Introduction
For a number of reasons, the consequence of sea water on concrete as a building material calls for extra interest. To begin with, buildings and other structures bordering or located offshore are open to the co-occurring processes of a number of physical and chemical wear and tear courses of action.
This presents an exceptional occasion to be aware of the intricacy of concrete resilience tribulations in practical applications. Secondly, seas constitute eighty percent of the earth’s surface and as a result, a huge number of constructions are accessible to marine water both in direct and indirect manners. While the structures along the coastline get in direct contact with the water, the ones that are inland also get contact with ocean water when strong winds carry the water inland in the form of spray.
When putting up of ports and docks, concrete is the material majorly used in wharfs, decks, retaining walls, and seawalls. Metropolitan overcrowding and contamination is a major problem that has led to the consideration(s) of putting up floating seaward platforms made mainly from concrete for placement of facilities like airfields, power plants, and throw away discarding installations (Threlfall, 4). Application of concrete seaward boring platforms and fuel storage reservoirs is also on an upward trend.
Concrete is a combination of rock or block fragments and sand aggregates with a binder substance, which is normally Portland cement. When muddled up with a correct proportion of water, the binder material hydrates resulting in tiny opaque gem webs encapsulating and bolting the collection into a stiff formation.
Archetypal concrete blends bear elevated resistance to compacting pressures, with typical values standing at approximately 28 Mega Pascal or 4000 psi. On the other hand, substantial tautness, for instance due to meandering will shatter the tiny firm pattern, ending up in fracturing and disjointing of the concrete. As a result of this, archetypal non-fortified concrete should be adequately propped up to put to a stop the advancement of tension.
If a component having elevated potency in tension is set in concrete, then the resultant substance, fortified concrete, stands firm against compaction forces, meandering forces and other direct tensile forces. A strengthened concrete segment where the concrete stands firm against compaction and reinforcement stands firm against tension can be cast into just about any form and dimension for the building sector (Portland Cement Association, 3).
Reinforced concrete refers to concrete within which fortification ingots, fortification meshes, laminates or twines have been set in to toughen the construction material under conditions of tautness. It was formulated by Joseph Monier in 1849. The reference Ferro Concrete means concrete that is strengthened using cast-iron or steel.
Other bits and pieces used to fortify concrete can be natural and amorphous fibers as well as composites in various kinds. Concrete as a construction material is tough in compression but frail in tension, as a result, incorporating fortification adds to its might in tension. What is more, the malfunction strain of concrete in tension is so little that the fortification has to cleave to the cracked segments together.
To end up with a strong, supple and long-lasting structure the fortification needs to have the following attributes; elevated strength, elevated tautness strain, superior tie to the concrete, thermal congenial combination, and hardiness in the concrete set up.
Fortified concrete can take in several forms of constructions and parts, together with slabs, partitions, beams, pillars, towers, foundations, among others. This form of concrete can be preformed or formed in place.
The way in which ocean water affects concrete was for the first time talked about in 1840. From that time the amount of information on the topic has gone up by a great deal, which is an implication of the significance of the topic.
For the most part, ocean water is fairly consistent in element composition, which is typified by the being there of approximately 3.5% soluble salts by weight. The concentrations of sodium and chloride ions are normally the utmost. They stand at 11,000 and 20,000 milligrams per liter, in that order. On the other hand, from the point of view of destructive activity to cement hydration products, adequate quantities of magnesium and sulfate are at hand.
They stand at 1400 and 2700 milligrams per liter, in that order. The pH (the logarithm of the reciprocal of hydrogen-ion concentration in gram atoms per liter) of ocean water ranges between 7.5 and 8.4. On the other hand, the mean value in balance with the atmospheric carbon dioxide stands at 8.2.
There are the particular environments like those in secluded bays and estuaries where pH measures of below 7.5 may be stumbled upon (Clear, 358). Such phenomena results from an elevated concentration of liquefied carbon dioxide, which in turn makes the ocean water more destructive to concrete made from Portland cement.
Concrete open to sea environment depreciates as a result of various activities. These include collective effects of chemical exploit of ocean water compounds on cement hydration products, base-cumulative spreading out in situations where rash conglomerations are existent, crystallizing action of salts inside concrete if one side of the construction is exposed to wetting and others to drying, ice activity in cold conditions, oxidization of set in steel in toughened or pre-stressed structural parts, and physical wearing down as a result of wave activity and floating matter.
