Introduction
A robot has been defined by the International Organization for Standardization as a device that is automatically controlled, can be reprogrammed and can manipulate programs in an industrial setting; The device can be fixed or mobile (ISO 8373). The construction industry is defined by several characteristics regarding its operations. It requires heavy lifting, high degree of accuracy is essential, it is a high risk job and time management is crucial. Until very recently, most of the activities in constructions were manually carried out or relied on machines requiring human control but due to the inadequacy of manual labor, automated and semi-automated devices were introduced. Balaguer and Mohammed have noted that robotics has infiltrated virtually every sector of the construction industry namely; Demolition, surveying, excavation and earth moving, tunneling, paving, house building and inspection activities (1135). Each of these activities has specific tasks that require the use of specific robots or automated machinery. This article looks at each of the construction categories and the type of robots being used.
Demolition
Demolition involves tearing down of structures and buildings in general. The demolition activity is usually very dangerous and requires precision so as adjacent structures are not destroyed during the process. Several types of robots have been introduced in the construction field to handle demolition activities however most robots in this field require some form of human input.
Aqua Jet H-450 and HV-550 Hydro-demolishing robots
This robot is used to remove weak concrete from structures such as bridges that may prove difficult to be done manually. The robots are controlled by computers using preset programs that are selected depending on the type of work to be carried out. The devices use a highly pressured water jet for the removal of weak concrete. The water jet passes across the surface of the structure and once it reaches a point of weakness, it removes the weak or damaged concrete. The identification of weak concrete is determined by the penetration of the water jet. Since the device has been programmed with the pressure normal concrete should withstand, this pressure is applied on the surface and if the water jet should chip away the concrete the device directs the water jet at that particular point until strong undamaged concrete is met or until a quality depth set by the operator is reached (IAARC 9).
Conjet Robot 361
This computer controlled robot uses highly pressurized water that forces its way into the surface of concrete structures for its demolition activities. The robot is remotely controlled by an operator whose main purpose is setting a timer that determines how long the water jet is released. The robot is fitted with ultrasonic sensors that aid in positioning of the water jet in inclined areas and also the sensors determine the distance of concrete removal. Water is forced out of the robot at supersonic speed creating an over pressure in the concrete surface which begins to chip away once the over pressure exceeds the concrete’s tensile strength. The nozzle, which is adjustable, is mounted on a cassette which is constantly oscillating. The cassette is bolted to a cradle that moves back and forth. The oscillation of the cassette and the back and forth movement are meant to increase the efficiency of the robot to provide maximum productivity.
This robot has been used for renovation and repairing purpose all around the world. The robot was used in 2008 to repair the Ponti Del Valico viaduct on the Swiss-Italian border. The robot was used to remove the concrete to a specific predetermined depth so as the concrete could be replaced. The advantage of this robot is that it can remove a specified amount of concrete in a specified place without damaging the surrounding surface or destroying the reinforcement. It also cleans the reinforcement and leaves the surrounding concrete rough so as to enable proper bonding of the newly placed concrete (IAARC 15).
There are other types of robots being used for demolition purposes and they include: Demolition unit Minicut, Concrete Hydro-Demolition robot, Water-Jet Concrete Chipping robot and BROKK BM demolition units. These robots mainly use the same principles as for the two named above.
Surveying
Surveying is a very tedious and time consuming task that requires high levels of accuracy in its execution. During the surveying of vast areas of land, manual execution may consume a lot of time which may not be practical. In surveying activities one robotized device is mainly used to collect and analyze data.
Navigation type surveying system using real time kinematic GPS
This robotic system utilizes satellites for topographic surveys so as to generate data to be used in earthworks activities for purposes such as construction of dams, airport and extensive building structures. The system comprises of a receiver situated on the datum point (point whose coordinates are known) and a receiver on the moving point (point whose coordinates are to be determined). The moving point receiver can be mounted on a car to enable collection of three dimensional coordinates constantly. The last component of the system is a transmitter which sends a signal to the satellites that is relayed back and collected by the receivers. The receivers can the process and determine the exact coordinates of the point (IAARC 19).
