Executive Summary
This recommendation report analyzes the production and logistical system of Richard & Trench to identify its major flaws and weaknesses, as well as propose a program of improvement to ensure that the company can produce and supply a set amount of semiconductors in a given time frame. The necessity for this report was brought upon by a large contract signed between Richard & Trench and a leading electronics company, requiring 3 million semiconductors to be supplied to them annually. It is a very important contract that could define the company’s future as a leader in the market of semiconductors.
The preliminary analysis of the company’s production, management, and logistics operations indicated several critical weaknesses. These weaknesses are the lack of quality control criteria for raw resources, an error in the automated quality control that could send a large number of half-completed semiconductors back, and the inefficient design of the warehouse for complete products, which could potentially be improved to house 6 million conductors instead of 3 million.
Other weaknesses of the system include the overreliance on one supplier for raw materials and inefficient supplying schedules that require the use of large warehouses. The transportation system is also inefficient, as the distances between the factory, the packaging facility, and the warehouses are too long and cause unnecessary time delays.
Two potential models could be adopted by Richard & Trench to counter these areas of weakness; the JIT model, which stands for Just-in-Time management, and the WCS model, which stands for Work Control System. The former relies on lean management and tight coordination between the production team and the suppliers to bypass the need for warehousing, while the other operates within the confines of the standard supply system but regulates the input and output of production to hold leaner stock and improve production times.
As the analysis showed, JIT would offer a cheaper alternative and help improve production times greatly, while at the same time solve the warehousing problem by rendering it obsolete. However, JIT is also prone to critical malfunctions and increases the overall production costs of the products. WCS would require greater investment in the construction of all necessary facilities near the factory, but will prove to be more stable and efficient in the long run, and would require fewer resources and training to implement. The report concludes that repairing the existing errors, as well as implementing the WCS system of management, would greatly enhance the company’s production rates and the quality of the product. The estimated costs for the implementation of the WCS model, warehouse construction, and personnel training, is estimated at 1,500,000 dollars.
Richard & Trench Recommendation Report
Introduction
Production planning and optimization play an important part in any production enterprise, big or small. Optimizations allow the company to reduce costs, improve production levels, increase the quality of the end product, reduce the number of workers required in the process, and promote labor safety. Periodic assessments of production efficiency are necessary, as no system is perfect and there are always ways to improve.
This recommendation report involves a case study of a company called Richard & Trench – a rising semiconductor company based in the USA. It has a 14-year history in the market and produces high-quality semiconductors, which are highly sought-after by many of the leading electronics companies. The company acts as a first-tier supplier to many high-tech ventures and manages to attract the attention of large contractors.
This case study illustrates a plausible real-life scenario. Large companies often employ services of smaller sub-contractors to supply all the necessary components. This is done to diversify its supply chain and becomes less dependent on just one supplier. The client company set up an annual production order of 3 million semiconductors, with a hard condition of not accepting any setbacks or delays. The purpose of this paper is to assess the company’s production chain, develop recommendations based on the initial assessment, calculate possible optimization costs, improvements, and drawbacks to the system, and, ultimately, develop a working change model for the company.
Current Production Chain Assessment
The assessment process was conducted over 2 months and involved a team of 5 people – two mechanical engineers, one finalist, one quality management expert, and the operation supervisor. The team was granted access to all areas within the company, use of their research facility, and a research fund of 10,000 dollars.
This inspection team made several key discoveries. The current production system involves four facilities – the raw materials warehouse, the packaging facility, the complete product warehouse, and the factory itself. These facilities, however, are not located in the same place. The raw materials warehouse is located 1 km away from the factory, the complete product warehouse is 3 km away, and the packaging facility, 1.5 km away. This creates complications and adds time to the production process as the raw materials and the products have to be transported to and from the factory.
The choices of locations for the packaging and the warehouse facilities, as well as their sizes, are motivated by the current supply and production system. As it stands, the materials are supplied by a local company on a bi-monthly basis. The production capabilities of the factory are large, capping at 6 million semiconductors a year, meaning that the number of materials supplied each time is also significant and requires a large storage facility. At the same time, the packaging facility needs to be equally large, as it has to deal with large amounts of products simultaneously. Actual production rates for the factory are at 5 million semiconductors a year, with 1 million lost due to imperfections in the raw resources supply and delivery, as well as the distances between the facilities. The holding capacity of the complete product materials warehouse is 3 million semiconductors. The report concluded, however, that the redesign of this warehouse space could potentially double its holding capability.
