Introduction
This report is about strategic quality management and outlines how companies, such as Renault Corporation, could respond to their internal and external operational environments to successfully improve their quality management processes. It is based on the concept of Total Quality Management (TQM) which means the involvement of organisational stakeholders in continuous improvement to enhance the standards of producing goods and services (Nanda 2016). The purpose of this report is to demonstrate how Renault could adopt strategic quality management as a key tenet of its corporate strategy. However, before delving into these details, it is important to understand the company profile of the French-based automaker.
Company Profile
Renault is a French-based automobile company established in the late 1800s (ESSEC Business School 2015). The company produces different types of vehicles for commercial and individual use. Cars and vans are the main types of automobiles produced by the company. However, throughout its history, it has manufactured autorail vehicles, trucks, trucks, tanks and even buses (ESSEC Business School 2015).
According to estimates by Peng (2013), Renault is among the ten biggest automobile companies in the world. For a long time, the company has suffered declining revenues and reduced market share because of increased competition in the automobile industry (ESSEC Business School 2015). This poor performance made it seek a partnership with Nissan Motors of Japan to improve its profitability and save it from bankruptcy (Loska 2013).
In other words, the company could not stand on its own because of increased competition from dominant automobile companies, such as BMW and Mercedes, in its core European market. The same situation was evident in the global automobile market because of stiff competition from giant global car automakers, such as Toyota, Honda, and Mazda (Peng 2013). These dynamics have forced the company to rethink its business strategy. Consequently, there has been a new strategic focus on quality management, at the expense of cost advantages. Currently, the company is still struggling to develop a workable strategy to execute this corporate strategic change. This report provides suggestions to help the company implement this quality change in the organisation.
Role of Operations Management in an Organisation
Importance of Effective Operations Management in Achieving Organisational Objectives
According to Ansoff (2016), operations management refers to the processes of designing and controlling an organisation’s business processes to improve its productivity. Different organisations have unique operations management processes, depending on their goals and objectives. Hill, Schilling and Jones (2016) refer to these goals as strategic management objectives, which simply mean the highest goals of an organisation. The strategic management objectives of Renault Corporation are to:
- Increase its market share.
- Increase its profitability.
- Improve its brand image.
- Get ISO 9001: 2015 certification.
The importance of effective organisational management in achieving the above-mentioned objectives includes:
- Cost reduction.
- Increased operational flexibility.
- Improvements in innovation.
- Quality control.
The Success of Existing Operations Management Processes in Meeting the Organisation’s Overall Strategic Management Objectives
Based on the core operational management processes of Renault, I have identified the inputs, processes, and outputs that are central to the organisation. They include
- Inputs: The main inputs used by Renault in the manufacture of its cars include aluminium, steel, plastics, and glass (they are standard throughout the industry) (ESSEC Business School 2015). These are the tangible products involved in the company’s operations management process. The main intangible input in the organisation’s business process is technical expertise (Loska 2013). However, it is only applicable in complex production processes because most of the manufacturing line processes are automated.
- Outputs: By developing its cars and providing technical services to other car manufacturers around Europe, Renault’s outputs include satisfied customers, improved product quality, and increased market share (Peng 2013).
Resources: Most of the resources available to Renault come from its partnership with Nissan Corporation. This is because the company has been striving to improve its key competencies by exploiting some of Nissan’s operational advantages (Loska 2013). Since 1999, when this partnership occurred, Renault has enjoyed vital resources in its quality management processes, such as shared warehouses for Nissan and Renault, containers, shipping crates, sea-going vessels, and customs-related processing (Loska 2013). Other resources available include technical expertise and research and development facilities from Nissan.
Importance of Managing Quality in the Organisation
Explain the Importance of Effective Quality Management in Achieving Organisational Objectives
According to Chang (2016), organisations should participate in continuous planning and strategic quality change, regardless of their line of business, or ownership structures. The same is true for Renault. However, each quality objective of the company should be tied up with a strategic goal to have a real impact on the organisation’s growth and place in the market. Nonetheless, the company’s strategic plans rarely mirror the quality objectives of the company. This is the main disconnect in TQM within the organisation. This gap exists despite the quality management processes in the organisation (outlined below).
Success of Existing Quality Management Processes in Meeting the Organisation’s Overall Strategic Management Objectives
Renault has several quality management processes borrowed from its partner Nissan. They appear below.
