Inconsiderate Use of Modern Materials in Old Buildings
As an associate surveyor for London Chartered Surveyor Practice, we visited a traditional building in London, which was built in 1891. The team observed that the building had a problem of dump. The team noticed that there had been an attempt to use modern materials to restore the building. A section of the building is shown in figure 1 below. A detailed inspection of the building showed that some outer parts of the building and the entire interior section was plastered. When asked, the owners explained that the reason for plastering was to beautify the building and to repair the cracks that had emerged over time. As shown in the figure below, the inconsiderate use of modern materials aggravated the damp problem in that particular building.
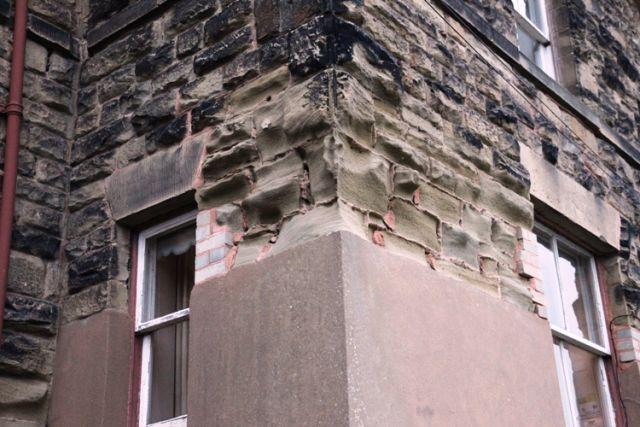
To understand dangers of inconsiderately using modern materials to repair old houses, it is necessary to start by understanding the nature and characteristics of such buildings. According to Suhr, Hunt, and McCloud (2019), an old building in the United Kingdom is defined as “a solid walled structure, built using breathable materials, which needs to breathe.” Traditionally, old buildings have been defined as structures built before 1919. As shown in the definition, there is emphasis on the breathability of materials used in such constructions. Example of materials that were commonly used in that era include timber, brick, stone, slate tiles, and lime-based mortars (Looser, 2021). The common characteristics of these materials is that they need to breathe. Figure 2 below is an example of an old building.
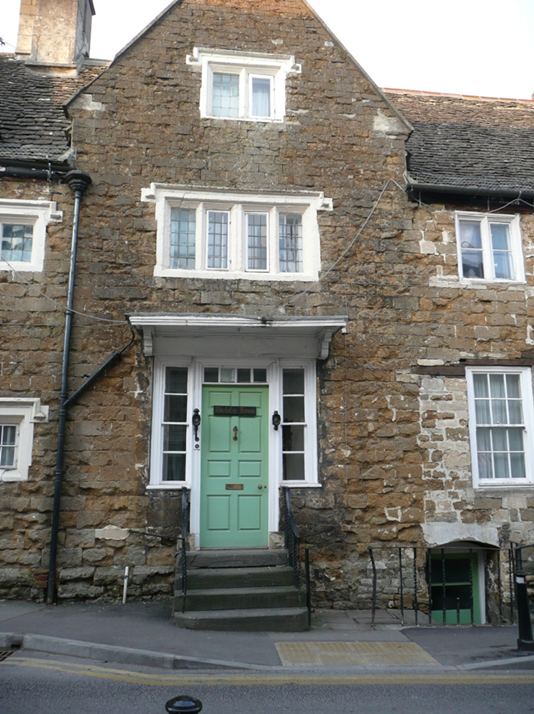
It is also necessary to understand the characteristic of the modern construction materials. Kabila (2019) explains that current popular materials for construction are artificial compounds. Some of these modern materials that have gained massive popularity include cement, gypsum plaster, silicones, plastic membranes and sheets, expoxy resins, fiberglass, polyurethane insulating sheets, paints, and plastic coatings (Bozack, 2020).
Some of these modern materials have gained massive popularity because they are light, hence they can be used in tall structures. They are also easy to mold into different shapes, which means that they are highly effective in decorating houses and making them look beautiful. Unlike some of the traditional building materials which are rapidly becoming scarce, Holland (2023) explains that these artificial materials are easily accessible, which means that they are cheap. However, they also share one characteristic, which is that they are not breathable materials.