The investigation of the actual production process discovered serious flaws in the processes of the raw material and final product quality control. Silicon, which is one of the key raw materials for the production of semiconductors, is investigated manually, but with no official protocols followed for quality control. This can potentially result in a decrease in the quality of the end product. Another flaw involving the production process involves an error in the automated semiconductor manufacturing that sends a significant number of half-finished semiconductors back should the machinery detect an error in a finished semiconductor during the testing phase.
The estimated time and costs for the reparations are 15 days and 350,000 dollars. Although the potential production errors may cause unnecessary delays and pauses in the process, fixing the issue will not directly improve the production values of the company. However, it would increase the quality of the final product and diminish the chances of a malfunction shutting down the manufacturing schedule.
Aside from the abovementioned issues, the review found no other potential problems that might hinder the completion of the 3-million yearly order from the client company. Even with the 1-million difference between the potential and the actual production values, Richard & Trench can complete the full order, and even have a production reserve ready, in the case of a sudden increase in workload.
Weaknesses of the Current Logistics and Production Model
While the current logistics and production model has been operating for some time, several possible weaknesses may jeopardize the new order and put the reputation of Richard & Trench at risk. The first flaw in the current model is the overreliance on a single supplier for the raw materials that enable the company to produce semiconductors. This puts the production schedule at great risk, as it relies not only on the company’s own ability to produce semiconductors but also on the supplier’s ability to supply the raw materials in large quantities.
The production of larger quantities of goods requires the involvement of greater production values on the part of the supplier and is thus prone to setbacks on a larger scale. For example, if the supplier suffered a malfunction or a large-scale accident that would halt its production, Richard & Trench would be left without any raw materials for an uncertain amount of time. The same would happen if the supplier’s storage facilities were to suffer an accident. Lastly, any accidental payment issues on the customer’s part, as well as sudden changes in the order, are also likely to cause unnecessary delays.
Another problem involves the size of the complete product warehouse. As it stands, it can hold 3 million complete semiconductors. While this is sufficient to satisfy the customer’s order, it is only one-half of the maximum production value of the company, thus meaning that other orders may find themselves without storage space. Depending on the logistics model, the warehouse would need to be remodeled to fit greater volumes of products, which would cost time and money. Lastly, storing large amounts of products and materials in warehouses potentially increases the damage dealt from an accident or an emergency, such as a flood, fire, or a large-scale equipment malfunction. Large distances between the factory and the facilities increase the chances of deliveries being delayed or damaged due to traffic accidents.
Potential Solutions
Potential solutions to the weaknesses of the logistics and production system may involve implementing a different inventory management system. This could smooth out the production and supply flow, as well as make it less reliant on the suppliers, and less susceptible to potential disasters that may result in Richard & Trench being unable to provide the semiconductors on time and, thus, violate the terms of the contract with their client. The two working inventory management systems that could be applied for this kind of organization are the JIT system and the WCS system.
