Introduction
Today the need for warehouse design has become significant to any company with increasing use of warehouses. The activities happening in warehouses have also intensified making it difficult to come up with an efficient warehouse design. This has even led to the emergency of warehouse design and layout consultancy firms.
This is because of increased need for space, rising operating and labor costs, as well as decrease in order cycle time. The purpose of warehouses has also changed from long time storage to just in time deliveries. This has lead to the change in complexity of warehouse designs.
A warehouse is designed to store goods safely for a while after which they are transported to their respective destinations. When designing a warehouse one has to consider mainly location, space, information, time, as well as cost. Today the purpose of warehouses has changed as compared to the 20th century. This is because today there are fewer inventories within warehouses but the need for larger assembly areas, larger picking areas; many pick slots, and less backup stock.
In designing a warehouse, the perfect balance for appropriate space, location, time, labor, and safety must be achieved. Therefore the design should be able to deliver the required storage space today and in the future. The design should also provide safety of products and ensure health of workers. The design should also be able to provide faster loading and off-loading of goods. Thus, while designing a warehouse all these factors should be considered.
Location
In designing a warehouse location is one of the major factors to consider. This helps to ensure that the warehouse meets needs of the company’s main source of business. The location of the warehouse must also be in a position to promote a design that offers easy and quick transportation means. This implies that a warehouse location should provide for easy access to roads, ports, and other means of transportation (Harrington, 2007)
Therefore before a company goes ahead and sets up a warehouse it must carry out an analysis of the requirements and operations of the warehouse. After such an analysis, the company is able to design operational processes that go hand in hand with the business needs of the company.
The company will then sets up a warehouse at a location which will allow smooth and easy flow of operations. This will enable the company to have an operating-low-cost supply chain. In designing the location, the company must also consider having a network which provides a high-service. This implies that the warehouse should be in a position to serve its customers as fast as possible. This also enables the company to have a superior warehouse design than that of its competitors.
A company should also consider cost when designing the location of a warehouse (Harrington, 2007). The transportation costs from the company to the warehouse then to customers should be minimized. Thus a company can choose to use one major warehouse or multiple ones, provided the location leads to minimal costs.
The company should also consider the inventory cost of using one major warehouse or a network of warehouses. The company should choose the warehouse location which allows for minimal transportation as well as inventory costs.
Safety and Security
One of the primary roles of a warehouse is to ensure that goods or products stored inside it are kept safe and in good conditions. A good warehouse design should ensure that goods are released in the same condition they were received. A warehouse should also be able to ensure the safety of workers working inside it. A warehouse should also ensure security of products to prevent their loss and damage. Therefore, when designing a warehouse the safety and security standards should be considered.
Safety
In ensuring safety within the warehouse, safety information must be available to all personnel. There should be signage posted announcing various precautions to guide workers on how to handle commodities as well as prevent themselves from accidents. The warehouse should also be designed to ensure aisles allow for adequate clearance and the floors should have efficient drainage systems.
The racks as well as other storage areas should be build in a manner to ensure items stored in them are stable to withstand things like earthquakes. The loading dock of the warehouse should also be built in a manner to accommodate the requirements of the warehouses. This is because a lot of damage on goods as well as accidents happens at the dock. The warehouse should also be designed to accommodate enough space for all activities happening inside it.
Security
A warehouse should ensure that goods stored inside it are secure from robbery and things like fire (Arabian Supply Chain, 2009). Thus, security is a major consideration when designing a warehouse. When designing a warehouse, local law enforcement should be involved so that they are able to locate those weak points that can be used as breakage points into the warehouse.
They should also contribute in locating where buildings within the warehouse premises should be built, so that they know how to secure the area in case of a robbery incident. The police should also have information about security guards, and other personnel accessing the warehouse during non-working hours.
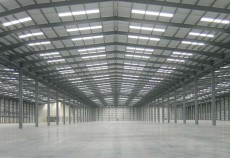
The warehouse design should also be in a position to allow a secure perimeter of property. This can be done through use of a chain link fence probably with barbed wire and which is at least six foot tall. In designing the warehouse, it’s also a good security measure to keep vehicles owned by the warehouse elsewhere out of the warehouse premises itself.
The main entrances should be designed with doors that are firm with serial number locks to ensure maximum security. Ventilations should be designed to have metal bars or wire mess to prevent entry of robbers. To prevent things like fire, a warehouse should be designed in such a manner that flammable goods are not kept near the fence. The design should also incorporate more emergency exit doors that are only unlocked from inside.
