Abstract
Materials used by the automotive industry in particular and the transportation industry, in general, are selected based on a set of technical demands, customer demands, legal requirements, and ecological needs. Such needs include fuel efficiency, reduced emissions, weight reduction, used vehicle disposal, and the recyclability of its components. Hence, these materials are required to further accommodate specific emerging and traditional requirements that are not only essential to assess the material type and mix, when manufacturing these vehicles, but also necessary to determine its cost and its ultimate compatibility regarding recycling.
In this study, the recycling of the main automotive structural materials is surveyed and assessed for two specific scenarios; aluminum-intensive and steel-intensive body structures. The deployed assessment in presented work computes the amount of energy required to recycle each vehicle structure and the cost incurred for these scenarios. The cost to energy utilized when recycling such vehicles is proposed as a parametric indicator of the recycling process. The survey part of the study highlights the ecological aspects of the automobile and further analyzes the material selection aspects and the Industrial Ecology IE aspects too. The assessment also covers the main light-weight alternatives including the high strength steel alloys, the variety of aluminum alloys and plastics. The survey features the different recycling systems from Type I to Quasi-circular to completely circular material flow.
Introduction
The automobile industry ecological aspects can be characterized through its product life cycles, the economic and profit views, and its potential impacts on the natural environment or its environmental footprint. Nowadays, vehicle manufacturers are being confronted with more ecological design principles, due to stricter environmental regulations and its enforcement that put continuous pressure to adopt more eco-friendly production and product design concepts and practices. O’Rourke & Connolly [1] introduced an integrated approach in response to reforming the automobile industry termed as Industrial Ecology (IE). IE is one of how the humanity can adapt rationally and deliberately to maintain a particular, desirable capacity necessary for technological, cultural and economic evolution. The concepts of IE should not be viewed in isolation, but should also incorporate a system based approach. IE is a system view that seeks to optimize the material cycle from virgin stock to finished material, products, components and ultimate disposal [1]. IE is a comprehensive strategy for redesigning vehicle industrial activities towards an environmentally sound industrial system.
IE systems are meant to minimize waste generation while optimizing energy and materials usage. O’Rourke & Connolly [1] argued that IE is an efficient system in coordinating industrial processes, technology, and consumer behavior. O’Rourke & Connolly [1] explain that the IE of an automobile is the complete recycling of all reusable parts and components conforming to ecological requirements.
In pursuit of a competitive position in the market, vehicle manufacturers have responded through advanced research and development programs on material selection, engineering efficiency, and end-of-life resource recovery strategies [2]. To achieve the sustainable development, recycling strategy has to be considered, its known that recycling has positive impact on the environment by saving natural resources and reducing the impacts caused by the landfill. From this point automotive industry should move from reactive to proactive approach in the environmental effects of its products that will lead to future success.
This study explores the concepts embedded in the IE of the automobile from the material selection aspect with the particular focus on the recyclability of two primary material candidates such as aluminum and steel. Such materials used on the automobile must accommodate new requirements related to determining the vehicle life cycle from the cradle to the grave, and therefore, it is necessary to have an up-to-date account of the vehicle material composition. To address the purpose of this study, we will analyze the current recyclability practices of the vehicle materials in the automotive industry so the current state can be predicted and present a basic energy and cost calculations for the current practices through investigating the recyclability of the automotive industry specific the light weight material options.
The aforementioned discussion may motivate a strategy supported with a systemic approach to help assess and benchmark the energy expenditures and its trend among different automotive production facilities, to help define potential best practices and opportunities for energy savings specific to the industry.
The sections of the paper are structured as follows: Section 2 focus on relevant literature on automotive material consumption such as lightweight steels, aluminum, and plastic while Section 3 discuss the automotive recycling and Energy Requirements from the EPI Model. The results and discussion are discussed in Section 4. Lastly Section 5, conclusion and future research directions are presented.
Automotive material consumption
The dependence of the automotive industry on raw materials versus recycled is among most intensive between other industries, especially when compared to other material dependent industries [3]. As shown in Table 1, the raw materials composition contributes to around 47% of the cost of a typical passenger car. The overall material used is composed of 54.8% of steel, 13% of iron, 7.8% of plastic, 5.6% aluminum, 4.3% rubber, and 2.8% glass [4; 5]. The World Steel Association estimates that the automotive industry accounts for roughly 12% of the overall global steel consumption, while steel also accounts for 60% of the weight of an average automobile [6]. Reports from the US Environmental Protection Agency, as shown in Figure 1, summarize key trends in light duty vehicle weight for model years from 1975 to 2012 in the US [7]. It indicates that the use of high-strength steel and aluminum has increased, while the applications of low carbon steel have decreased.
Table1: Material composition of a Typical Passenger Car, Source: 5.
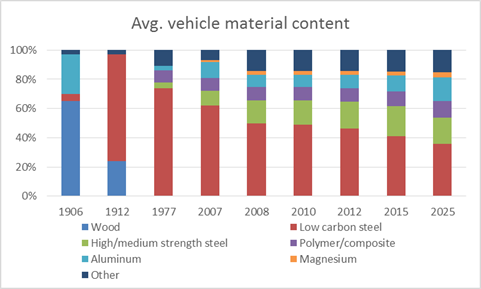
A study by Kallstorm4 revealed several changes in the overall vehicle material composition for the periods of 1993-2002 and 2010-2014 as shown in Table 2, vehicles ranging from mini-vans, sedans, sports utility vehicles, and trucks were analyzed. It also shows the automakers who are trying to decrease the weight of each of their vehicle offerings in the market to answer consumer demand for more features and accessories 9.
