Introduction
The objective of this report is to evaluate the properties, limitations, and prospects of future applications of fiber-reinforced concretes and polymer reinforced concretes. Chapter one will focus on Portland cement concrete as a construction material. The microstructure and imperfections of Portland cement concretes will also be examined.
Chapter two will focus on the types, properties, imperfections, admixtures, and future prospects of fiber-reinforced concretes. It will also examine how carbon and steel fibers can be used to reinforce conventional cement concretes in order to prevent micro-cracks and other flaws emanating from excess water, heat, shrinkage stress, and external loads. A literature review will be done to evaluate mechanisms of fiber reinforcement in conventional concretes. Different types of admixtures used to improve the corrosion resistance of fiber-reinforced concretes will also be evaluated. Finally, a discussion on the properties of fiber-reinforced concretes and their limitations will be conducted. These properties include compressive strength, tensile strength, and flexural strength.
Chapter three will begin with a brief description of polymer concretes and the major types used including polymer concrete (PC), inorganic polymer concrete (IPC), latex-redispersible polymer powder concrete, liquid resin concrete, water-soluble polymer concrete, and monomer-modified concrete. Different types of admixtures and their respective properties will be also be evaluated. Some of the admixtures discussed in this chapter will include styrene-butadiene latex, acrylic latex, epoxy polymer modifiers, and redispersible polymer powders. Finally, a literature review will be conducted to evaluate the mechanical properties of PCs, such as compressive strength, flexural strength, tensile strength, and bond stress.
Chapter four will focus on the differences between PRCs and FRCs. Special attention will be on the differences between PRCs and FRCs in terms of their mechanical properties, microstructures, and characteristics. Chapter five will focus on the applications of fiber concretes and polymer concretes in the construction industry. The first section of chapter five will discuss the application of FRCs in reducing rebar corrosion caused by carbonation and chloride penetration in conventional concretes. This section will also cover the uses of FRCs in repairing bridge-deck slabs, airport pavements, and tunnel linings. A brief discussion on the future prospect for bio-inspired FRCs will also be undertaken.
The second section of this chapter will cover both the current and future applications of PRCs in the construction industry. Among the current uses of PRCs discussed under this section will include its uses as overlays in swimming pools, floors and sewer pipes. The future prospects for using polymer reinforced concretes will entail a discussion on its application in shear wall structures as well as ductile concrete foundations. This chapter will conclude with a discussion on some challenges of using polymer reinforced concretes in the construction of cement composites. Finally, chapter six will present the conclusions of this report and recommendations will be made regarding the applicability of both fiber concretes and polymer concretes in the construction industry.
General Portland cement concrete
Portland cement concrete has been used as the main construction material for over a century since its structure has suitable properties (Islam et al., 2011, p. 55). Nevertheless, Portland cement concretes have a number of weaknesses such as low chemical resistance; large drying shrinkage; low tensile strength; and deferred hardening. Polymers have been used on several occasions in order to minimize these weaknesses (Ohama 1995, p.1).
The microstructure of concrete and the imperfections of Portland cement concrete
The properties of Portland cement concrete can be determined from its chemical composition as well as its structure (Tennis & Jennings 2000, p. 855). For instance, hydrated concrete (visible at microscopic level>200 μm) can be observed as a three-stage material made up of cumulative particles of different shapes and sizes, entrapped air voids within the hydration products, and a disjointed mass of hydrated cement paste. The fourth stage (interfacial transition zone, ITZ), can be discerned by examining cement concrete at the micron scale. The fourth stage (ITZ) embodies a thin-shell area (usually 10 to 50 μm thick) enclosing large cumulative particles (He & Shi 2008, p.13).
Although Portland cement concrete has a strong compression, its tension is somewhat weak. In addition, Portland cement concrete is porous. The pores in the Portland cement concrete emerge when concrete is formed. Hardened cement concrete is a byproduct of the reaction between cement particles and water. Thus, pores emerge when the water dries out of the cement concrete and creates avenues for chemical substances, gases, and water vapor that can damage the concrete. What’s more, Portland cement concrete has other weaknesses that can affect its performance. For instance, concrete cannot bond with some materials. Therefore, any attempt to adorn it with such materials will eventually deteriorate the roughness of the concrete surface. The application of Portland cement concrete is further hindered by its weak resistance to electric insulation, heat, saline water, and aggressive media (Islam et al., 2011, p. 55).
Fiber Reinforced Concrete
Concrete is considerably more brittle and displays a weak tensile strength in comparison to other construction materials such as polymers and metals. As noted earlier, Portland cement concrete has micro-cracks and faults both at the interfaces and in the materials. These flaws and micro-cracks stem from the plastic settlement, excess water, heat and shrinkage stress, and strain concentrations due to external restraints. Thus, when concrete is subjected to extremely heavy loads, it cracks easily. The resultant cracks provide easy entry points for harmful agents that result in scaling, steel corrosion, and freeze-thaw damage. The micro-cracks and flaws prevalent in the Portland cement concrete can be alleviated by inserting short (arbitrarily distributed) fibers of different appropriate materials. Fibers not only inhibit the surfacing of cracks but also halt their spread and growth. Thus, fiber reinforced concrete is the resultant material when fibers are inserted in cement concrete to suppress and abate the formation of cracks (Banthia, 2007, p.1).
Mechanisms of Fiber Reinforcement
When fibers are appropriately bonded, they interrelate with the matrix at micro-cracks levels and efficiently alleviate these cracks (see Table 1). As a result, they provide stress transmission media that effectively postpones their unstable growth and coalescence. If the fiber volume fraction is adequately high, the tensile strength of the matrix may increase above the BOP (Bend Over Point). When the matrix’s tensile capacity is attained, fibers (subject to their length and bonding attributes) will prevent crack formation and growth by efficiently bridging the macro-cracks. Therefore, this is the principal reinforcement mechanism employed in fiber reinforced concrete composites (Banthia 2007, p.2).
Fiber-reinforced concrete model
Flexibility-based fiber models are currently used for nonlinear analysis of FRCs. In figure 1, the fiber component is partitioned to form longitudinal fibers. The geometric features of the fiber are represented by the fiber area (Aifib) and in the local y, z reference system. The constitutive relation of the section is obtained via integration of fiber responses which pursue the uni-axial stress relation of the given composite as demonstrated in fig. 1. The key assumption in these models relates to the dispensation of the internal forces in the component. In a steady-state determination process, the section forces are computed using the component forces as well as through the calculation of the equivalent fiber stresses based on equilibrium (Taucer et al., 1991, p. 17).
The flexibilities and strains of the fiber are computed using the section deformations as well as stress-strain relations. On the other hand, section flexibilities are calculated using the principle of virtual force. The computation of fiber stresses (using section forces) is nonetheless a statistically indefinite setback (especially for a section with two or more fibers). It is impossible to compute fiber stresses using bending moment and the axial force due to the presence of only two equilibrium equations. This problem can be solved by assuming a stress distribution inside the section. However, the problem is merely deferred to the fiber-state determination stage of the algorithm. The solution implemented in the flexibility-based fiber models is to calculate the section deformations (subject to the linearization of the section constitutive relation) using the section flexibility as well as the new section forces from the initial step (Taucer et al., 1991, p. 17).
Types of Fiber Reinforced Concrete
There are two major categories of FRC: conventional FRC and high-performance FRC. In conventional FRC (with the low-medium volume fraction of fibers), fibers do not augment flexural/tensile of the concrete, and advantages of fiber reinforcement are restricted to either toughness (augmentation of energy absorption) or a drop in the plastic contraction crack control in the post-cracking phase. On the other hand, under the high-performance FRC (with superior fiber dosage), advantages of fiber reinforcement are manifested by a rise in tensile strength and strain-hardening response (Banthia, 2007, p.3).
Types of admixtures used for fiber-reinforced concretes
The types of admixture proportion used for fiber reinforced concrete are determined by the demands of a given work (i.e. workability and strength). There are various types of admixtures used for fiber reinforced concrete. Nevertheless, other forms of fiber reinforced concrete, such as steel fiber reinforced concrete (SFRC), require unique considerations (Lie & Kodur 1996, p. 511). For example, steel-fiber reinforced concrete (SFRC) admixtures v superior cement content as well as superior proportions of fine to coarse aggregate compared to conventional concrete. As a result, the admixture procedures for ordinary concrete are somewhat different from those used for SFRC. For instance, fly ash is typically used to reduce cement proportion in SFRC. What’s more, air entrainment and superplasticizers are frequently used to augment the workability of water-reducing admixtures and higher fiber volume admixtures. The aspect ratio (I/d) is another factor that can considerably influence the workability of the fibers (Chanh n.d. p.109). The proportions for normal weight FRC are depicted in table 2 while typical admixtures for SFRC are shown in table 3.
The mechanism for creating Steel fiber reinforced concretes
In general, SFRC can be created using normal concrete procedures although some key disparities abound. The main problem is how to insert an adequate volume of evenly distributed fibers to attain the preferred enhancement in mechanical behavior, while preserving adequate workability in the fresh mix to allow appropriate placing, mixing, and finishing. The performance of hardened concrete is further augmented by fibers with superior aspect ratio given that they enhance the fiber-matrix bond. Conversely, a superior aspect ratio can reduce the workability of the fresh mix. Consequently, problems related to uniform distribution and workability of the fresh mix enlarge when the length and volume of fiber are increased. In addition, the propensity for steel to clump together hinders the ability to realize a uniform fiber distribution (Chanh n.d. p.111).
There are a number of factors that can cause steel fibers to clump together:
- The clamping of steel fibers prior to their insertion into the mix. As a result, typical mixing techniques cannot unfasten the clumps.
- Clumping can take place if fibers are inserted hurriedly to permit them to scatter in the mixer.
- Clumping takes place when an extremely high volume of steel fibers are inserted into the mix.
- The inability of the mixer to scatter the fibers can result in clamping
- Inserting other concrete components after the fibers have been introduced to the mixer can result in clumping (Chanh n.d. p.111).
Therefore, caution must be observed during the mixing phase. For instance, steel fiber may be incorporated into the fine aggregate (on the conveyor belt) during the insertion of aggregate into the concrete mix. Clumping can also be alleviated by using assembled fibers fastened together by a water-soluble sizing agent that melts during mixing distribution (Chanh n.d. p.112).
Effects of admixtures on corrosion resistance of steel-reinforced concrete
Admixtures are commonly employed in concrete to enhance workability, corrosion control, impermeability, freeze-thaw durability, bond strength, and mechanical properties. Examples of admixtures include carbon fibers, polymers (i.e. methylcellulose and latex), and silica fume. Hou and Chung (2000) conducted a study to examine the effects of carbon fibers; methylcellulose; latex; and silica fume on the corrosion resistance of steel-reinforced concrete (p. 1490).