ANPQP
Renault acknowledges that each component sourced from its suppliers represents a key output metric in its operations management process. Consequently, the company has established key quality controls to make sure its operations align with its corporate goals. The company has used many resources to establish stringent controls on its most complex operational processes because they are key areas of organisational weakness (Loska 2013).
These complex manufacturing processes include planning and development validation, performance testing, and transforming blueprints into prototypes. To maintain high operational standards, the company ensures that its suppliers meet stringent quality controls outlined in the ANPQP (Alliance New Product Quality Procedure) system, which is designed to procure precision-built inputs for production (Nissan Corporation 2016).
This system requires the company’s technicians to conduct quality tests on every component procured from the suppliers. This test can cover up to 387 quality assurance criteria (Nissan Corporation 2016). More complex components require more critical involvement of the company’s technicians to make sure it meets the required standards. Broadly, the ANPQP is based on the ISO/TS 16949 standard, which outlines quality requirements for automobile parts (Nissan Corporation 2016). The ANPQP system traverses across different operations management processes for the company. The diagram below shows its placement in the company’s operations management processes
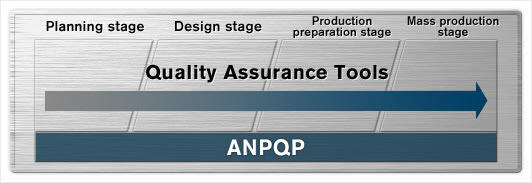
ASES
Renault also uses the ASES control to rate some of its components as either being “flawless” or “defective.” This system contains 240 evaluation criteria (Nissan Corporation 2016). Its usefulness emerges in helping the company to identify problems early in the manufacturing process. Specially trained evaluators, who is trained to oversee this process are the only ones mandated to participate in this process. This system largely allows Renault to ensure the quality of its sourced components.
Periodic Inspection of Suppliers: Renault also carries out periodic inspections of its suppliers to make sure that they adhere to the company‘s quality standards. To do so, the company maintains a supplier scorecard that contains different quality metrics, such as market quality (Loska 2013). The inspections are not limited to the products supplied only; the company also periodically carries out inspections of the suppliers’ factories through the Alliance Supplier Audit Standard in Production system or ASAS-P. This system contains 170 items for quality review and is meant to analyse the quality control processes of the company (Loska 2013).
Renault has a lot of faith in this system, as is pointed out by its managers who say, “These two periodic inspections ensure our suppliers adhere to a system that consistently delivers superior components, and drive our suppliers to continually improve on quality” (Nissan Corporation 2016, p. 7). The diagram below shows a sample of the supplier scorecard that Renault uses.
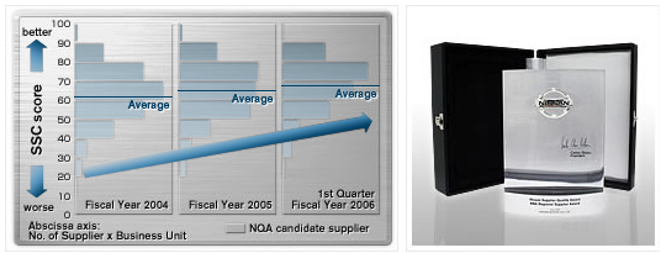
Throughout the years, Renault has issued a supplier scorecard (annually) and ranked them according to the best and worst performers. The best performers always get a reward at the end of every year. Overall, these quality controls have only managed to partially help the company meet its strategic and quality objectives. The table below shows an assessment of the strengths, weaknesses, opportunities, and threats of the company quality management process.
Table 1: SWOT Analysis.
Fishbone: We used the Fishbone (Ishikawaa) strategic management tool to analyse the Renault’s operational weaknesses. They appear below
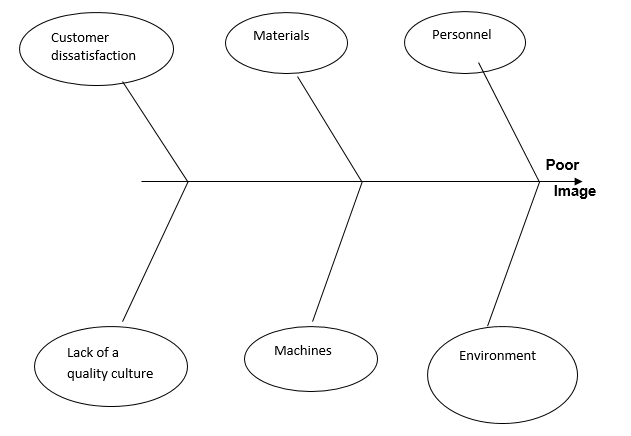
Causes
As described above, poor customer satisfaction standards, poor quality materials and untrained personnel are some of the weaknesses of Renault’s quality management system. These issues are further compounded by the lack of a quality culture, poor machines, and a cut-throat business environment. The implication is that the existing controls and resources available to the organisation could only partly help it to meet its objectives.