Table 2: Material composition of vehicle models: from 1993-2002 and 2010-2014, Source: 9.
From 1993 to 2014, the shares of ferrous materials such as steel and iron have decreased significantly. It can also be observed that aluminum alloys increased considerably, and the composites share did increase in all market sectors even for high volume models. Other aspects included redesigning vehicles to be lighter weight, while ensuring that the performance requirements of the subsystem of the advanced model are resized, depending on the total vehicle weight such as engine, suspension, and others. According to such requirements, these changes are expected to continue as vehicle manufacturers’ responds to legal requirements regulating fuel economy and policies that involve the conservation of the environment. Figure 2 illustrates PSA Peugeot-Citroën model with the use of alternative materials to major parts of a vehicle.
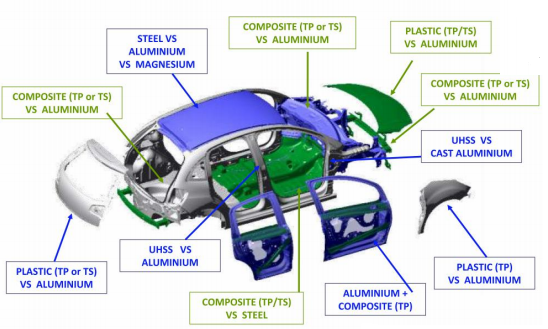
Lightweight Materials
Lightweight materials usage has been increasing in the automotive products and their design due to recent global focus on resource efficiency; specifically meeting the Corporate Average Fuel Economy (CAFE) standards while reducing harmful emissions such as CO2, while increasing the material recyclability [11]. In the United States, scientists from the US Vehicle Technologies Office (VTO) [11] are continuously working to improve the use of lightweight materials to improve their properties such as strength, stiffness, and ductility. It also focuses on improving the aspects of manufacturing such as the material cost, production rate or yield, and improving their recyclability.
According to the US Department of Energy [12], advanced lightweight materials have shown a significant increase in the production of vehicles since 1996: medium and high-strength steel have increased by 70%; aluminum increased by 70%, and the use of plastic composites has increased by 45%. The 2015 BCC Research report indicated that the global market for lightweight materials used in transportation reached US$115.4 billion in 2014 from US$80.5 billion in 2006 including motor vehicles, aircraft, trains, and ships. It is expected to reach US$188.7 billion by 2020 with a compound annual growth rate (CAGR) of 11.6% from 2015 to 2020. For motor vehicles, the largest end-use segment is passenger cars and light trucks. Based on a study by McKinsey and Company [13], the automotive industry will heavily increase the use of lightweight materials from 30% to 70% by 2030, mainly the amount of high-strength steel, aluminum, and plastic.
Automotive designers and engineers analyze components and identify the benefits and constraints to achieve design flexibility and weight reduction using new materials. The amount of weight savings of any alternative materials, when used in vehicular parts and component depends on the application and design requirements. Weight reduction can be achieved in three specific ways [12]: (1) material substitution; (2) vehicle redesign; and (3) vehicle downsizing. Material substitution involves replacing conventional materials used in the production of a vehicle such as iron and steel with lightweight materials like aluminum, plastics and polymer composites [12].
Redesigning vehicles refers to optimizing the size of the interior and exterior components as vehicle weights decrease, while at the same time, improving the vehicle’s packaging and maintaining the same passenger and cargo space and functionality regarding performance. An example is the use of the typology optimization technique, which is a mathematical approach that can be utilized during the layout of the initial design concept, using computer-aided techniques to analyze components and prescribe sets of performance targets to help predetermine the design goal [14]. Lastly, vehicle downsizing such as vehicle size reduction means shifting from larger and heavier segments to smaller and lightweight vehicles. If large cars were downsized to midsize, and midsize to small or compact segments, weight savings could range from 9 to 12% [14].
McKinsey & Company [13] investigated the material used, accounting for more than 90% of the vehicle weight while suggesting different lightweight packages depending on the vehicle segment, brand, and powertrain options that OEMs may consider in the future [14] as shown in Figure 3.
(1) Extreme lightweight – this package extensively uses carbon fiber materials for maximum weight savings towards improving driving dynamics. Maximum weight savings for a medium-sized luxury car is around 35% at an additional cost of EUR 8 to 10 per kg saved.
(2) Moderate lightweight – currently the automotive industry uses aluminum, magnesium or high-strength steel in the replacement of steel. The use of even lighter material such as carbon fiber is considered only on selected components which require a high level of weight reduction and stiffness like Mercedes-Benz E-Class Series. Maximum weight savings is around 30% at an additional cost of EUR 4 per kg saved.
(3) Conventional lightweight like Toyota Corolla, they heavily used high-strength steel in the replacement of heavier steel and iron. Carbon fiber is not implemented due to cost considerations. Maximum weight savings is around 18% at an extra charge of EUR 3 per kg saved.
