Introduction
The surface engineering sector makes a major contribution to the UK economy with over 70% of all manufactured products requiring some form of surface engineering. This figure rises to over 80% in the aerospace sector. Surface engineering is therefore a vital part of the UK’s manufacturing supply chain, but mounting environmental legislation and excessive red tape are threatening the survival of many surface engineering companies and reducing the global competitiveness of the UK’s manufacturing sector. On average, during the past two years, one company has closed each week in the surface engineering sector, predominately in the metal finishing/electroplating area. So what are these pressures and how can we address them and possibly turn them to our advantage? In the last few years we have seen the introduction of a host of environmental directives such as Integrated Pollution Prevention & Control (IPPC), the Landfill Directive, End of Life Vehicle Directive (ELV), Restriction of Hazardous Substances Directive (ROHS), European Waste Catalogue (EWC), and Waste Acceptance Criteria (WAC). The list seems to go on for ever and there is more in the pipeline such as the Control of Major Accident Hazards directive (COMAH). (Selinger et. all, pp. 19-74)
Each year a lot of waste is produced by the automotive industry due to end of life vehicles. The main difficulty why vehicles are not being recycled as they should be is because numerous amount of the material is un-recyclable or incredibly costly. This report examines the impacts of the insinuation of this legalization with respect to the design of the vehicle components in a vehicle to look at what is being prepared by the industry to meet new legislations about recycling.
Nucleus of the problem
Every year the amount of cars being produced in Europe are increasing and every year the amount of waste produced by the end of life cars is know exceeding 9 million tons. This is having a big impact of the environment. The End of Life Vehicle Directive was put in place by the European union (legally adopted in September 2000 and published in October 2000) to reduce the amount of wasted materials that goes into landfill sites From January 2006, the Directive sets targets for the reuse, recovery and recycling of materials resulting from End of Life Vehicles (ELVs) in Europe. By January 2006 85 % of the weight of the ‘average’ car will have to be recovered, with 80 per cent of that target being met through reuse and recycling of the vehicle’s constituent materials this is set to increase to 95% reuse and recovered and 85% recycled be 2010.
Methodology
Through this methodology we will understand where the actual problem is and where the legislations stand today. The data was collected through interviewing different legislators and stakeholders. The vehicle industry started a lobby through its industry organizations in order to avoid government regulation. The mainly significant among these were the End-of-Life Vehicle Recycling Project of the German car industry (PRAVDA) and the lobby at the European level by the European Association of Car Manufacturers (ACEA). In discussion with other industry organizations, the business developed alternative policy plans. Personal car manufacturers started alleged ‘vehicle dismantling pilots’ in 1990-1991. These pilots served multiple objectives:
- assessing the cost and potential benefits of vehicle disassembly;
- developing cost-efficient disassembly routines;
- developing and testing concepts for larger scale end-of-life vehicle recycling;
- developing knowledge of design for disassembly and design for recycling;
- increasing the efficiency of current vehicle designs and assembly procedures;
- Continuing research into material recyclability; and, centre dot creating markets for recovered automotive materials.
Discussion
All of these thing will cost the car company millions and millions or pounds if not followed. All manufacturing companies are spending millions in research and design development to meet these requirements. Recycling of a car will have to begin for every manufacturing company abiding by the directive at the point of original design. Manufactures are now designing their cars with recycling materials as a priority. This means that grate pressure has been put on the manufactures. Manufactures know using material which can be recycled… If we look at ferrous metals like steel, steel is not really a problem for manufactures when is comes to recycling. As we said before steel can be easily recycled is makes up about 70% of the car so really in terms of recycling to meet the new regulations the manufactures need to find a way to recycle a further 15 to 20 percent by 2006 rubber as it makes up only 5 to 7% of the car can be recycled Also rubber is now being recycled it is being recovered to be used for waterproofing against weather for doors and windows but its not as a big factor as plastic. The main priority will be the plastic in the cars in recent years plastic has become a major material used in cars if manufactures can recycle this they will be able to meet regulations (Anderson, pp. 16-84).
