Problem Description
This design proposal prototype will adopt the Howe truss bridge since it is one of the most structurally sound bridge designs. Truss bridges have considerably more triangular designs than other bridge types, such as beam and arch bridges, which aid in weight distribution. Truss bridges integrate triangular and symmetrical shapes, such as squares, to create a bridge with a robust structural design.
The bridge is intended to distribute loads uniformly across the structure, preventing rapid failure due to a concentrated force. A comparatively lightweight bridge can withstand a substantial load if properly engineered. A triangle is the best shape because it distributes weight and is far more stable than a basic rectangular or squared structure (English & King, 2019). The materials used and how they will be utilized determine the stability, durability, and balance of the bridge.
Background
The truss bridge is a design that leverages the stability and weight distribution that triangles naturally possess. When wooden triangles are linked, stress is evenly distributed across the entire bridge. As a result, the truss bridge can withstand tremendous loads without breaking. Non-uniform outside forces, such as wind and traffic vibrations, are equally evenly dispersed across the structure, allowing the bridge to endure these forces (Harris, 2021).
There are various advantages to using a Truss bridge. Builders can achieve maximum material economy because the truss bridge can hold weight. Because of its design, the structure can readily cover long distances. Furthermore, by constructing a truss bridge, builders can save money on pricey materials. Similarly, if necessary, the structure is conveniently accessible for maintenance.
Design
The truss is the most vital structural component, and its primary purpose is to disperse applied pressures across the system, minimizing the amount of stress that might develop in a particular region. High-pressure areas develop without a truss to provide this necessary distribution, resulting in premature structural failure. Gravity is a major force influencing bridges since it is always tugging on the bridge, and the bridge deck spans free space, which provides no resistance to gravity.
Larger bridges that cover longer distances are more vulnerable to shorter and heavier bridges. There are two other factors to consider when dealing with gravity on bridges: compression forces and tension forces. Compression compacts or shortens the material it operates on, whereas tension stretches or extends the object it is acting upon. The bridge will have compression at the top and tension at the bottom. The design will use a total of 150 popsicle sticks, as illustrated in Figure 2.
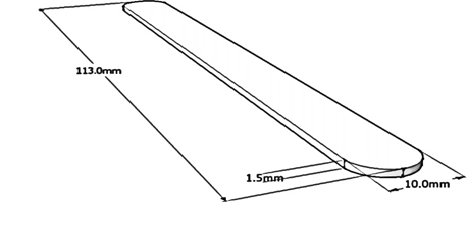
Materials
- 150 wooden Popsicle Sticks
- Multipurpose white glue
- Meter Stick
Constraints: Certain limitations will be observed in this proposal, as detailed in the accompanying specifications. The only materials permitted for the bridge construction will be:
- White multi-purpose adhesive to hold bridge elements together
- Bridge components must be made using 150 wooden popsicle sticks.
The bridge’s maximum weight must not exceed 120 grams, and its dimensions must be 55mm broad and 60mm high. The Howe Truss bridge design will be effective since the diagonal and vertical members distribute forces across the whole structure. It puts tension on regions of the bridge that can handle the stresses and relieves strain on weaker areas. Furthermore, the bridge will meet the 500mm length requirement because the truss can cross long distances.
The Construction Process
- Construction started immediately, with a model blueprint created to ensure the consistent assembly of both truss faces. Each member was fastened with binder clamps to ensure firm adherence, and hairdryers were utilized to speed up the drying process.
- The faces of the prototype were temporarily attached while the top road was bonded after the construction of both sides of the bridge.
- The final product was weighed and allowed to be set after all of the members had been assembled. Because the bridge weighed less than the maximum, more members were added to reinforce potential weak places until the maximum weight was achieved.
Limitations, Hazards, and Risks to the Design
Several issues emerged during the process of coming up with the proposal that may have an impact on the overall intended performance. The lack of forethought resulted in an unbalanced plan, with different angles of the diagonals on either side of the truss. The process of coming up with the proposal for the project offered several lessons in the engineering design process and the value of cooperation and member accountability. The creation and overcoming of problems were thrilling and fulfilling. Having the ability to apply principles learned over the course gave us insight into our potential engineering careers.
The Proposed Prototype
Figure 2 illustrates the design proposal for the popsicle bridge, and the proposed final bridge is illustrated in Figure 3, with the representation of the dimensions and angles of its structural members.