During the visit, the team investigated the owners of the building to understand how the repairs and beautification of the building was done. It emerged that the handyman who was hired to do the repairs has little knowledge about the nature of old buildings. When interviewed, he explained that he used cement, plastic coatings, fiberglass, and paints in most of the interior sections of the building. As shown in figure 1 above, the handymen were also in the process plastering and painting the outer walls of the building. They believed that it was the best way of protecting the old building and making it last longer. However, they could not explain why the damp problem in the building became worse.
In the traditional building materials discussed above, air moves in and out of the structure easily. It is important to note that when the moving air cools, it loses the kinetic energy and condenses into a liquid. In these traditional materials, it will get to the surface and evaporate, which means that there will be no problem. The damp problem is created when these traditional materials are covered with the artificial non-breathable materials. As the small water droplets continue to form into larger water molecules inside the traditional material, they try to find a way out. The cement, concrete, gypsum, or plastic paint seals all the breathable spaces, which means that the moisture cannot escape. The result is that the wall will become damp, and unless the problem is solved, it will become worse. Figure 3 below shows the impact of inconsiderately using artificial materials to repair old building walls.
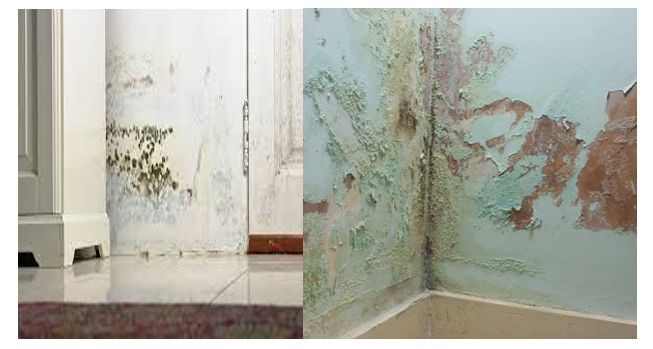
The problem is not with the modern construction materials. Kabila (2019) says that the main challenge is the inability of the handymen to understand how to use these materials to repair and to modernize old buildings. They fail to understand the nature of the traditional construction materials and how a change in temperature is likely to affect them (Bozack, 2020). As such, they completely conceal these materials in thick cement and plastic paints, denying them the opportunity to breath. They need the assistance of experts to know how to fix these synthetic materials into walls and roofs of old buildings. This way, they will be able to repair and beautify these buildings without exposing them to the damp problem.
Failure to Identify the True Cause of Defects Can Result In Undue Alarm
Failure to identify the true cause of defects in buildings is a common occurrence in the construction sector. The problem is that such misdiagnosis may result in undue alarm, which would expose the property owner to unnecessary expenses. In many parts of the United Kingdom, a report by a surveyor is critical and its recommendations should be observed. When the report states that the cause of the defect is a major problem that may lead to a collapse or major destruction of the building, it becomes necessary to undertake an immediate major repair or sometimes a complete demolition of the building to protect lives and property.
One of the possible misdiagnosis that can occur is the true cause of a crack on the walls of a building. Kabila (2019) explains that a crack on the wall may be a sign of a major or minor problem. The example of the crack, shown in figure 4 below, is most likely caused by moisture movement on the wall. It is likely that after cementing the wall, there was no proper curating done, which possibly resulted in the cracks.
The concrete and the stones, which are the fundamental parts of the building, could be sound and unaffected in any way by the cosmetic cracks of the plaster. Such a crack on the wall is a relatively minor problem that can easily be remedied using simple and cheaper processes, such as the one to the left in the figures below. However, if it is misdiagnosed as a crack caused by a more serious problem such as wall tie failure shown in the second picture below, the property owner will be alarmed. A wall tie failure requires a more expensive repair that has to be done immediately to protect the integrity of the structure. If in the process of repair it is revealed that the wall tie failure was not the cause, the property owner can sue the surveyor for the damages resulting from the misdiagnosis.