The JIT system revolves around a lean management model. This means that the materials are delivered from the supplier and are immediately put into the production process, with little to no warehousing required. This system is implemented by many companies across the world as it allows savings on warehouses, warehouse employees, and transportation fees. Also, it creates a more fluid system and eliminates extra wait times and manipulations with the product and the material, which would enable increasing the production value of the company (“Just-in-Time”). A comparison between the traditional production system and the JIT production system is well-illustrated by the diagram below (Pic. 1):
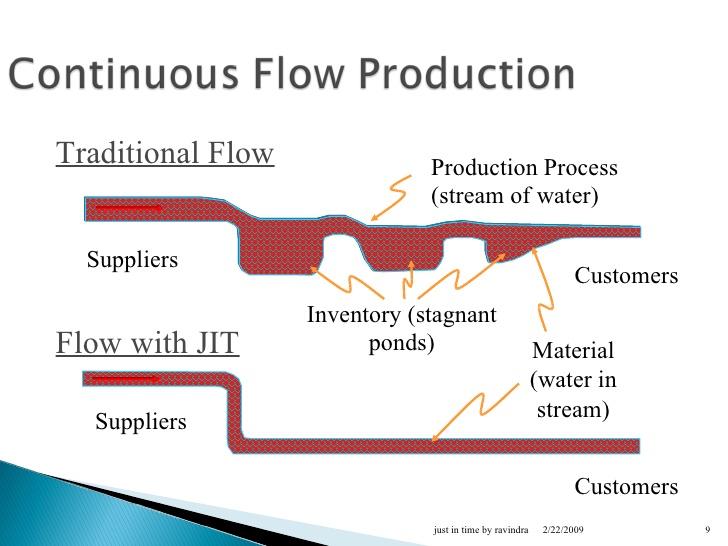
Another system that could be implemented by Richard & Trench is the WCS management model. This model revolves around managing the customer’s demand and adjusting the input and output of the system according to each customer inquiry. It is a system largely implemented by small and medium-sized companies, as it allows them to reduce lead times, control the capacity of the enterprise, and control work-in-progress and the inventory, thus resulting in leaner warehousing and management. It is also relatively simple to implement (“Workload Control”). For easier understanding of how WCS works, see Pic.2 below:
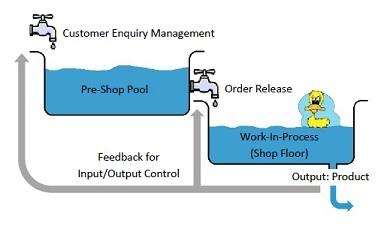
Pros and Cons of JIT and WCS
As has been mentioned, the JIT system would allow the company to remove warehousing facilities from the equation, as they would be able to receive the raw materials upon demand and send the products to the customer as soon as they were manufactured. As it currently stands, the company has four major facilities, two of which are warehouses. With this system, these warehouses require modernization and expansion, particularly in the case of the warehouse for storing the finished products. The adoption of the JIT system would allow the company to close down these warehouses and open smaller ones within the vicinity of the factory, thus saving money on both the maintenance and transportation of the larger warehouses and potentially speeding up the production. However, this system has certain risks. A smooth and steady supply of materials on demand requires greater cooperation between the company and the material supplier. Instead of only having to rely on the supplier for large shipments twice a month, the company has to rely on the supplier every day to produce semiconductors on-demand. The number of transactions is thus increased, and so is the chance of these transactions failing and causing a material shortage. This could jeopardize the company in the event of a major accident or a disagreement between Richard & Trench and the suppliers.
WCS, on the other hand, can be applied to the current system without significant modifications. The company would still operate in terms of warehouses and large-scale orders. By managing customer orders and inquires, the company would be able to reduce warehousing, though not eliminating it, as well as reduce lead times, which would help save money. This system is easier to implement than JIT and does not require the same levels of coordination. At the same time, producing in larger quantities would help reduce the individual price for the semiconductor, as the company would operate economies of scale – the price of production per individual product will decrease with the increase in production. Also, the company would be more resilient to sudden changes and increases in production. However, there is a downside to this method as well. WCS would require closing the existing warehouses and constructing new ones in the direct vicinity of the factory. These warehouses would be bigger than with the JIT system and would cost money, time, and land to build them on.
Applying JIT and WCS to the Richard & Trench Case
When comparing JIT and WCS in regards to the Richard and Trench case, it is important to consider both short-term and long-term perspectives. JIT will provide immediate monetary savings for the company, as the necessity for having warehouses will vanish. The majority of employees working there would thus become unnecessary, all maintenance costs will be cut as these warehouses would no longer need to be supplied with water and electricity, and all the machinery utilized in the warehouses could be repurposed or sold. Much smaller warehouses for managing insignificant loads and material stockpiles could be set up within the factory building or right next to it, which would significantly cut transportation times and improve the workflow.