The cementitious material used in the study was Portland cement (Type 1). The admixtures used were silica fume, methylcellulose, latex, and carbon fibers. The researchers used eight concrete formulations to assess the effects of various admixtures on the corrosion resistance of steel-reinforced cement concrete (Hou & Chung 2000, p. 1492). The findings of the study are summarized below.
Effect of silica fume
When silica fume is added to cement concrete, it merges with lime to produce calcium silicate hydrate (Jennings 2000, p. 102). In addition, silica fume decreases the volume of large capillaries and pores. Consequently, the resulting cement concrete is impermeable, yield superior strength, has a denser microscopic pore structure, and is more resistant to harmful chemicals. The insertion of silica fumes in concrete reduces the volume of capillary pore thereby halting the amount of water entering the concrete. As a result, the rates of carbonation and oxygen diffusion are significantly reduced. Since the level of alkalinity in the concrete is extremely high, the corrosion rate is significantly reduced (Hou & Chung 2000, p.1503).
Effect of methylcellulose
According to the findings of the study, when methylcellulose was used as a dispersant in carbon fiber concrete, the water absorption rate in the resultant concrete was 2.7% higher compared to that of ordinary concrete. This suggests that when methylcellulose is added to concrete with silica fume, the resistance to corrosion is enhanced. Therefore, methylcellulose seems to seal small capillary pores more effectively than it does for larger pores (Hou & Chung 2000, p.1504).
Effect of latex
Latex has the ability to decrease stress concentrations, augment the cement-aggregate bonding, improve the concrete density, and fill tiny pores in the concrete. It appears that the addition of latex in concrete reduces the amount of water absorbed compared to plain concrete. As a result, latex improves the corrosion resistance of FRC. In addition, when carbon fiber and latex are inserted, the electrical resistivity of concrete is lower compared to ordinary concrete. Consequently, the low electric resistivity decreases corrosion resistance in FRC. However, the insertion of latex decreases the amount of water absorbed and hence augment corrosion resistance (Hou & Chung 2000, p. 1504).
Effect of carbon fiber
When carbon fibers are added to concrete, the corrosion resistance of FRC is reduced, particularly in destructive settings such as chloride content solution. Silica fume tends to alleviate the drawback of carbon fibers with respect to the corrosion resistance of FRC. When both carbon fibers and silica fume are incorporated in FRC, the corrosion resistance is somewhat lower compared to concrete with only silica fume. The low corrosion resistance is principally attributed to the huge disparity in volume resistivity between the two types of concrete (Hou & Chung 2000, p. 1505).
Properties of Fiber Reinforced Concrete
Compressive Strength
Fibers have a limited ability to augment the static compressive strength of cement concrete. Nevertheless, fibers can considerably augment the energy absorption of the cement concrete (post-cracking ductility) (Chanh n.d. p.112). This property is depicted graphically in figure 2 in the appendix.
Tensile Strength
Fibers (lined up in the tensile stress direction) can enormously amplify the direct tensile stress of the concrete (up to 133% for 5% of straight, smooth steel fibers). Nonetheless, the tensile strength increment for unevenly dispersed fibers is somewhat smaller and can range from 0% in some cases to possibly 60%, with a number of studies reporting intermediate values as depicted in figure 3 (see appendix). Therefore, inserting fibers simply to augment the direct tensile strength may not be meaningful. Nevertheless, steel fibers (as in compression) can result in a considerable increase in the tensile toughness of the concrete or post-cracking behavior (Chanh n.d. p.113).
Flexural Strength
Steel fibers typically have a much greater influence on the flexural strength of FRCs compared to either the tensile or compressive strength. For instance, some studies have shown that steel fibers can increase the flexural strength of FRCs by more than 100%. The increase is especially sensitive to both the volume and aspect ratio of the fibers (superior I/d augments flexural strength). Figure 4 shows the effect of fiber reinforcement with respect to collective parameter WI/d (where W=percent weight of fibers and I/d=aspect ratio). As noted earlier, fibers are added to conventional concrete to augment energy absorption capacity. Therefore, flexural strength refers to the total energy to fracture. In effect, flexural strength rises as WI/d rises (Chanh n.d. p.114).
Polymer Concretes
According to San-Jose and Frias (2007), polymer concretes (PCs) are made from “a mixture of inorganic aggregate with a strictly controlled particle size distribution and a polymer resin as a binder” (p. 30). Polymer concretes are not only durable and strong but also have lower permeability (San-Jose & Frias 2007, p.30). There are various terms used to describe polymer concretes, such as latex modified concrete or polymer Portland cement concrete. Polymer modified concrete (PMC) is described as hydraulic cement mixed with organic polymers that are dissolved in water (with or without aggregates).
An organic polymer is a material made up of immeasurable simple molecules that are merged to form large molecules. In this report, PMC refers to polymer-modified concrete, mortar, and cementitious slurry (Kaeding et al., 2003, p.3). According to Ohama (1995), polymers are commonly used to reduce the weaknesses apparent in ordinary concretes or mortars (p.1). For example, polymer modified concrete (PMC) is produced by altering ordinary cement concrete with polymer additives such as monomers, liquid resins, water-soluble polymers redispersible polymers, and latexes. PMCs have a monolithic co-matrix whereby the cement gel matrix and organic polymer matrix are homogenized. The properties of polymer-modified concretes are portrayed by the co-matrix (Ohama 1995, p.1).
Types of Polymer Concretes
There are various types of polymer concretes polymer concrete (PC), polymer impregnated concrete (PIC), and polymer-modified concrete (PMC). Inorganic polymer concrete (IPC) is also another type of PC produced using industrial waste materials such as granulated blast furnace slag, fly ash, and mine tailings (Sofia et al., 2007, p. 251). Other types of PCs include: latex-redispersible polymer powder, liquid resin, a water-soluble polymer and monomer-modified concretes (Ohama, 1995, p. 11). Polymer concretes consist of resin which is employed as the sole binder. In PIC, concrete is impregnated with polymer through the insertion of a prepolymer or monomer into the pore network of the cement concrete after it solidifies. Ensuing polymerization closes the capillary pores in the cement concrete. Lastly, polymer-modified concrete is produced when Portland cement concrete is modified with polymer resins whereby the binder matrix comprises of a polymer and cement, with the former acting as a co-matrix or modifying agent (Ebead & Neale 2007, p. 367). The polymer is usually incorporated during the mixing phase (San-Jose & Frias 2007, p.30; Czarnecki 2005, p.56).
Polymer concretes have a number of shortcomings compared to cement concretes. One of the main drawbacks to polymer concrete products relates to their soaring cost, especially with respect to prime materials. Since polymer concretes have less alkaline content compared to carbonation-free ordinary concretes, they provide limited corrosion protection for reinforcing steel. As a result, the steel in polymer concretes must be effectively shielded to avert corrosion should the concrete crack. Thus, one technique that can be used to stretch the durability of the reinforced concrete structure is by replacing the steel bars with fiber-reinforced polymer (FRP) in reinforced concrete. Fiber-reinforced polymer beams are more effective for reinforcing concrete under circumstances in which the performance of ordinary steel beams may be deplorable (San-Jose & Frias 2007, p.31).
Properties and types of admixtures used in polymer concretes
Properties of Styrene-butadiene Latex
Styrene-butadiene latex has been used as an admixture for Portland cement concrete ever since the 1950s. Styrene-butadiene latex-modified concretes and mortars are valuable for several applications (with a number of property requirements) since they provide low permeability and strong bonds for these applications. In addition, styrene-butadiene latex enhances thawing and resistance to freezing for outdoor applications. Elements in styrene-butadiene latex act as dispersants for the Portland cement concrete thereby increasing workability and flow of the concrete mixture without extra water (Kaeding et al., 2003, p.9). As a result, the amount of latex used will influence the physical properties in two ways: by the amount of water excluded and by the amount of latex applied.
Film properties
In a study conducted by Shah and Frondistou (1972), styrene-butadiene latex films were inserted in a concentrated lime solution to examine the effect of Portland cement concrete on latex addition. Their findings revealed that the films were not destabilized when exposed to the lime solution. On the contrary, the tensile strength of the films increased after insertion. In fact, the films’ mass grew by 5% during the first two days of immersion. In addition, the lime solution maintained a constant pH value during the insertion period (Kaeding et al., 2003, p.9).
Properties of fresh polymer concrete reinforced with latex
Air content
Since latex is manufactured using surfactants, surplus air can be entrained when Portland cement concrete is mixed with latex, unless an antifoam agent (i.e. silicon products) is incorporated into the latex. The correlation between antifoam agent and air content is determined by the type of latex, amount of antifoam agent, and surfactant system employed. Past studies have revealed that air content is affected by the composition of the aggregates and cement. Consequently, the mixture should be assessed before use since no research has been carried out to evaluate the effect of aggregates or cement on-air content (Kaeding et al., 2003, p.9). According to figure 5, an increase in air content reduces the compressive strength of concrete. In contrast to ordinary concrete, air-entraining agents are not added to PMC to provide resistance to thawing and freezing since both water and latex entrain some air during the mixing phase (Kaeding et al., 2003, p.11).
Workability
The workability of concrete modified with styrene-butadiene latex is superior compared to that of ordinary concrete. This is attributed to the dispersing effects of the components in the latex merged with water. This property is demonstrated in figure 6 where a flow table (ASTM C 230) was used to measure the workability of latex concrete. The data reveal that the dispersion effect is not determined by latex content. This is a clear demonstration that styrene-butadiene latex enhances the workability of latex modified mortar (Kaeding et al., 2003, p.11). Similar properties are demonstrated in concrete. Figure 7 depicts the relationship between latex content and water-cement ratio for concretes with constant slumps. When latex is included, it is possible to significantly reduce the water-cement ratios without reducing the slump.
Clear and Chollar (1978) compared the change in a slump of three latex modified concrete mixtures with that of ordinary concrete (fig. 8). According to their report, the slump loss in the three latex modified concrete mixtures was similar to that of ordinary concrete. Kuhlmann and Floor (1984) used aggregates from Maryland and Michigan to create workable concrete at low water-cement ratios. Both mixtures had a 229 Kg/m3 cement content, a 1.20 fine-course aggregate ratio, and 0.15 latex solid-cement ratios. Maryland’s aggregate yielded a 150mm concrete slump (at 0.37 water-cement ratio) while the Michigan aggregate yielded a 200mm slump at 0.33 water-cement ratio (Kaeding et al., 2003, p.12).