Action on concrete as a result of any of the mentioned activities has a tendency to add to its permeability. This means the structure can be easily pervaded by sea water and this serves to make the material more and more predisposed to additional deterioration by the similar disparaging force and also other forms of destruction. For that reason, a network of interlinked chemical processes and physical forces are at hand to wear down concrete structures open to sea water.
The effect of corrosion on concrete constructions
From the point of view of chemical attack on hydrous Portland cement in unsupported concrete, in cases where base rash aggregates are lacking, sulfate and magnesium are the destructive elements in ocean water. In the case of well water, sulfate attack is referred to as rigorous when the concentration of sulfate ions is above 1500 milligrams per liter. In the same way, Portland cement mixture can wear down through swapping over of positively charged ions when ions of magnesium surpass 500 milligrams per liter.
Captivatingly, regardless of the lamentably elevated sulfate concentration of marine water, it is a widespread phenomenon that even when an elevated C3A Portland cement has been utilized and high volumes of ettringite are there as a consequence of sulfate attack on the cement mixture, the wear and tear of concrete is not set apart by spreading out. In its place, it more often than not takes the form of wearing away or loss of the solid elements from the volume (ACI Committee 222, 23).
It is strongly thought that ettringite spreading out is held back in settings where hydroxide (OH) ions have for all intents and purposes been substituted by chloride ions. While we are on the subject, this observation is in line with the proposition that an alkaline setting is crucial for the enlargement of ettringite by surface assimilation.
No matter the system by which the sulfate swelling linked with ettringite is held back in elevated C3A Portland cement concretes bare to marine water, the effect of chloride on the set up makes obvious the inaccuracy too many a time. This results in reproducing the performance of matter when, for the sake of plainness, the consequence of a single aspect on an occurrence is seen coming minus satisfactory regard to the other aspects existent. These effects may transform the outcome considerably.
It is worth noting that in accordance to the ACI Building Code 318-83, contact of sulfate with marine water is categorized as temperate, a case for which the use of ASTM Type II Portland cement is allowed.
The actuality that the existence of disjointed calcium hydroxide in concrete can result in wear and tear by a swap over effect concerning magnesium ions was identified as a early as 1818. This was from explorations on degeneration of lime-pozzolan concretes carried out by Vicat, without a doubt one of the originators of the expertise of modern cement and concrete (Clear and Hay, 67).
Depreciated structure members show evidence of a reduced amount of lime than the others when examined. What is lacking then has been liquefied and wiped off. Nature works to attain correct percentages, and to achieve them, rights the faults of force(s) which has fiddled with the measures. As a result, the upshot gets more discernible the more there is a move away from these correct fractions.
Quite a lot of high-tech assessments on the performance of constructions in sea settings bear out that Vicat’s analysis is by the same token suitable for Portland cement concrete. From long-standing researches of Portland cement mixtures and concretes bare to marine water, the verification of magnesium ion attack is well founded by the being there of white set downs of magnesium hydroxide and magnesium silicate hydrate.
In marine water, sufficiently-cured concretes having huge quantities of slag or pozzolan in cement normally go one better than orientation concrete having only Portland cement, to a certain extent since the former has not as much of disjointed calcium hydroxide following curing. The entailment of loss of lime by cement mixture, whether by magnesium ion attack or by carbon dioxide attack is illustrated in figure 1.
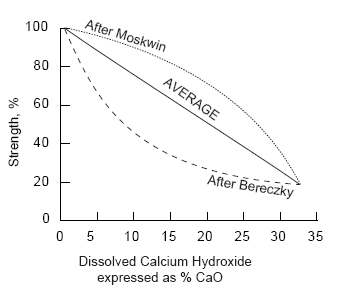
In view of the fact that marine water investigations rarely take account of the liquefied carbon dioxide substance, the prospect for loss of concrete volume through percolating away of calcium from hydrated cement mixture as a result of carbonaceous acid attack is in most times ignored.
In porous concrete the usual quantity of carbon dioxide existent in marine water is enough to putrefy the cementitious compounds in the long run. The existence of calcium silica-carbonate, calcium carbo-aluminate and calcium carbonate have been cited in cement mixtures drawn from depreciated concretes open to marine water for protracted times.