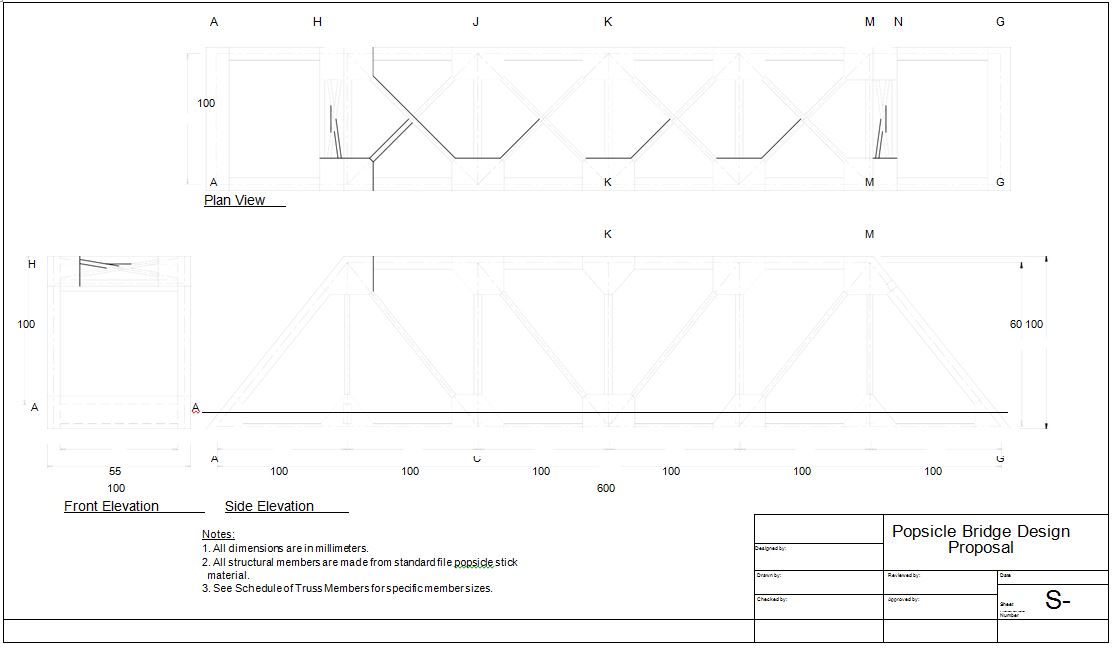
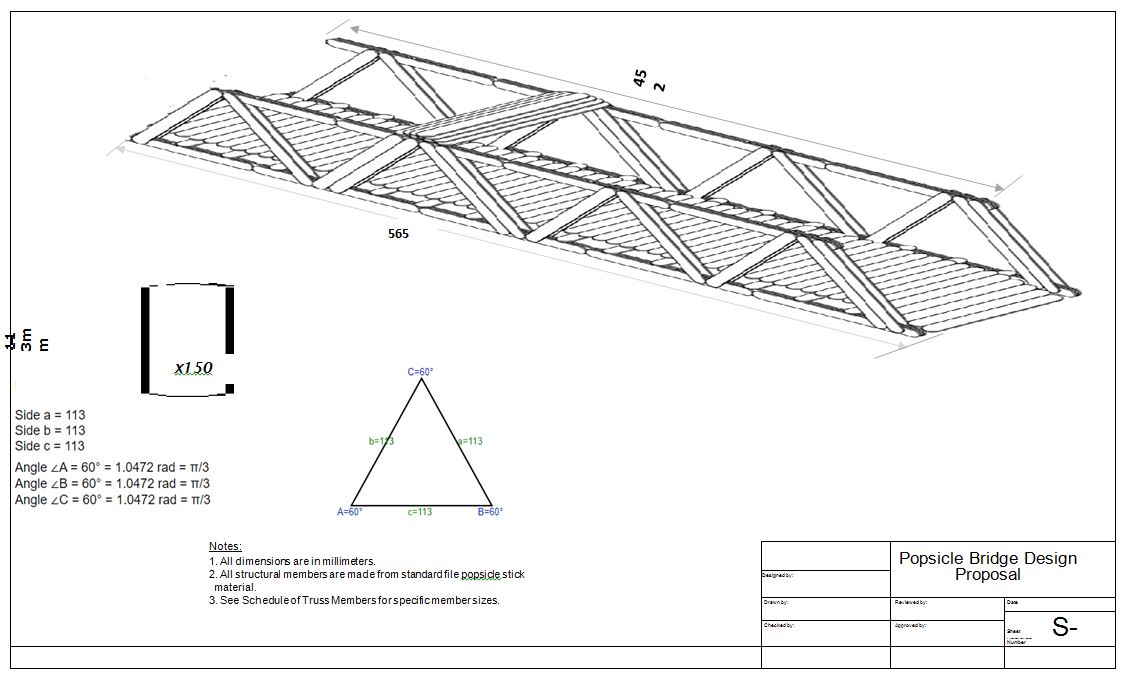
References
English, L. D., & King, D. (2019). STEM integration in sixth grade: Designing and constructing paper bridges. International Journal of Science and Mathematics Education, 17, 863-884. Web.
Harris, A. (2021). Balsa Wood Bridge. Central Washington University. Web.