The main advantage of robotics in surveying is that it saves time as a task that can be done by many men for a long period of time can now be carried out by a single person in a very short time period. The use of robotics in surveying also increases accuracy in the collection of data.
Excavation and Earth Moving
In most cases, earthwork activities are carried out by the use of machinery such as bulldozers, excavators, draglines and in some cases manual digging. This machinery is quite effective in open areas where there is minimal confinement. The need for underground earthwork activities and in the removal of materials from very deep pits that is very dangerous has necessitated the use of robotics in this field of construction. Robotics in earthwork not only enhance safety but also save on time and enable carrying out activities to hard and complicated for manual labor or use of simple machinery. Various projects have been undertaken by the EU in this field and they include the OSYRIS and CIRC projects.
OSYRIS project
The OSYRIS and CIRC projects were initiated by the EU to come up with machines that utilize GPS and laser data to enhance earthworks in road construction. The projects uses semi-autonomous machines that collects and processes data to enable the control of aspects in road construction such as speed, temperature of the bitumen to be laid, thickness of the layers and distance control. The project also aims to coordinate several machines at the same time to improve efficiency and productivity. This will be carried out by using computer programs fitted into each machine that decide when and how each machine will be activated. OSYRIS and CIRC projects involve the use of robotic technologies in a variety of tasks and are not as such a single robot (Balaguer and Mohammed 1140).
Tokyu Digging Work Robot
This remote controlled robot developed by the Tokyu Construction Company is mainly used for digging vertical pits and subsequent loading of materials on trucks for carting away.
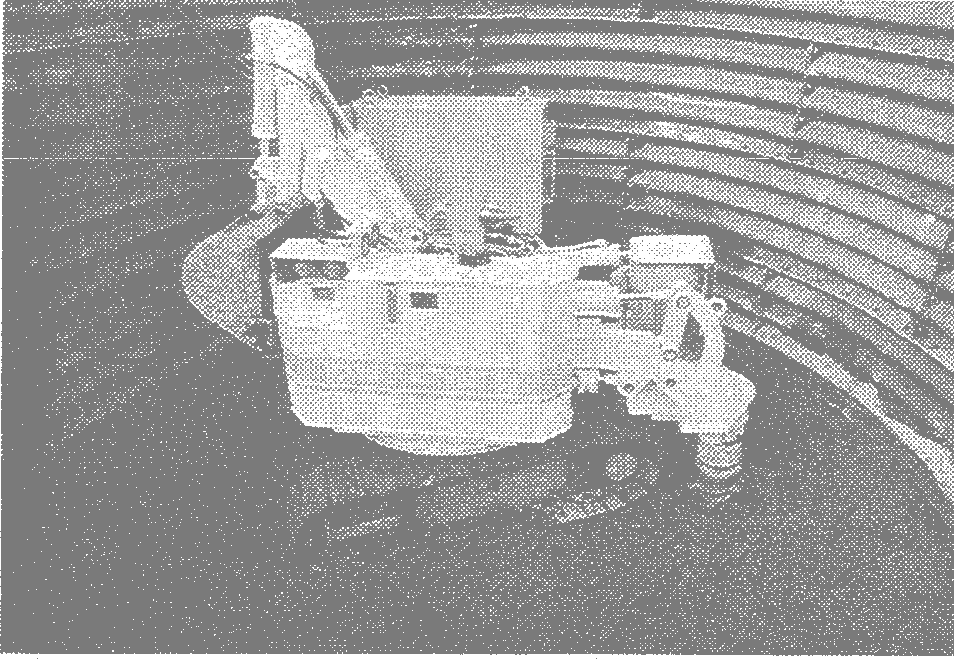
The robot is fitted with a turning body that can maneuver according to the area being excavated. The robot also has cutters for the actual digging work and vacuum extraction system that removes the excavated material from the pit to the surface. The robot can also be used in digging areas with soft rock which may prove difficult and dangerous for other techniques. The robot is fitted with a cutter drum that scrapes out soft rock thus reduces the risk posed by actual digging in soft rock. The cutter drum has little vibration hence noise pollution is minimized and the risk of collapse is also minimized. The free travelling robot can be used regardless of the pit shape. The entire functioning of the robot is controlled by a control panel contained within it. Signals are sent to the panel from the surface regarding the speed of digging and when to remove the dug materials. The controller also initiates emergency shutdown if any problem arises (IAARC 23).
