year, £ 795 million contract to operate and maintain the entire asset base of the Dubai Metro system: including trains, railways, and stations. Besides the basic transit service revenue, Serco Dubai Finance was to oversee cash flows from selling prepaid fare cards and operations to sell top-up or otherwise replenish stored-value Metro cards (Wray 1; Golden 1).
So far as operational costs are concerned, both Finance and Purchasing would have to concern themselves solely with running the Metro system for the first three years of the contract. The DURL consortium bore the responsibility for maintenance in the interim. Nonetheless, Finance ultimately bore the burden of seeing that the promise of cost-efficient operations, successful recruitment and training of the required personnel by a privatised Metro system would be realised so that the RTA could concentrate on legislation and regulatory oversight.
Cost and Revenue Projections
By the time DURL turns over maintenance to Serco Dubai, the total payroll would be 3,200 employees all told. But, as the following analysis strongly suggests, payroll is not the most significant component of project cost.
After engineering and technical design specifications were completed in early 2004, it was estimated that total construction cost for the Dubai Rail Project would come to AED 14.3 billion and that operating cost would run AED 570 million annually, the latter to be met from fares and advertising sales (Dubaifaqs.com 5). Over the ten-year period of the service contract, total cash flow would therefore be AED 5.7 billion or £948 million (at AED 6.01 = £ 1), ensuring a comfortable margin for the Serco £ 795 million contract to meet contingencies and cost inflation. That construction cost eventually rose to AED 27.9 billion for the Red and Green lines combined has no impact on the profitability of Serco Dubai since RTA absorbed all construction costs. In any case, DIFC chief economist Nasser Saidi had also estimated in early September 2009 that the Metro would, in just the first five years of operation, spin off some AED 17-28 billion in gains to employers owing to the aforementioned staff productivity gains (Dubaifaqs.com 5).
As of Fall 2009, the standard fare is AED 2.00 for travel within one zone, about 3 kilometres. This rises to AED 6.50 for travelling across five zones, the total length of the Red Line when launched in September. A one-day unlimited pass costs AED 14.00. Disabled and special-needs passengers ride free. The lowest level of prepaid, refillable plastic card, the Silver, retails for a 10% discount. “Gold Class” prepaid plastic cards cost at least AED 3.50 for the privilege of an unhampered view out the front of the (driverless) train, leather seats and carpeting.
Table 1: Dubai Metro Tariffs.
Such popular pricing bodes ill for projected Serco Dubai operating revenues. Project plans completed in 2006 forecast a daily average of 1.2 million passenger-trips and 355 million passenger-trips annually when both the Red and Green lines are completed. Owing chiefly to the limited number of stations on the Red Line thus far, passenger load factor and hence, revenue are running 95% below projections. And it remains doubtful whether all 29 stations of the Red Line will be in place by February 2010 and the follow-on 20 stations of the Green Line by end-2010 since the recession that spilled over from America throughout 2008 began to be felt in Dubai by mid-2009 (Baxter 1). It is likely, therefore, that the ambitious four-line plan will have to await the fallout from the Dubai World debt crisis.
Purchasing and the Corporate Structure
By the nature of the operation, the Dubai Metro organisation segments into Corporate on one hand and the Operating Divisions on the other. The latter embrace all the mechanical, front office and facilities upkeep functions (Serco 1). Thus, there is Engineering (for the rolling stock) separate from Maintenance and Cleaning. Customer Service subsumes all frontline matters and Security essentially prevents passengers from jumping the turnstiles while keeping a wary eye out for unforeseeable acts of terrorism.
Purchasing comes under Corporate, which comprises IT, HR, Finance and Marketing. While IT, HR and Finance are prosaic administrative services, the role of Marketing is to generate incremental revenue by selling outdoor advertising placements within the stations, at access and exit points, and accomplish the unusual merchandising opportunity of naming the stations for companies and brands that would like a high profile with the local commuter mix.
The Procurement Function
Purchasing: Structure within the Organisation
To define how Purchasing can become a strategic partner, it is necessary to situate its activities within the context of the Dubai Metro corporate mission, strategy and goals. This mission has to remain clear to all those in management and especially all employees asking the questions: “What is our business? Who is our customer? What is value to customer? What should our business be?” These are all questions that the company has presumably addressed in creating the strategic plan.
