Background of Existing Supply Chain of Finnforest
The major international mechanical forest product industry Finnforest Corporation has belonged to the Finland based Metsäliitto Group as a subsidiary and that runs its UK and European operation. SAP UK, (2008) mentioned that the company operates with two industrial divisions controlling the entire product category with engineered wood and forest wood with an annual revenue of €1.7 billion. As a global player, the large portion of the Finnforest’s major markets are located in Finland, East, West and Scandinavia and further more than 20 countries with 7,500 employees. Target customers of Finnforest has involved to handle with in industrial end users, targeted to building contractors, building suppliers and developers as well as DIY (do-it-yourself) stores customers and wood traders.
Chapman, P, Thayil, V. & Harrison, A, (2001) illustrated that the recent supply chain flows of the Finnforest corporation has focused on the European activities including both crucial and resulting wood manufacturing with three broader categories of consumers have patronised finished goods supply and distribution as-
- DIY (Do-it-yourself) retailers or the home improvement,
- Construction and industrial companies,
- Timbers merchants and builders.
Business Week, (2009) reported that the Finnforest Corporation employs themselves in manufacturing and selling wood products including product line such as spruce sawn timber in bulk, do-it-yourself (DIY) products for the individual customers, structural timber for the construction contractors. It is also concerned with solid wood products with exterior and interior goods including permeate timber products for the developers, components, comprising Nordic pine and thermo timber products for the industrial users. They also afford indoor and out door birch plywood and interior and exterior spruce plywood for construction work and also produce wood pulp for paper mills when most of its woods comes from Finish forest and sawmills and branded under the name of Finnforest.
This study would focus on dealing with the Finnforest Corporation UK‘s major DIY retailers and make proposals to improve customer services by redesigning the supply chain operations to reduce operational costs and lead time for Finnforest that would amplify to bring highest customer satisfaction and revenue maximisation opportunity for the organisation.
Existing supply chain of Finnforest
Metsäliitto Group (2008) mentioned that almost all wood products of the Finnforest Industry mostly used natural wood materials and very small portions of synthetic substances are used when its supply chain involves chemical supply, supply of raw materials in cooking papers and tissue, paper and board industry. It also deals with wood products industry and plum industry when its plywood, saturated wood products and laminated veneer lumber production necessitate chemical use that strictly follows the NCR (National Chemical Regulations). Metsäliitto Group (2008) also added that to implementing its supply chain Finnforest pursue the guidelines of the NWPC (Nordic Wood Preservation Council) as well as the FSA (Finish Standards Association) quality control of the wood manufacturing compliance with integrated standards in order to bear both the inspection stain and the quality mark under Finnforest for its impregnated wood products and raw materials. Existing supply chain of Finnforest has involved in four broad stages slot in as bellow-
Stage-1: Concept of Key Supply Chain Process of Finnforest
Chapman, P, Thayil, V. & Harrison, A, (2001) pointed out that the first stage starts with a diagnosing approach to clarify the overall recent processes and operational system that procedure has enabled to focus on the reasons behind poor performances. At the same time, it also could assess the ways to recover that process designed in such a way that in future performance could be measured. Chapman, P, Thayil, V. & Harrison, A, (2001) have structured overall supply-chain of Finnforest into five key stages presented in the following figure marked as “Block Flow Diagram” that represents each stage and stage to stage the flow of goods has been identified with arrows where a profound investigation has conducted by to portray each of the supply broadly for Finnforest.
- The forest: Forest is the preparatory point of the supply chain where trees are grown in the Finland.
- Primary manufacturing: In Finland, at swan mills collected logs are processed.
- Secondary manufacturing: For secondary manufacturing operation, make use of the seaways timber is transported to the UK and utilizing them into machinery to fulfill a wide range of consumer goods.
- Finishing products warehouses: Until calls off by a retailer finished products or the customer, goods are stored in warehouses.
- Retail outlets: Finnforrest mostly used direct transaction of its customer products or the finished products to do-it-you (DIY) retail outlets from the warehouses.
To facilitate data for the existing process aforesaid figure has shown the supply chain stages. Walk through this stages Vend enabled to gather necessary data from each steps of the overall supply chain process.
Data gathering
Employing three broad categories of time, principal Vend, decorated his data for the process’s steps. The principal unit of time is utilized here so to easily finding the cause of poor performance, waste diagnosing and identifying effectively. It would be useful if identified data would communicate to the existing process. Thus, proposed method would influence the poor performances to improve. Moreover, inventories are quantified to time at every step of the process. For three principal units collected data is as bellow-
- Activity time: For a single item completion process’s required time involved to undertake physical activities.
- Lead time: In short, time required to finish an activity that produces complete form of consumer goods. In another word, time will end when the current process finishes that start at the end of preceding activity.
- Inventory: A collective form of inventories evaluated through the demand of the number of days and that might be raw materials, held in finished goods or work in process.
Collected data from the Finnforest in order to evaluate their performance is presented in the following table. Here identified lead time is 50 days to turn the raw materials gathered from the forest into finished goods out of activity time 20 days during worked upon the timber. Whole supply chain process requires 161 days inventory.