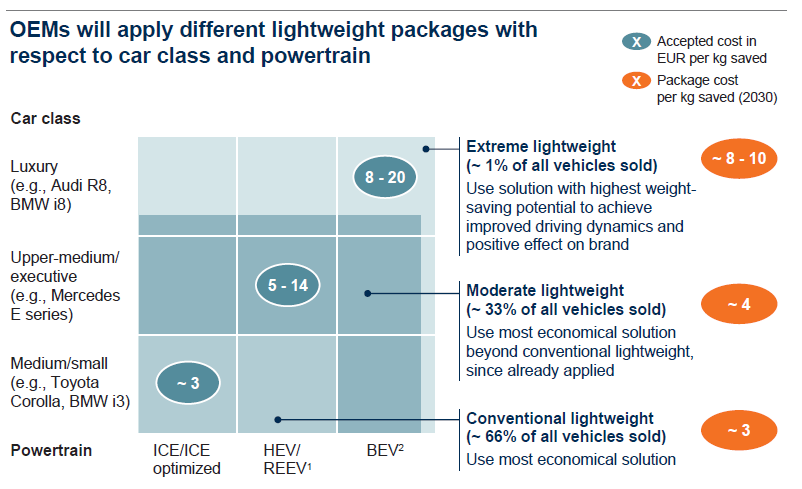
In the competitive environment of the automotive industry, OEM tries to maximize the efficiency of their material selection by lowering its costs and maintaining its quality [15]. The lightweight materials offer weight reduction but come at higher costs, which have made a noticeable difference in the price of the vehicle. For example, the use of high strength steel with 20% lighter and aluminum with 40% lighter, offers significant weight advantage over steel, however, but they are 15% and 30% more expensive, respectively [13]. Table 3 shows how lightweight materials are costly. But offer significant weight reduction is provided in Table 3.
Table 3: Weight savings and costs for lightweight automotive materials, Source: 15.
Steel
The most common material for vehicular body structures and other parts is still steel. Steel technologies are critical elements used in manufacturing a vehicle and mainly include the exterior body, engine, chassis, wheels and many other parts. The automotive industry has seen considerable development in new designs and redesigns over the past decade as steel industry heavily invests in innovation [16]. With the use of stronger steel, engineers can use thinner steel to improve strength and performance properties. Steel has the following advantages: high formability, relatively low cost, stable supply versatility, high impact resistance, broad hardening ability, excellent corrosion resistance, simplicity of assembly, reforming possibility in manufacturing and service life-cycle stages, well-developed repair and maintenance technology, and relatively easy recycling. Mass reduction through advances in the use of iron and steel are shown in Table 4 with 64.3% of the total vehicle in the late-90s model, and in the years 2011-2014 models have decreased significantly to 54.8% [9]. Lightweight steel and iron technologies compete with potential substitutes in all of these applications.
Table 4: Iron and steel percentages in vehicles and vehicle systems over time, Source: 9.
There are many types of steel used by vehicle designers to reduce weight, and they can be divided into three main categories [17], as shown in Table 5. First is the high-strength steels (HSS) that serve as the baseline for comparison with other steel in automotive design. Second, is the first generation of advanced high-strength steels (AHSS), and lastly is the second generation of AHSS. Each of these types has different physical attributes and metallurgical properties. For example, the principal difference in their microstructure. Based on the 2014 World Auto Steel AHSS Application Guidelines, HSS are single-phase ferritic steels, while AHSS contain a matrix phase such as ferrite, pearlite, or cementite, martensite, bainite, and austenite [17].
Table 5: Types of automotive steels, Source:17.
Also, some of the major distinction between HSS and AHSS is their total elongations or overall stretchability, yield strength/stress and tensile strength/stress (shown in Figure 4). The yield strength of HSS steel is between 210 to 550 Mpa, while tensile strengths range from 270 to Mpa. AHSS has yield strength greater than 550MPa, and the tensile strength higher than 700MPa.
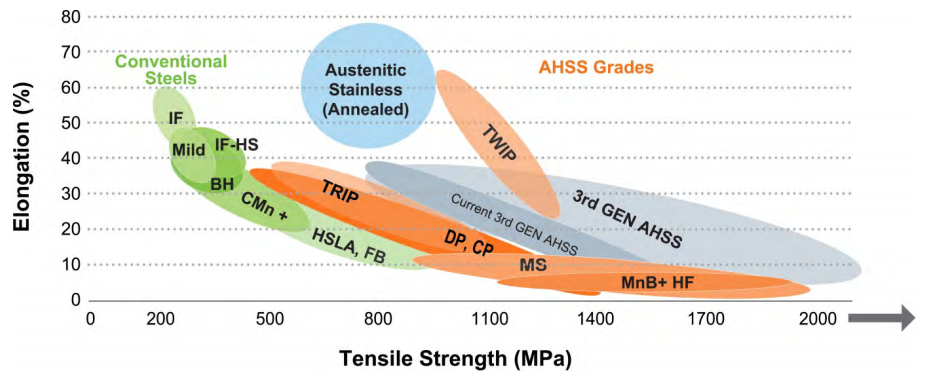
Types of Steel Used In Automobiles
High Strength Steel (HSS)
Steel suppliers are continuously developing steels with a range of strength and formability that will be ideal for any given application in the production of vehicles. The results of innovation are new formulations of iron, HSS, cost-effective use of stainless steel, new designs, assembly techniques, and weight reduction [16]. HSS or HSLA are manufactured using a combination of alloy compositions and processing methods to achieve strength, stiffness, and other structural performance characteristics with almost the same as mild steel [17]. Ultra-Light Steel Auto Body (ULSAB) has a yield strength of 210 Mpa and 550 Mpa; ultra high strength steel (UHSS) has a yield strength greater than 550 Mpa with material thicknesses ranging from 0.65mm to 2.00mm. HSS is compatible with existing manufacturing infrastructure [17]. It could reduce component weight by up to 25% (US Energy Department, 2015) [17].