Other types of earth works robotic systems present in the construction field include: Unmanned Caisson system, ROVO Caisson Method, Pneumatic Caisson, Tele-Earthwork System.
Tunneling
The tunneling process involves high risk tasks of digging underground. The tunneling process requires heavy lifting and digging in potentially unstable areas hence a need for accuracy. Various robots have been developed for this process so as to limit the risk for human operators.
Segment Automatic Carrier System for Shield Works
This machine developed by Shimizu Corporation is intended to convey materials from the surface stock yard to the underground where the materials are received by the shield tunneling machine. The system contains five components: A central control unit equipped with an optical communication system, battery operated carriages, an automatic elevator, a lifting and transfer device and an automatic stock-rack device (IAARC 53).
The battery operated carriages receive commands from the control unit regarding the conveyance of materials from the point of tunneling to the point where the elevator system is situated. The carriages run on rails present in the tunnel and are loaded by the tunneling machine. The carriages are controlled by the control unit and all activities are coordinated such as efficiency is maximized.
The stock rack device moves up and down the shaft as commanded by the control system. The elevator is the means by which the carriages travel through the shaft. The elevator is controlled by the control unit such that each time a carriage is loaded the elevator is turned on. The segment lifting and transfer device collects materials from the carriages and transfers them to the elevator. It is comprised of a forklift that receives the materials and a trolley hoist whose main aim is to ensure every piece is transferred to the elevator.
Tunnel Swift Lining Robot
This robot is used for the lining of tunnels (both new and existing) using concrete. The robot is equipped with a movable segment that is attached to an endless belt. The robot also contains an arm that can extend and contract as required, a sliding device and a hydraulic unit. A computer in the robot controls the extension of the arm, the sliding device the thrust force of the movable segment and the rotation of the belt. The positioning of the robot is through ultrasonic sensors that measure distances from the far edge of the tunnel. The rotation of both the arm and the belt are set to be equal such as the materials being delivered by the belt are conveyed to the arm where they are placed on the tunnel surface.
The lining process is through shotcreting concrete at a high speed into the space between the tunnel edge and the interior movable form. The positioning of the movable form is achieved by use of stroke detectors that measure the stroke and arm length of each thrust jack (IAARC 57).