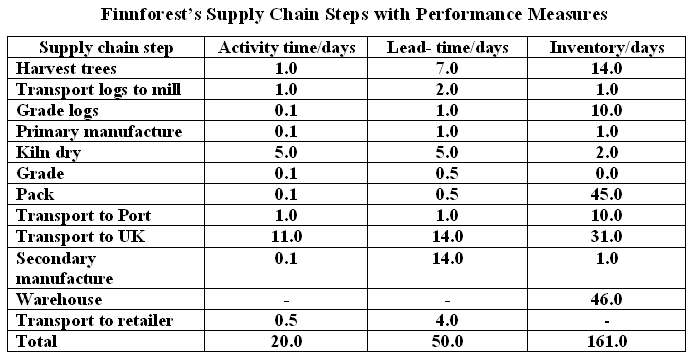
Process analysis
Second stage re-engineers in order to analyses the process of the supply chain management of Finnforest considering data of the structure and the performance of the process. Above table is diversified into two graphical modes to analyze. They are-
- A structural design
- Processed design based on time
Tools of these forms are described as follow-
A structural design
According to the pipeline map overall process involves in presenting inventory and the process lead time at once as following table-
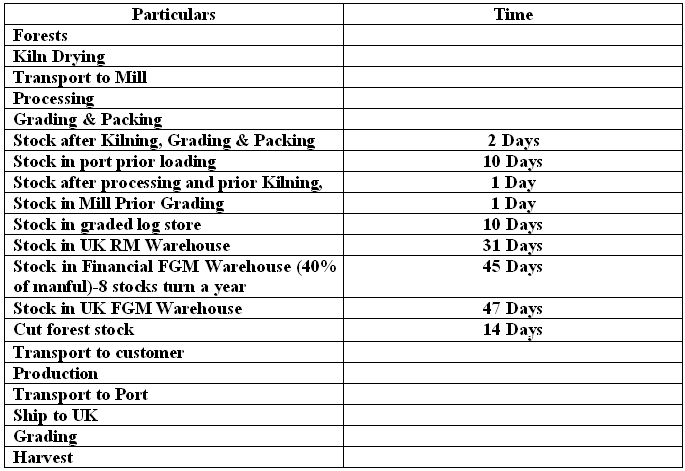
Processed design based on time
This model is also refers as “TOP” that presents the lead time schedule using Gantt chart for the supply chain. For every step of this process integrated lead time and the activity period at a time. Harmonize this approach there need additional data for the process. Amount of activity period is valued by the each step of the process’s lead time and also there should be mentioned whether time would finished or ending point of the activity. In addition, a clear definition of the term “waste time” also is plotted. In this mode, TOP makes available current performances as well as wasted time and its areas. Stage on the TOP term of the activities of the Finnforest has shown in following figure. Here in the horizontal bar, pipeline map has presented and in the vertical bar, lead time is shown in times of days. Thus, this map allocates two categories of activities lead-time and the waste time at once.
The supply chain redesign
Diversification of the supply chain performance can be expressed through the same units requires lead time and inventory measurement. Relationship between inventory and lead time helps to magnify safety stock and cyclical stock. There has a proportional alignment between inventory and lead time. If one of them increase by quantity, that influence another to increase. In addition, working capital and customer demand have also been increase in response of this proportion.
The proposal
Considering all of the stages of Finnforest proposal stated that recent supply chain of Finnforest has to improve so that lead time would be reduced, cost of the product decreased and on behalf of this quality will developed.
Effectiveness of the process flows
Roekel, J. V. Willems, S. & Boselie, D. M. (2002) argued that the most important market driving forces that insist on supply chain allies to pool resources are to be précised on market segmentation, amplified customer’s demand as well as low cost strategy. Finnforest UK emphasised more than ever for supply chain collaborates in all operating countries those who are willing to take part on the global supply chain alliance of Finnforest. It is paramount significance to connecting profitable markets, raising consumer’s demands, free flow of information, products, technology and investment as well as cost reducing initiatives to argue on the effectiveness of the process flows of Finnforest.
The continuous altering life-style of European consumers are motivating the demand for exacting products which are environmentally safe, organic, predestined ready to use and ensure fair trade. Finnforest is well organized to face these development challenges of supply chain management to make a distinction on the existing chain to put forward the value-added forest raw materials and finished goods to the exacting market segment.