Productivity
When coming up with the warehouse design its essential to make sure the space available is fully utilized to store as much products as possible. This ensures maximum utilization of the warehouse although it should not be to the expense of safety and organization (Richards, 2011). The use of different types of racks to well suit the type of your products helps in utilization of space. The type of inventory determines which layout for your racks to use.
For example if products of the same type make the inventory then deeper rows can be efficient. On the other hand shallow rows will apply for variety of products in small quantities. The spaces between rows again should be able to accommodate pallet trucks. The space should not be too small such that the pallet jack cannot make a single turn as this can lead to damaging of products.
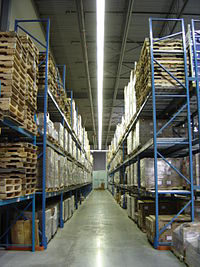
The warehouse design and layout should also include selection of machines and equipments that best fits it. The equipment should be selected according to their specific tasks to ensure no failures which could lead to damages. For example if your design allows for narrow spaces between rows then you can use European pallet trucks as they are narrow than those of United States.
Managing of inventory in the warehouse also ensures productivity. Today a warehouse design should promote just in time deliveries. This implies that products stored in the warehouse are constantly been received and shipped. Good software to aid in managing inventory in a quicker way should be implemented.
This will aid in quick recording of products received and been shipped out of the warehouse. Products should also be arranged in a manner that promotes easier and faster access. Those products which are constantly received and/or shipped out should be stored in racks which are near the doors or loading docks (Richards, 2011).
Keep Green
With global warming been a major issue in the current world, companies have joined in the race to maintain the environment clean (Arabian Supply Chain, 2009). Companies thus have adopted in using facilities that are environment friendly. The same case will apply for those companies designing warehouses today.
A warehouse should be designed in such a way that it uses little artificial light. This means use of translucent roofs, as well as clerestory windows to allow natural lighting. The provision of good ventilation to bring in outside air in the warehouse is another green attribute. The use of down lighting is also another green recommendation.
Doors
Today warehouse are mostly used for just in time deliveries. This implies that there is heavy in-flow and out-flow of products. These products thus have many inventory turns and do not last for long in the warehouse. This use of just in time deliveries determines how doors are designed to facilitate faster receiving and shipping of products.
A warehouse dealing with receiving of for instance raw materials and shipping them as finished products, receiving docks can be designed opposite of shipping docks. This is the opposite of warehouses which offer just-in-time deliveries as receiving and shipping doors are designed adjacent of each other (Ackerman, 1999). Doors are also designed on the basis of how many operations per day they will handle. Other things like security and maintenance costs are also considered when designing doors.
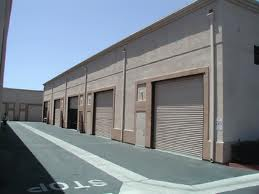
Automation and Technology
With the fast growing high-tech equipment, it’s essential to implement automation in the designing process (Arabian Supply Chain, 2009). During the designing process consultation of an automation expert is required. This is because he is involved in determining the column layout as well as the height of the warehouse.
The expert is also in a position to understand the aim of the warehouse as well as operations that will be taking place, and which equipments will be used. This enables the expert to generate a suitable automation solution which after the client’s confirmation can be applied.
Technology must also be highly considered when creating a warehouse design. The purpose of the warehouse determines which Warehouse Management System (WMS) will be applied (Arabian Supply Chain, 2009). The complexity of the WMS is determined by the volume of products received and shipped per day.
The WMS can also be complex if the company owing the warehouse has a complex supply chain network. When designing the warehouse consultation is important in determining the right WMS to be used to suit the operations as well as the purpose of the warehouse.
Design Approach
When designing a warehouse the first approach should be through collection of data about the company which owns it. This should then be followed by understanding the aspects of the company through use of collected data, and then developing concepts to be applied in the designing process. In designing a warehouse, collection of operations data should be the first step. This aid in clarifying things like how much the Stock Keeping Unit (SKU) will expand, its size, or weight that will be stored in the warehouse (Ackerman, 1999).
A database should be developed on all the operations of a company before coming to sizing and the layout of the warehouse. This data on operations should include daily shipments and receiving cycles of the warehouse (Harrington, 2007). This data will aid in determining the space needed to allow for storage of daily inventory.
This will also allow for addition of safety stock number to the data collected allowing for fluctuation of inventory levels. The data collected is also used to make future projections which play a great factor in coming up with a design that will accommodate future storage. When collecting data many factors of goods stored should be included.
The data collected should have information about inventory turns. The inventory turns will reveal information on a company’s inventory cycle within one year. This shows how long the warehouse will be holding goods before shipping them. This information thus is applied in designing a warehouse that will hold goods according to the time they are stored before been shipment.