In recent years manufacture main concern would be to purify the plastic being used. This means when it comes to the recycling point is can be done without having to separate different polymer. Many manufactures are now designing components using the same type of thermoplastic resin for a complete assembly. Toyota in recent years has developed a unique resin Toyota Super Olefin Polymer (T SOP), to replace conventional reinforced composite polypropylene. It has the high rigidity and high impact resistance the most important thing about this material is that it dose not lose its properties during recycling. For its methodical attack on automobile shredder residue, Toyota has developed technologies for dry separation, sorting and recycling. These are enabling copper to be recovered from wire harnesses for use as a reinforcing material, while powdered glass is the basis for tiles of remarkable density and strength. Miscellaneous resins are bulked into blocks for burning as a fuel, which has a heating value equivalent to that of coal. One of the most significant achievements is the use of urethane foam and fibre, which is a major element in the shredder residue, to produce a novel sound proofing material now being used on several models. Toyota has also succeeded in replacing sodium azide, which generates the gas that inflates airbags in the event of an accident. This material is harmless when the bag expands but toxic when un-detonated and therefore presents a danger on dismantling. Toyota is one of the richest car manufactures on the planet the have managed to produce very efficient and effective manufacturing for there cars. They have already hit the target as the now cars made by Toyota cars in 2006 will be 89% recyclable many manufacturing company I obtain these goals as the new directive means they have no other choice (Pocklington, pp. 75-87).
Findings
First, industry characteristics are considered. In Pavitt’s taxonomy, the automotive industry is a ‘production intensive’ industry, dominated by economies of scale and a strong tendency to cost reduction. From this perspective it may well be understood why car manufacturers have used the automotive waste issue to improve their vehicle designs through the exploration of design for dismantling–or ‘design for recyclables'(Pocklington, pp. 75-87). To the extent that reconsidering vehicle design through a new lens results in cost reduction, design innovations have been adopted. This perspective also sheds light on the reluctance of car manufacturers to engage in take-back and recycling activities, as they have traditionally not been in this business and expected small or negative returns of these activities. Take-back and recycling activities would increase the complexity of the business, which is at odds with current trends of outsourcing major parts of the production process, including the design and supply of parts and components. However, the intra-industry diversity in developing recycling strategies is too subtle to be captured within Pavitt’s taxonomy. To be able to recycle 85% percent of car in not easy this would mean that everything you see I the picture below must be recycled except. As you can see this is a picture of a older car this is just to show you how many parts there are in a car now a days there more complex and probably have double the amount of components in a car due new technology because there is so much technology being introduced the car needs to be kept as light as possible so plastic use is inevitable. For example if we take the car bumper, we know that car bumpers are know being constructed of plastic more than ever before, we also know that car bumper is being replaced on a car more than another part simply because of its function is to absorb light impacts but because its made of plastic it is really difficulty to recycle it as it is made from many different types of resin which have different properties. To break these down during recycling it is a very expensive process if not impossible. But like Toyota if we made the hole car bumper out of there new technology resin Toyota Super Olefin Polymer (TSOP) with its properties it can do the same job and it can be recycled because its made from pure resin and above all it dose not lose its properties after recycling. ELVs impact the environment in many ways, but what must not be forgotten is that the largest environmental burden from a vehicle is during its use. For this reason a material like composites that is hard to recycle can still be environmentally preferable because of its low weight, and hence low fuel demand. The environmental impacts from ELVs can be divided into two categories, resource loss and pollution (Zoboli et all, pp. 16-29).
Abandoned vehicles
ELVs that never enter the waste stream cause problems in both categories. The materials are slowly degraded making recycling hard or impossible and the different materials in the vehicle leak into the environment.
Transport
Transport and processing of ELVs require energy which also contributes both to resource use and pollution, for example the release if carbon dioxide and particles from burning fossil fuels (Deutz, pp. 132-38).
Auto shredder’s residue (ASR)
The metal content in the ASR is due to incomplete removal of metals and means a loss of material. ASR also risk having a toxic content of mercury, lead, hexavalent chromium, cadmium, arsenic and PCBs. Shredding the vehicles before the removal of these substances makes it virtually impossible to remove them. ASR is land filled in many countries, for example the US and Australia. This means there is a substantial loss of resources. The problems with recycling are both technical and economical; it is hard to find a market for the materials (Anderson, pp. 16-84).