Permeability is the main solution to the durability of any concrete structure exposed to sea water or any other type of water (Song & Saraswathy). Injurious contacts of severe outcome involving components of hydrated Portland cement and marine water comes about in instances where the water is not put off from make a way into the interior of the concrete.
Archetypal foundations of not enough water protection are inadequately balanced concrete mixtures, lacking of adequately entrained air in instances where the construction is situated in a frosty type of weather, insufficient integration and curing, inadequate concrete cover on set in steel, poorly devised or put up joints, and mini fissures in consolidated concrete traceable to deficiency of power of stack circumstances and other aspects like thermal contraction, curing contraction, and base collection spreading out.
It is attention-grabbing to call to attention that engineers on the front position of concrete expertise are getting all the time more wide awake of the importance of permeability to resilience of concrete open to destructive waters. For instance, concrete stipulations for seaward constructions in Norway at present spell out the upper limit allowable permeability directly.
It is also worth noting that the nature and rigorousness of wear and tear may not necessarily be the same all the way through the structure. As illustrated in figure 2, with a concrete structure of cylindrical form, the segment that for all time remains higher than the high wave line will be more vulnerable to chill and ice wear and corrosion of set in steel. The segment that lays between high and low wave stripes will be susceptible to fracturing, not only as a consequence of chill action and steel oxidization but also from damp-dried up sequences. Substance attacks as a result of base-collection chemical reaction and marine water cement mixture contact will also be in operation here (Campbell & Folk).
Concrete that has been weakened by mini fracturing and chemical wear and tear will ultimately go to wrack and ruin by action and affect of sand, grate and frost. As a result, utmost wear and tear takes place in the tidal area. Then again, the completely sunken section of the construction will only be exposed to substance wear and tear by ocean water.
This is for the fact that it is not open to subfreezing temperatures and as a consequence there will be no dangers of ice smash up, and as a result of deficiency in oxygen only a slight corrosion can be expected. It comes into view that continuous chemical wear and tear of cement mixture by marine water from the outside to the core of the concrete tags on a common outline.
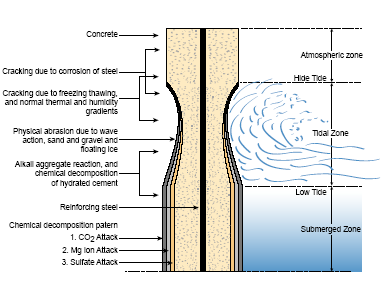
The configuration of aragonite and bicarbonate by carbon dioxide deterrioration is normally restrained to the outside of concrete, the configuration of brucite by magnesium ion deterioration is located under the exterior of concrete, and proof of ettringite development in the inside illustrates that sulfate ions have the ability to make way even deeper.
Except if concrete is very pervious, no smash up comes about from chemical deterioration of marine water on cement mixture for the reason that the chemical reaction resulting compounds (aragonite, brucite, and ettringite) are insolvable and they have a propensity to reduce the permeability and bring to a close additional way in of marine water into the interior of the concrete. This form of defensive action would not be on hand under circumstances of active stacking and in the tidal area, where the chemical reaction resultant compounds are taken away by tide action as soon as they are established (LMI Draft Report to the DoD).
Oxidization of set in steel is, by and large, the main foundation of concrete corrosion in toughened and pre-stressed concrete constructions open to marine water, save for little-permeability concrete this does not occur to be the primary foundation of cracking. The corrosion pace on a structure counts on the cathode/anode area.
Oxidization and spreading out going along with the corrosion does not take place pending enough availability of oxygen at the exterior of the strengthening steel, that is, an augment in the cathode area. Results from several case studies seem to suggest that cracking oxidization exchanges in all probability tag along the course diagrammatically shown in Figure 3 below.
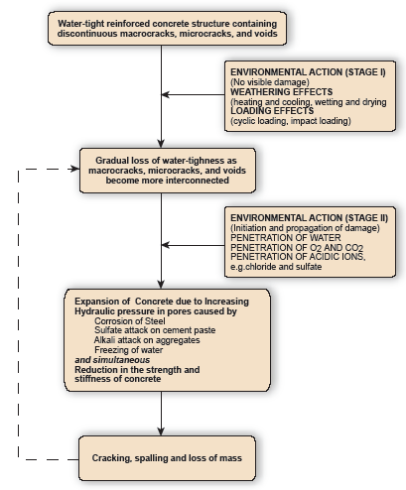
This does not take place as much as the permeability of steel-cement mixture bonding area remains low. Apertures and mini fissures by now are present in the bonding area, although their expansion by way of an array of events other than oxidization seems to be essential ahead of the setting for noteworthy corrosion of the set in steel. When the settings for noteworthy oxidization are set up, a more and more shooting up sequence of cracking oxidization commences, ultimately directing to full wear and tear of concrete.