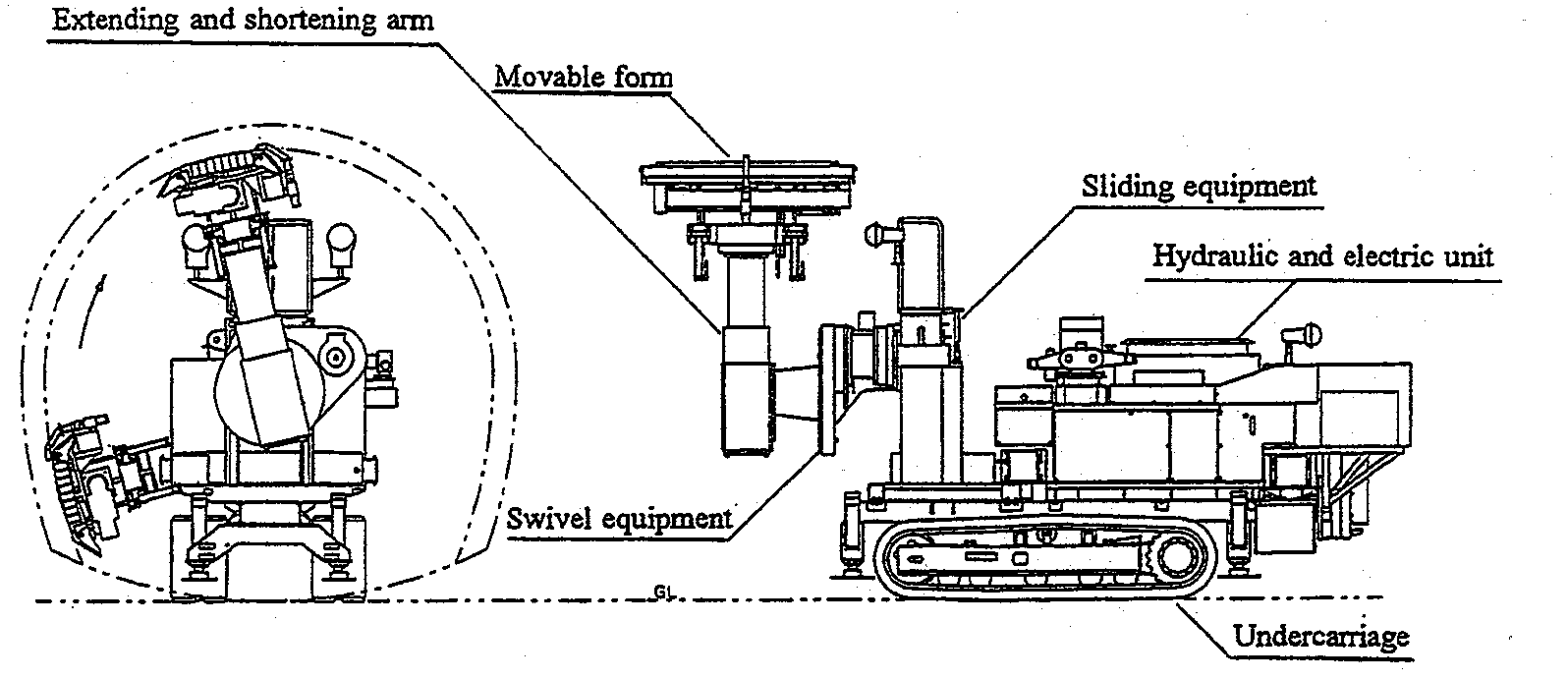
Road Paving
The major function in road construction is the actual paving activity. Road paving requires high degree of accuracy so as to ensure an even surface. Due to increasing cost of road construction it has become a necessity to automate the whole process so as to increase both productivity and efficiency so as to enable the reduction of costly operations.
SAKAI road profile cutter
This is a profiling robotic machine that uses programmed data to adjust the cutting depth automatically along the road. The cutter contains an automatic control system (ACCS) with two modes, a contour dependent mode and a longitudinal contouring mode. The two modes depend on different cutting methods with the contour dependent mode maintaining a steady cutting depth that depends on the surface of the road. The longitudinal contouring mode changes the cutting depth progressively depending with the changes of the lateral road surface. The robot is fitted with electro-hydraulic servo valves that control the cutting depth. As the machine moves forward, sensors pick up data pertaining to the gradient and condition of the road surface which is the processed by the on board microprocessors. The micro processors send signals to the servo drums on what depth of cutting is required thus raising or lowering the cutting drum as appropriate. The robot requires proper input of the road datum points so as to be able to compare the data collected by the sensors and the actual road surface required (IAARC 39).