HSS is also known as structural steels and is mainly used for structural applications. They are sought for their ductility through their simple ferritic microstructure, low carbon content, minimal microalloying elements, readily formed, and have good weldability [17]. The automotive industry is interested in HSS to achieve exceptional energy absorption of vehicle structures that will lead to a five-star EuroNCAP rating [18]. It resulted in more than a three-fold increase in consumption in the automobile industry from 2006 to 2010 [18]. Typical applications of HSS in a vehicle include automotive body structures, reinforcements, brackets, and various seating components such as pillars, risers, tracks, and towers [18].
According to Osayi [18], the USLAB program demonstrated that using HSS in Mercedes-Benz C-class body structure could result in a mass savings of 25%. HSS steel materials used in manufacturing doors, hoods, deck lids, and hatchback of vehicle body allow a significant optimization of vehicle body components and structures [18]. American Iron and Steel Institute (AISI) and ULSAB studies demonstrated mass reduction of 19% in a body structure that had superior strength and structural performance and it is considered as the relatively low cost and its accessibility is greater than a conventional steel body [16]. Oyasi [18] used Life Cycle Assessment (LCA) to study the greenhouse gas emissions of vehicles and he found that using HSS rather than can produce the smallest carbon footprint during the life cycle of the vehicle.
Mild steels or low carbon steels (LC)
Mild steel is known as carbon steel. It is defined by the American Iron and Steel Institute (AISI) as steel with low carbon content with no more than 2% carbon, (minimal alloying elements) making it formable, and has a simple ferritic microstructure known as iron. They make up the largest volume of steel production because of its widespread application and low cost [18]. Their applications in vehicles are body structure, closures, and other ancillary parts.
Solid solution strengthened (SSS)
SSS is the act of dissolving and combining one metal into another type of metal. It is a mixture of different atoms forming crystal structure that holds the mobility defects that creates obstacles against dislocation movements [18]. It is used on vehicle parts such as compartment railing, side panels, and rear longitudinal rails [18].
Bake Hardenable (BH)
BH or bake hardening is the way for improving the strength of the structure of the automotive components by positively exploiting strain aging [19]. According to Puttewar [19], BH has two hardening mechanisms: 1) strain hardening caused by cold stamping and 2) bake hardening due to finely dispersed hardening. It is an advanced processing technique used for car body panels and structural stampings that produce low carbon steels with high strength [19].
High strength low alloy (HSLA)
The need to improve safety and fuel economy, steel manufacturers, developed high-strength low-alloy (HSLA) steels or known as microalloying steels with improved weldability, ductility, and crash resistance [19]. They are made to give better mechanical properties with greater resistance to atmospheric corrosion compared to traditional carbon steels. They are used in vehicle parts such as the body in white, chassis, brackets, steering, suspension, bumpers, and wheels [19].
Advanced High Strength Steel (AHSS)
The World Auto Steel AHSS Application Guidelines (2014) stated that AHSS are steel with yield strength levels more than 550 Mpa. AHSS with higher tensile strengths exceeding 780 Mpa is known as ultra-high strength steel, while 1GPa or known as GigaPascal steel has a tensile strength of at least 1000 Mpa. Based on American Iron and Steel Institute (AISI) report that AHSS consumption in the automotive industry increased more than three times from 2006 to 2010 [19].
Based on the case study of AISI on the AHSS family car (2016), the development of steel and technology provides greater efficiencies such as the development of AHSS which can reduce vehicle weight from 17% to 25% of mass savings and cut greenhouse gas emissions by as much as 15%. AHSS also improves vehicle crashworthiness and penetration resistance [19].
AISI tested the use of AHSS in a five-passenger family car, and they found a massive reduction of 117kg, which corresponds to a lifetime savings of 2.2tons of CO2. This weight saving means less steel is required for each vehicle. For example, the weight of a typical five-passenger family care is 1,260kg, and the body in white (BIW) accounted for 360kg or 29% of the overall vehicle mass. BIW is consists of integrated box structure, panels, bulkheads, and sub-frames. With the use of AHSS in BIW, the structure was optimized to overall savings of 117kg. This weight reduction gives the automaker a chance to down-size the power train to achieve the vehicle performance. Table 6 shows BIW steel material grade analysis for a different range of car models by Puttewar [19]. It indicates that there is a gradual shift from MS to HSS and AHSS.
Table 6: BIW material grade analysis for different range of car models, Source: [17].
Steel industry developed a broad range of AHSS to meet the diverse properties and performance of vehicle parts and components economically viable on a high-volume scale:
Dual phase (DP)
The dual phase is also known as the two-phase structure, orchard phase or martensite and soft phase or ferrite. It is a combination of work-hardening and bake-hardening properties [17]. It is considered as the most common type of AHSS and is widely used in the automotive industry to increase strength and down gauge HSLA structural components [17]. This type has a very low yield ratio for a very high tensile strength. It is characterized by having good cold-forming properties and is suitable for pressed parts, particularly wheel disks.
High hole expansion (HHE)
High hole expansion is a stretch flanging performance of steel sheets. It is obtained by having a hole expanding test with the use of cylindrical or conical punch. This is used to increase the strength of the tensile [17]. According to Yadav [20], HHE is recommended for vehicle parts with sheared edge because of its stretchability and frangibility.