Measurement tools for corrosion
The plan, putting into place and functioning of corrosion examination equipment requires know how in material science and electrical engineering. Thus, collection of data in this field has to be understood well. Oxidization probes are essential tools that cannot be serviced. They are planned and produced to go well with the particular construction. Essential aspects taken into consideration in the plan are the strengthening compactness and plaster, kind of form work, position of enduring examination apparatus, contact in the process and the period after construction.
There are the probe type tools and the M3 probe is the common one used. It is a multi-component feeler used to examine the pace of oxidization and state of toughened concrete constructions. It is designed to be set up at some stage in concrete erection and the probes are planned and produced to go well with the particular structure (Marusin, 58). A typical M3 probe consists of the following fundamentals: A carbon steel operational conductor, silver chloride/potassium chloride orientation conductor, stainless steel back up conductor and a thermostat hotness feeler.
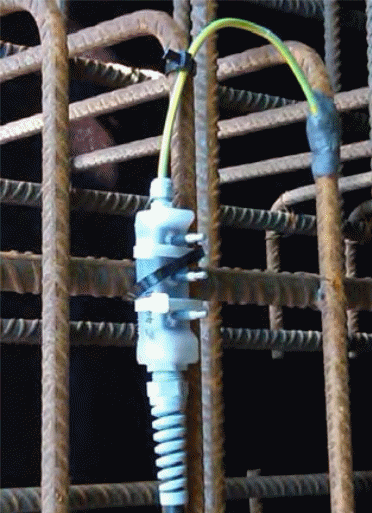
The C4 probe is another multi-component feeler used to examine the corrosion pace and state of toughened concrete. It is modified for utilization in channel constructions but it is as well perfect for putting in place into any toughened concrete construction. The typical capacities the C4 probe gives touch on corrosion and hotness details for interiors and exteriors of curved constructions with respect to an orientation conductor at the same time as using an central hoop as an secondary conductor.
This probe is normally linked to the Rate of Corrosion in Concrete Concerto and gives the subsequent lay down of dimensions: corrosion prospective, oxidization pace, concrete resistivity, concrete temperature and concrete humidity.

The M9 probe is another multifaceted component for use in aggressive settings like structures submerged in water where the capability to take readings at a range of depths giving timely caution of wear and tear is essential. Another example of such structures is nuclear storeroom plants.
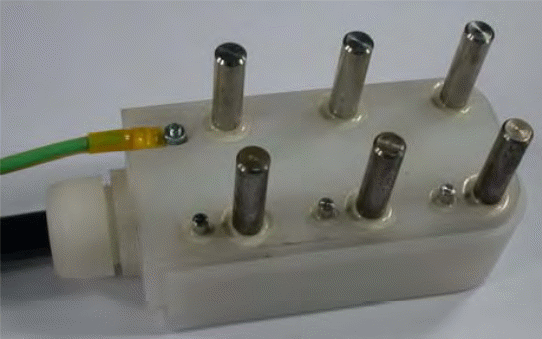
Another very important tool used in monitoring corrosion is the Concerto HTP engine that offers state-of-the-art monitoring for various purposes be it for field or research lab. Electrochemistry is applied in the instrument and the typical output from the tool is open-access information set up appropriate for straight transfer into catalog or worksheet functions. Adjustment software is made available to let users to fiddle with the dimension series for their specific application (ISO 7031).