Setting and working time
Several studies have demonstrated that the setting time of styrene-butadiene latex modified concrete is higher compared to ordinary concrete. This property is demonstrated in figure 9 where data from two studies (Smutzer & Hockett 1981; Ohama et al., 1980) are presented. These data reveal that the setting time rises as the latex-cement ratio increases up to 0.10, with minimal increment after that. Nonetheless, the working time and setting time of latex modified concrete are not related. The working time is determined by the surface hydration while the setting time is subject to the hydration of cement. If the surface of LMC dehydrates before finishing is done, a crust (or skin) appears and may cause tears. The period needed to create the crust is influenced by the drying conditions (i.e. wind speed, humidity, and air temperature). In general, it takes about 30 minutes to process and finish the material after exposure to air (Kaeding et al., 2003, p.12).
Properties of hardened polymer concrete reinforced with latex
Compressive strength
Generally, polymer-modified concretes possess less compressive strengths compared to Portland concretes with identical quantities of water, aggregate, and cement. A number of studies have been done to evaluate the influence of specimen size on latex modified concrete. Figures 10 and 11 depict the outcomes of studies by Clear and Chollar (1978) and Ohama and Kan (1982) respectively. The effect of specimen size was deemed insignificant in both studies. In ordinary cement, large specimens are typically ineffective at inferior average stress compared to small specimens (Kaeding et al., 2003, p.13).
Shrinkage
Ohama and Kan (1982) utilized three latex contents in three concrete specimens of dissimilar sizes to show that total shrinkage does not rise when the latex is added to concrete. The researchers adjusted the water-cement ratio to hold the slump steady. Shrinkage measurement was done after several curing times (see fig. 12) and the results revealed that shrinkage was determined by water content (not the quantity of latex) (Kaeding et al., 2003, p.13).
Bond strength
Knab and Spring (1989), Ohama et al. (1986), and Kuhlmann (1990) have already assessed the adhesion of styrene-butadiene-modified concrete on different applications. Fig. 13 compares tensile bond strength in conventional mortar and latex modified mortar. Fig. 14 demonstrates that the tensile bond strength of styrene-butadiene LMC grows with time. Carl Walker and associates (1982) have also evaluated the tensile bond strength of latex modified concrete for reinforcing steel. In this study, 460 mm long of uncoated and epoxy-coated steel bars were inserted 40 mm deep in a latex modified concrete overlay (50 mm thick) on an ordinary concrete base. The results presented in table 4 show that the design capacity of the steel bars was attained in the latex modified concrete overlays (Kaeding et al., 2003, p.15).
Permeability
The micro-pores in the structure of latex modified concrete and latex modified mortar that usually emerged after the Portland cement hardens are partly crammed into the polymer film during curing. The polymer film decreases the permeability and water absorption of both LMC and LMM. Several tests have been done to measure these properties (i.e. chloride permeability, carbonation resistance, water absorption, and water vapor transmission). Previous studies have revealed that the permeability of latex modified concrete reduces considerably after 28 days. Fig. 15 presents outcomes of water absorption test of styrene-butadiene latex modified mortar. The data reveals a drastic decline in water absorption of latex modified mortar when the quantity of latex is increased (Kaeding et al., 2003, p.18).
Ohama (1973) also measured the transmission of water vapor by latex modified mortar. The results of the study revealed that water vapor transmission decreased when latex content was increased. A study by Ohama et al. (1984) sought to assess the carbonation resistance of latex modified concrete (LMC). The results showed that LMC carbonation resistance was superior compared to conventional concrete. The researchers used latex modified concrete exposed to carbonic acid and carbon dioxide gas. After exposure, a phenolphthalein liquid was employed to analyze the latex modified concrete samples. The results showed that carbonation was considerably reduced for both types of exposure when latex was included in the concrete. Clear and Chollar (1978) conducted a study to measure the chloride-ion permeability in latex modified concrete. The results of their study showed that PMCS has lower chloride penetration compared to those of ordinary concretes (Kaeding et al., 2003, p.18).
Resistance to thawing and freezing
Several studies have been done to evaluate the resistance of latex modified concretes to thawing and freezing. A study by Smutzer and Hockett (1981) compared conventional concrete and the deicer scaling resistance and reported:
The scaling resistance of LMC slabs at 50 cycles was excellent, with all receiving an ASTM C 672 rating of 0, while the air-entrained conventional concrete control block received a rating of 2. These ratings indicate no scaling and light-to-moderate scaling respectively (Kaeding et al., 2003, p.20).
The results showed that all samples used in this study did not have sufficient air-void system. It seems that the exceptional performance of Latex modified concrete is attributed to the resistance of the paste to water permeability. Therefore, extra air entrainment is not needed. However, the least amount of air content needed for resistance to thawing and freezing is not known. Ohama and Shiroishida (1983) revealed that when latex modified concrete (with 4.5% air content) was exposed to ASTM C 666 Procedure A after being cured for 13 days in the air, it did not perform well compared to LMC samples with 6% air content (Kaeding et al., 2003, p.21).
Creep and mass
There is insufficient data on the creep characteristics of latex modified concretes. However, a study by Ohama (1995) revealed that the creep coefficient and creep strain of styrene-butadiene latex modified concrete are less than those of conventional concrete. Results from a study by Ohama and Kan (1982) revealed that the mass of latex modified concrete reduced with time. The researchers used concretes with different latex contents and revealed that an increase in latex content reduced mass loss (Kaeding et al., 2003, p. 21).
Limitations of latex modified concrete
Latex modified concrete is a valuable and flexible material. Nonetheless, it has a number of limitations that merit consideration.
Weather
Latex modified concrete dries at the same rate as ordinary cement concrete. When exposed to dry air for extended periods, it develops a crust or skin on the surface although the underneath concrete is still plastic. This phenomenon occurs when moisture evaporates rapidly from the surface layer and can cause the mixture to tear during the finishing phase. This phenomenon is exacerbated by a sunny, dry, hot, windy environment. Nevertheless, the evaporation reducing techniques (stipulated in ACI 305R) can be used to reduce this condition. Compared to ordinary cement concrete, LMC is less responsive to low temperatures (Kaeding et al., 2003, p. 25).
Underwater
Latex-modified concrete cannot be placed underwater since the latex-modified composites attain their potential properties via air curing (Kaeding et al., 2003, p. 25).
Chemical resistance
Although latex modified concrete is watertight and consequently resistant to water infiltration, it has a modest resistance to chemicals. As a result, it can only be used in an environment with low or modest chemical content (Kaeding et al., 2003, p. 25).
Acrylic Latex
Acrylic latexes have been used as admixtures to modify cement concretes for more than three decades. These polymers are used to enhance certain properties of cement concretes including resistance to permeability, flexural strength, impact strength, abrasion resistance, and adhesion. Acrylic latexes enable cement concretes and mortars to preserve their adhesion and strength in dry and wet conditions as well as their resistance to ultraviolet exposure and weathering (Kaeding et al., 2003, p. 25).
Properties of acrylic polymers
Acrylics polymers are a group of polymers produced via polymerization of methacrylic and acrylic acids derivatives such as methyl methacrylate and acrylate respectively. There are two main factors that influence the properties of acrylic polymers: the length of the ester chain and the presence of CH3 (Kaeding et al., 2003, p. 25).
Concrete density
Acrylic latex entrains air and reduces the density of the ensuing cement concrete. Consequently, a suitable amount of antifoam agent is needed to reduce air entrainment. Since the tensile strength of concrete rises with an increase in density, the adhesive, flexural and compressive strengths of concrete can be enhanced by increasing the density of concrete (Kaeding et al., 2003, p. 27).
Curing conditions
Cement concretes modified with acrylic latex must be air-cured to achieve desired physical properties. This process is different from the one used for conventional concrete because the latex must be permitted to combine and form a film to enable it to modify the properties of the concrete in a constructive manner. Thus, when acrylic latex is permitted to undergo appropriate film formation, the potential of enhancing the properties of concrete is realized. Although air-curing is suitable for acrylic latex modified concrete, caution should be taken to prevent rapid drying (in the first 24hours) which can cause the formation of cracks on the concrete surface. Thus, suitable measures must be implemented to impede drying when environmental conditions are unfavorable. For instance, evaporation can be reduced by covering the concrete surface with wet polythene or tarpaulin (Kaeding et al., 2003, p. 25).
Strength
The strength properties of acrylic latex modified mortar are summarized in table 5. The data reveals that acrylic latex admixture enhances tensile strength, adhesion, impact strength, flexural strength, and abrasion resistance. These data suggest that the water-cement ration reduces when the mass of polymer-cement ration is increased. However, Walters (1992) demonstrates that property enhancement can also be realized when a polymer is added to the mixture (Kaeding et al., 2003, p. 28).
Durability
Acrylic polymers are highly durable and resistant to discoloration when exposed to acids or high temperatures. Acrylic polymers are composed of single chains of carbon elements that are not vulnerable to hydrolysis. Although it is possible to hydrolyze the ester side bonds, the main framework of the polymer cannot be breached. Thus, acrylic latexes can be inserted in cement mortars and concretes to achieve lasting durability under wet conditions. Acrylic polymer provides cement mortars and concretes with a considerable amount of water resistance in wet (high alkalinity) conditions. Table 5 summarizes the adhesion and strength properties of cement mortars modified with acrylic latex in both dry and wet conditions. Previous studies have demonstrated that slim acrylic latex-modified cement coatings enhance resistance to cracking, blistering, and surface degradation (Kaeding et al., 2003, p. 28).
Epoxy polymer modifiers
The creation of PMC using epoxy resins varies from other forms of composites modified with the polymer. This is because the polymer is created after the addition of epoxy components to the cement mixture. The benefits of epoxy modifications are the same as those derived from other polymers such as adhesion, tensile strength, and flexural strength (Kaeding et al., 2003, p. 32). The mixture proportioning of concrete modified with epoxy resin is identical to other concretes modified with polymers. Concretes modified with epoxy polymer need less water for mixing compared to conventional concretes. In addition, air entrainment is not needed to enhance resistance to thawing and freezing (Kaeding et al., 2003, p. 33).
Concretes modified with epoxy resins have pozzolans or chemical admixtures. The inclusion of silica fume and fly ash can augment the strengths of concrete modified with epoxy resin. In general, epoxy modified concretes have a high quantity of cement. The usual mixture proportions are presented in table 6. Epoxy resin is incorporated into the Portland cement concrete as a liquid after the concrete is mixed. As epoxy undergoes polymerization, the tiny spherical elements that develop in the hardening paste are interlocked with thin layers of epoxy, producing an uneven (but consistent) three-dimensional network, interlaced all through the cement paste. This network enhances abrasion resistance, tensile strength and flexural strength including reduced permeability of the epoxy modified concrete (Kaeding et al., 2003, p. 33).