In brief, the corporate strategy of Dubai Metro rests on leveraging the competencies of Serco against the opportunities and constraints inherent in the marketplace that is Dubai. Technical competence of Serco is established by the fact of having operated the London Docklands Light Railway and by having won the competitive bidding for the first two lines in operation.
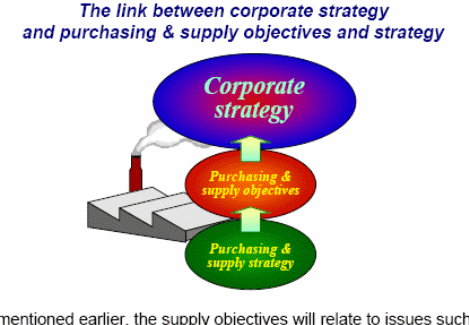
The job of formulating Dubai Metro strategy is made easier by the fact that competition is nonexistent (except from traditional, street-level public transport). As well, Serco essentially takes over operation and maintenance of a mass transit system for which the market need and demand can be taken for granted. Launching a mass transit system was a policy decision. The headcount of tourists and residents gives the starting numbers for evaluating demand. Whether the first two lines will be profitable at all is therefore a matter of judicious pricing. But then, economic theory assures us that a natural monopoly such as urban mass transit has great flexibility for pricing above all points on its average cost curve.
The company will examine the external environment and the internal environment before deciding on the best process to achieve its mission objectives. Metro business objectives and goals are to provide a good product at the best prices and to expand its market share while checking any unwanted expenses. This is then tied into the development and supervisors prepare programme plans and finally gather feedback while exercising control.
Among other matters, the Purchasing function must respond to customer satisfaction as the overriding goal of the company since commuter perceptions of the service is obviously vital to the sustainability of Dubai Metro. Concretely, this means that Purchasing must select suppliers for, and acquire, not only the high-technology traffic control system but also the spare parts and consumable maintenance stocks that would be needed within foreseeable mean-time-between-failure (MTBF) time scales and prudent maintenance schedules for the rolling stock. As well, it is essential that Purchasing contract for cleaning and maintenance subcontractors, including the upkeep of air conditioning systems at every station, and for installing security systems, given the always-imminent risk of vandalism and externally-induced ‘terrorist’ attack. Serco Dubai must also plan for acquiring sufficient stocks of one-off fare cards and self-service systems for topping off value-bearing cards. Finally, there is the matter of acquiring required stocks of food and beverage stocks for those ‘concessionaire’ stands that Serco wishes to operate in-house.
The ‘Greenfield Opportunity’
Having come in at the point of the operational turnover from DURL, the Serco Gulf Purchasing operation had an initially free hand in recruiting expertise wherever it could be found internationally (and let the future take care of “emiratization” or the mandatory proportion of staff that should be filled by natives of Dubai). In respect of logistics and inventory management (see section B-3 below), Purchasing could take advantage of the fluid state of the organisation initially to make a pitch for centralising all inventory management with the same functional group that acquired the parts and consumable supplies in the first place. In effect, Purchasing succeeded in having oversight of Materials Management and Inventory.
Thirdly, Purchasing took the initiative to define inventory as more than just rolling stock parts, lubricants or items on hand. Taking the cue from the experience of running municipal mass transit systems in the UK, Denmark and Australia, Purchasing could predict with reasonable confidence what the minimum annual usage volume and minimum dollar value was for every item. Logically, therefore, the Purchasing Department helps render the financial statements of Serco Gulf more accurate for reflecting the true worth of inventory.
Logistics
The process
After power cost and payroll, management of inventory costs holds out the promise of generating profits from the fixed-price contract during the anticipated period of revenue shortfalls. Such is the magnitude of this concern that the Dubai municipality was impelled to organize a task force counting three RTA managers – one from data processing system group, the second a chief engineer, and the third a profit centre controller – and to liaise with their counterparts from Serco Gulf Operations and Purchasing. The task force was asked to:
- Diagnose the inventory reduction opportunity;
- Develop a comprehensive program for reducing inventory; and,
- Implement the programme.
Diagnosing the problem
The first assignment was to assess what opportunity existed for inventory reduction and investigate how inventory could be reduced without curtailing service. The scientific inventory planning computer simulation model showed the top management a quantum opportunity existed. The size of the opportunity confirmed, the task force next investigated how to achieve the reduction. First it examined in depth the current operations scheduling and planning, parts and consumables inventory control and through interviews, the task force identified two key analytic tasks that would lead to inventory reduction.