Stretch flangeable (SF)
The stretch flangeable (SF) is also known as Ferritic-Bainitic (FB) with soft ferrite and hard bainite. It has an improved stretch formability of sheared edges and ability to resist stretching on blanked edge [20]. It is composed of a microstructure of fine ferrite and bainite, coupled with grain refinement [20]. They are used for vehicle cross beams, wheels, suspension, and the chassis.
Transformation induced plasticity (TRIP)
Transformation induced plasticity steels have ferrite matrix is a combination of strength and ductility as a result of their microstructure [20]. The microstructure features are 5% retained austenite, plus martensite and bainite. It has a high hardening rates which are best for vehicle parts with complex shapes and high crash energy management because of its stretchability, elongation, and high energy absorption [20].
Complex phase (CP)
Complex phase steels are similar to TRIP in composition but they have less rained austenite but they contain fine precipitates and ferrite for hardening [20]. They are capable of good bendability, stretch frangibility, good wear characteristics, good crash safety features, and achieving higher strengths with lower alloy contents which enhance weldability at lower cost [20]. CP is used in vehicles parts, particularly in body structure, suspension, fender beams, door impact beams, reinforcements for B-pillar, and chassis components [20].
Boron heat treatable steel
Boron steels have been designed to enhance hardenability during heat treatment. They are considered the most potent alloying element because they provide better extrudability, machinability, and are less susceptible to cracking and distortion during heat treatment than conventional steels [20]. Boron steels containing carbon and alloy steels are widely used in the automotive industry for axle parts, excavator teeth, wiring, sheet, strip, plate, tubular, rod, rotors and bar.
Twinning induced plasticity (TWIP)
TRIP is part of the second generation of AHSS. It is known for its combination of very high strength with extreme elongation capacity [20]. It is a kind of austenite steel containing high-manganese steels up to 30% combined with Interstitial-free steels (IF) and TRIP strength for high rate of work hardening that is highly ductile resulting from formation of deformation twins [20]. The work of Frommeyer et al. (2003) renewed the interest in the properties of high Mn TWIP steels for the automotive industry [21].
Lightweight steels with induced plasticity (L-IP)
Lightweight steels with induced plasticity (L-IP) is a combination of lightweight steel and transformation induced plasticity (TRIP) which is a development of stronger and lightweight steel. It is a further alloying elements reduced in density while the strength remains the same as TRIP steels [21].
In response to automobile industry demands for more efficient AHSS capabilities, steel industry, academic institutions, and research laboratories continue to search for new types such as the third-generation AHSS to reduce weight and cost while increasing strength.
Aluminum
The use of aluminum started in 1899 with an aluminum body of a small sports car followed by the introduction of Parisian buses in 1910 to commercial vehicles in the 1930s [21]. Aluminum usage in the automobile has grown substantially within past years from 110kg of aluminum in 1996 to 142kg in 2007 to 170kg per vehicle by 2020 [21]. Based on the forecast reports of Ducker Worldwide and Aluminum Association (2011) as shown in Table 7, there is a net increase of aluminum net pounds per vehicle from 2008 to 2025 vehicle models and a major decline of HSS such as FR, BH, and HSLA. Properties of aluminum have higher strength, stiffness, and lifespan ratio in comparison with advanced metals like HSS [21].
Table 7 Average light vehicle material content in net pounds per vehicle, Source:21.
Global material flow balance for aluminum industry as of 2010 is 50.5 million metric tons of finished products into use in which automotive industry accounts for 16%, and 11 million metric tons of aluminum are old scrap recovered for recycling [21]. European car manufacturers have taken technological advances for aluminum applications in the light weight passenger vehicles as shown in Table 8. There is a broad range of opportunities for employing aluminum in vehicular body structures, chassis, driveline, engine, heat exchangers, power train, transmission, and wheels as shown Figure 5.
Table 8: Europe leads vehicles light-weighting, Source: 21.
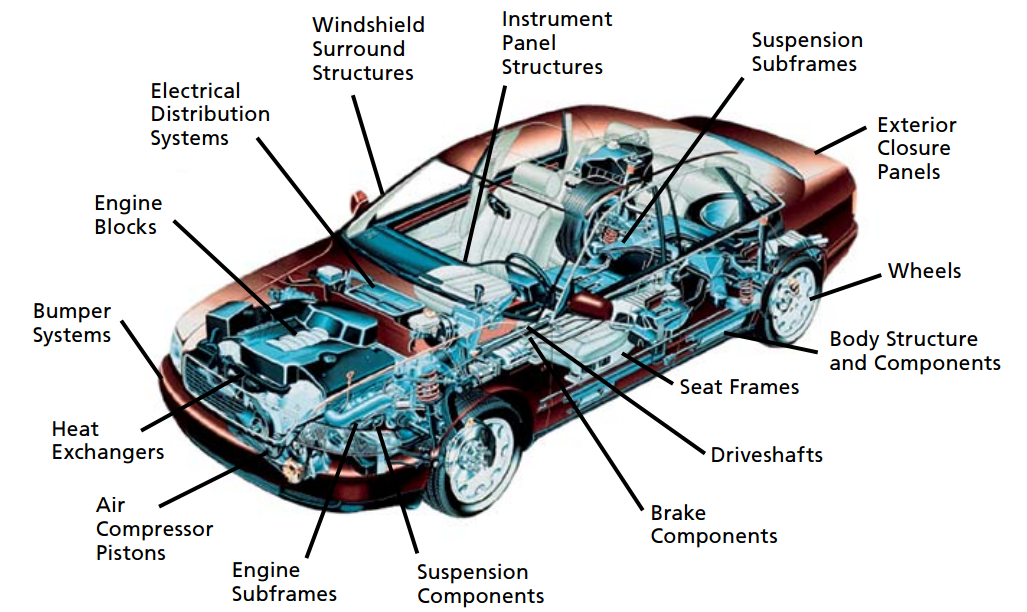
Based on Aluminum Automotive Manual (2013), the first car manufacturer to introduce all-aluminum body frame was the Honda Acura NSX in 1989. At present, Audi A8 and Jaguar XJ are popular aluminum-intensive car models developed further the light-weight vehicle technology such as a further extended use of lightweight aluminum casting, extrusions, and stamped panels are known as space frame [21]. Figure 6 shows Ducker Worldwide Report (2012) on the 2012 car models on weighted average aluminum content. It proves that Jaguar is the leader while Fiat car manufacturer has the lowest aluminum content.