Properties of epoxy modified concrete
Compressive strength
The compressive strength of concrete modified with epoxy is somewhat similar to that of conventional concrete that is properly air-cured and with the same water-cement ratio. Nonetheless, the compressive strength can be higher since the surfactant in the epoxy resin has a water-reduction effect that keeps the slump stable (Kaeding et al., 2003, p. 33).
Flexural and tensile strength
The flexural and tensile strength polymer reinforced concrete can be improved up to 100% when the epoxy modification is incorporated into the concrete mixture (Kaeding et al., 2003, p. 33). Table 7 presents typical values computed by Popovics (1974).
Other properties
The elasticity of concretes modified with epoxy resin is lower compared to those of conventional concretes, irrespective of the fact that the former s superior strength. In addition, epoxy modified concretes have superior ductility. What’s more, epoxy-modified concrete mixtures are extremely resistant to chloride-ion penetration (Kaeding et al., 2003, p. 33; Xi & Bazant 1999, p. 58).
Redispersible polymer powders
Redispersible polymers are produced through emulsion polymerization and the ensuing latex is changed to powder form via spray drying process. Examples of redispersible powders are acrylic copolymers, vinyl acetate copolymers, and vinyl acetate homopolymers. After polymerization, the latex is prepared further via the inclusion of various constituents such as application chemicals, spray-drying agents, and bactericides. Application chemicals are composed of materials such as antifoam materials anti-sag agents as well as water-reducing admixtures that influence air content and workability of the concrete composites (Kaeding et al., 2003, p. 35).
Properties of redispersible powder
Redispersible powders are typically white, free-flowing powders. The quantity of ash in the powders is about 10% of the total weight. The ash content (produced by anti-blocking agents) differs with respect to material type. For example, clay and calcium carbonate yield fewer ash contents compared to silica. The size of the powder particles is about 0.08 mm although they are agglomerates and split up when re-dispersed in water to form usual latex particle sizes (Kaeding et al., 2003, p. 35).
Properties of powder-polymer modified mortar
Properties of mortars modified with redispersible polymer powder are slightly reduced than those achieved with latexes of the same composition. Table 8 compares the properties of mortars modified with polymers using VAE (vinyl acetate-ethylene copolymer) in powder and latex form respectively. The concrete mortars were air-cured for between 16 and 24 hours in the mold then stored under laboratory air (about 14 °C and 50% RH) for 27 days. A study by Afridi and Associates (1990) showed that mortars modified with redispersible polymers are resistant to thawing and freezing, a property prevalent in latex modified mortars (Kaeding et al., 2003, p. 35).
Bright et al. (1992) also evaluated the properties of different types of polymers such as vinyl acetate-ethylene redispersible copolymer powders; acrylic copolymer latexes; styrene-butadiene; and vinyl acetate-ethylene when utilized in cement patching compounds. According to the results of the study, vinyl acetate-ethylene redispersible copolymer powders are somewhat similar to the latexes in formulations created using the same water-cement ratios. Hackel et al. (1987) also reported that the properties of concretes produced using VEOVA copolymer powders and vinyl acetate satisfied the conditions for concrete restoration. Decter and Lambe (1992) and Lambe et al. (1990) also evaluated the properties of concrete repair mortars with redispersible polymer powders. The results of both studies showed that these mortars have low drying shrinkage as well as low diffusion properties to carbon dioxide, oxygen, and chloride-ions (Kaeding et al., 2003, p. 35).
Mechanical properties of Polymer Concretes
Compressive strength
Steel and concrete are frequently used as structural materials in construction projects. However, PCs are progressively being utilized as a substitute for steel and cement concrete in many construction projects. Reis (2005) conducted a comparative study to investigate the compressive properties of fiber-reinforced epoxy polymer concretes (p. 357). PC formulations were produced by combining an epoxy resin (20% in mass) with foundry sand. The epoxy resin system used in the study was eposil 551, based on an aliphatic amine hardener and diglycidyl-ether of bisphenol. 1% of chopped glass fibers and 2% of carbon fibers were used in the preparation of fiber-reinforced epoxy polymer concrete (Reis 2005, p. 357).
The researcher used foundry sand (siliceous type) with even grains and a mean diameter of 245 μm. The sand was dehydrated first then incorporated into polymeric resin using an automatic mixer. The introduction of a silane coupling agent (γ-MPS) was done via pretreatment of glass fibers. The trimetoxy group was then hydrolyzed in an aqueous solution and the resultant hydroxyl groups created oxane bonds on the surface of fibers. With the aid of these mix proportions and binder formulations, polymer mortars were combined and shaped into cylindrical specimens as depicted in figure 16. Three cylindrical specimens were produced for each formulation and left to cure for seven days (at room temperature). Afterward, the polymer concrete specimens were post cured for three hours at 70 °C before compression tests were administered. A constant loading rate (1.25 mm/min) was used to perform compressive tests (Reis 2005, p. 358).
According to the results shown in table 9, the compressive strength of epoxy polymer concrete was enhanced by fiber reinforcement. In addition, carbon fiber and glass fiber reinforcements improved the compressive strength of the polymer concrete by 16% and 8.7% respectively. However, both glass fiber and carbon fiber reinforcements did not augment the compressive elastic modulus of the mixtures. Compared to conventional concretes, epoxy concretes display superior values of compressive strengths that range between 17.2% and 33.6%. Likewise, glass fiber and carbon fiber reinforced composites have high compressive strength values ranging between 27.4- 45.3% and 36 – 55 % respectively. The result above shows that the mechanical properties of polymer concretes can be improved through fiber reinforcement (Reis 2005, p. 360).
Flexural strength
Studies done on cement concrete where polymer resins were used as binding materials have revealed that the flexural strength of polymer concretes is influenced by strain rate, temperature, and curing. Given that polymer concretes are somewhat expensive, several studies have been done to determine the lowest amount of polymer resin that can be employed to attain satisfactory flexural strength. Abdel-Fattah and El-Hawary (1999) conducted a study to evaluate various factors that affect the flexural properties of polymer concrete such as ductility, compressive strain, and flexural strength (p. 254).
The researchers used 54 beams (measuring 150 × 150 × 750 mm) in the study. Three control cylinders (100 × 200 mm) for each beam were tested to establish the compressive strength (ƒ1c) of concrete. Three dissimilar types of resin (labeled as type I, II, and III) were employed. Type I and II were based on solvent-free epoxy resin; the former was utilized as a multi-use bonding agent for concrete and the latter for grouts. Type III was based on a polyester resin system and employed as an all-purpose repair agent. The researchers prepared three different composites for each resin. The ratios of resin prepared for each composite were 9%, 12%, and 15% of the entire weight of the mix respectively. Quartzite coarse aggregates and natural sand, measuring 12.7 mm and 9.5 mm respectively, were used. The researchers reinforced 18 beams with 3ɸ10 bars (ρ=0.0042) and another 18 beams with 3ɸ6 bars (ρ=0.0042). The rest of the beams were not reinforced (Abdel-Fattah & El-Hawary 1999, p. 254).
The researchers also reinforced the beams with ɸ6 vertical stirrups (spaced at 25 mm) and fastened them using superior strength wire to prevent shear failure. The properties of steel utilized for flexure reinforcement were: E=210 GPa, ƒu=500 MPa, and ƒy=412 MPa. The properties of shear reinforcement were: E=200 GPa, ƒu=340 MPa, and ƒy=275 MPa. An ordinary concrete mixer was used to mix the materials together and then transferred them into metallic molds. All specimens were vertically cast and shaken on a shaking table. A bar was used to compact each specimen and then vibrated on a shaking table for about 3 minutes. The researchers then de-molded the specimens after 24 hours and left them to cure for 28 days at room temperature. Seven strain gages were attached on each specimen’s surface (fig. 17) to examine strains at various depths of the beams (Abdel-Fattah & El-Hawary 1999, p. 254).
The results of the tests are summarized in table 10 while the variation in the compressive strengths (ƒ1c) for concrete composites is presented in figure 18. The optimal ratio (for resin type I, II, and III) that produced the maximum compressive strength was 12% while the strength reduced at the ratio of 15% for the two types of epoxies. On the other hand, the compressive strength for the polyester used remained stable. The modulus of rupture (ƒr) values for unreinforced polymer beams were significantly higher compared to those for conventional concrete. The concrete composite with 12% resin had the highest value for the modulus of rupture. Figure 19 shows that epoxy type I had the highest ƒr value while the polyester had the lowest value (Abdel-Fattah & El-Hawary 1999, p. 255).
Bond stress
Polymer modification improves flexural strength, tensile and compression strength in polymer concretes. Flexural and tensile strength improves when the transition zone is refined. As a result, the bond between the matrix and the aggregate is improved and the occurrence of micro-cracks is reduced. The polymer matrix (combined with hydrated cement paste) restrains the development of micro-cracks as a result of stress. However, polymer reinforced concretes have a low resistance to fire. In addition, polymer reinforced concretes are somewhat combustible and the bond strength reduces when temperature increases (Kardon 1997, p. 87).
Soroushian et al. (1993) conducted a study to evaluate the effect of different levels of polymer on the modulus of rupture, elastic limit, crack size, and flexural strength under various aging circumstances. The study examined the application of polymer latex in glass-fiber reinforced concrete (GFRC). The impulsion for the study was the observed depreciation of glass fibers in GFRC. The results showed that chemical deterioration was caused by the alkali-silica reaction which happened even in alkali-resistance glass fibers in humid cement conditions given adequate time. The chemical reaction reduced the tensile strength as well as the cross-sectional areas of the glass fiber. It seems that the deterioration was due to the moisture-induced growth of CH (cement hydration) product in filaments of the glass fibers.
The CH bonds with the glass fibers and enhances the bond strength which produces stress risers that result in embrittlement of glass-fiber reinforced concrete. However, when polymer content was increased, the strength of GFRC improved considerably under all conditions. The improvement in GFRC strength was attributed to the bonding of CH as well as the buildup of polymer particles on the fiber filaments which averted alkali attack (Kardon 1997, p. 88).
Differences between Polymer Concretes and Fiber Concretes
Polymer concretes
Polymer concrete comprises aggregate and a polymer binder. In addition, Portland cement is not used in polymer concretes. What’s more, PCs are produced using uniformly graded aggregates to attain close packing so that the spaces between aggregates can be reduced before the polymer is inserted. Applications for PCs include overlays for concrete repairs, precast polymer elements, and cast-in-place polymer concrete bonds for precast concrete production. One major weakness of PCs relates to their susceptibility to high temperatures. PMCs are produced when a polymer admixture is added to conventional cement concrete. The cement concrete and the polymer combine to produce two inter-penetrating matrices that collaborate to improve the material properties of the conventional cement concrete. Polymer-modified concrete generally refers to concrete with low polymer content (5% or less) whereas polymer cement concrete (PCC) typically refers to concrete with more than 5% of polymer content (Kardon 1997, p. 85).