- First task was to determine a better approach for managing and allocating inventory outlays.
- The second task was to find a better balance of cost of carrying inventory against the risk of shortages.
- The team constructed seven scientific models that addressed the two tasks.
At the end of the day, supply chain management in a mass transit operation is not only about selecting suppliers and ensuring proper logistics but also about inventory management. The Purchasing Department can only track the effectiveness of its operations if it recognises and tracks such benchmarks as number of material issues and receipts logged against those, stock-outs associated with unfilled orders and what proportion of the rolling stock has to be taken off the schedule (for lack of a vital part), backorders and inventory carrying costs. The latter can be especially critical since Transit Operations will nearly always opt to have a very large safety margin of parts and consumables on hand without acknowledging the carrying and opportunity costs these entail.
Accordingly, Purchasing organised Materials Management activities to cover this end to-end process and along the way, created a manual of operations:
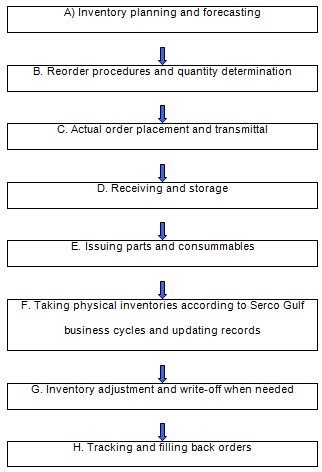
The overarching policy objective is obviously that of minimizing cost while maintaining very high, same-day service levels when Operations has need of parts and consumables.
Supply Strategy: The Goods and Services to be Purchased
When Serco Purchasing comes on board in January 1, 2007, it is assumed that all the subsurface structures (for the part of the line running through the city centre), the elevated viaducts (aboveground supports and railways for the rest of the line), ground level terminals, station shells, electrical substations that will power the electricity-conducting third rail line under the trains, and access facilities (stairs, escalators, elevators) will be turned over by the Japanese-Turk Dubai Rail Link consortium complete and in good, sturdy working order. Accordingly, Serco Purchasing must plan for the acquisition of the train cars themselves, for finishing the interiors of both train cars and the stops, for the control system that will enable driverless service, equipping the stations with all necessary amenities, and contracting outdoor advertising placements from ad agencies.
The very first task of Purchasing (and the critical path through the installation and pre-operational phases of the project) is then to source train fabrication and assembly from a supplier that:
- Is located in Asia or Europe so as to minimize the cost and elapsed time of shipping the units to Dubai;
- Has the capability for the number of cars required (see below);
- Can produce a pleasing bare-bones model and significantly different amenities for economy, regular and premium classes;
- Can do laboratory-accelerated tests equivalent to five years of continuous operation for mechanical reliability, hermetically tight air conditioning systems and resistance to high ambient temperatures that prevail in the dessert.
- Is willing to run extensive on-site test operations for each train before earning final approvals and project payments.
The number of trains that must be acquired is a factor of the intended speed, the length of the first two lines, the intervals between arriving trains that can be tolerated by planners and passengers.
In turn, the “consist” or composition of each train is a management and Finance decision. In all municipal mass transit rail systems around the globe, the minimum number of cars comprising each train seems to be three. This is the minimum that Serco Purchasing must plan for. The maximum cars per train is a function of decisions by Dubai Metro/RTA senior management and the finance department on maximizing revenue by implementing any number of fare classes.
To accommodate that variable-fare plan – a five-car train length seems most feasible because there will be two cars allocated to economy-level “Silver Class”, two exclusively for women and children, and one the premium “Gold Class” for expatriates and tourists – as well as physical dimensions roomy enough for between 600 to 700 standing and seated passengers, and absorb a probable peak commute time load of between 11,500 to 12,000 passengers per hour running both east and west, Purchasing must bid out at least 85 trains that will run on the Red and Green lines initially.
That number of trains is more modest than the initial estimate, based on theoretical system design capacity, of 106 trains bearing at least 25,000 passengers hourly at peak commute time. This is a compromise for safety, lengthening intervals between trains to 3 minutes and 45 seconds to permit a greater margin of safety in a driverless system. In other systems abroad with maximal signalling provisions and highly-trained drivers, waiting time can be reduced to as little as ninety seconds up to two-and-a-half minutes. Obviously, the negligible wait of 90 seconds optimises customer satisfaction during “rush hour” periods.