However, switching from the standard operational and logistics management towards a leaner system of management like JIT will take time. Working schedules would need to be rehashed, and the suppliers would also need to adjust to the new supply schedule. Warehouse workers would need to be remunerated for losing their jobs, the warehouses themselves would need to be sold or rented, and the management system would have to be reconfigured to operate at peak efficiency, to prevent materials from stockpiling, instead of being sent directly into production. This would cost time and money. It is estimated that the shift towards JIT would take from two weeks to about a month.
Another potential downside of JIT is that it will diminish the overall profits of Richard & Trench while working with a large order of 3 million conductors per year. The Just-in-Time system is geared towards manufacturing and managing of multiple small orders coming in at different and unexpected times. Some examples of successful JIT implementation include companies like Toyota, Dell, and McDonald’s (see Pic. 3):
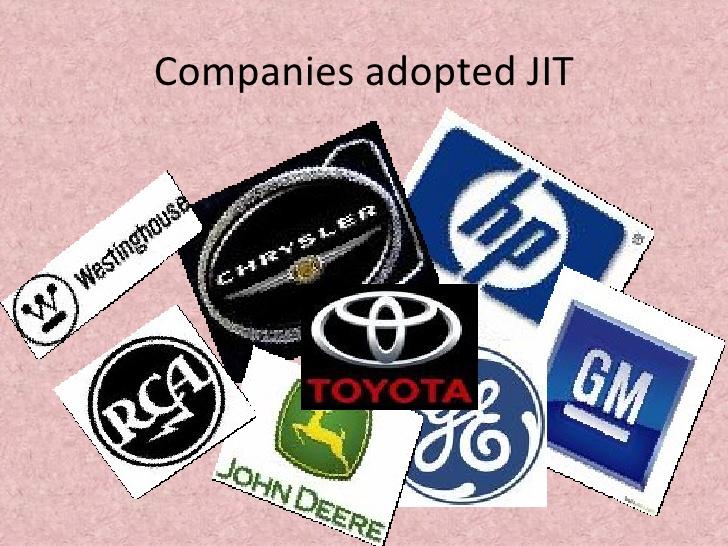
These companies adopted the JIT strategy for a specific reason – they have to serve a great number of clients with different demands, in different areas around the world, and at different times. In the case of McDonald’s, JIT is a forced measure, as food supplies cannot be left in storage for a long period (Kiger). Richard & Trench is not a very large enterprise, and as per the contract with the client, it will supply semiconductors primarily to one company. Due to a lack of large storage facilities as per JIT logistics strategy, the company would need to send batches of semiconductors to the client as soon as they are ready, and at the same time order new batches of raw materials to be delivered to the factory to continue production. This means that an additional price on production will be put into transportation expenses – the supplier will have to impose these to compensate for the large amounts of small orders, as it is more beneficial for the supplier to deal with big orders rather than small ones. Charging extra to compensate for the additional expenses may make the client reconsider the offer and find a different supplier of semiconductors.
Also, since JIT does not suggest stocking extra supplies, the entire system is vulnerable and overly reliant on the capabilities of the supplier to provide the required materials on-demand and in time (Kiger). The supplier would need time to adjust from having to deal with one large order every half a month to a multitude of orders, potentially within the same day. This is a much more complex operation and requires managerial prowess from both Richard & Trench and its supplier. Should any major incident happen, the company would be left without stock? This can be remedied by diversifying the supplier pool. That, however, will require time and financial expenses. It would also create an additional problem of having to manage numerous different suppliers at the same time.
Lastly, switching over to JIT would require Richard & Trench to vastly upgrade the quality of training of its managers and employees. JIT is a very intensive logistics model that does not allow any slip-ups or delays, as these could potentially disrupt the entire operation. Investing in recruiting managers familiar with JIT, or providing in-house training for current managers to ensure they are up to the new tasks, means additional expenses.
To summarize, switching over to JIT will provide short-term gains in saving money from the abolishment of the warehouse system and general efficiency of the process, but will induce long-term expenses in training personnel, upping the production price of an individual semiconductor, and increase the potential of production freezes in case of an accident. Switching over to JIT would also require up to one month cross-over time (and, so, potentially, up to 1 month of loss of production as well). The immediate expenses with JIT would amount to 500,000 dollars, with 350,000 dollars spent on repairing the automatized quality control sequence, and 150,000 dollars spent on staff training, worker remuneration, and other expenses.