Characteristics of polymer concretes
A typical physical property of PCs relates to their range of glass transition temperature (Tg). When the temperature exceeds Tg, PCs become elastic and undergoes plastic deformation when loaded. When the temperature is below Tg, PC becomes glassy, deforms elastically, and is vulnerable to brittle failure. The influence of polymer’s elastic behavior on the properties of the concrete is determined by the value of Tg. The minimum film temperature (MFT) is another property of polymer concretes. MFT refers to the temperature at which polymerization will produce discrete particles. Thus, the Tg value of polymers used in PCs must be lower than the temperature used to air-cure the composites (Kardon 1997, p. 86).
Polymers are added into PCs in different forms: as a resin; as a redispersible powder; and as latex. When polymers are added as latexes in PCs, the mixture is known as latex-modified concretes (LMCs). The latexes are usually incorporated with other components when the fresh concrete is mixed. When polymers are added as a powder in latex-modified concretes, they are known as redispersible powders because they are produced through the spray-drying polymer process. In addition, they must be converted into latex form before they can be dispersed inside the cement paste. Resins refer to liquid polymers under room temperature and pressure. Resins are usually merged with their catalysts and then combined with fresh concrete. Examples of resins used in PCs are phenolics, furan, urethane, and epoxies (Kardon 1997, p. 86).
Microstructures of PCs
The interactions between the microstructure of polymers with cement microstructure vary, according to the curing conditions, delivery system, polymerization method, and type of polymer. When the polymer is combined with fresh concrete, its particles (suspended in the latex) are scattered within the cement paste. When the hydration of cement begins, the solution is saturated with CH and produces bulky and ettringite CH particles in the area next to aggregates. The particles of polymer settle on the wet clinker particles and gel products. When the hydration process occurs and hydration products increase, the polymer particles steadily fill the capillary pores and form an impermeable layer on the surfaces of the gel products, on the silicate layer over the aggregates, and on the wet cement grains. When the hydration process removes more water, the impermeable polymer particles, entrenched on the gel products, combine to create a co-matrix fused with the dried cement paste and bind the hydrates to the aggregates (Kardon 1997, p. 86).
Fiber concretes
Fiber concretes, also known as fiber-reinforced concretes (FRCs), are produced when discreet fibers are added to Portland cement with aggregates. There are various types of FRCs, such as carbon fiber-reinforced concrete (Tavakkolizadeh & Saadatmanesh 2003, p. 30) and steel fiber-reinforced concrete. The fiber reinforcement can be employed in various forms. For example, it can be used as a tensile membrane to coat the steel reinforcement in order to achieve an efficient orientation of the fibers (Chanh n.d., p. 109).
Steel fiber-reinforced concrete (SFRC) can be created using an ordinary concrete procedure. However, the major problem relates to the insertion of an adequate amount of evenly scattered steel fibers to improve the mechanical properties as well as preserve the workability of the composites. Steel fibers (with a high aspect ratio) can improve the performance of hardened concrete since the fiber-matrix bond is strong. However, the workability of the fresh composite is compromised by a superior aspect ratio. In addition, the problems of even distribution of fibers and workability of the concrete composite grow with increasing volume and length of fibers (Chanh n.d., p. 111).
Mechanical properties of fiber-reinforced concretes
Conventional concretes have micro-cracks and other defects even before the external load is applied. These flaws are caused by thermal and shrinkage strains, plastic settlement, bleeding, and excess water. If not addressed, the micro-cracks can merge to form macro-cracks when a bulky external load is applied. However, the micro and macro-cracks in cement concrete can be prevented by inserting short, unevenly scattered fibers of different materials. When fibers are inserted in the concrete composite, segregation and bleeding are reduced. As a result, the dehydration process is reduced and the overall concrete shrinkage is decreased (Banthia 2007, p. 3).
However, fibers cannot improve the compressive strength of concrete composites to the desirable level. Even in concrete composites that have normal reinforcements, the fibers do little to improve compressive strength. In addition, when carbon or steel fibers are unevenly scattered in the concrete composites, the increase in tensile is insignificant and may range from 0% to about 60%. Therefore, incorporating fibers simply to augment tensile strength is perhaps not useful. However, steel fibers can improve the flexural strength of fiber-reinforced concretes than on either tensile or compressive strength (Chanh n.d., p. 113).
Applications of Fiber Concretes and Polymer Concretes in Industry
Fiber-reinforced concretes
The declining lifetime of concrete structures is a critical issue in the construction industry. The main problem relates to steel corrosion in reinforced concrete structures. Carbonation and chloride penetration seem to be the main cause of corrosion in structures with fiber-reinforced concretes. Therefore, any actions that aim to alleviate carbonation or chloride penetration in concrete composites will considerably improve the resilience of concrete structures. These destructive agents penetrate concrete via permeability, capillary absorption, and diffusion. However, permeability stands out as the main penetration mechanism. Studies have shown that permeability and rebar corrosion occur when cracks develop in concrete. Thus, FRCs can be used to reduce permeability and improve the durability of concrete structures (Banthia 2007, p. 9).
Future prospects for bio-inspired fiber-reinforced concretes
Bio-inspired fiber-reinforced concretes are produced using eco-friendly and bio-degradable natural fibers (i.e. cellulose) which are sustainable. The University of British Columbia is currently conducting research on such composites. According to the provisional results, bio-inspired fibers are extremely effective in construction and reinforcing a sustainable infrastructure (Banthia 2007, p. 10).
The effect of a superficially applied stress on concrete permeability is not well comprehended. Banthia and Bhargava (2007) devised a new method to measure concrete permeability under external stress and assessed the advantages of fiber reinforcement (p. 303). The results of the study revealed that fibers reduced concrete permeability in the absence of externally applied stress. The data of the study also showed that the permeability of fiber-reinforced concretes remained unchanged when external stress was applied (Banthia & Bhargava 2007, p. 306). As a result, fiber-reinforced concretes are promising materials in the construction industry since the fibers suppress cracking and reduce permeability in the concrete. In addition, fiber-reinforced concretes perform well in arid climates as well as in other chemically destructive conditions. As a result, FRC is promising construction material, especially in the Middle East, for improving the durability of structures (Banthia 2007, p. 16).
The applications of fiber-reinforced concretes in the last three decades have been diverse and extensive. Fiber-reinforced concretes are currently used in repairing bridge deck slabs, airport pavements, and pavements and tunnel linings. Future applications of fiber-reinforced materials may also include the current experimental study on roller-compacted concrete strengthened with steel fibers. However, since steel fibers are somewhat costly, the use of steel-fiber reinforced concrete (SFRC) will be limited to special construction projects (Chanh n.d., p. 115).
Polymer reinforced concrete
Polymer reinforced concrete (PRC) is currently used as covers on newly constructed bridges and highways, as well as in the restoration of the existing dilapidated structures. Other uses of polymer-reinforced concretes include overlays on ship decks, pipes, drainage systems, silos, septic containers, swimming pools, and floors (Van Gemert 2004, p. 3). There are two promising applications of polymer reinforced materials in the industry. These are its application as shotcrete and its application together with fiber reinforcing materials. Other future uses of polymer reinforced concretes are: in offshore and marine construction projects; shear wall structures and ductile concrete foundations; and parking bays, highways, and airports. Other future applications of PRCs include the construction of concrete structures that require impermeability, resistance to cracking, and tensile strength (Kardon1997, p. 87).
The combination of polymers with conventional concrete cement produces extremely strong, tough, and long-lasting construction materials that are eco-friendly and affordable. These materials can meet the numerous requirements of the present and future constructions. Structures subjected to dynamic, cyclic, or impact loading, those inaccessible to refurbishment or subjected to harsh environments can benefit from the application of polymer reinforced concretes. What’s more, polymer reinforced concretes can be used to restore depreciating structures. However, there are several challenges that can compromise the application of polymer reinforced concretes. One is the apparently enormous number of various polymers with dissimilar attributes and properties as well as the different methods of their inclusion in mortar and concrete composites. This problem is amplified further by the failure of producers of polymer modifiers to reveal the properties of their products (Kardon 1997, p. 90).
The future prospect for the application of polymer modified materials in sewer conditions cannot be ignored. Sewer pipes are extremely susceptible to attacks by biogenic sulfuric acid that results in severe damage. The acid attack occurs on a microscopic level and is harmful to the C-S-H and C-H constituents in the cement concrete. The application of PRC can avert this problem. First of all, polymer reinforcement prevents large C-H crystals from sulfate attacks. Secondly, the porosity of the concrete used in the sewer pipes is improved by polymer modification. The size of the capillary pores decreases and the polymer film deters the infiltration of bacteria and sulfides. Lastly, since the polymer film is resistant to sulfate attack, it can protect the surface layer susceptible to sulfide attack for a long time which means further corrosion is prevented (Beeldens 2003, p. 158).
One of the major benefits of polymer concrete relates to its ability to reduce vibrations, especially in machine foundations. Several attempts are being pursued currently to apply this benefit in construction structures to manage dynamic loads. Other studies have been done to evaluate the possibility of improving some poor properties of polymer concretes. For instance, studies on resistance to low fire have been conducted to assess the feasibility of reducing combustibility and flammability of polymer concretes. In addition, experiments on the sensitivity of polymer concretes to moisture have also been done. The future prospect for use of polymer concretes in various industries continues to be examined. For example, two future applications include the use of PCs to manufacture precast components such as electrolytic cells, containers for harmful waste materials (i.e. radioactive materials), and synthetic marble; and the use of polymer concretes for producing void-free non-ceramic concrete insulators (Czarnecki 2005, p. 60).
Research on polymer concretes (with both post-mix and pre-mix additives) is currently in progress to establish the effect of different modifiers on the properties and structure of the composite. For PCs with post-mix admixtures, the major sphere of research is producing mixed epoxy cement (polymer cement) binders as well as resin binders that can adapt to the alkaline conditions of the conventional cement paste in the absence of hardeners. For PCs with pre-mix type of admixtures, the main sphere of research is concerned with examining the influence of the lowest temperature required for film-forming for the properties and structure of the composite as well as the production of materials with reduced brittleness (Czarnecki 2005, p. 60).
Fiber Reinforced Polymers
Fiber-reinforced polymers (FRPs) have been used since the 1940s as construction composites by civil engineers to attain notable advantages in the functionality, economy, and safety of structures constructed to satisfy the general requirements of society. However, fiber-reinforced polymer materials have lately attracted the interest of engineers engaged in the erection of civil structures by combining fiber and polymer materials (Bakis et al., 2002, p. 73).