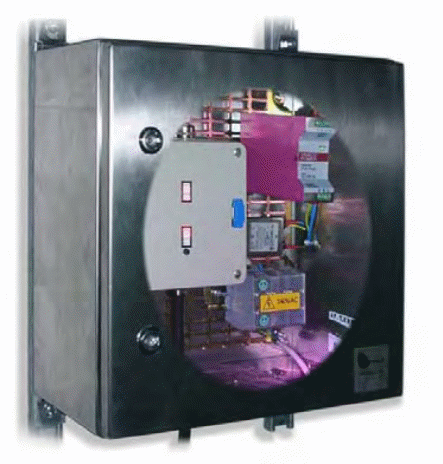
The Concerto RCC offers asset proprietors and sustainers with an incessant state account for the steel fortification and concrete mold in the face of compound wear and tear coercion from chloride dissemination, sulfate attack, permeation, thermal, and natural well water outcomes. When set up using DL or NT settings the dimensions permit straight correspondence with equipped and ecological bounds making it possible for performance developments to be set up and creating timely cautions of wear and tear with enough time to map and carry out corrective practices. The schemes are similar in temperament with upcoming cathodic safeguard application and can alter operation to bear out CP performance.
The RCC-DL undeviating data cataloguing set up is used to offer oxidization monitoring data for vital concrete constructions in both harmless and risky area settings where moveable components cannot be used and far-flung interactions are not necessary or achievable. At the same time as the RCC-DL set up is devised to function with the M3 and M9 probes, other set ups and probe kinds may be used.
The cost of corrosion on constructions and water front buildings
The cost of corrosion on concrete constructions exposed to marine water is enormously high and, thus, the focus on how the process takes place and how it can be slowed down or eliminated altogether. Following 21 years of use, the concrete stacks and tops of the supporting tower corners of the James River Bridge at Newport News, Virginia, called for a 1.4 million US Dollars patch up and substitution work.
This job entailed 70 percent of the total of 2500 stacks of the bridge. In the same way, 750 pre-formed concrete stacks driven back in 1932 in close proximity to Ocean City, New Jersey had to be patched up later in 1957 following 25 years of use (Nilson, 80).
A number of the stacks had been trimmed down from the initial 550 millimeters diameter to 300 millimeters. In both of these instances, the deprivation of matter was kinked with elevated levels of dissolved carbon dioxide existing in the marine water. Much later on, the 2002 findings of the research of the price tag of corrosion in the United States stood at the vale of three percent of the Gross National Product, GDP. This was an equivalent of 276 billion dollars.
Materials used for corrosion prevention
Majorly there are two kinds of up-and-coming expertise to take the edge off oxidization in strengthened concrete constructions. The first one comprises of exterior-applied oxidization inhibitors. These are substances that retard the process of oxidization. The other method involves an exterior-applied sacrificial cathodic safeguard outside layer. The oxidization inhibitor set up consists of three main components (US Patent 6627065).
These are; an ionic-anode form of inert piercing oxidization inhibitor, an unrefined steam part piercing oxidization inhibitor, and a rash silicone exterior safeguard means. The mutual utilization of these three oxidization-barring conceptualizations offers a long-lasting and multifunctional oxidization-barring setting. It also goes a long way in trimming down the water infiltration pace.
The sacrificial cathodic outside layer set up consists of an inert salt medium having zinc, aluminum, magnesium, and indium metals in the form of powder. This is applied to strengthened concrete on the outside along with titanium lattice stripes that are linked to the rebar to carry on cathodic electric current.
Tests carried out point out that oxidization rates of the rebar are trimmed down by a figure of 3.5 for the piercing oxidization inhibitor and 2.7 for the sacrificial cathodic safeguard outer layer. Water infiltration rates were also drastically went down. These outcomes show that appropriately picked and instituted piercing oxidization inhibitors or sacrificial cathodic outside layer set ups can be effectively utilized to lengthen the life of toughened concrete constructions by trimming down oxidization rates.
Other than the two ways of inhibiting corrosion in concrete discussed here, there also exist other methods of going about the exercise. Corrosion of set in reinforcing bars can be to a great extent trimmed down by setting crack-free concrete with little permeability and enough concrete plaster (Schiecl & Raupach, 56).
Reduced permeability concrete can be achieved by reducing the water to cementitious substances percentage of the concrete and use of materials like pozzolana and dross. These materials add to the concrete strength and trim down the corrosion rate even after it commences. Reinforcements can also be covered, for instance, using an epoxy resin, and use of sealants and casings on the concrete exterior. Sealants and casings, if applied, have to be from time to time reapplied.