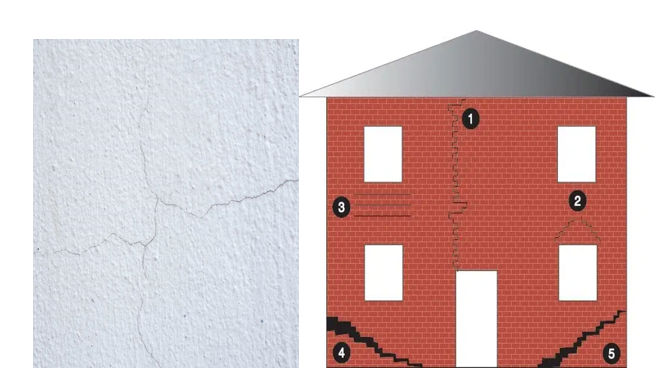
Sewer blockage is another example of an area where misdiagnosis may happen. Looser (2021) explains that buildup of oil and objects from the kitchen is the most common cause of blockage in the sewer system within a building. In such cases, there are liquid solutions such as boiling water, baking soda, and vinegar that can be used to unclog the system. These are relatively cheap and simple solution that will easily address the problem. However, a property owner will be alarmed if they are informed that the blockage is caused by a collapse of pipe in the system, which would require hacking the wall. They may be forced into a higher expenditure to solve a problem that required a simple solution.
As a RICS member, I will reflect on my professional practice by keenly abiding by the new rules of conduct. Rule 1 states that “Members and firms must be honest, act with integrity, and comply with their professional obligations, including obligations to RICS” (Royal Institution of Chartered Surveyors, 2021, p. 2). I will ensure that when making a diagnosis, I base my findings on thorough investigation of the building. I will be driven by the desire to protect both the tenant and the property owner, and will avoid the temptation of providing wrong information with the goal of stealing from the client.
Rule number 2 states, “Members and firms must maintain their professional competence and ensure that services are provided by competent individuals who have the necessary expertise” (Royal Institution of Chartered Surveyors, 2021, p. 4). I have the obligation of ensuring that I have the expertise to provide accurate diagnosis when assessing a given structure. I will avoid providing a professional advice in instances where I feel I lack the expertise that is needed. When necessary, I will work alongside other professionals to ensure that I provide accurate information.
As a member of RICS, there is a need to ensure that I offer the best service to my client at all times. Rule 3 states that “Members and firms must provide good-quality and diligent service” (Royal Institution of Chartered Surveyors, 2021, p. 4). I will ensure that those who are part of my team have the right skills and experience before they can be allowed to make independent assessment of structures. Rule 4 states, “Members and firms must treat others with respect and encourage diversity and inclusion” (Royal Institution of Chartered Surveyors, 2021, p. 5). It is common to find a workplace that is highly diversified in terms of race, religion, age, and gender.
I will remain committed to respecting everyone in the firm irrespective of the demographical differences that may exist. I will consider such differences as a strength that makes it possible for our firm to serve more clients from different backgrounds. Table 1 below summarizes the Royal Institute of Chartered Surveyors’ rules of conduct that I will observe.
Table 1: RICS’ Rules and How I Will Apply Them.
Source: ((Royal Institution of Chartered Surveyors, 2021).
Use of Thermal Imaging
The use of thermal imaging has gained massive popularity over the recent past. Kramer and Tighe (2020) explain that its use by building surveyors as a non-destructive testing method has spread to various countries around the world. One of its uses is determining the continuity of insulation. Using the infrared rays, this instrument can locate broken defective insulation. The rays can also help in detect poorly installed insulation. The comprehensive thermographic survey makes it simple to detect if the insulation is working as expected.
This technology has also proven to be effective in thermal bridge. This instrument measures surface temperature of the wall by using still cameras and infrared video (Singh et al., 2019). The tool is capable of seeing light, which is in heat spectrum (Kramer and Tighe, 2020). Images obtained from the film will then record the variations in temperature of the skin of the building, which often range from black for cool areas to white for warm areas.
The technology has also been determined to be an excellent tool for detecting dampness within the fabric of a building. When using it to detect dampness, the thermograpic cameras help in visualizing infrared radiation emitted from the object or material. Singh et al. (2019) state that dry areas of surfaces tend to emit different radiations from damp areas. When the rays are beamed on the wall, the thermal imagine cameras are capable of showing parts of the wall or floor, which are damper than the rest of the house (Kramer and Tighe, 2020). In building pathology, it is necessary to understand mechanisms or agencies that cause defects, as shown in table 2 below.