The second critical system component is that needed for optimally speedy but maximally safe train traffic and routing control system. Serco Purchasing must administer bids for a train control and supervisory control and data acquisition system (SCADA) with the optimal combination of length of zero-error operation, provision for running below the risky threshold of 100 kilometres per hour, primary and back-up modules, autonomous power supply (possibly even solar-powered solutions to take advantage of the eternally-sunny Gulf climate), and a self-tripping signal system skewed towards safety. It is likely that supplier evaluation will require both on-line conferencing and travel for the purpose of on-site inspection of installed systems. In any case, the process will start with the release of preliminary Requests for Information and Requests for Expression of Interest to such reputable suppliers as Siemens, Thales Rail, Invensys, Ansaldo, and General Railway Signal.
Given ambient humidity and extremely high summer temperatures in Dubai, Serco Purchasing should plan to finish station interiors with centralised air conditioning and suitable glass walls or air curtains at trackside.
By mid-2007 in the case scenario or seven months before the original scheduled start of operations, the Purchasing team in charge of passenger amenities and merchandising should swing into action. The Department can present to the RTA options for either operating internally or leasing to third parties station concessions for beverages, snacks or meals, newspapers and periodicals, tourist souvenirs, prepaid mobile phone credits and similar passenger conveniences.
At this time, given the cost overruns triggered by system design changes and the consequent likelihood that passenger-friendly fares alone will not enable Dubai Metro to generate positive cash flows over the long term, Purchasing will likely give priority to running the concessions internally. The drawbacks, of course, include increased marginal cost for staff and inventory, allocating storage space, and an increased workload for the Serco Audit team.
However, Purchasing can anticipate another source of marginal (but ongoing) revenue in the propensity of mass transit systems for accepting outdoor advertising systems. These are typically lighted signs running from a minimum of four-poster size to spectaculars quite as large as billboards that are common in city streets. Multiple signs can be accommodated in each station and even within the trains. Purchasing might even seriously explore the new-found opportunity of marketing station branding to prominent multinational makers of consumer goods that are sold in Dubai Duty-Free. For a minimal incremental cost of power (that can be generated by solar panels anyway) and maintenance, the Metro gains a dependable income stream.
The final significant pre-operating investment will consist of the disposable fare cards and intelligent terminals for reading them at ingress and exit points. The cards can be either the traditional magnetic strip type or the new contactless radio-frequency identification (RFID) cards, the latter permitting replenishment of stored values for residents who will use the system every day.
Otherwise Dubai Metro will purchase various goods and services that will be used for their activities. These goods and services range from food and beverage vending machines, ticket dispensers, main frame systems, software, electronic devices, furniture, monitoring equipment, metal and glass, escalators, elevators, conveyor, buses, security systems, access control and many others.
Supplier Issues
By capital cost, the two most important items in the system are the rolling stock itself and the train/central traffic control system itself. The relevant suppliers will already have been in place by the February 2007 starting point for this case analysis.
For the rolling stock, an initial order of 87 trains with a five-car consist (one for Gold Class, one for Women and Children, and three for Silver/Economy Class ticketholders) was already placed with Japan-based assembler Kinki Sharyo. When the Green Line is ready, the balance of the full order of 110 train sets will likely be placed. Reliability and timely delivery can be taken as givens since, aside from being supplier for Japan’s Shinkansen “bullet train” system and many others around the world, Kinki Sharyo has a flawless reputation for kaizen-based (continuous improvement) production processes and an unbroken record of on-time fulfilment. With delivery of the first train scheduled for March 2008, the Purchasing Department mainly has to wait 15 months, ensure the promised time scales are on track and train skilled workers to assemble the completely-knocked down trains on-site. These same skilled workers will leverage their experience with the car components to form the Maintenance teams when Dubai Metro is in full operation.
Just as critical for the operation of Dubai Metro is the SelTrac IS communications-based train control and NetTrac central control system to be provided by Paris-based and publicly-traded Thales Rail Signalling Solutions (Dubaifaqs.com 2). NetTrac can be programmed to run trains with as little as 90 seconds in between arrivals. However, this may not be practicable for a riding public that is unused to rapid ingress and egress from fast-paced municipal rapid transit systems. Hence, system pace on the Red Line will initially be set for 3 minutes and 45 seconds during rush hours and no less than 7 minutes at all other times of the day.