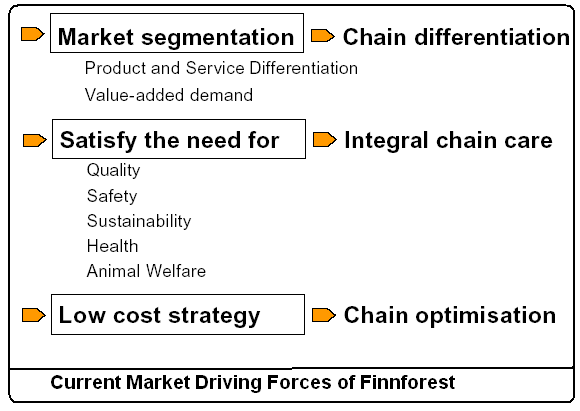
Finnforest’s customer preferences are more aggressively determined by necessities in the point of environmental safety, social components and health. Finnforest is striving to sustainability achieve the organisational goal set by the board’s corporate social responsibility. Its chain should argue to cooperate to keep away from loss of consumer confidence, chain care, lead time reduction and quality assurances as key factors.
Thus, the supply chain partners of Finnforest are mandatory to minimize costs to face the challenge of worldwide escalating competition. The collaboration of the successive links to tune activities and minimize costs by decreasing transaction costs optimizes chain results.
The opportunities of the Finnforest supply-chain management move toward are abundant factors as:
- Escalating of sales,
- Cutback of product losses in carrying and storage,
- Distribution of advanced techniques, resources and knowledge for chain partners,
- Enhanced information flow of products, markets & technologies,
- Intelligibility of the supply chain,
- Tracking & tracing to the resource,
- Superior control of product safety & quality,
- Outsized investments and risks sharing amongst partners of the chain,
SAP UK, (2008) has forecasted the opportunities and success factors of Finnforest‘s supply chain taking into account of buying and selling in the wood industries as an exceptionally complicated process. SAP UK, (2008) argued that the wood industry where Finnforest UK operates its business considered as vital due to numerous products and multiple sectors Finnforest serves which is the prevalent outside Finland. Its DCM involved raw materials impending from Finnish forests and sawmills and the finished goods manufactured and circulated in UK that the business model facilities the opportunities as-
- The project was modeled on demand planning in the DIY flow
- Being completed with SAP APO for IT integration
- Improve forecasting accuracy among 5,000 SKUs & 4,000 delivery points
- The group as a whole has behind the project.
Fundamental dilemmas of Finnforest’s SCM
Holma, H. (2006) mentioned that still the supply chain of Finnforest is moderately extensive involving more than a few intermediaries. The extensive distribution arrangement is challenging where exists some non-transparency that formulates the supply chain management complicated for Finnforest to achieve accurate information flow from the end users. Consequently, a variety of delays occurs within the supply chain management Finnforest.
Moreover, Finnforest has a far-reaching capacity to stock within its supply chain. The stocks and inventories are situated at numerous points stating from forest to end-users where inventories have argued to rise and fall seriously all over the business cycles. Thus, it is necessary to opportunism of the partners of the supply chain of Finnforest in perception of future demand of the wood market.
To redesign the supply chain of Finnforest, there are partial opportunities to modify the configuration and behavioral members with the supply chain identified above. The suggestive modifications for the fundamental dilemmas are as follows-
Structural dilemmas
- Distribution arrangement: elongated marketing channel with numerous intermediaries
- Widespread capacity to stock within the existing supply chain
Dilemmas of Relationship
- Non-transparency of the supply chain of Finnforest and inadequate communication
- Relationships of wood suppliers & the cycles of sawn goods are not simultaneous
- Internal relationship problems at Finnforest; internal inducement and control systems are weak
- Short term of business relationships
Behavioral management tools
- Delays in distribution chain and allowance assumption
- Consolidation and management philosophy
- Uses of control basis and relationships
- Investments pulses management philosophy
Introduction
Finnforest (2000) mentioned that the organisation has set up a subsidiary on the banner ‘Wood eXtreme Oy’ to generate e-commerce solutions for Finnforest and build up a new business opportunity in forest industry sector incorporating all the stakeholders of the company would be associated to the network by using Extranet fatalities. The project started grounding and accomplishment of the opening pilot projects concerning the customers from autumn 2001 where necessary Investment has been provided by the Engineered Wood Division of Finnforest with a cost of €42.7 million.
SAP (2004) pointed out that Finnforest is a global leader of forest industry producing mechanical finished goods and intermediates where the company need to address individual customers’ industrial users. Finnforest with its DIY (do-it-yourself) stores including building-suppliers, wood merchants, construction contractors and developers put into practice with the mySAP (SAP Software Trade Mark) and mySAP CRM (Customer Relationship Management) as a way out of its ecommerce aimed to endow with enhanced tune-up to the smaller customers as well as to enhance sales revenue without sales staff. The implementation of mySAP CRM has provided a little advancement for Finnforest but there are some complicacy to address all buyer seller and supplier of Finnforest. Thus, it is needed to redesign the e-commerce model of Finnforest. This paper would go to suggest a complete B2B model for Finnforest.
Finnforest’s E-Supply Chain Integration
Finnforest Corporation has missed a significant portion of revenue and cost saving opportunities because of their e-business more emphasize on customer application. Improvement of their e-supply chain would expand their operating activities in a wide range. Monitoring overall application success is critical in consumer integration. Ways of Finnforest’s production process and product and services has integrated by the value chain approach. Entire value chain approach conducts with product planning, manufacturing, procurement, support, service and order-fulfillment. In an effective and efficient manner value-chain approach, deliver products and services to the end user of the Finnforest. As a part of the Metsäliitto Group, Finnforest Corporation’s all steps of product delivery is composed in the term supply chain management and use of Web-based technology produces a significant power to this approach.