Table 2: Mechanisms or agencies causing defects.
Figure 5 below shows infrared thermal imaging technology in use. Termites pose a serious threat to buildings if left unchecked. Thermal imaging can detect heat patterns on a wall, floor, or roof. When there is a termite inversion, Singh et al. (2019) explain that there will be a change in the normal patterns of heat on the affected areas. The thermal cameras will be able to detect these heat pattern changes, making it possible to precisely locate termite infested areas. Instead of destroying a large part of a floor, wall, or roof, the repair will be targeted to the specific locations. The technology can also help in testing air exfiltration and infiltration (Kramer and Tighe, 2020). It does this by identifying heat loss patterns invisible to the naked eye, which helps to detect possible air leaks on the wall or any surface within the building.
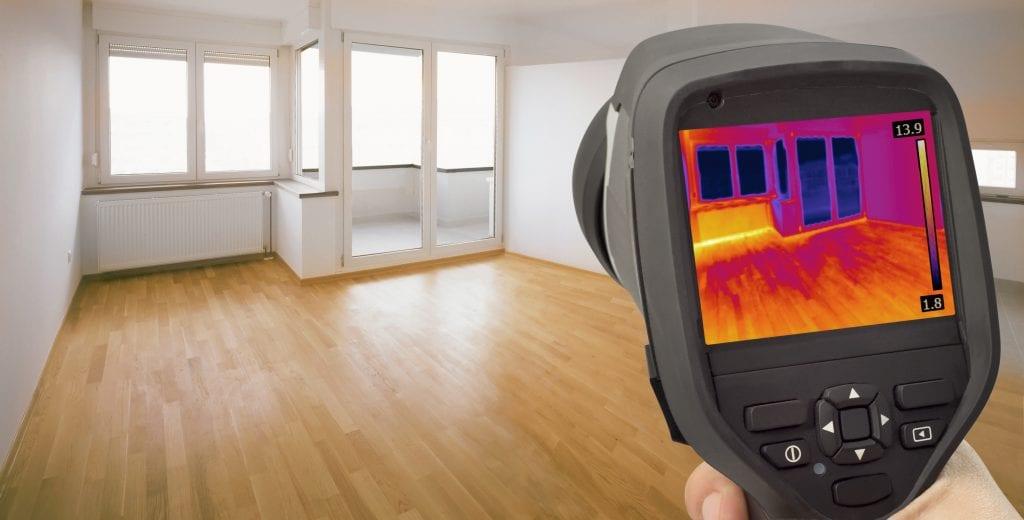
It is necessary to assess the pros and cons of using thermography versus video borescope. Thermal imagine has become a superior tool of detecting defects on buildings because it is a non-destructive technology. It does not require any form of demolition to inspect the wall, floor, or roof to detect specific problems (Vollmer and Möllmann, 2017). It is also a fast and simple way of conducting a diagnosis. Video borescope is a more involving process when compared with thermography. It means that when inspecting voids in cavity wall insulation and dampness in a building, thermography is a simple and faster process.
However, its main challenge is that it requires a highly skilled expert to interpret the results obtained from the infrared lights. Comparatively, video baroscope takes more time. However, its benefit is that it provides a greater detail because the video image of the void or dampness will be provided. The results from video baroscope are easier to interprete, as shown in figure 6 below, compared to those from thermal imaging. It means that sometimes it may be necessary to use the two technologies to determine the exact location of the problem and the degree of the damage.
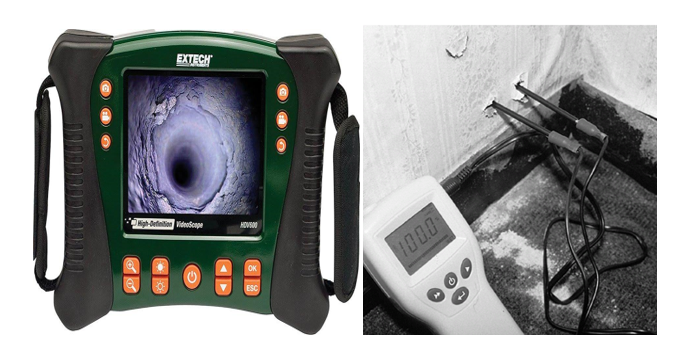
Possible Causes of the Icicle-Shaped Calthemite Stalactites on the Slab
Figure 6 below shows an icicle-shaped calthemite stalactites on a concrete slab in a basement car park. The possible cause is that water has percolated through this concrete slab for some time. Because the maintenance team failed to detect and address the problem in time, it has formed the icicle-shaped calthemite stalactites (Nix et al., 2019).