Applications of FRPs
The initial FRP composites incorporated glass fibers entrenched in polymeric resin that was provided by the petrochemical industry after the culmination of the Second World War. The amalgamation of structural fibers with superior stiffness and strength with low-priced, low-density, environment-resistant polymers produced composite materials with superior durability and mechanical properties. For instance, fiber materials with lower density, superior stiffness, and strength (i.e. aramid, carbon, and boron) were used to satisfy the escalating requirements of air travel and space exploration in the 1960s and 70s. As the price of fiber-reinforced polymer materials continues to decline and the demand for dynamic replenishment of infrastructures becomes more and more apparent in the industrialized countries, pressure has increased for the application of FRP materials to satisfy public requirements with respect to the functionality of the infrastructures. As a result, fiber-reinforced materials are widely used in various construction industries. Thus, the future prospects for use of FRP materials in the construction industry are bright (Bakis et al., 2002, p. 73)
Challenges of using FRPs
Several FRP decks are scheduled for use in the future. In addition, there is mounting interest with respect to the application of FRP decks in the future. Nonetheless, a number of technical issues must be tackled first:
- durability and competence of surface overlays (i.e. PC) as well as the use of hot-mix asphalt with respect to the transition temperature of the glass in the PC;
- global buckling modes as well as ultimate strength and failure modes;
- durability properties under both environmental and mechanical loads;
- the performance of panels and connections under fatigue;
- proficient design and properties of joints between panels; and
- development of guidelines and standards of deck design.
What’s more, the application of guardrails remains in doubt and is subject to the changeability of deck designs. The problem encountered in the FRP bridge deck industry is similar to that prevalent in other industries (i.e. concrete and steel) when new products are launched in a competitive market. It seems that the prospect of using FRP decks will be based on their ability to adapt and incorporate benefits of material properties of both FCs and PCs composites (Bakis et al., 2002, p. 78).
Conclusion and Recommendations
The objective of this report was to evaluate fiber concretes and polymer concretes with respect to their types, mechanical properties, admixtures used, and weaknesses. Portland cement concrete has been used as the main construction material for over a century. Nevertheless, Portland cement concretes some weaknesses such as low chemical resistance; large drying shrinkage; low tensile strength; and deferred hardening that can compromise the durability of structures (Islam et al., 2011, p. 55).
There is no doubt that polymer concretes have superior properties compared to those of fiber concretes. As the discussion above has demonstrated, the compressive strength of polymer concretes achieved from the tests described above is higher than those of fiber concretes. In addition, the modulus of rupture for PCs is superior to those of conventional concretes reinforced with fibers with similar compressive strength. What’s more, beams reinforced with PCs have superior flexural strength compared to those reinforced with Portland cement. Consequently, it is highly recommended that the design of construction beams should be done using polymer concretes rather than fiber concretes. The flexural strength of PC beams increases marginally when steel fibers are used as reinforcements. However, when steel reinforcements are incorporated into conventional concrete beams, the flexural strength increases significantly. Furthermore, polymer concretes have a superior ductility compared to conventional cement concretes (Abdel-Fattah & El-Hawary 1999, p. 261).
The advantages of using polymer reinforcement in preventing sulfates attack are diverse. The penetration of harmful substances, such as sulfuric acid, is deterred by the diminished size of capillary pores as a result of polymer reinforcement. Furthermore, the influence of polymer reinforcement on tensile strength, flexural strength, and adhesion strength on cement composites is quite significant. In addition, the compressive strength can be increased if concrete composites are allowed to cure for a longer time to facilitate cement hydration. The best conditions for curing must comprise of an extended period of moisture or water curing, followed by a hydration phase so that the polymer film can develop properly (Beeldens 2003, p. 159).
Both fiber concretes and polymer concretes have useful applications in the construction industry. For example, FRCs are promising construction materials in reducing cracking and permeability in the concrete. Some uses of FRCs include repairing bridge deck slabs, pavements, and tunnel linings. Furthermore, FRC works well in arid as well as chemically destructive environments. Consequently, it is a promising construction material especially in the Middle East for long-term concrete structures. However, concrete composites reinforced with steel or carbon fibers are susceptible to steel corrosion, carbonation, and chloride penetration. Thus, any efforts to prevent these harmful substances will considerably improve the resilience of FRC structures (Banthia 2007, p. 9).
On the other hand, polymer reinforced concretes are used as covers on newly constructed bridges and highways, as well as in the restoration of existing dilapidated structures. PRCs are also used as overlays on ship decks, pipes, drainage systems, and septic containers. The future uses of PRCs include applications in marine construction projects as well as in shear wall structures and ductile concrete foundations. Other future applications for PRC include the construction of concrete structures that are impermeable and resistant to cracking (Kardon1997, p. 87).
One major problem associated with future applications of FRC is the scarcity of knowledge about polymers. As noted above, polymers are used to produce new concretes and restore the existing ones. Polymers are frequently used in restoring concrete structures without lending credence to the root cause of the damage. In addition, adequate preparations are not done before the damaged structure is repaired. What’s more, polymers are used in the construction of new concretes without taking into account the function of the polymer-modified material. When such information is ignored and the composite fails, the polymer is blamed. However, the main problem rests with the individuals conversant with polymers but have insufficient knowledge about the construction materials. In addition, individuals familiar with construction materials have limited knowledge about polymer technology. Therefore, a clear grasp of knowledge about concrete material science will enable one to use PRCs as effective building composites (Kardon 1997, p. 91).
From a technical point of view, the requirement for regulations and standards for fiber-reinforced polymer stems from their considerable dissimilar physical and mechanical properties compared to other ordinary building materials. Currently, efforts are underway to develop the standards and regulations to guide the application of FRP materials in construction. These efforts are mainly inspired by the apparent demand for cost-effective, improved materials for retrofitting and restoring structures that are dilapidated, outdated, or situated in seismic regions. In other situations where the demand for new materials is somewhat ambiguous from a temporary economic point of view, standards and regulations will aid in the application of FRP composites to facilitate the acquisition of long-term knowledge. This knowledge may ultimately result in the acquisition of pledged life-cycle cost advantages of fiber-reinforced polymer materials by both the structure owners and designers of FRP materials. Given that the lack of adequate standards and regulations affect FRP bridge decks and shapes, future explorations on the standards and the regulation should therefore lend more credence in these areas (Bakis et al., 2002, p. 84).
In addition, educating structure owners, construction employees, and civil engineers on diverse pertinent facets of fiber-reinforced polymer technology will play an integral role with respect to the successful application of these materials in the building. Nonetheless, it must be underlined that in spite of the expected modest decline in the outlay of fiber-reinforced polymer composites; the application of these materials will be principally limited to those uses where their exceptional properties are critically required (Bakis et al., 2002, p. 85).
References
Abdel-Fattah, H & El-Hawary, M 1999, ‘Flexural behaviour of polymer concrete’, Construction and Building Materials, vol. 13, pp. 253-262.
Bakis, C, Bank, L, Brown, V, Consenza, E, Davalos, J, Lesko, J & Machida, A 2002, ‘Fiber-Reinforced Polymer Composites for Construction: State of the Art Review’, Journal of Composites for Construction, vol. 6, no. 2, pp. 73-87.
Banthia, N 2007, Fiber Reinforced Concrete for Life Time Engineering of Civil Infrastructure, University of British Columbia, Canada.
Banthia, N & Bhargava, A 2007, ‘American Concrete Institute’, Materials Journal, vol. 104, no. 1, pp. 303-309.
Beeldens, A 2003, ‘Influence of polymer modification on the behavior of concrete under severe conditions’, Structural Concrete, vol. 4, no. 3, pp. 155-162.
Chanh, V n.d., ‘Steel Fiber Reinforced Concrete’, pp. 108-116.
Czarnecki, L 2005, ‘Polymers in Concrete’, Concrete International, pp. 55-61.
Ebead, U & Neale, K 2007, ‘Mechanics of fibre-reinforced polymer concrete interfaces’, Canadian Journal of Civil Engineering, vol. 34, no. 3, pp. 367-377.
He, X & Shi, X 2008, ‘Chloride Permeability and Microstructure of Portland Cement Mortars incorporating Nanomaterials’, Journal of the Transportation Research Board, vol. 3 no. 2070, pp. 13-21.
Hou, J & Chung, D 2000, ‘Effect of admixtures in concrete on the corrosion resistance of steel reinforced concrete’, Corrosion Science, vol. 42, pp. 1489-1507.
Islam, M, Rahman, M & Ahmed, M 2011, ‘Polymer-modified Concrete: World Experience and Potential for Bangladesh’, The Indian Concrete Journal, pp. 55-63.
Jennings, H 2000, ‘A Model for the Microstructure of Calcium Silicate Hydrate in Cement Paste’, Cement and Concrete Research, vol. 30, no. 1, pp. 101-116.
Kaeding, A, Maass, J, Anderson, M, Ball, J, Bartholomew, J, Bodea & Depuy, G 2003, Polymer-Modified Concrete, American Concrete Institute, Farmington Hills.
Kardon, J 1997, ‘Polymer-Modified Concrete: Review’, Journal of Materials in Civil Engineering, vol. 9, no. 2, pp. 85-92.
Lie, T & Kodur, V 1996, ‘Thermal and mechanical properties of steel-fiber reinforced concrete at elevated temperatures’, Canadian Journal of Civil Engineering, vol. 23, no. 4, pp. 511-517.
Ohama, Y 1995, Handbook of polymer-modified concrete and mortars: Properties and Process Technology, Noyes Publications, Park Ridge, N.J.
Reis, J 2005, ‘Mechanical Characterization of Fiber Reinforced Polymer Concrete’, Material Research, vol. 8, no. 3, pp. 357-360
San-Jose, J & Frias, M 2007, ‘High performance polymer concrete’, Mater. Construcc, vol. 57, no. 286, pp. 29-39.
Sofia, M, Van Deventer, J, Mendis, P & Lukey, G 2007, ‘Engineering properties of inorganic polymer concretes’, Cement and Concrete Research, vol. 37, pp. 251-257.
Taucer, F, Spacone, E & Filippou, F 1991, A Fiber Beam-Column Element for Seismic Response Analysis of Reinforced Concrete Structures, University of California, Berkeley.
Tavakkolizadeh, M & Saadatmanesh, H 2003, ‘Strengthening of Steel-Concrete Composite Girders Using Carbon Fiber Reinforced Polymer Sheets’, Journal of Structural Engineering, vol. 129, no. 1, pp. 30-40.