The reinforcing steel can be set in at appropriate depths such that corrosion compounds from the outside do not get in touch. The water/cement relation can be kept lower than 0.4 and adequate detailing done to put off fracturing. Counteractive act for corroded concrete can consist of patch up the fractured part, and covering the exterior to bar additional entrance of corroding substances into the segment.
Construction designers have to mull over the amount of metal that is required to hold up the expected stress for a specific application. Due to the fact that they can make errors, the use of the construction can be altered, or the set up can be used wrongly, they normally are obligated to over design the construction by a factor of safety between 20 – 30%. A corrosion allowance is essential to maintain the construction secure if it does corrode.
Conclusion
Coastal regions and other areas bordering water bodies are very important to humanity and as a result have to be developed with various constructions like ports, harbors and hotels. The main construction material used is concrete. As a result, the way in which this material fairs on when subjected to water and marine conditions has to be fully understood so that structures set up in these areas can be put up to stand the tests of time.
This research has established that with proper set up and reinforcement, concrete constructions can last for long periods of time even when subjected to sea water. For that reason, the high costs associated with corrosion of concrete constructions can be significantly reduced with the proper procedures as a result of adequate knowledge on the matter.
Works Cited
ACI Committee 222. “Protection of Metals in Concrete Against Corrosion.” ACI 222R- 01, American Concrete Institute, Farmington Hills, Michigan. (2001). p 23 – 41.
ACI Committee 318. “Building Code Requirements for Structural Concrete.” ACI 318-05, American Concrete Institute, Farmington Hills, Michigan. (2005). p 121 – 443.
Clear, K.C., and Hay, R.E., “Time-to-Corrosion of Reinforcing Steel in Concrete Slabe, V.1: Effect of Mix Design and Construction Parameters,” Report No. FHWA-RD- 73-32, Federal Highway Administration, Washington, DC, 1973, 103 pages.
Clear K.C., “Time-to-Corrosion of Reinforcing Steel in Concrete Slabs,” Federal Highway Administration, PB 258 446, Vol. 3, 1976.
Donald H. Campbell and Robertt L. Folk. “Ancient Egyptian Pyramids–Concrete or Rock”. Concrete International 13 (8): 28 & 30–39.
D.S. Robertson. “Greek and Roman Architecture.” Cambridge, 1969, p. 227 – 233.
Ha-Won Song and Velu Saraswathy. Int. J. Electrochem. Sci.,”Corrosion Monitoring of Reinforced Concrete Structures.” A Review, 2 (2007) 1- 28.
ISO 7031: Concrete Hardened; Determination of the Depth of Penetration of Water Under Pressure, 1963.
Kosmatka, S.H.; Panarese, W.C. “Design and Control of Concrete Mixtures.” Skokie, IL, USA: Portland Cement Association. (1988). pp. 17, 42, 70, 184.
Lancaster, Lynne. “Concrete Vaulted Construction in Imperial Rome.” Innovations in Context. Cambridge University Press. (2005).
LMI Draft Report to the DoD: “The Annual Cost of Corrosion for the Department of Defense Facili-ties and Infrastructure,” 2007.
Newby F. “Early Reinforced Concrete.” Ashgate Variorum. (2001).
Nilson, Darwin. “Design of Concrete Structures.” MacGraw-Hill Education. (2003). p. 80- 90.
Portland Cement Association. “Types and Causes of Concrete Deterioration.” IS536, Portland Cement Association, Skokie, Illinois, 2002, 16 pages.
Robert Mark, Paul Hutchinson: “On the Structure of the Roman Pantheon”, Art Bulletin, Vol. 68, No. 1 (1986), p. 26, fn. 5.
Schiecl, P. and M. Raupach. “Laboratory studies and calculations on the influence of crack width on chloride-induced corrosion steel in concrete.” ACI Mater. J., 94: 56-62. Web.
Stella L. Marusin.. “Ancient Concrete Structures.” 18. Concrete International. (1996) pp. 56–58.
Threlfall A., et al. “Reynolds’s Reinforced Concrete Designer’s Handbook – 11th ed.” (2003).
Uomoto, T., K. Tsuji and T. Kakizawa. “Deterioration mechanism of concrete structures Caused by corrosion of bars.” (1984). Trans. Jap. Concrete Inst., 6: 163-70.
US Patent 6627065. “Liquid Galvanic Coatings for Protection of Imbedded Metals,” Inventor(s) Louis G. MacDowel and Joseph J. Curran, 2003.