Hazardous substances
Vehicles contain many potentially problematic substances, for example mercury which is toxic to humans, persistent in nature and bio-accumulative. If this and other harmful substances such as lead are not removed prior to treatment they will end up in the ASR and then possibly in landfills. If the landfills are badly managed or constructed there is a risk that these substances will leak into the environment. If recycling facilities, scrap yards etc have a poor pollution control this also means that hazardous substances risk being released into the environment. These substances include oils, coolants, fuel, brake and other fluids, air-conditioning gases and heavy metals for example lead hexavalent chromium, cadmium and mercury. In order to explain the divergence in recycling strategies of European car manufacturers, I proceeded as follows in testing the relationships between complementarily, technological opportunity and appropriability. I thoroughly analyzed the three options that emerged from the problem definition (selective disassembly of parts and materials, improved processing of shredder waste and metallurgical recycling) on the dimensions of complementarily, technological opportunity and appropriability. Table 4 summarizes the results of this analysis. Next I hypothesized for each option that the corresponding organizational arrangement would be chosen for implementation, assuming first that my analysis of the options was correct and, secondly, that car manufacturers proceeded in the same way. Finally, I compared which were the options of choice and which organizational arrangements were adopted in developing and implementing these options. It appeared from this comparison that: he hypothesized relationships are confirmed by the empirical data (collected through extensive interviewing and document analysis). Thus, BMW, Ford Europe and Opel, pursuing the option of selective disassembly of parts and materials for recycling, adopted a strategy of close co-operation through a dedicated network of car dismantlers when it came to the implementation of this option, because profits from such activities would be low and hard to appropriate. The other car manufacturers implemented their preferred option of improving the processing of shredder waste through a strategy of distant cooperation by concluding framework agreements with shredder and metal refining firms as a ‘third party’. They did so because the level of complementarily and appropriability of profits was considered to be low’, despite a significant technological opportunity in improving the efficiency of the shredding process. Moreover, to the extent that car manufacturers identified cost-efficient solutions to improve their vehicle designs and assembly procedures during the first stage of dismantling pilots, they kept those solutions under their own close control (Perchard, pp. 65-69).
Table 4. Assessment of the end-of-life vehicle recycling options along the complementarity, technological opportunity and appropriability dimensions
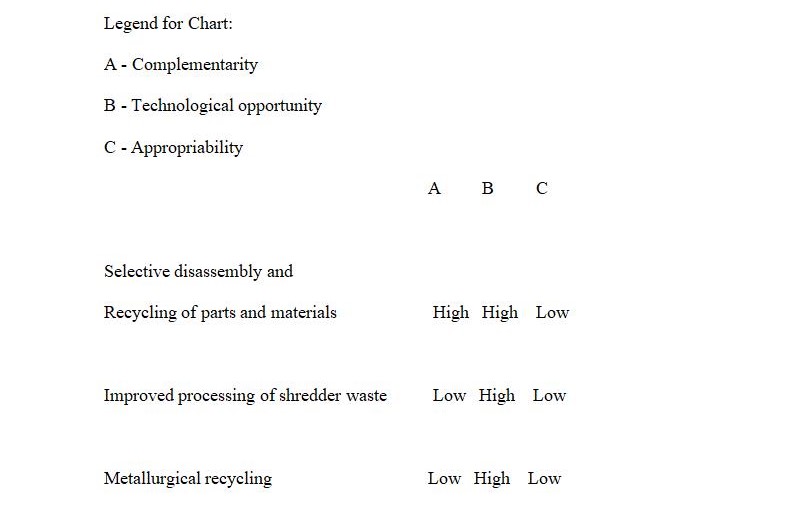
Conclusion
Depending on the level of detail in the analysis, different styles of innovation might in some cases be distinguished, I propose, however, that sources of variety stem from managerial discretion in directing and co-ordinating the innovation process. It is proposed that the choice of a specific solution and mode of coordination by individual firms depend on the relation between the resources needed for this solution and the core competencies of this firm. The relation is described in terms of complementarity of resources and activities, perceived technological opportunity, and appropriability conditions. To the extent that innovation is about the acquisition, development or recombination of resources (including tacit, intangible resources such as knowledge, capabilities and experience) in order the undertake new activities, I propose that ‘complementarily’ is another innovation stimulating factor in addition to growth and size of the market, technological opportunity and appropriability. If firms may choose among a variety of organizational arrangements in developing and marketing innovations, including internal integration, various modes of inter firm cooperation and outsourcing, I propose that firms’ perception’s of technological opportunities to innovate are an additional factor to complementarily and appropriability in the mode of governance choice. (Deutz 132-38)
Works Cited
- Anderson, Richard A. Microwaves & RF: 2007, Vol. 46 Issue 2, p66-84, 10p.
- Deutz, P. Environmental regulation as a driver for change in the value chain: 2004, EU End of Life Vehicle Directive and its impact on the automotive value chain. Supply chains and total product systems: a holistic perspective, 132-38.
- Perchard, D. Transposition of the ELV Directive in other EU member states: 2004, Perchards, 65-69.
- Pocklington, David. European Environmental Law Review: 2006, Vol. 15 Issue 3, p75-87, 13p.
- Selinger, A., Steiner, C., and Shin, K. TwinRec- bridging the gap of car recycling in Europe: 2003, International automobile recycling congress, Geneva, 19-74.
- Zoboli, R., Barbiroli, G., Leoncini, R., Mazzanti, M. and Montresor, S. Regulation and innovation in the area of end-of-life vehicles: 2000, European Commission, 16-29.