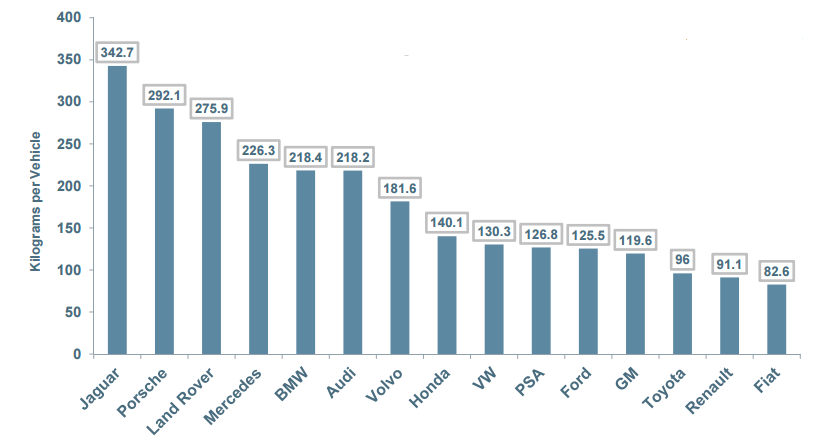
According to Cole and Sherman (1995), there are two methods of designing and manufacturing an aluminum body structure. First is the steel construction using stamped option. And the second is the space frame which involves castings, extrusions, and stampings welded together, for example, aluminum castings have been used in power train for almost 100% of pistons, about 85% of intake manifolds and transmission, and 75% of cylinder heads. Aluminum castings have been applied to various automobile parts for an extended period. According to Szeteiová, Katarína (2012), the material for engine blocks, which is considered as one of the heavier components, it is being switched from cast iron to aluminum resulting in significant weight reduction. The use of aluminum in the manufacturing of vehicle offers advantages. For example, reduction of weight of the exterior panels of a vehicle because they are two times lighter than a regular steel body, such as, a 0.8mm steel component can be substituted by a 1.2mm aluminum which can be reduced up to 50% of weight [22].
Types of aluminum used in automobile
Aluminum-manganese (3xxx)
The combination of aluminum with manganese provides greater solid solution strengthening with ultimate tensile strength of 110 to 285 Mpa (16 to 41ksi) which account a quarter of the total usage of aluminum [22]. They have good corrosion resistance, good formability and non-heat-treatable materials suited at elevated temperatures. Typical applications of 3xxx in an automobile include exchangers, sheet, and tubular.
Aluminum-magnesium alloys (5xxx)
5xxx is the highest strength non-heat-treated aluminum alloy with ultimate tensile strength of 125 to 350Mpa (18 to 51ksi) that is considered the most extensively used for wide variety of structural applications [22]. Such alloys have excellent corrosion resistance, toughness, and weldability. Series 5252, 5457, and 5657 are used for automobile trim applications while series 5754 is used for body panels and frame applications. 5xxx alloys are mostly used in North America [22].
Aluminum-magnesium silicon alloys (6xxx)
6xxx alloys, in particular, AA6016 is mainly used in European automobile industry among due to the outstanding combination of elongation, dent resistance and surface constancy [22] as shown in Table 9. The 6xxx are heat treatable with ultimate tensile strength of 125 to 400Mpa (18 to 58ksi) [22]. They have excellent corrosion resistance, excellent extrudability, and with a yield strength comparable with mild steel. They are commonly used in vehicle handrails, bridge structure, electrical conductor wire, frames, tubular, and shafts.
Table 9: Modern automobile aluminum alloys, Source: 22.
More than 90% of aluminum currently produced for building, automotive and transportation in the EU countries originates from scrap or recycled raw materials [22]. Used aluminum from vehicles has a high scrap value, and they can be sold at an excellent price in the second and third-hand market because they are easily recyclable. It also has a high corrosion resistance that offers financial savings, long service life, and scrap costs up to 50% than steel with only 15% [22]. Figure 7 shows the forecast in North America that aluminum will grow from 327lbs in 2009 to 550lbs by 2025. By 2025, every automobile manufacturer will have an aluminum body program in its operation making light weight vehicles the most significant industry for aluminum [22].
