SIPOC diagram (High-level process map)
The term SIPOC stands for Suppliers, Inputs, Process, Outputs, and Customers. It is a tool employed in the six sigma style for proper identification of processes and any improvements required before the real work on the project commences. The voice of the customer (VOC) initializes the beginning of the SIPOC process. The six sigma style has several phases, including the definition; measurement; analysis; improvement, and control phases (also known as DMAIC). It is applicable during the measurement stage to help in determining the outputs and the targeted customers who gain from the results of the process. Basic steps of the processes involved in improving or coming up with a new project are clearly outlined. When creating the SIPOC diagram, the basic step is usually determining the critical processes involved, then the outputs of the project, the customers, inputs then suppliers.
The suppliers, whether internally based on the company/ organization or externally based give the required inputs to the process. These include raw materials, information; forms, and etcetera. The inputs to the process include staff and the supplied materials. The process involves the detailed step by step method of carrying out a project. The focus on the process method is to make sure its output adds value to a customer or his/her needs and expectations are met. The output is the result of the process, such as a finished product or service sold to customers. The customer is the person receiving the good or service. Majority of the time, customers’ response to the provided product results in the improvement or betterment of the product. SIPOC aids the organization in:
- Clarification of the project’s scope.
- Setting borders of the project’s work scope such as the first and end time.
- Determining the ways and rules involved and all the factors tackled.
- Ensuring the right and enough resources are provided and evenly distributed.
- Securing funding from the government or other financial institutions.
An example of a SIPOC diagram showing the SIPOC procedure for repairing a damaged car is shown in figure 1.
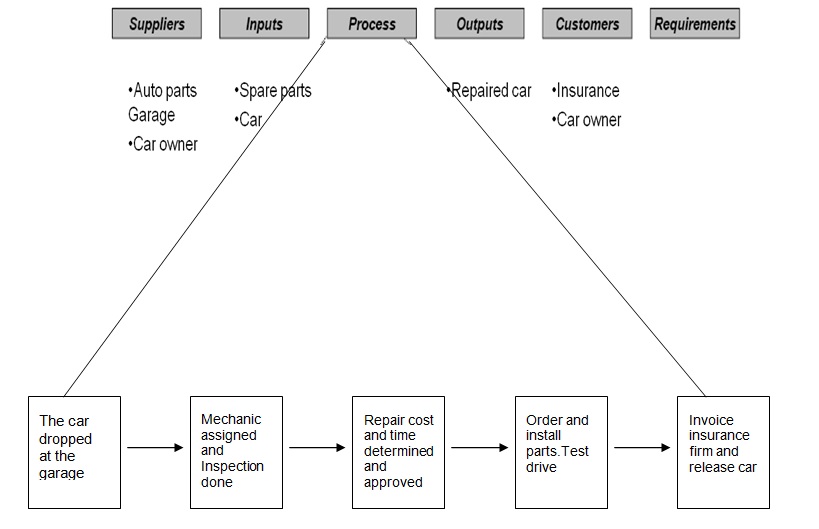
Significance of the term “process owner”
A process owner is a person who is in charge or responsible for coordinating teams to make sure the goals of the project are met or the process (in the SIPOC diagram) runs smoothly from beginning to end. The teams involved in the process all work together in completing a single process. In the SIPOC diagram in figure 1, the process owner could be an automotive engineer at the garage responsible for ensuring cars brought in are repaired to the customer’s satisfaction as well as ensuring the garage gets adequate compensation for the work done. The responsibilities and significance of the automotive engineer include:
- Determining and defining the reasons for undertaking the repair on the car. This is through visual inspection (together with staff from the insurance company) of the car, the nature of the damage, repair cost, and time required for completing the work.
- Ensuring that the company can undertake the repair works completely and comfortably. This could be in terms of its structure or finances or the make and type of cars it can handle and repair.
- Ensuring an equal distribution of resources and assigning different mechanics for various stages of the repair, such as mechanics involved in panel beating and spraying, those involved in engine repair and assembly, and etcetera.
- Ensuring that he is constantly updated on any new developments or problems arising from the repair work.
- Ensuring the mechanics involved can meet the company’s targets as well as finish the work on time and provide quality work surpassing the customer’s expectations.
- Preparing reports to the company and insurance firm on the nature of repairs done on the car and communicating to them on any changes made during the entire process.
- Preparing the last invoice to the insurance company for payment.
- Test driving the car to make sure it has been repaired well and releasing it to the car owner.
When the process owner carries out his duty effectively, the output in the SIPOC diagram enables the car owner to be satisfied, and thus, quality service is provided to the owner.
Kano’s VOC model
The Kano VOC model is a tool used for articulating the customer’s voice through the prioritization of the critical to quality features (CTQ). The customer gives his or her perception and observations of the goods and services. Three main customer needs are usually addressed in this model. These are:
- Must be- the customer normally expects some of his/her needs to be met. If there is a lack of these needs, he/she automatically becomes unsatisfied i.e., this need is a measure of the quality of the service or product being sold and lack of fulfillment forces the customer to look for it elsewhere.
- More is better/performance- in this model, the customer may be satisfied, and the more the needs are met, the better and the more he/she will be satisfied.
- Delighters- no dissatisfaction is caused by the lack of these needs. The customer will view these needs as a gratuity and his/her expectations will still be met.
The Kano’s VOC model enables the organization or company to selectively decide on the products or services it can sell, their specifications, the kind of improvement to be done to meet the customer needs, and discover what factors make the customer happy.
An example of the Kano VOC model is shown in figure 2.