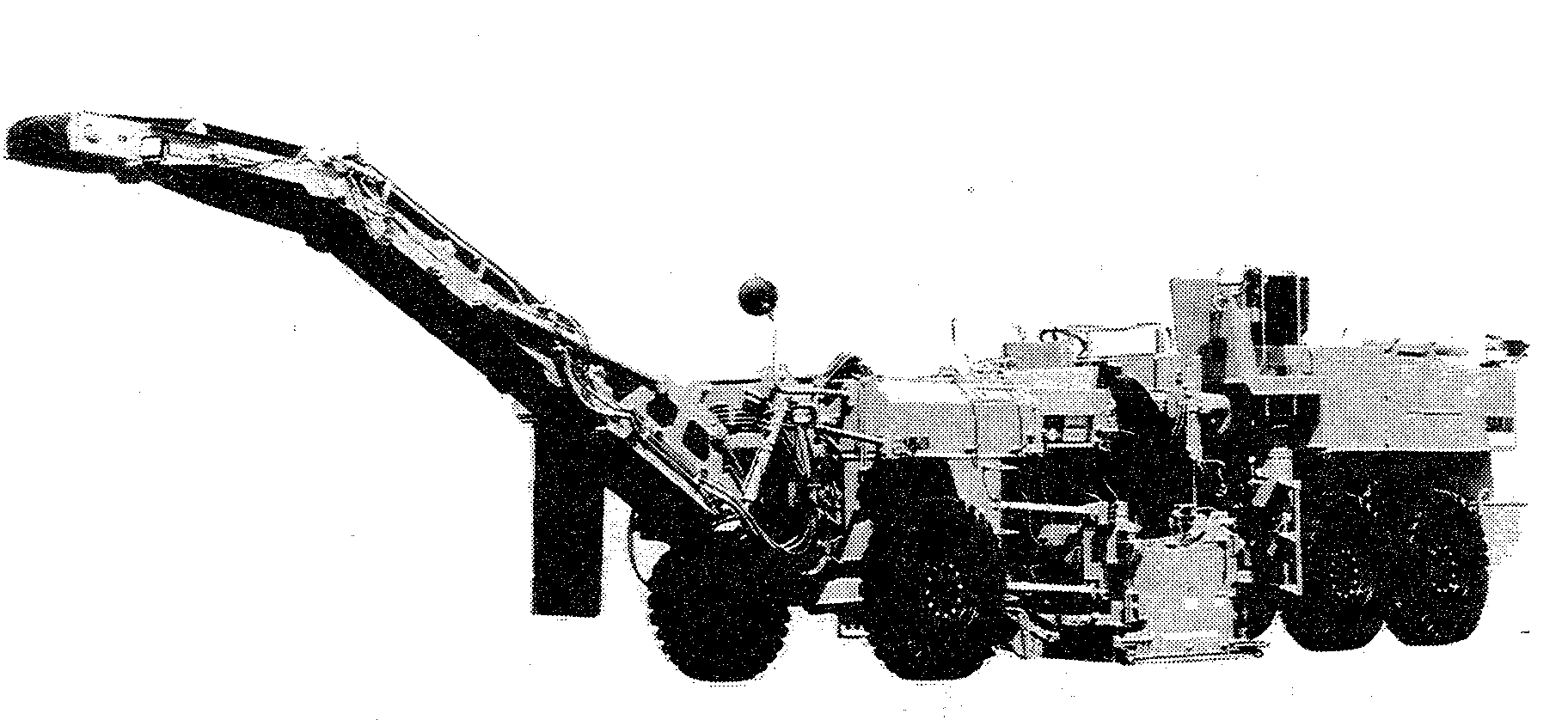
The RoadRobot
The RoadRobot is a multipurpose machinery that has automated various functions of the paving process (IAARC 43). The robot can receive asphalt automatically, has an automated asphalt conveyance system, can control the asphalt laying process, has sensors for automatic control and finally the robot can start and stop automatically depending on the controlling programs.
The robot contains sensors situated at the driver’s compartment that sense and judge the distance to the asphalt feed vehicle and also the height at which the asphalt conveyors are situated. The robot then forwards this data to the driver who can the reverse and set the correct parameters required to receive the asphalt. The robot can initiate where to start and where to stop the paving process depending on the level of asphalt it carries. This ensures that the road surface is smooth, even and to the required depth.