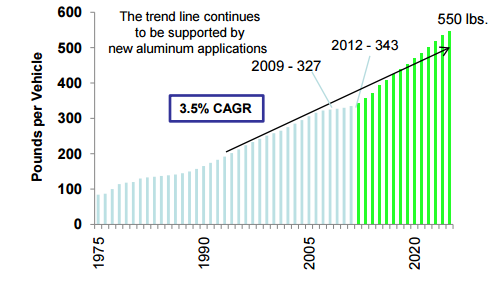
Plastics and polymers in general
First synthetic plastic known as phenol formaldehyde (PF) or Bakelite was introduced in 1907. In 1916, Rolls Royce used of Bakelite in its car interiors [22]. The first mass-produced vehicle with glass reinforced plastic chassis is Chevrolet Corvette in 1953 [22]. Plastics and polymer composites currently make up about 8% of a vehicle by weight and 8% of raw material costs of a vehicle (Automobile Engineering Partners, 2015). According to Economics & Statistics Department and American Chemistry Council (2015), in 2014, there are 14.08 million light vehicles manufactured in the United States and Canada required some 4.6 billion pounds of plastics and polymer composites valued at $6.1 billion.
According to American Chemistry Council report [22] “plastics refers to two-dimensional chains or three-dimensional networks of repeating chemical units formed into a material. The majority of manufactured plastics are thermoplastics, two-dimensional chains that, once formed, can be heated and reformed over and over again. The other group of plastics, called thermosets, is formed by creating three-dimensional networks that do not melt once formed. Both types of plastics are used in automotive applications today.” At present, the most type of plastics used in the automotive component is thermoplastic materials which can substitute metals in the future [22].
The advantages of using plastics are weight saving, design flexibility for high complex shapes and sizes, corrosion resistance, easy assembly, material anisotropy, mechanical properties, and negligible damage after low-velocity impact [22]. However, they are hindered by used vehicle disposal and recycling [23]. They also have a high material cost of fibers which is ten times greater than using carbon fibers, long production cycle times, and recycling challenge which hindered volume scale of plastics in automotive applications [23]. Average volume of plastics content of light vehicles in North America as of 2015: polypropylene (PP) (25.8 %), polyurethane (PUR) (17.9 %), and nylon (11.2 %) as shown in Table 10 (Economics & Statistics Department and American Chemistry Council, 2015). Plastics used in Volkswagen vehicle by thousands of tons weight as illustrated in Figure 8.
Table 10: Average large volume plastics content of North American light vehicles (pounds per vehicle), Source:22.
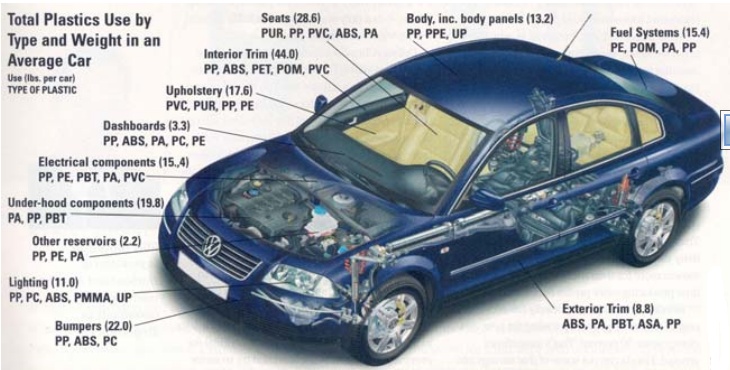
Types of plastics used in automobile
There are 13 different types of polymers used in a single car as shown in Table 11 23.
Table 11: Plastics/Polymer used in a typical car, Source: 23.
Polypropylene (PP)
Polypropylene is widely used plastic in a wide variety of applications with a tensile strength of 25 to 33Mpa. It is a thermoplastic polymer with properties includes semi-rigid, translucent, good chemical resistance, good fatigue resistance, integral hinge property, good heat resistance, and offers excellent electrical and chemical resistance at higher temperatures [23]. They are commonly used in automotive bumpers, battery boxes, bottles, carpet fiber, cable insulation, chemical tanks, indoor and outdoor carpets, and petrol cans [23].
Polyurethane (PUR)
Polyurethane is thermosetting or thermoplastic with exceptional properties variance including rigid, flexible, soft, solid, or cellular. Physical characteristics of Polyurethane are hydrolysis-resistant, good flexibility, excellent abrasion and adhesion resistance to weather, ozone, radiation, oil, gasoline and most solvents [23]. They are commonly used in automotive suspension bushings, cushions, elastomeric wheels and tires, electrical potting compounds, flexible foam seating, foam insulation panels, hard plastic parts such as electronic instruments [23].
Polyvinyl-Chloride (PVC)
The essential materials of polyvinyl chloride are 43% ethylene from oil and 57% chlorine from salt water with a tensile strength of 2.60 N/mm². PVC has good thermal stability, good resistance to chemical and solvent attack. Molding compounds of PVC can be extruded, injection molded, compression molded, calendered, and blow molded to form a huge variety of products. They are commonly used in automobile instruments panels, chemical tanks, floor covering, interior doors panels and pockets, pipes, protective strips, sheathing of electrical cables, sun visors, and waterproof clothing [23].
Acrylonitrile Butadiene Styrene (ABS)
Acrylonitrile-butadiene-styrene is a durable thermoplastic made by styrene-acrylonitrile san copolymer (SAN) and fine polybutadiene rubber particles with a tensile strength of 40 to 50Mpa. The styrene gives the plastic a shiny, impervious surface. It is good for structures that required strength, impact resistance and stiffness. It is easy to be painted and glued with stable dimension. They also have electrical properties over a wide range of frequencies.
Polyamide (PA)
PA is known for nylon 6, nylon 6/6, and nylon 12 with a tensile strength of 48 to 85Mpa. Nylon is a crystalline polymer with high heat distortion temperature, high modulus, strength, low coefficient of friction, sharp melting point, low melt viscosity and resistance to abrasion [23]. It also absorbs water in wet or humid conditions. They are used in bearings, bushes, cams, carpet liners, gears, reinforced structural parts, tire cord, upholstery, and weather proof coatings.