Tennis, P & Jennings, H 2000, ‘A Model for two types of C-S-H in the microstructure of Portland cement pastes’, Cement and Concrete Research, vol. 30, no. 6, pp. 855-863.
Van Gemert, D, Czarnecki, L, Lukowski, P & Knapen, E 2004, Cement Concrete and Concrete-Polymer Composites: Two Emerging Worlds, Warsaw University of Technology, Poland.
Xi, Y & Bazant, Z 1999, ‘Modeling Chloride Penetration in Saturated Concrete’, Journal of Materials in Civil Engineering, vol. 11, no. 1, pp. 58-65.
Appendix
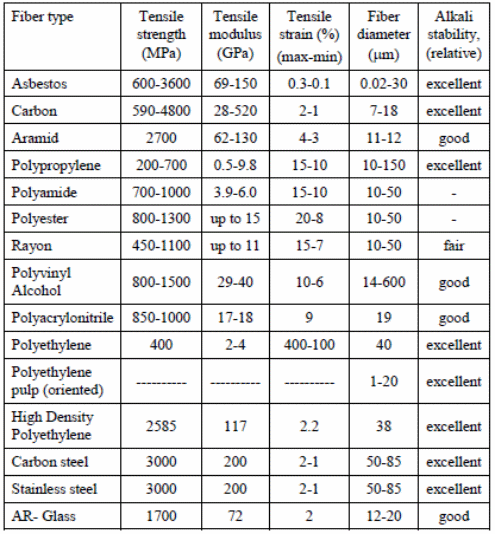
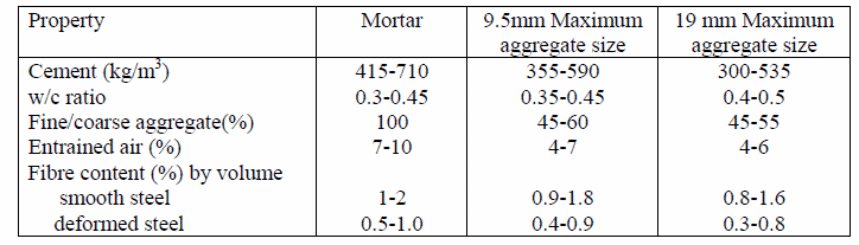
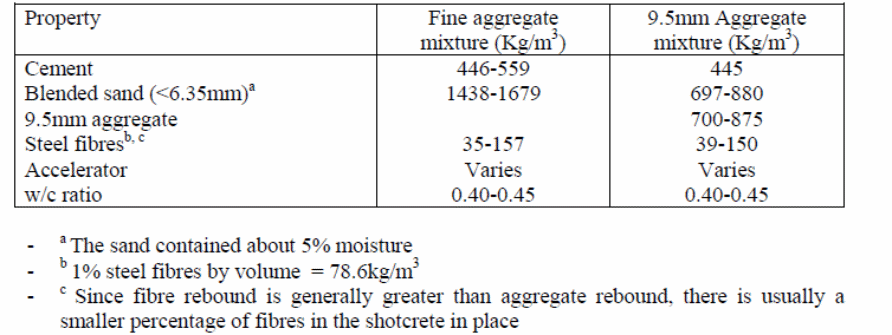
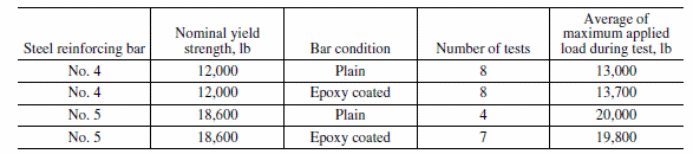
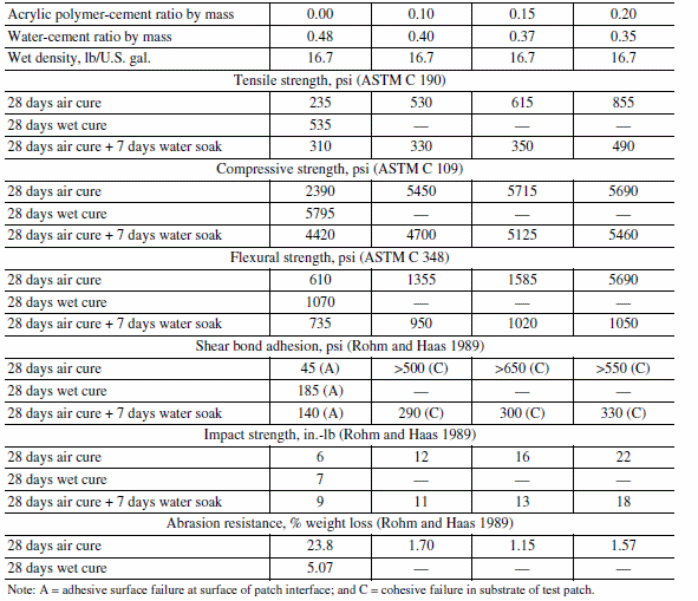
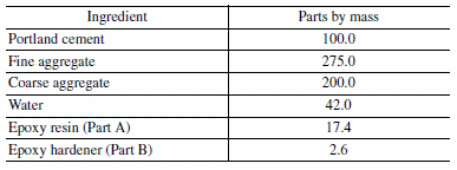
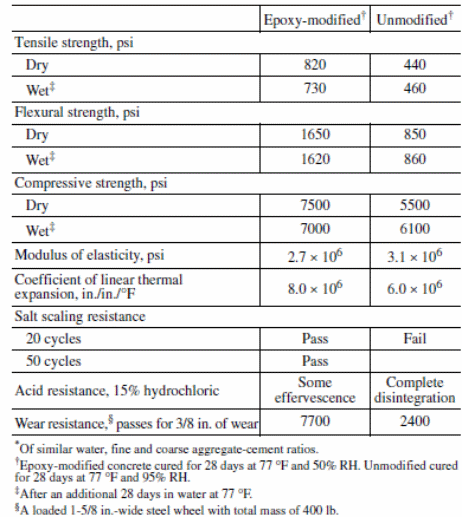