E-Supply Chain
Develop business-to-business (B2B) system Finnforest’s e-supply chain management (e-SCM) deals with agility, speed, customer satisfaction, real-tie control improvement. Other than technological areas, the e-SCM also entries cultural changes, performance matrices, management policies, organisational structures that walk through supply chain and the business processes. Managing inventory supply chain has become considered as a substitute and on behalf of this information, visibility passes through strict policies and discipline and most importantly daily forecasting and monitoring. Value chain and supply chain integration was built up in this corporation with the legislation of trading partners, suppliers and distribution channel and logistics provider.
E-Commerce Environment of Finnforest
Road map of e-business environment entrance requires a broad change in organisation of Finnforest. Regarding this, call for changes would involves in three essential components technology, process and people in both of operational and strategic level. Proposed e-commerce model of the Finnforest is shown ion following figure-
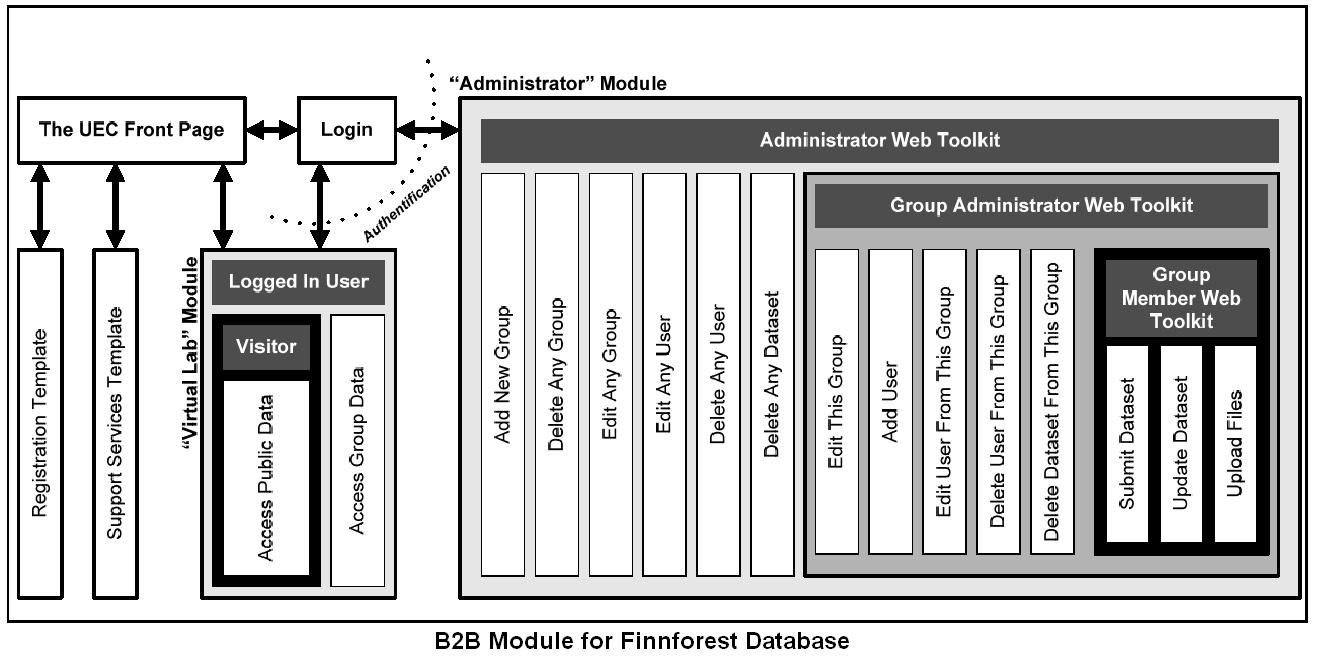
Strategic Issues
Technology
In implementing enterprise resource planning (ERP) issues are almost same as strategic technological issues and construction of this here should first prior on per day order. Technology of this corporation must focus on cost, flexibility and sociability. Software suppliers and key hardware have to maintain a strong relationship technological strategy. Concerning this people issues and management technologies would exhibit an extensive role in practice.
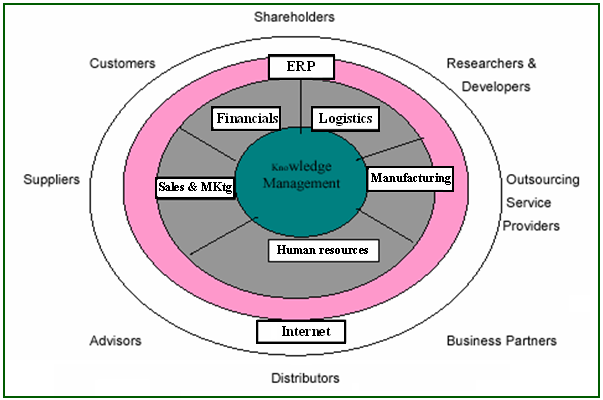
Process
For effective e-business architecture, Finnforest needs to reengineer the recent process business-to-consumer (B2C). Reengineering of the corporation would have to involve in transparent accountability and owed the enterprise widely, improve quality of delivery systems and budget execution. Coordination among them entails conflicts resolution is essential.