The RoadRobot uses pre-programmed data to lay the asphalt to the required depth. The paver moves along the road laying and compacting the asphalt to the appropriate depth that depends on the initial surface of the road and the required preset final surface. All functions regarding paving i.e. compacting, laying and leveling are all controlled by computer programs inbuilt into the robot.
Although the robotic paver has an operator, the steering process is completely automated. The operator’s job is mainly to set the paver along a given guideline and perform small task such as setting the paver to receive asphalt. A specific guideline such as a curb forms the basis of mechanical referencing through which the RoadRobot steers. In situations where a guideline is absent, a laser based navigation system installed in the robot is utilized. The laser system scans the surrounding area and analyzes the angle between the robot and positioning elements installed by surveyors along the road profile. The RoadRobot is a pioneer in its field as it is the first paver able to navigate itself.
House Building and Inspection
Various robots are used to carry out certain functions in house construction. These robots provide work that may require high levels of precision otherwise unattainable manually. Inspection activities also require automated machinery since visual inspection is not reliable and cannot accurately judge if a structure has been constructed to the required degree.
Concrete-Slab Finishing Robot
This robot is designed to carry out the final finishing of concrete slabs in building projects. After concrete has been laid on a floor it is essential to carry out smooth finishing. This was traditionally done using trowels by skilled craftsmen but it has proven to be too tiresome and time consuming. The robot has been equipped with sensors that allow it to move automatically within a specified area. The robot carries out the finishing process by use of installed trowels attached on its bottom side. Due to the homogeneity of the trowel marks, the final finishing is of excellent quality. The robot has been programmed to lay a specific amount of concrete to achieve a level surface. The robot contains sensors that determine the amount of concrete to be placed depending on the initial texture of the slab (IAARC 93).
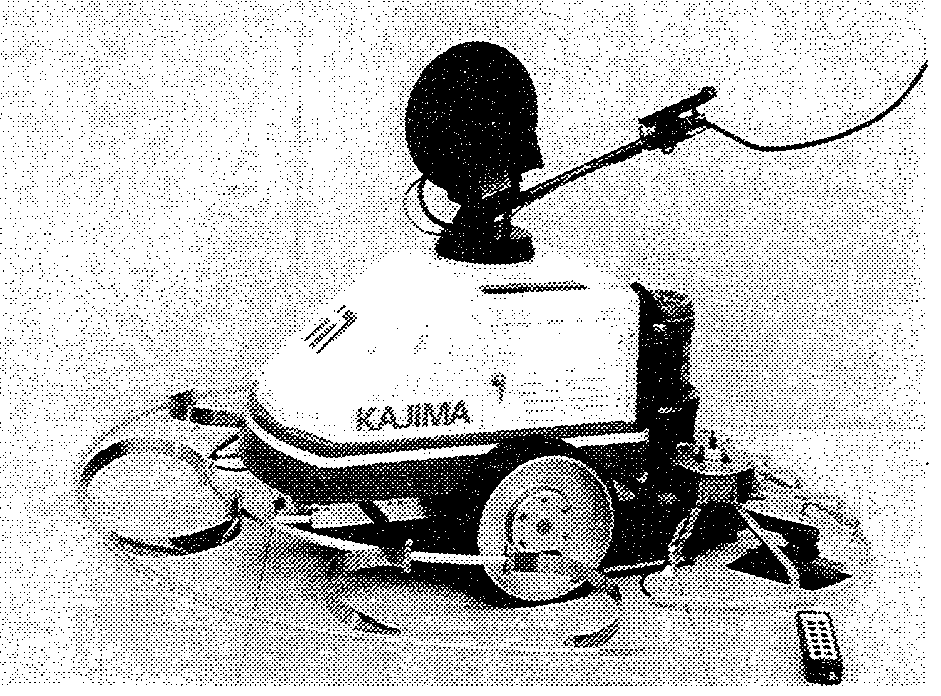
Exterior Wall Tile Inspection Robot
This robot was developed so as to analyze the bonding conditions of tiles for external walls. The boding strength of exterior wall tiles reduces with age. This shortens the life of a structure and may even lead to the tiles falling off. The robot is designed to move up and down the wall surface by use of cables suspended from the roof parapet. The robot has ten diagnosis balls that tap the tiles continuously and the resulting sound is analyzed. The robot then provides a graphical representation of the results (IAARC 95). The robot movements up and down are automatic and the collection and analysis of the data is also automatic.