Should the logistics management system be updated to WCS, Richard & Trench will encounter a different set of benefits and disadvantages. While the company would benefit from leaner warehousing needs under WCS, that benefit would be reduced by the necessity of opening warehouses closer to the installation. The construction of these new warehouses in the direct vicinity of the factory will cost about 1,000,000 dollars. The transition from the old warehousing system to the new one would be less disruptive than with JIT, however, as the staff from the old warehouses could be employed to work in the new ones, and the old warehouses could still be used until the new ones are built.
The transition to WCS will be smoother and easier than with JIT, as this model does not require the same amount of coordination and timeliness between agents to be effective. While the warehousing process is made leaner, the company will still be able to retain a certain amount of resources in stock, so that any supplying interruption would be compensated, if only for a short amount of time. Lastly, the system is more efficient in handling large orders from a single client, as the output of production and resources can be adjusted to fit both the client’s and the company’s needs. While Richard & Trench will still rely on its suppliers for raw materials, a failure to provide the resources on time would not be as catastrophic as it would be in a JIT system.
Building new warehouses near the factory would help minimize transportation expenses and greatly improve the production process, as transfers of materials between the raw materials warehouse and the factory, as well as between the factory and the warehouse for complete products, would be sped up considerably. The immediate expenses with WCS would amount to 1,500,000 dollars, with 350,000 dollars spent on repairing the automatized quality control sequence, 1,000,000 dollars for the construction of warehouses and packaging facilities near the factory, and 150,000 dollars spent on staff training, and other expenses.
Final Conclusions and Recommendations
To prepare Richard &Trench for a long-lasting and lucrative partnership with the large client, and to ensure the quality and security of the products and orders, some changes in the production and logistics system are essential. These changes include solving the problem of the automatic quality control of the finished product. This issue can cause an unacceptable setback and jeopardize the contract. This change will benefit the company from both long and short-term perspectives, as it would improve the quality of the product and remove the potential issues with singling out defective semiconductors. The other change involves the creation and enforcement of quality standards when controlling the quality of raw materials such as silicon, which is very important in semiconductor production. Developing a set of standards and enforcing them will not cause any major expense for the company, though it may force the supplier to improve the quality of the material to adhere to these standards.
Between JIT and WCS, the latter presents itself as a more appropriate logistics management method for Richard & Trench. Although it requires greater investment in the short-term, involving the construction of two warehouses near the factory, the company would benefit in the long term from having dedicated facilities located so close. JIT has a set of weaknesses that may compromise the order and generate delays, which are unacceptable to the client as per the contract demands. Even large companies, such as Toyota and Dell, have encountered major failures related to their suppliers, which paralyzed the company and resulted in millions of dollars in financial and material damage (Kiger). JIT is not fit to handle large orders from a single client, as the branching of the production process into a multitude of smaller sub-processes is simply unnecessary. Also, the implementation of the WCS will not cause any major disturbances in current working schedules, and the factory will be able to maintain its current workflow while the new warehouses are being built. The WCS management system can be maintained until the contract with the major customer expires, and can be switched to a different system if necessary.
An alternative solution, which requires the least modifications and changes to the current method of operation would involve simply increasing the capacity of the warehouse for the finished product. As it stands, with the actual yearly output of 5 million semiconductors per year, Richard & Trench is capable of producing several semiconductors prescribed by the order without any improvements to the current production line. The only necessary measures, thus, would require investing in the redesign of the warehouse. This solution is the most effective from a short-term perspective. However, it does not solve any of the fundamental issues behind the current system which hinders the company’s growth. The expenses associated with switching to WCS, JIT, or any other management system would eventually have to be dealt with, but doing so right now would not only improve the company’s capabilities and the quality of the product, but it would also give it more time to reap the benefits of improved transportation, management, and production changes for the duration of the order.
Works Cited
“Just-in-Time – JIT.” Investopedia. Web.
Kiger, David. “Analyzing Top Examples of Just in Time Inventory and Production Management.” WordPress, 2017. Web.
“Workload Control.” Workload Control. Web.