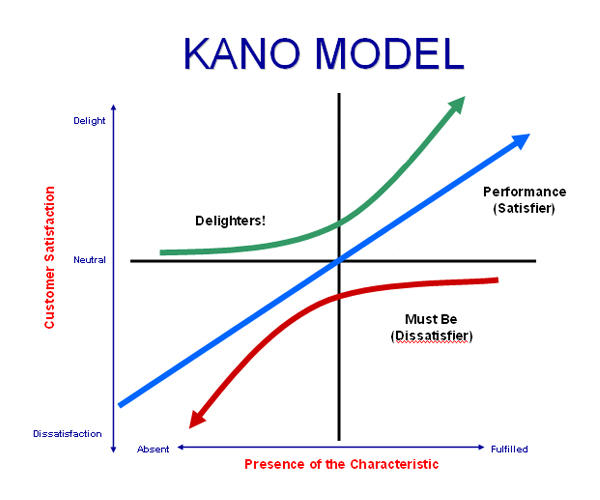
Kano VOC model is applicable when renting out a room at a hotel. When a customer wants a room at a hotel, he/she expects a bed, shower or bathtub, and breakfast. These are the must be needed in the Kano model, otherwise, the customer will look for another hotel. The performance or more is better needs include: friendly room prices, the locality of the hotel, a restaurant offering good food and a fast mode of checking in and out of the hotel. The delighters include internet in the rooms, a swimming facility, Jacuzzi, and a gym. These needs are summarised in table 1.
Table 1: Example of Kano VOC model.
Difference between customer need and customer requirement
Customer needs refer to an essential service or product that the user cannot live without. It is determined by the present state of the customer and what he intends to eventually have, i.e. his goal, and his present mission or situation. In the Kano model, the customer’s needs are the must be and performance needs.
Customer requirements refer to any good, asset, or service that must be provided to satisfy the needs of the customer, i.e. the customer’s requirements are derived from his needs. The customer requirements are the must be needed in the Kano model.
Relating the endeavor for excellence with Kano’s model (Dimension Three)
Kano’s model is used for articulating the voice of the customer. When the customer’s needs are sufficiently met beyond expectations or the needs are met to his/ her satisfaction, the tendency of shifting elsewhere is minimal. When a company offers delighters to customers, the feedback from them is always positive and through word of mouth, the business tends to grow due to an influx of many customers who bring in a lot of business. The company’s profit will tend to increase resulting in excellence. Moreover, the application of the Kano VOC model helps the organization in improving the quality of its products and services by combining with the SIPOC model.
The Pareto chart
The Pareto chart uses the 80/20 rule. When it comes to ways of improving the quality of products or services of a company, analysis is done based on the major causes of the problems (80%) and the few reasons that caused the problem (20%).
The Pareto diagrams for the error codes of the diskettes for the five days are shown in figures 3, 4, 5, 6, and 7.
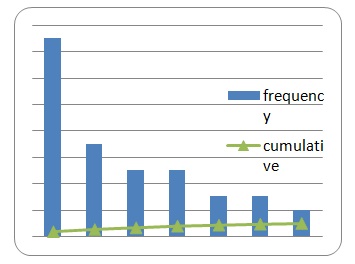
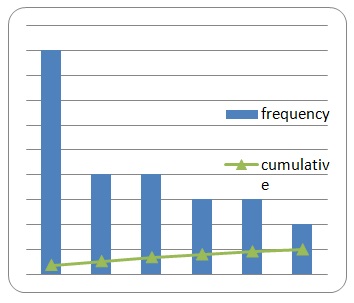
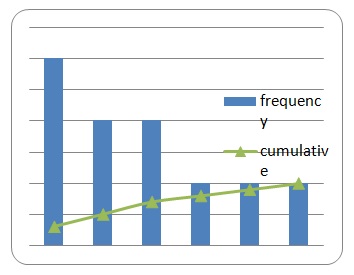
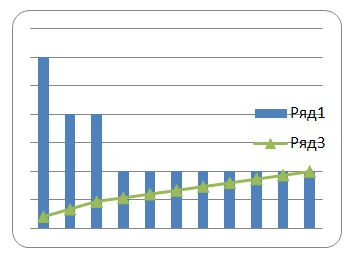
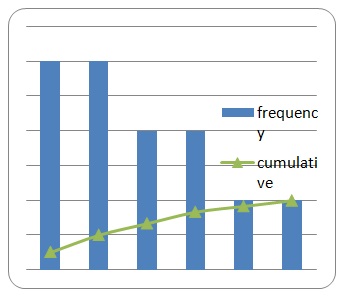
Figures 3 & 4 show the largest code to produce errors was code 410 while figures 3, 4, 6 &7 show the second-largest code to produce errors was code 413. Applying the Pareto principle of the 80/20 rule, it is observed that more than 20% (about 50-60%) of the codes account for 80% of the errors. Thus the Pareto rule does not hold in the production of the diskettes besides the fact that the codes generated reduced with subsequent days. Moreover, the diagrams illustrate that the most frequent codes to be generated as errors were code 410 and code 413 hence measures to reduce their generation were proposed. Code 841 is the least error code generated during the five days.
The measures to be put in place to reduce the errors or improve the quality of the diskette drive include:
- Providing training to workers so that their growth and development is enhanced. This goes a long way in honing their skills thus improving the quality of the output. Furthermore, the workers can come up with new ideas and methods of reducing the errors.
- Employing new technology in the production process of the diskettes or using newer technology such as the compact disc technology other than the diskette technology.
- Ensuring that there is a quality check at each stage of the production process for error minimization.