When concrete or lime-derived secondary deposits, which consists of calcium carbonate, is allowed to grow under an alkaline structure, it forms a stalactites, such as the one shown in the figure below. It is easily formed when there are cracks which allows for the seepage of water, which carries minerals such as calcium ion or calcium hydrogen. These deposits will remain on the underside of the structure, and when the leachate solution comes into contact with carbon dioxide, which is readily available in the air, there will be a chemical reaction (Nix et al., 2019). A calcium carbonate will be formed on the outer part of a concrete structure. If measures are not taken to address the problem, additional elements will react with the compound. If it is iron that comes from rusty surfaces, the calthemite will change its color to red tint or orange such as the one shown in 7 figure below.
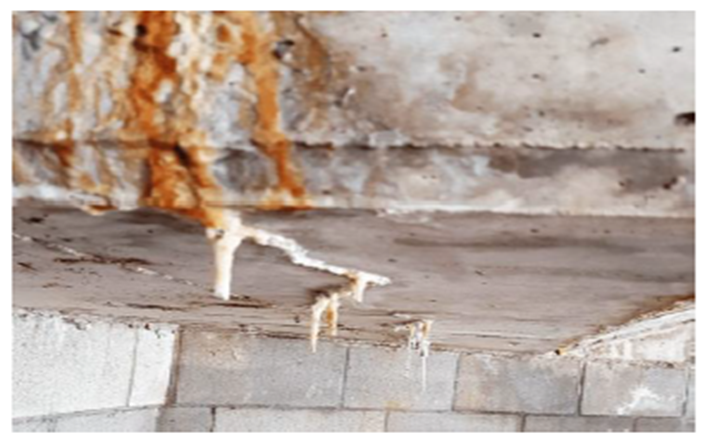
The solution to the above problem would be to ensure that there are no cracks on the slab in the basement of the car park. The maintenance team should ensure that any cracks on the slab are repaired as soon as they are detected. There should be a proper drainage system that channels the water through specifically defined paths. Care should be taken to inspect all the drainage system to detect and repair leakages. The team should also be keen to identify if calthemite starts developing on the slab. As soon as it is detected, it should be eliminated and the surface cleaned. The slab surfaces should also be regularly cleaned to reduce presence of minerals such as calcium hydroxide or calcium ion.
Reference List
Bozack, M. (2020) Avoiding a parental freak-out: straight talk from college professor to Christian parent. New York: Deepriver Books.
Georges Quality. (2022) Quality information. Web.
Heritage House. (2022) Managing damp in old buildings. Web.
Holland, M. (2023) Practical guide to diagnosing structural movement in buildings. Wiley-Blackwell.
Kabila, H. (Ed.) (2019) Urban and architectural heritage conservation within sustainability. London: IntechOpen.
Kent, D. (2020) How to treat damp. Web.
Kramer, S. and Tighe, R. (2020) Thermomechanics & infrared imaging inverse problem methodologies and. London: Springer Nature.
Looser, D. (2021) Moving islands: contemporary performance and the global pacific. Ann Arbor: University of Michigan Press.
Nix, C. et al. (2019) Hidden London: discovering the forgotten underground. London: Yale University Press.
Royal Institution of Chartered Surveyors. (2021) Rules of conduct. London: RICS.
Singh, R. et al. (2019) Non-destructive evaluation of corrosion and corrosion-assisted cracking. Hoboken: John Wiley & Sons.
Suhr, M., Hunt, R. and McCloud, K. (2019) Old house eco handbook: a practical guide to retrofitting for energy efficiency and sustainability. 2nd edn. London: White Lion Publishing.
Vollmer, M. and Möllmann, K. (2017) Infrared thermal imaging fundamentals research and applications. Hoboken: Wiley-VCH.
Waterstop Solutions. (2022) Seepage in car park: calthemite stalactites. Web.