Introduction
The principles of solid mechanics, which are generally applied for construction of rotating components generally entail the consideration of several aspects, such as possible loads, the mass of the construction, torque, friction powers as well as solidity of the material.
The aim of the paper is to design the two main components of the system, which are CHS (Cylinder Head Sector) and RHS (Rectangular Hollow Section). The key task is to calculate the suitable length of the sections, and consider the stresses, which will be applicable to each component. Then, the connection details proposed tension rods should be discussed.
Components Design
First, RHS component should be designed. The initial data entail the loads, which the component will be subjected to. In fact, the length of the RHS component in general will correspond to the rule of levers, as the loads are not equal, the length of l1 and l2 components will differ. Thus, the actual length will be proportional to the loads. In accordance with the lever equation
i = F1 / F2 = D2 / D1
Thus, the length of the RHS levers will be 10kN / 6 Kn = 0,6m / 1m
The material, which will be used for this component is Grade 350 Steel
Thus, pressure, which will be the top for this element will be 350 kg/m2 in the case of uniform allocation of the loads. However, considering the bending stress of the RHS element, and the sizes of CHS, the loads will be mainly concentrated in the place of RHS and CHS contact, and the square of the contiguity will be the defining moment of the maximum loads calculation. 6 and 10 KN (16 000 kg*m/s2) are the forces, which will be applied, and the maximum pressure will be calculated considering the maximum loads, applicable for the steel, which will be used for the construction. Thus, the minimal square of the RHS contact surface should be close to 0,000045 m2 in order the loads were maximum. (1,6m X 0,000028m)
As for CHS, the sizes are defined, and the stiffness will be calculated on the basis of the loads applied. Thus, the stated load is 16 KN, and the square of the RHS surface is defined. The square of the rod surface will define the max loads, and the sizes and physical characteristics of the rod. It will be created of Grade 250 mild steel. The width of the contact surface should be 0,000064 m2 for the loads were maximum. Thus, the required rod will be 21,9 mm X 4,8 CHS. The external surface area will be sufficient for the equal allocation of the loads along the entire construction. Considering the fact, that rod steel is milder, in comparison with RHS steel, the loads should be allocated with better accuracy, as the bent loads of the rod (CHS) will cause the bent deformation, if not applied properly.
The vertical deflection of the rod will be -0.57 m. Thus, the total loads will not cause the essential deformation and deflection of the rod, as these are allocated equally along the surface of projected RHS. Consequently, the actual importance of deflection rate will be closely associated with the mildness of the steel used for the construction.
Connection Details
The connection type of the construction details will be calculated considering the possible friction powers and the deflection rates, which will affect the entire construction. The nominal shear strength of the required connection type (including connection plates) will be calculated n accordance with the following formula
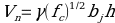
Whereas
- Vn is the nominal shear stress
- γ – is the fracture of unbalanced moment
- bj – average dimension
- h – overall thickness
Thus, the calculation will be as follows
34138,72 = 1 * (27)½ 30 * 0.219
34 kN is the nominal stress for the junctions of the construction, and the total value of dimension of the joint is acceptable.
The required steel area is derived as follows:
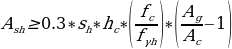
Whereas:
- Ash – total cross-sectional area
- sh – spacing index of reinforcement
- hc – cross-sectional dimension index of column core
- Ag – gross area
- Ac – cross-sectional area of the structural member
- fyh – yield strength of shear reinforcement
The actual value of the cross sectional area, required for the calculation of pin diameter will depend on the matters of bending stresses, which will affect the entire construction. However, the stated range of plates, which should be between 3 and 10 mm will be calculated basing on the torque, applied for the connection.
The plate diameter will affect the bending angle of the construction, when the perpendicular force is applied towards the junction. Considering the fact, that force of such vector has small likelihood, the diameter of the plate and the junction pin will be proportionate to the size of size of DE element, and the loads, which will be applied towards it. The plates will not be subjected to deformation, however the bending rate and welding process will require the increased diameter of the pin, for smoother spinning around the pin.
In fact, when the external force is applied to the connection place (as in the case with plates and pins), the force in the pin will increase. Simultaneously, the rod will be subjected to increased elongation, as well as the plates will be equally decreased (proportionally to the rod elongation). Consequently, the force of the plate assembly should be decreased in order to avoid increased friction. The value of the force, which will be transmitted through the pins by increasing the spinning force, generally depends on the behavior of the connection and the construction in general, which is defined by the mildness and elasticity of the steel, used for construction assembly. Considering the fact that the elasticity rate is different for various components of the construction, the connection calculation should be based on possible fatigue rates.
The parts should be connected with preloaded pins for increasing the fatigue durability of the construction. Thus, while the torque forces will be measured considering the pressure of the applied forces, the protection of the junctions by leaving the increased pinhole diameters will define the necessary precaution for assuming the additional stress forces, which will be originated by the environment.
Conclusion
The calculation of the forces, applied to the rotating components in engineering constructions requires the particular and thorough consideration of the applied stress factors and the torque forces, which affect the construction. In fact, the actual values of these forces are defined by the initial loads of 10 and 6 kN, applied for the RHS component. Then, these forces are affecting the CHS component, as well as the junction pins and plates.