People
Efforts on major technology integration people would effectively do that. Having no change in difficulties some of the areas will coordinate with Internet. Any type of business success managerial ability work behind. On the other hand, key issue that would help in making change is the executive sponsorship.
Operational Issues
Operational issues in e-business entire downfield vision of the Finnforest Corporation. Major issues are under this field is report in bellow-
Technology
Technology operation of the Finnforest Corporation involves in product selection, concept of the requirements of the product support, performance expectations details, implementation schedule coordination, budget planning ought to ensure a sound phase, integration of data base management and make certain its security.
Process
Redesign the e-business model of Finnforest Corporation is committed to hardly exercise in implementation of objectives and evaluation of timelines that was developed in the strategic level. In this mode supply processes would established as a process of B2B.
People
Managers faced common dilemmas in the operation level in B2C model are organisational scope, complexity transformation, confrontation of the political issues, alteration of the culture and capability.
Other Technological Developments
Proposed business model B2B of the Finnforest Corporation will develop their present complexities in adoption of XML that was originated from SGML (Standard General Zed Markup Language). Exercise of this will brought their web delivery at an optimal level. In the road of WWW (World Wide Web) consortium XML make certain a uniform structured data that consists of industry standard and a vendor-neutral so that it will apply independently.
Today, IP (Internet Protocol) network is growing immensely. In addition, there have a significant prospect of XML in the Finnforest Corporation’s B2B e-supply chain model and walk through this way the firm will stand in the spotlight of profound paradigm shift in terms of powerful approach. For this forestry business presentation and evaluation of local inventories will be possible by the use of XML and transformation of database. Moreover, it also enables server-to-server data shifting worldwide. In practice of this, the XML utilize HTTP protocol that deliver data flows in general application form and exchange that in a simple form open text format.
Building B2B E-commerce Systems CSFs
This part of the case study has emphasized B2B e-commerce systems building and here speak to mostly of Critical Success Factors (CSFs) that aimed to this analyze is processing speed enlargement, accuracy, transact personally and improve business efficiency. In addition, significant difficulties that would be faced B2B in affiliation of current system are incomplete solution, requirements those are inflexible, interoperability in an inadequate scale, poor coordination with the existing model ad security and trust not in a reliable stage. Most considering and focusing point to efficiency development of the Finnforest Corporation are lawful expertise adoption, standard reputation, reliability, security and trust, accuracy, progress speed in transactions.
Electronic brokerage architecture suggests adoption of the systems that featured with heterogeneity rather than exercise of a wide range of product line and services. Supply chain of all categories of business as well as the Finnforest Corporation includes consumers, developers, suppliers and brokers who create the networks. Challenges of the supply chain will over come if there would be properly coordinate among enabling technologies that acts as key player with the business alliances, core business objectives and interoperability controlling.
All of the above considerations have need of two categories of key security factors-
- Affiliate user and the security tools so that they would make a fair trade by defending technical failure and criminal behavior.
- In order to trade and utilize digital goods make the environment friendly to the suppliers and also facilitate sufficient independency.
In the world-class business like the Finnforest Corporation does proposed e-business model has designed in such a way that diverse the application from the organisational models. Therefore, their business policies will be both flexible and dynamic in global perspective.
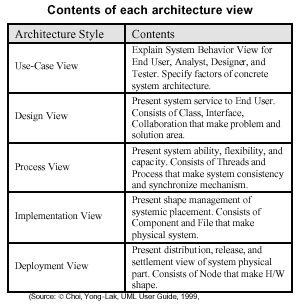
B2B e-business model of the Finnforest Corporation will be succeeding if they properly established the following Critical Success Factors (CSFs). This establishment also will get benefited trading and negotiation among unrelated parties along with a legal expert system.
- Users and developers communication will maintain a melodious phase,
- Transactions period will take less time than now,
- Transactions and business data base should be accurate,
- Transactions cost of the production ought to be decrease,
- Implementation of the proposed system will be passes through an efficient way,
- Life cycle of the system development will not be continue a longer period.
- Transactions data base have to be reliable,
- Data transmissions have to be secured.
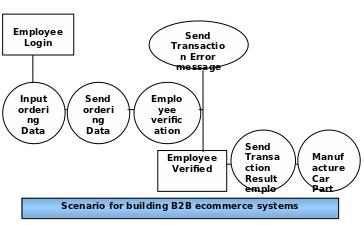
Classifying B2B Hubs of the Finnforest
Based on two dimensions, it has been addressed what to purchase and how to purchase through the B2B Hubs of Finnforest Corporation has divided into four major parts-
- MRO hubs (supply operating, sources are categories systematically and horizontal focus): for a versatile category of industry supply operation requires efficiency in procurement and MRO hubs concentrate to develop all of these. Tasks of these tasks work horizontally and the term horizontal refers as “third-party logistics”. Under this method, stock of the current assets does not require to reproduce.