The SelTrac communication and control system to be installed is the top-of-the-line IS, a fully moving-block completely-automatic system. The IS links to each train via trackside, high bandwidth, open-standards wireless receptors compatible with either Ethernet IP IEEE 802.3 or radio wave IEEE 802.11 standards. Each wireless trackside antenna subsystem communicates to the onboard computers of passing trains to maintain separation between trains running in the same direction and serve unspecified security needs as well.
As soon as the viaducts, stations and rails are turned over in early 2007 and the power-link third rail has been electrified, Purchasing will notify Thales to commence installing the system in partnership with Serco Gulf Engineering. The supplier will have 13 months to accomplish the job and perform simulation runs before the first trains arrive and are ready for assembly in March 2008. From then on, the Project Management Department will have up to mid-2009 to test safety and reliability on every train as it is assembled. As to systems operators, diagnostic engineers and security technicians, these can be recruited from the London Docklands staff since this Serco-operated system employs the Thales network system too.
Such items that will be purchased by Dubai Metro will be intended to provide utterly reliable service. The work for Dubai Metro is to use various construction materials, including spare parts, replacement rails, ties, electrical systems, alarm systems and many other systems that are needed for the project.
Benchmarking The Supply Chain
The Global Supply Chain Forum (GSCF) describes Supply Chain Management as:
“Supply Chain Management is the integration of key business processes from end user through original suppliers that provide product, services and information that add value for customer and other stakeholders.”
In order to gauge the effectiveness and efficiency of key business processes it is important to measure their performance (Shepherd and Gunter, 2005). Measuring performance may provide an in-depth understanding of the supply chain, their characteristics and improve its overall performance (Chen and Paulraj, 2004). Performance measurement is defined as a process of quantifying the effectiveness and efficiency of action (Neely et al., 1995). Measuring performance is translating the complex reality of performance into a sequence of limited symbols that can be communicated and reproduced under similar circumstances (Lebas, 1995).
Beamon (1996) proposes few inherent characteristics for an effective performance measurement system. These are inclusiveness, universality, measurability and consistency. In order to measure the efficacy of a process it is important to benchmark the same. Benchmarking serves as an ideal tool for identifying improvement (Camp, 1989). There are large number of performance metrics available ranging from 13 to 60 (Huang and Keskar, 2006).
In view of such large numbers of performance measures, it is important to categorize them. Categorization helps the measures to be compared and analyzed so that performance measurement selection within a category can be easier (Beamon, 1999). Neely, et al., (1995) proposes 4 categories in his paper, including quality, time, flexibility and cost. Holmberg, (2000) argued that there should be synchronization between a measurement system and the overall objectives of the firm. Van Amstel and D’hert (1996) indicated that the performance measures depends on the level at which the measurement is done e.g. activity level, functional area level.
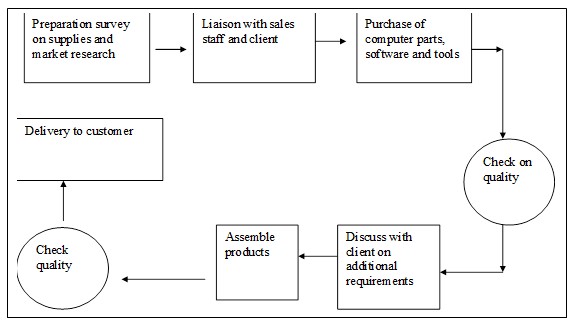
Process Issues
The process will be tested and analyzed with regard to time needed for completion, efficiency of each member of the team, the understanding of the job by both supervisors and workers and other criteria. Control is exercised at each step by setting up targets, providing a checklist and identifying weak points along the process. The feedback will be the basis of making any changes to the business objectives or to personnel. Information will also be shared with all other departments such as human resources, marketing, accounting and warehousing.
The external customer consists of the passengers, of course. A well defined process will guarantee that the Dubai Metro service is delivered trouble-free and in financially sustainable fashion for years to come.