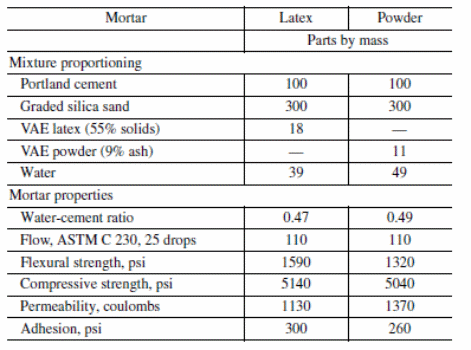
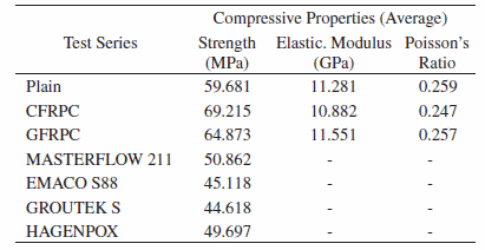
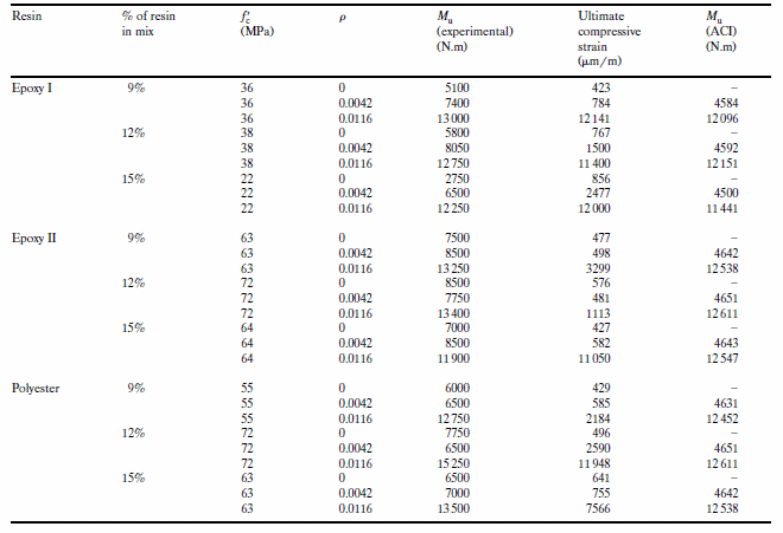
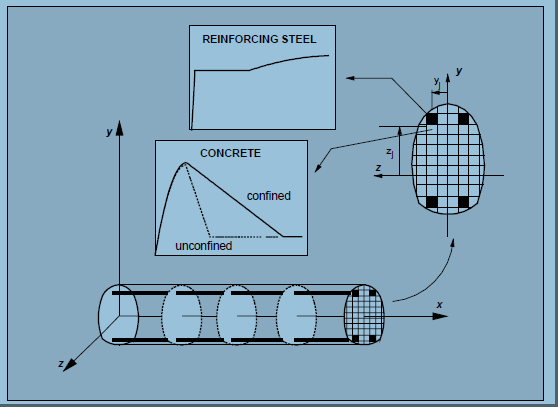
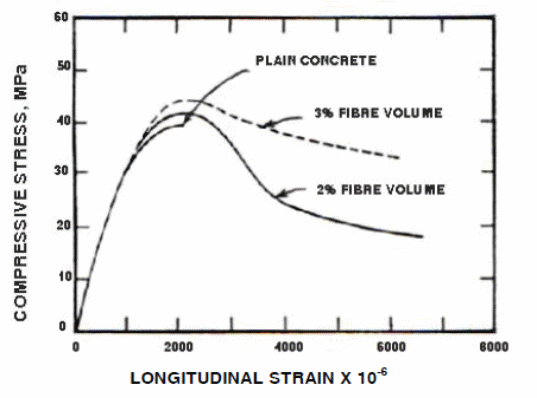
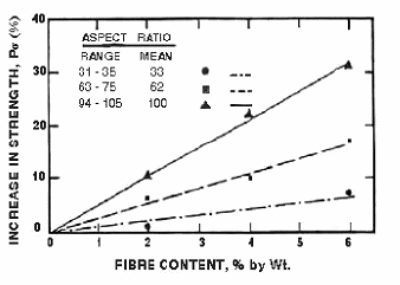
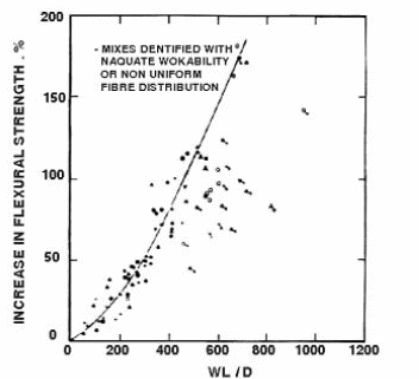
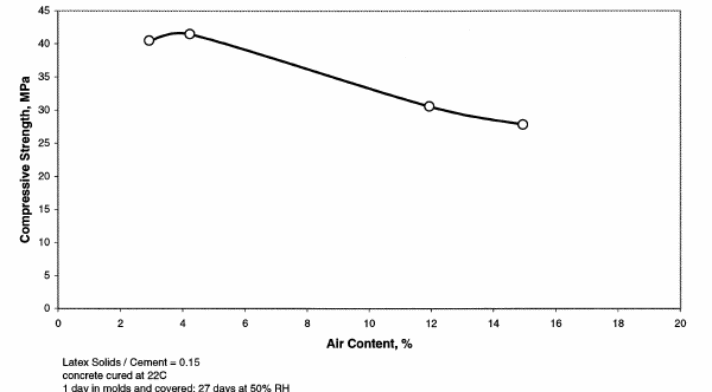
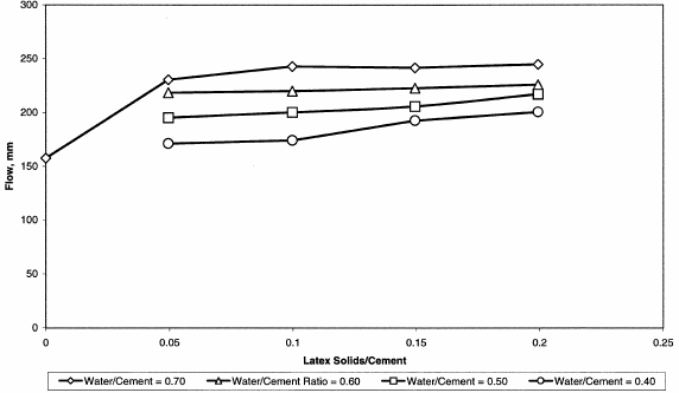

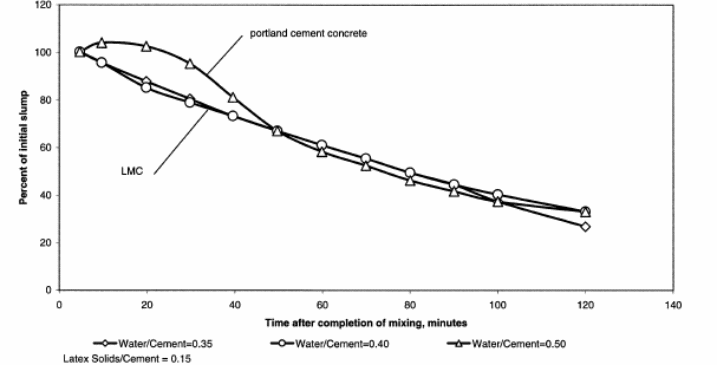
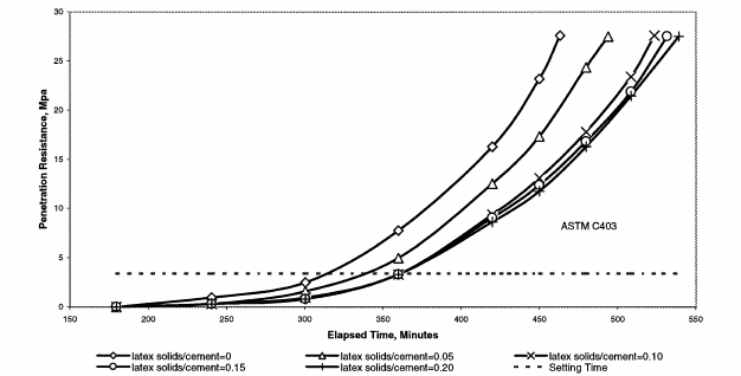
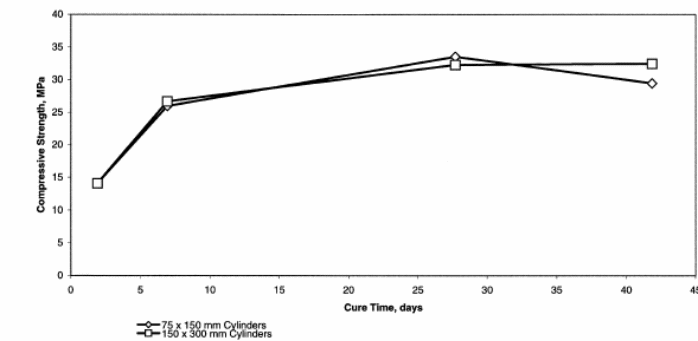
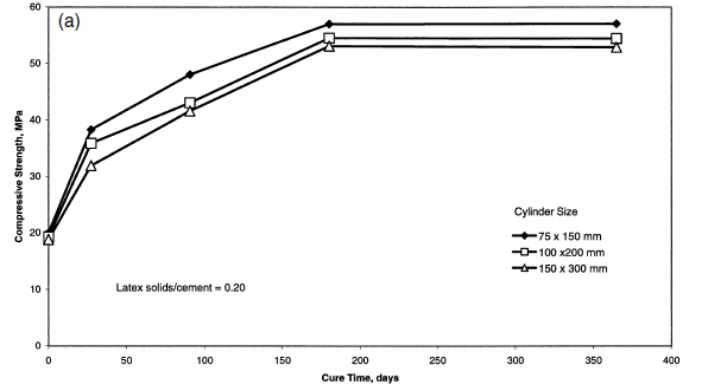
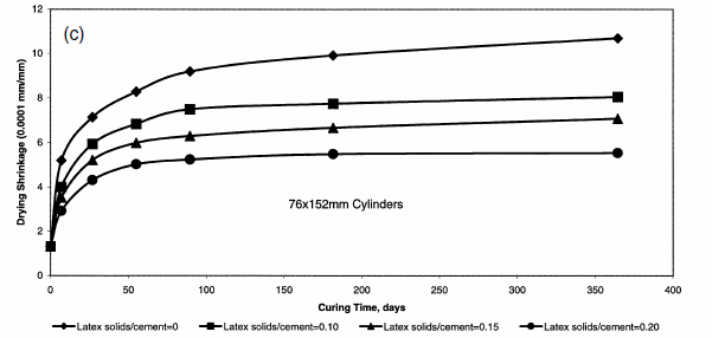
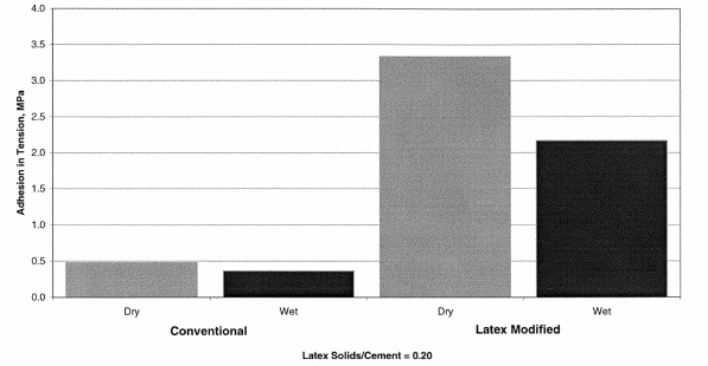
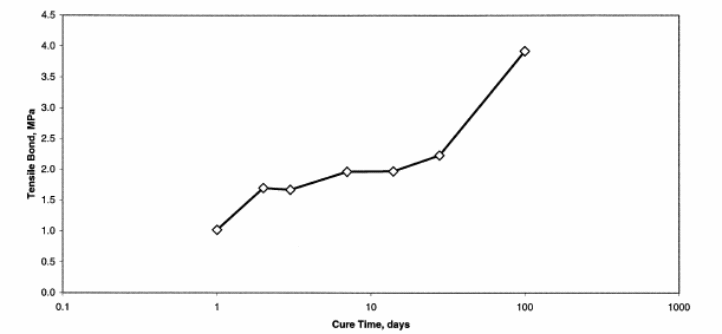
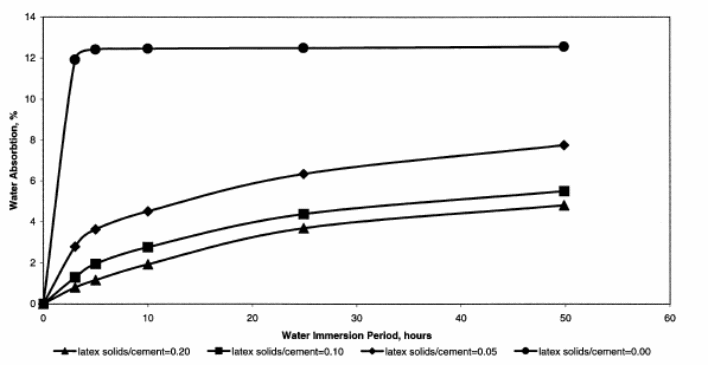

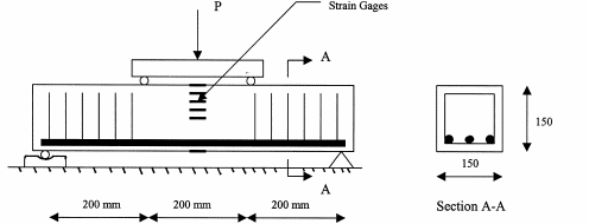
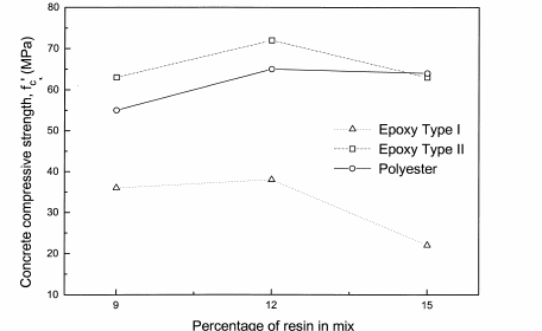
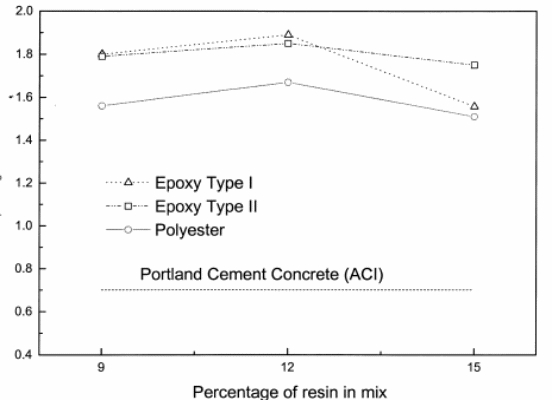