- Yield managers (supply operating, sources are spotted as necessary, and horizontal focus): view point of significance of the operating inputs task of the yield managers labeled the procurement items and procure them sequentially. With the fluctuation of product demand mangers job is to evaluate the upper and lower limit of the products form both side of the consumers and the sellers or the suppliers. Demand utility, pricing strategy and the value of the product are also being included here.
- Catalog hubs (input of the manufacturing materials, systematic sourcing and vertical focus): in an industry vertical, there will emphasize on existing most promising market and the market that have most promising prospect. Here exchange of the commodity will be at a large and the relationship of the buyers and the sellers also will be in direct. In between this transaction there will have a significant role of the yield managers.
- Exchanges (input of the manufacturing materials, spot sourcing and vertical focus): At the last phase, vertical industries will get store manufacturing sources as input or inventory through a systematic catalog hubs streamline. Establishing online business industry and through a vertical supply catalog the Finnforest Corporation will be start transaction of supplies. This procedure focuses either on the buyer or on the seller from viewpoint of greater value generation and lower cost of production.
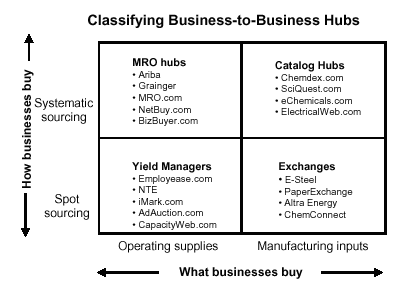
Kaplan, S., & Sawhney, M., (1999) addressed that the logical concluding inquiry has to be raised for what the turn around opportunity exist to integrate the B2B? The existing middle-of-the-road hubs of the Finnforest Corporation in the pertinent horizontal and vertical markets are doubtful to generate reverse and most significant hubs are obliged to endow with effective nonaligned status among the buyers and sellers to get hold of B2B Model that would generate customer’s satisfaction and higher productivity reducing lead-time for production of Finnforest.
B2B e-business system for the Finforest Corporation
Introduction
Proposed B2B e-business system for the Finforest Corporation, just allows only server programs transactions. Utilization of socket the application transmitted XML documentation. Storage of the database here will use the DTD and the XSL at a global percept as presented in bellow-
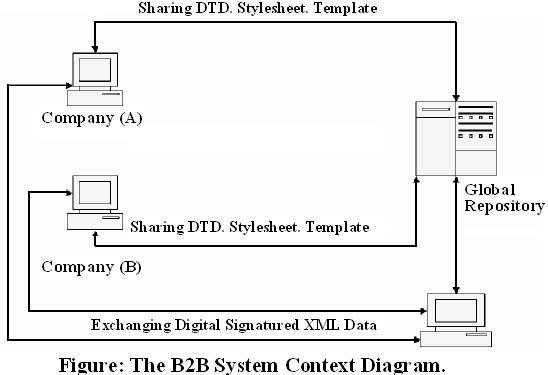
Sketch of the B2B system for the Finforest Corporation will get benefit in following aspects-
- There will be a melodious communication among the users and the developers. Therefore, both physical and conceptual visualization the Finnforest Corporation produce and make use of the XML and use case diagram in order to improve the coordination of the personnel and the developers.
- Second benefit of the procedure is greater use of Internet as well as lead-time it also reduces the data base management and exchange time of the personnel and the business activities.
- After the decrease of time B2B system is also cost effective. From view point of employee remuneration at the end of the year it will save large amount of money though this system is not practice yet.
- Data transaction and data base management accuracy will be improved at a large scale and also be less time consuming. Regarding this it will be possible interact and response more than now along with an error free guarantee. Finally, it develops tabulated form of using codes immensely.
- Gradually the system efficiency will improve and it would be possible to implement the use of digital signature after the delivery would be documented in front of the XML and the DTD. Based on the functions design of the components will occur so that it could be reuse and make possible to extent the current module. It also simplifies the error removing process and makes improvement in efficiency.
- B2B will make shorter the product development process and the product life cycle in combining prototyping development life cycle (PDLC) and the system development life cycle (SDLC).
- Another significant part system reliability will also be improve and decrease the errors since the employee has been progressed. In case of order delivery, tabular format will used greatly.
- Finally, shift of security; make use of digital signature make the overall security system much better than current system.
Customer service levels
Adoption of mass customization brought the customer service level in a high quality. It is the replacement version of mass production for adopting in present turbulent markets, rapid product differentiation and e-commerce scopes. Other features are-
- Used for individual customer service like bicycle.
- Customization of niche market like telephone companies,
- Variation in “standard” goods like electronic products.