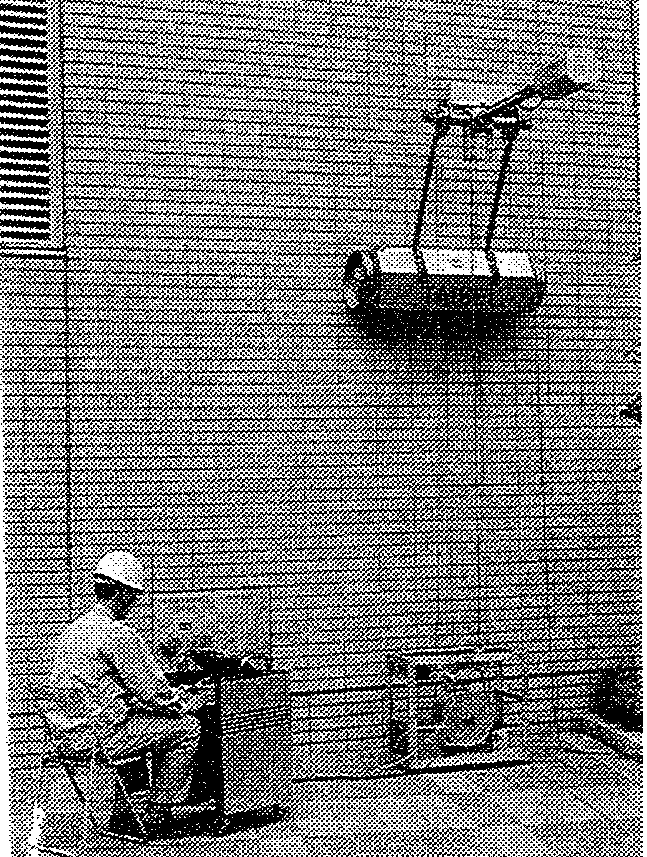
Conclusion
It can thus be seen that the construction industry has been infiltrated by robotics to a large extent. Robotics in construction offer very many advantages to the conventional methods that included manual labor and use of machinery. First, robots enable work that may prove unsafe for humans to be carried out. Activities such as digging of large pits, construction of tunnels and earthworks in unstable formations are too risky to be carried out by human beings thus robotics can be utilized. The second advantage of robots is that they are accurate and conserve time. Work that may take ten men ten days can now be done on a single day by a single person using a robot. Robots can also gather information that could previously impossible or too expensive. The use of GPS surveying in large areas is an example since manual execution may take too long to be of use. The use of the tile inspection robot is also another example since the determination of the quality of the tiles would otherwise been have left for visual inspection which could have been too late to manage the problem.
In considering these advantages we can conclude that the construction industry has greatly benefitted from the use of robotics and future developments in the application of robotics in construction is highly welcomed.
Works Cited
Balaguer, Carlos and Mohammed Abderrahim. “Robotics and Automation in Construction.” Automation in Construction 18.8 (2009): 1135-1143. Print
ISO 8373: Manipulating Industrial Robots. Geneva (Switzerland): International Organization for Standardization, 1994. Print.
Robotics and Automated Machines in Construction. Watford: International Association for Automation and Robotics in Construction (IAARC). 1998. Print