Ultimately, the leadership of the Purchasing Department will demonstrate compliance with the mission, strategic goals and business aims of both Serco and the Roads and Transport Authority. The process described above, obviously participative in nature, will engender greater cohesiveness and commitment from the staff, thus preserving compliance with service levels to both internal and external customers. In turn, both leadership style and staff commitment will enable a smooth transition to total quality management and ISO accreditation further down the road.
E Process Issues
E processing has provided many benefits to businesses in the world. E-process has redefined the purchasing department and improved stock management in the organization. The Dubai Metro project will benefit greatly by implementing E processing within Purchasing, this enabling the organization to efficiently manage supplies procurement and inventory. At the very least, such a system should trigger alerts when, for instance, the stock of lubricants falls close to the safety level needed to maintain availability while replenishment stocks are in transit. Such resupply can be automated by giving key suppliers fully-encrypted electronic data interchange (EDI) links that give them visibility to Metro stocks in real time.
Supply Strategy and Supplier Relationship Management
The goal of ensuring continuous service and maximal customer satisfaction mandates tasks such as:
- Deciding whether to procure replacement parts from the original equipment manufacturer (OEM) for such rolling stock components as third-rail spring-loaded contacts, brake systems and the side windows that are subject to wear and tear from UV rays, mechanical brushes, cleaning chemicals, and vandalism.
- Or maximise cost-efficiency. Given the reduced-revenue outlook, the Purchasing organization at Serco Gulf may well take the route of writing detailed technical specifications and canvassing suppliers for reasonably good substitutes.
It is then possible to recap supply strategy as follows:
Supply Positioning Quadrant Analysis
Figure 5 (overleaf) is the initial presentation of Purchasing segregating benchmark items (not the entire inventory by any means) into the classic four zones. “Telematics”, for example, is an all-embracing term for the radio antennae and onboard computer receivers that constitute the backbone of the fully-automated and driverless Dubai Metro system. Positioned in the high priority zone on the upper right of the quadrant, this means that such equipment must be given the utmost attention. In terms of Supply Strategy, this is “critical” for being capable of halting mass transit operations. This is especially true because network backbones are not famous for being equipped in redundant fashion.
Adjacent to telematics are the fare and ticket vending equipment. These also deserve medium-to-high attention because a failure in the underlying software and communications links degrades the capacity to generate revenue. But if only a few turnstiles and vending machines fail, then this is a potential “bottleneck”. In time, there will be more suppliers for these since the spread of magnetic stripe and RFID technology has moved apace. Against this is the fact that initial investment is quite high but replacement expenditure is not since electronics technicians on the staff of Serco Gulf are routinely trained to restore intelligent terminals to “good as new” tolerances. Since there is little incentive for more fabricators to enter the field, this category of requirements also deserves fairly close attention.
By extension, all other items merit less attention to supplier management because replacement cost is low and the impact on sustainable operations is correspondingly low as one moves to the lower left quadrant of the model.
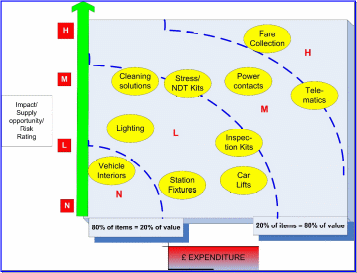
Corporate Social Responsibility Issues
Beyond relieving congestion on roads, the chief impact of a mass transit system is that it displaces public and private transport running on internal combustion engines. Hence, the Metro should deliver a measurable reduction in carbon dioxide and other emissions of gasoline- or diesel-fed vehicles. This was in fact cited by the Municipality Public Transportation Department which projected a 12% reduction in total man-trips when the system is fully operational (Baxter 1). Were this to be the sole contribution of the Metro to the community, it must count as significant since the US Department of Energy’s Carbon Dioxide Information Analysis Center (1) reports that the UAE ranks second in the world in per-capita emissions of carbon dioxide (32.8 metric tons per annum). Others in the top four are all in the Gulf: Qatar, Bahrain and Kuwait.
Time Scale Issues
The project will take a number of years to complete however the following shows the timeline of essential stages the Purchasing Department will be responsible for.
Works Cited
Baxter, Elsa. ‘Dubai Metro Lifts 1.7m Passengers in First Month.’’ ArabianBusiness. 2009. Web.