This also helps to design a warehouse that separates those goods with many turns from those that will be held even for more than a year (Ackerman, 1999). This facilitates easy withdrawal and keeping of the different goods safe.
When collecting data, information about receiving and shipping should also be researched. There should be information about number and type of receipts received or shipped daily.
You need to know if the company is dealing with full pallets or full truckloads of goods. The data should also include information on if shipments have multiple SKU’s or are they in parcel form. Data should also be collected on daily operations to known those days with more shipments or receiving. This aids in designing equipments at the loading docks that facilities those many shipments.
The data collected should also include information about customers shipping goods from the warehouse. Data of how many shipments are made to customers on normal and peak days should be considered. The number of customers shipping products should also be known.
This information on customers’ shipments determines how busy the loading dock is thus its design. Inbound shipments data also determines a lot when designing a warehouse. There are those goods which are received and shipped in a single SKU and are always ready for putaway. Other goods take time before been stored; for instance those products that require testing for example chemical products. In designing the warehouse different docks are used for those goods ready for putaway and those which need repacking or testing.
Phases of Warehouse Design
Generally in designing a warehouse three phases are involved. These steps include: analysis, design planning, and implementation phase
Analysis
When a company is undergoing preparations to come-up with a warehouse design, data is collected. The data collected on all operations and types of products to be handled in the warehouse is analyzed. These analyses help to generate specifics and assumptions of the warehouse’s size, height, racking, among other factors that contribute to its overall design.
Statistical analysis on the available data should be done (Murray, 2011). This will aid in generating specifics like; what volume of goods will be received or shipped per day? What is the highest expected volume of products received or shipped? Which days are normal and when do we have peaks? Data on type and form of products to be stored should be analyzed to aid in determining the type of racking to be applied.
If products are of similar nature and size then deeper rows will apply. These analyzes will also aid to determine the size of the warehouse to be built to cater for present and future needs. When analyses are finished a consideration of company’s objectives and goals should be carried out to ensure assumptions made are in line with those objectives. After having a rough picture of the needed space thus size of the warehouse, you can now start to plan the warehouse design.
Design planning
Using the specifics and assumptions generated after analyses, the company now starts generating the design for the warehouse. This starts by planning where different operations will be based within the warehouse. This helps to ensure that those activities that relate are positioned in a way to allow for easy and fast moving of products between them. This is then followed by planning which equipments to use according to the racking used and type of products to be carried. The estimation of labor is done so as to estimate number of workers needed.
After determining all these factors different warehouse designs are planned and developed for comparison and evaluation in determining the best design to suit the needs and objectives of the company. The plan should first show major tasks and how they will then break down to smaller ones. The design should show the path of a task from where it starts to where it gets finished indicating equipments and resources used. The design should also show estimation of time products will take to undergo a certain activity.
The different design alternatives are then evaluated financially and some trade-off principles considered. The cost of each design is evaluated to come-up with the most appropriate design financially without the expense of productivity (Murray, 2011). The need for a design with shortest paths is considered.
These designs are evaluated on the basis of how fast products are received, stored, and shipped. These designs are also evaluated on basis of which design provides for the smallest space to put inventory. This is because a design should be able to ensure productivity on basis of space and time.
The best design should ensure less handling of products. This implies that less labor will be involved which leads to reduced cost and less damage on products. The designs should also be evaluated on the basis of balancing activities. A good design should ensure activities are located in a manner to reduce time for products moving from one activity to another. After all these evaluations are done, the best design is selected for the warehouse.
Implementation
In the implementation phase the company should first issue proposals with specifications to different suppliers of same items and equipments needed (Murray, 2011).
This enables the company to choose the supplier with the right items and equipments and who will deliver them on time at a lower cost. The warehouse is then built according to the specifications of the design. After the design has been implemented a series of checks should be carried out. These checks show if the design is in accordance with set objectives of the warehouse.
References
Ackerman, K. (1999). Designing tomorrow’s warehouse: A little ahead of the times. Journal of Business Logistics, Vol. 20, No. 1, pp. 1-4.
Arabian Supply Chain. (2009). Top 10 tips for warehouse design. Web.
Harrington, L. (2007). Designing the Perfect Warehouse. Web.
Murray, M.(2011). Planning Your Warehouse Layout. Web.
Richards, G. (2011). Warehouse Management: A Complete Guide to Improving Efficiency and Minimizing Costs in the Modern Warehouse. Philadelphia, PA: Kogan Page Publishers.