In short, it would enable to serve customized products as well as a speedy re-provide the stores with required goods, which have passed with the replenishment of built to order-system and finally, for the suppliers of industrial-units. Finnforest introduces demand responsiveness on pull basis as a supply-chain module by which market can be served in better way to meet the target customers.
Avoiding the creation of excessive lead times and inventories
- Product and service design should reflects joint efforts of many areas of the management working together to achieve a match between financial resources, operations capabilities, supply chain capabilities and consumer wants and needs. In addition, special characteristics of a product or service can be a key factor in consumer buying decision.
- Cost of a company output is a key determinant of price, productivity and profits.
- Location can be vital in aspect of cost and for the convenience of customers. Location near inputs can result in lower input cost. Location near markets can result in lower transportation cost and quicker delivery times. Convenient location is particularly important in the real sector.
- Quality offers a large competitive advantage since customers are normally willing to give high for a commodity or service if they are perceived as higher feature comparatively better than the competitor.
- Quick response can be ensured in number of processes. Firstly, launching of a new item. Then, quick delivery of current goods after ordering and finally, attention of customer complains.
- Flexibility offers a drive to change. Changes might be alternative features in design, or to the quantity as demanded by people, or a traditional mix of items by the company.
- Inventory management can be a competitive advantage by effectively matching supplies of goods with demand.
- Supply chain management involves coordinating internal and external operations (buyers and suppliers) to achieve timely and cost-effective delivery of goods throughout the system.
- Service might essential after sales of the products. These are perceived by customers as value-added, for example delivery, set-up, assurance work, any technical support, development, and informing the customers and attention to detail etc.
- Competent managers and staffs are the heart and soul of the entire process because if they are experienced and motivated then they can provide a distinctive competitive edge by their skills, proficiency and ideas.
Postponement in product or process
Nowadays, a number of manufacturers are moving towards postponement strategy for differentiation for keeping the best inventory amount at each of the segment of PLC (Product life cycle). This strategy allows the manufacturer to use a “pull” or demand-oriented supply chain. Studies have shown that a systematic application of this can decrease the expense of inventory more than 40%. It is also been observed that implementation of postponement enables the manufacturers of keeping 80% to 90% of the finished stocks.
Stevenson, W. J. (2006) provides an example that furniture manufacturer can produce reading room sets such as table, chair but they do not apply stain unless customer allowing stains. Customer choice is important because once required stains, this will be applied in a comparatively short period of time. To achieve competitive advantage, Finnforest should remove a long wait for customers though the product line is different.
Cohen, S., and Roussel, J, (2005) stated that in Finnforest workers produce various Solid Wood and Engineered Wood which is unfinished, allowing the customers to alter their preference as to the exact length regarding the issue whether it should have maintain instruction of the customer. In the same way, delayed differentiation approach has been used by a number of market leaders of many sides, basically the manufacturers of semi-conductor industries as well as consumer electronics goods like Dell, HP, Home Depot etc.
Besides manufacturing, postponement can also be successfully implemented in service sector of Finnforest. For instance, different internet and e-mail services can deliver to the customers offering various packages, which have designed according to the customer’s choice. The output of this differentiation of a service with customized features which can be easily produced, focusing the customer’s wish for differentiation and delivery speed on which the majority is standardized, capable the user to understand the usefulness of that service.
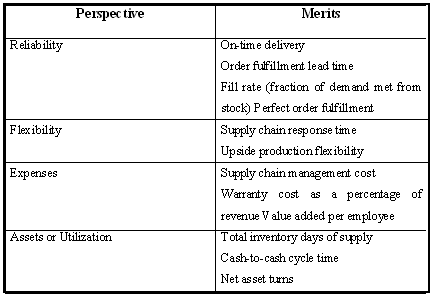
Appropriate marketing and distribution channels
Anand, K. S., & Mendelson, H., (2007) argued that polar diagrams are helpful for measuring the potential necessity of performance goal to the process while competitiveness is an important factor in whether a company prospers, barely gets by or falls.
Thus, marketing influences competitiveness in many ways, including identifying consumer wants and needs, pricing, and advertising and promotion. The proposed e-solution can change its distribution channels.
Details
- Speed: Speed can be a competitive advantage. Christopher, M. G. (2005) specified that quickly bringing new product or service in the market, instantly delivering existing product and service to convince the intended purpose and rapidly handling customer complains are some ways to amplify speed. Thus, services of Finnforest are quicker than services of competitors that work as an important competitive advantage for it.
- Dependability: It reflects on timely response while Finnforest provides the best time conscious service to the customers than competitors.
- Flexibility: It is the ability to respond to changes. It can be a competitive benefit in a variable environment. Changes might relate to alteration in design of the transportation service, or to the volume demanded by the customers. In this regard, competitors are somewhat rigid that Finnforest service relating schedule, ways or other means.
- Cost: Cost is an important determinant of price decisions, productivity and profits. Cost reduction efforts are generally in Finnforest rather than competitors.