Planning a Strategic Quality Change in the Organisation
Plan a Strategic Quality Change to Improve Organisational Performance
The proposed strategic quality plan for Renault will have seven steps that include the following:
- Step 1 – Clarify mission, vision, and values: Renault should make sure that all its employees understand that their actions are tied to quality initiatives in the organisation, which ultimately lead to the realisation of organisational goals. To make sure that the employees do what is required, they need to understand where the organisation is headed (vision), how it intends to get there and what it intends to accomplish (mission).
- Step 2: Identify Critical Success Factors: Identifying the critical success factors would enable the company to understand those drivers that would help it to accomplish its strategic goals.
- Step 3: Develop Measures to Track Data: Renault needs to have an instrument for tracking its progress in quality management. The company could use the scorecard technique to collect specified data about the quality management process.
- Step 4: Identify Key Customer Groups: Renault needs to identify its core customers so that it can tailor its quality initiatives to align with the needs of its customers. The company also needs to recognise that its employees form a key customer group because they need their buy-in to implement the quality initiatives (Hill, Schilling & Jones 2016).
- Step 5: Solicit Customer Feedback: Renault needs to start a customer focus group to get feedback from its clients regarding its quality initiatives. According to Harrington (2016), most companies fail to do this because they believe they know what customers want. Usually, they are wrong.
- Step 6 – Develop Improvement Plan: Renault should develop an improvement plan, based on the information it has received from the customer focus groups. The improvement plan should have a SMART goals framework.
- Step 7 – Monitoring: It is important for Renault to monitor its quality initiatives to make sure that they align with the organisation’s goals. This process should allow the company to make corrections on its strategic focus in case its goals, or focus, shift.
Define Resources, Tools and Systems to Support Business Processes in a Strategic Quality Change
Realising strategic quality change in Renault would require the organisation to mobilise its resources, tools, and available systems. The required resources appear below:
Technology
The automobile industry is largely a technology-intensive industry. If Renault wants to meet its quality objectives, it needs to innovate and develop industry-leading technology to be ahead of the pack.
Workers
Some elements of Renault’s quality management plan require skilled labour to execute. This is an important resource for the company because it needs to get the right skill-set for quality managers to lead the quality initiative in the organisation (Harrington 2016).
Training and development
Although we have emphasised the importance of having a dedicated management team to spearhead quality initiatives in an organisation, Renault needs to invest in training and development of lower level employees to acclimate themselves with the new quality management plan.
Evaluate the Wider Implications of Planned Strategic Quality Change in the Organisation
The planned strategic quality change at Renault would have far-reaching implications for the company because it could potentially revolutionise its business model. For example, it could lead to the delivery of high levels of service and the production of high quality products, which would improve the company’s image in the automobile industry. In turn, the company would benefit from increased customer loyalty because they would be attracted to the improved quality of its cars.
Design Systems to Monitor the Implementation of a Strategic Quality Change in an Organisation
As mentioned in this report, designing systems to monitor the implementation of a strategic quality management change at Renault is an important step in the quality management process of the company. There are several considerations to make when designing systems to monitor the implementation process. One of them is having a provision for monitoring customer complaints. The complaints should be properly documented to understand quality trends. The monitoring process should also have provisions for after-sales service calls, a compliment monitoring system, and a provision for monitoring repeat customers (Harrington 2016).
Implementing a Strategic Quality Change in the Organisation
Implement a Strategic Quality Change in the Organisation
Implementing strategic quality change at Renault would require the adoption of benchmarking as a management tool. Researchers refer to this method as a strategic process of identifying best practices in a highly competitive industry, such as the automotive industry that Renault operates in (Ansoff 2016).
Embedding a Quality Culture in the Organisation to Ensure Continuous Monitoring and Development
Executive Participation: For a long time, Renault has professed to respect a culture of quality in the organisation. However, there has always been a gap between what the executives say and what is actually implemented on the ground. Consequently, employees have always got a mixed signal regarding the importance of quality in the organisation (Loska 2013). The company’s leadership needs to be more hands-on in making sure that they nurture a culture of quality in the organisation. In other words, they need to show enthusiasm and commitment to the concept because without it, they are only playing lip service to the company’s stakeholders.