Beamon, B.M (1996) ‘Performance Measures in Supply Chain Management’, Proceedings of the 1996 Conference on Agile and Intelligent Manufacturing Systems, Rensselaer Polytechnic Institute, Troy, New York. Web.
Beamon, B.M (1998) ‘Supply Chain Design and Analysis: Models and Methods’, International Journal of Production Economics, 55, 281-294.
Benbasat, I, Goldstein, K.D and Mead, M (1987) ‘The Case Study Research Strategy in Studies of Information System’, MIS Quarterly, 11:3, 369-384.
Camp, R.C (1989) Benchmarking- The Search for Industry Best Practices that Lead to Superior Performance, ASQS Quality Press, Milwaukee, WI.
Chan, F.T.S (2003) ‘Performance Measurement in a Supply Chain’, International Journal of Advanced Manufacturing Technology, 21, 534-548.
Chen, I.J and Paulraj, A (2004) ‘Towards a Theory of Supply Chain Management: The Constructs and Measurements, Journal of Operations Management, 22, 119-150.
Chopra, S and Meindl, P (2001) Supply Chain Management: Strategy, Planning, and Operation, Prentice-Hall, Upper Saddle River, NJ.
Christopher, M (1992) Logistics and Supply Chain Management: Strategies for Reducing Cost and Improving Services, Pitman, London.
Dubaifaqs. “Dubai Metro.” 2009. Web.
Ellinger, A.E (2000) ‘Improving Marketing Logistics Cross Functional Collaboration in the Supply Chain’, Industrial Marketing Management, 29, 85-96
Golden, Lara Lynn. “RTA Signs 10-Year Agreement with Serco for Dubai Metro Operation and Maintenance.” 2008. AMEInfo. Web.
Gunasekaran, A and Ngai, E.W.T (2003) ‘The Successful Management of A Small Logistics Company’, International Journal of Physical Distribution & Logistics Management, 33:9, 825-835.
Gunasekaran, A, Patel,C and Tirtiroglu, E (2001) ‘Performance Measurement and Metrics In A Supply Chain Environment’, International Journal of Operations & Production Management, 21:102, 71-87.
Gunasekaran, A., Williams, H.J and Mcgaughey, R.E (2003) ’Performance Measurement and Costing System in New Enterprise’, Technovation, 25:5, 523-533.
Huang, S.H, Sheoran, S.K and Keskar, H (2005) ‘Computer-Assisted Supply Chain Configuration Based on Supply Chain Operations Reference Model (SCOR) Model’, Computers & Industrial Engineering, 48, 377-394.
Knemeyer, A.M and Murphy, P.R (2004) ‘Evaluating The Performance of Third-Party Logistics Arrangements: A Relationship Marketing Perspective’, Journal of Supply Chain Management, 40:1, 35-5.
Lebas, M.J (1995) ‘Performance Measurement and Performance Management’, International Journal of Production Economics, 41:1/3, 23-35.
Lambert, D.M and Pohlen, T.L (2001) ‘ Supply Chain Metrics’, International Journal of Logistics Management, 12:1, 1-19.
Mcginnis, M.A (1978) ‘Shipper Attitude towards Transportation Choice: A Factor Analytic Study’, International Journal of Physical Distribution & Material Management, 10:1, 25-34.
Neely, A, Gregory, M and Platts, K (1995) ‘Performance Measurement Systems Design: A Literature Review and Research Agenda’, International Journal of Operations & Production Management, 15:4, 80-116.
Rao, K, Young, R.R (1994) ‘Global Supply Chains: Factors Influencing Outsourcing of Logistics Functions’, International Journal of Physical Distribution & Logistics Management, 24:6, 11-19.
Serco. “Corporate Roles.” 2008. Web.
Serco. “Five-Year Summary.” 2009. Web.
Shepherd, C and Gunter, H (2005) ‘Measuring Supply Chain Performance: Current Research and Future Directions’, International Journal of Productivity and Performance Management, 55: ¾, 242-258.
Toni, A.D and Tonchia, S (2001) ‘Performance Measurement Systems: Models, Characteristics and Measures’, International Journal of Operations & Production Management, 21:1/2, 46-70.
US Department of Energy/Carbon Dioxide Information Analysis Center. ‘Carbon Dioxide Emissions per Capita.’ 2009. Web.
Wray, Lucy. “Serco’s US$795 million Dubai Metro Deal.” 2007. AutomoilSport, 1.