- Quality: it means to material, objectives, workmanship plus design. Finnforest normally judge the quality of a transportation service when they design distribution channel of their products. Therefore, Finnforest will become more efficient to satisfy customer by changing their e-solution and distribution channel.
Mukhtar, M. et al (2009) addressed that the introduction of the Internet has been facilitated the business world to amend the way of accomplishing their businesses with e-procurement, e-marketplaces and e-supply chains that has amplified the business drives to reducing the lead time within the supply chain and ensure success to the e-business. The openness B2B has facilitated Finnforest with various potential in increasing and performing new ways of doing business and the management may often become over serious in implementing suggested e-business model in terms of humanising fast retort and customer’s service echelon at the same time keep away from the creation of too much lead times as well inventories. It would bring substantial benefits for Finnforest and the customers would enjoy the adoption of e-business by efficiency improvements when the stakeholders get better asset deployment, superior customer tune-up as well as eventually elevated shareholder value of Finnforest Corporation.
Bibliography
Anand, K. S., and Mendelson, H., 2007, Postponement and Information Systems in a Supply Chain, Web.
Alderson, W. 1950, Marketing Efficiency and the Principle of Postponement, Cost and Profit Outlook, Volume 3, Number 4.
Antariksa, Y., 2008, Five Tasks of Strategy. Web.
Bowersox, D. Closs, D., and Cooper, M. B., 2002, Supply Chain Logistics Management, 1st ed., McGraw-Hill/Irwin: London. Web.
Business Week, 2009, Finnforest Company Profile. Web.
Christopher, M. G., 1998, Logistics and Supply Chain Management, 2nd Edition, Pearson Education: London. Web.
Cohen, S., and Roussel, J, 2005, Strategic Supply Chain Management, 2nd ed., McGraw-Hill: London. Web.
Chapman, P, Thayil, V. & Harrison, A, 2001, Supply Chain Redesign at Finnforest Corp., Case -38, Case Data 2001, Pearson Education, Harlow.
Coyle, J. J. et al, 1995, The Management of Business Logistics: Instructor’s Manual, 6th edition, International Thomson Publishing: London. Web.
Damery, D., 2008, Using E-Commerce in the Forest Products Industry. Web.
Enslow, B., 2004, Supply Chain Inventory Strategies Benchmark. Web.
E-Business Forum, 2004, Minutes of The Meeting of the E-Business Forum. Web.
Finnforest, 2000, Annual Report 2000. Web.
Fred, C.P. M. & Sollish et al, 2007, The Procurement and Supply Manager’s Desk Reference, 1st edition, Wiley, London. Web.
Enslow, B. 2004, Supply Chain Inventory Strategies, Benchmark Report, Aberdeen Group. Web.
Kaplan, S., & Sawhney, M., 1999, B2B E-Commerce Hubs: Towards a Taxonomy of Business Models. Web.
Karuranga, É., Frayret, J., & D’Amours, S., 2005, E-business in the Quebec forest products industry: perceptions, current uses and intentions to adopt. Web.
Holma, H. 2006, Supply Chain Management and Industry Cyclicality: a Study of the Finnish Sawmill Industry, Universitatis Ouluensis, Oeconomica. Web.
Laudon, K. C. & Traver, C. G., 2008, E-commerce: Business, Technology, Society, 4th edition, New Jersey: Pearson Prentice Hall. Web.
Matthews P. and Syed, N., 2004, The Power of Postponement, Supply Chain Management. Web.
Martin, I., 2002, e-Business for Forestry Conference, Hilton Dunblane Hydro. Web.
Martin, J., & Roth, R. 2007, Supply Chain Management, ECRU Technology Inc. Web.
Metsäliitto Group 2008, Annual Report 2008. Web.
Mukhtar, M. et al 2009, A Framework for Analyzing e-Supply Chains, European Journal of Scientific Research, Vol. 25 No. 4, Euro Journals Publishing, Inc. Web.
Nobilis L., 2008, Competitive Advantage of Supply Chain. Web.
Oracle Corporation, Ernst, C. G. Young and APICS, 2003, Postponement for Profitability. Web.
Roekel, J. V. Willems, S. & Boselie, D. M. 2002, Agri-Supply Chain Management: To Stimulate Cross-Border Trade in Developing Countries and Emerging Economies. Web.
SAP AG, 2002, Finnforest, CRM. Web.
SAP UK, 2008, Finnforest UK improves its forecasting with SAP Advanced Planner and Optimizer 3.0: Planning Makes Perfect, SAP INFO 102 · Forum. Web.
SCA, 2007, SCA Timber, European Top 10 Sawmill companies. Web.
Semenov, A. V., 2007, Building Online Communities in Forestry: The Cases of Timberia.Org and the Urban Ecology Collaborative. Web.
Sheldon, F., Kwon, Y., & Kim, W-H., 2002, Case Study: B2B E-Commerce System Specification and Implementation Employing Use-Case Diagrams, Digital Signatures and XML. Web.
Srinivasan, M., 2001, E-Business and ERP: An Evolving Relationship, The Pennsylvania State University. Web.