Ensuring Message Credibility: Renault has always tried to communicate a message of quality throughout all of the organisation’s departments. This message has always been tailored towards letting the employees know that the company is serious about quality issues (Peng 2013). However, the main problem has been the failure of employees to believe it. Renault’s managers need to test its messaging strategy with employees, regularly, to make sure that they resonate with it. Similarly, they need to refresh this message over time and use the feedback they get from the employees to sustain the quality processes.
Increase Employee Ownership and Empowerment: Renault needs to communicate to its employees the importance of having a quality culture. They need to do so by stipulating rules and guidelines about the same. By doing so, they will empower employees to recognise quality issues that fall outside the parameters of quality management in the organisation. Consequently, they would easily identify their root causes and corrective actions.
Relative to this suggestion, Stamatis (2016) says that the actions that would force a company to shift from a rule-based quality management system to one spearheaded by a quality culture would vary according to the company. Nonetheless, empowering employees to identify quality areas that fall outside the stipulated guidelines would increase their ownership in the process and empower them to promote the quality culture in the organisation.
Monitoring the Implementation of the Strategic Quality Change In the Organisation
When Renault develops a culture of quality leadership in the organisation, all employees (from people in leadership positions to bottom-level staff) would have to infuse quality initiatives into their work processes. Nurturing a quality culture is the first step of creating this culture. Monitoring the implementation of strategic quality change is another aspect of quality management that Renault needs to focus on.
To do so, we propose that the company starts a continuous process improvement process, which would not only help to identify the root causes of quality problems, but also contribute towards eliminating them. Generally, this step would involve making small and gradual improvements in quality management to reduce variances and redundancies in the process. To do so, we propose the use of the six-sigma method.
Be able to evaluate The Outcomes of a Strategic Quality Change in an Organisation
Evaluating the Outcomes of the Strategic Quality Change in the Organisation
Strategic quality change is needed at Renault to improve the organisation’s efficiency and eliminate areas of wastage that would compromise the desired quality. It is helpful for Renault to better manage its resources and promote cost-effectiveness and to compete favourably with other global automakers, such as Honda and Toyota. Overall, the outcomes of the strategic quality change in the organisation should assist the French-based automaker to improve its competitiveness and achieve sustainability.
Areas for Improvement to the Strategic Quality Change that Align With the Organisational Objectives
In this section of the paper, I propose the use of the balanced scorecard technique to make sure that all departments of the organisation work towards achieving its TQM goals. The balanced scorecard technique would help to merge the organisation’s internal processes with its vision and strategy (Nanda 2016). Conversely, it would help Renault to improve its internal and external communication systems and support the coordination of departmental activities for the overall realization of organisational goals. Using this tool, I have identified two controls and resources for further evaluation. They include:
- Controls: Periodic inspections and ANPQP.
- Resources: Technology and employees.
Conclusion
To close the quality gap that exists in Renault, there is a need to implement small, but incremental changes in the company’s operations management processes. Bigger changes would be expected in the long-term, when there would be a complete redesigning of its operations. In the near-term, incremental changes should be tailored towards changing the decision-making process in the organisation and bridge the gap between the overall business strategy of the company and the organisational culture.
Reference List
Ansoff, I 2016, Strategic management, Springer, New York.
Chang, J 2016, Business process management systems: Strategy and Implementation, CRC Press, New York.
ESSEC Business School 2015, Experiencing innovation in Asia: Cases in business model development, World Scientific, New York.
Harrington, J 2016, Performance Acceleration Management (PAM): Rapid improvement to your key performance drivers, CRC Press, New York.
Hill, C, Schilling, M & Jones, G 2016, Strategic management: Theory & cases an integrated approach, Cengage Learning, London.
Loska, T 2013, Strategic alliances: The Renault & Nissan alliance – celebrating 10 years of synergies, GRIN Verlag, London.
Nanda, V 2016, Quality management system handbook for product development Companies, CRC Press, New York.
Nissan Corporation 2016, Quality initiatives. Web.
Peng. M 2013, Global strategy, Cengage Learning, London.
Stamatis, D 2016, 10 Essentials for high performance quality in the 21st century, CRC Press, New York.