Polystyrene (PS)
PS is commonly produced in three forms: extruded PS, extruded PS foam, and expanded PS form [23]. It is a polymer made from the aromatic monomer styrene with a tensile strength of 30 to 100Mpa. It exhibits excellent chemical and electrical resistance but poor UV light resistance. It can be used in buttons, car fittings, display bases, and equipment housings.
Polyethylene (PE)
PE is a semi-crystalline polymer. It is strong, low density, exhibits good toughness, lightweight thermoplastic with strong chemical resistance, and a versatile synthetic resin. It also exhibits resistant to concentrated acids, alkalis, many organic solvents. PE is classified into many categories: ultra-high molecular weight PE (UHMWPE), high-density PE (HDPE), medium-density PE (MDPE), low-density PE (LDPE), and very low-density PE (VLDPE) [23]. They are commonly used in body panels and electrical insulation.
Polyoxymethylene (POM)
POM are formaldehyde-based thermoplastics. It is a plastic with metal like features used in vehicle precision parts that require high stiffness, excellent chemical resistance, low water absorption, low friction, and excellent dimensional stability [23]. It is widely used in caster and wheels, bearing, fasteners, frames, fuel pumps, lock systems small gears,
Polycarbonate (PC)
PC exhibits hardness, toughness, stiffness, excellent weathering, UV resistance or excellent optical clarity, good resistance against high temperatures and high impact, electrical and thermal properties, and low flammability. It has a tensile strength of 60 to 70Mpa [23]. They are used in bumpers, central panels, headlamp lenses, security screens, and spectacle lenses.
Polymethylmethacrylate (PMMA)
PMMA or known as acrylic is a highly transparent. It is 40 to 50% lighter than conventional glass which transmits up to 92% of visible light [23]. It also has a good impact strength, uniform thickness tolerance, and better shatter-resistant than glass. They are used in displays, headlights, glazing, screens, and windows.
Polybutylene Terephthalate (PBT)
PBT is typically used in airbags, brake and fuel clips, bumpers, door handles, mirror and sensor housing, power fuse and switches, ignition, and windshield wipers [23]. It is semi-crystalline polyester. It is highly chemical and heat resistant. It has a wide range melt viscosities for molding and extrusion.
Polyethylene Terephthalate (PET)
PET is known as polyester in the textile industry and is commonly used in plastic bottles and containers. It has excellent surface properties, good thermal stability, good electrical properties, and excellent resistance to gas, moisture, solvents, and chemicals [23]. It is widely used vehicle wiper, headlamp, and engine cover [23].
Acrylonitrile Styrene Acrylate (ASA)
ASA are amorphous plastics similar to ABS. It has great rigidity, toughness, good chemical resistance and thermal stability, outstanding resistance to weather, aging and yellowing, and high gloss [23]. Typically used in boxes of connectors and electronics, bumper covers, drip rails, exterior side view mirror, radiator grilles, and housings.
The common type of composites is glass fiber reinforced thermoplastic polypropylene, which is applied to brackets for the instrument panel, door inner structures, door surrounds, and rear hatches, roofs. Other types include glass mat thermoplastics, bulk molding compounds or glass fiber reinforced thermoset vinyl ester, and sheet molding compounds made of glass fiber reinforced thermoset polyester. Carbon fiber reinforced polymer (CFRP) composites are more expensive and less popular due to the cost of $13–$22 per kilogram, compared to $1–$11 per kg of glass fibers, although they offer significant strength and weight-saving benefit. Recycling of composites is still the main challenge during vehicle disposal because it remains in shredder fluff and landfills [23]. The research and development of the biggest plastic suppliers are continuously working to develop biodegradable plastics for wider applications and easy dismantling and recycling [23].
Concluding remarks
This chapter considers a new form of lightweight automobile materials use as parts and components such high-strength steels, aluminum, plastics and polymers as a material substitution as a means to achieve weight reduction. It also shows its benefits of each materials used in by the automotive industry. It highlights the advantages of using lightweight materials in a passenger car structures, from both economic and environmental perspective. Weight reduction of the vehicle has a significant effect on its lifetime monetary cost. It provides weight savings in the overall car mass which is considered to be a major research focus not only for vehicle manufacturers but also by Original Equipment Manufacturers (OEMs) since materials have different requirements regarding costs, applications, formability, resistance, strength, temperature, and weight.
Automotive recycling
In pursuit of a competitive position in the market, vehicle manufacturers have responded through advanced research and development programs on material selection, engineering efficiency, and end-of-life resource recovery strategies [24]. This study explores the concepts embedded in the industrial ecology with a specific focus on the automobile to help highlight the potential to enhance sustainability performance. It is an attempt to demonstrate ecological processes in vehicle manufacturing. It highlighted some environmental aspects and processes regarding types of system of IE, principle components of automobiles that affect the environmental aspects, concept of automobile lifecycle, and the recycling aspect of the automobile. The objective is to present IE plays a significant role in evaluating the efficiencies of vehicle industrial ecosystems manufacture and operation.
It provides an expanded perspective of IE of the automobile by analyzing the life cycle of the automobile. The current issues regarding the environmental concern, climate change has greatly affected the creation of the automobile. However, the automobile industry is always faced with many challenges and stringent regulations for each life cycle stage and more dramatic changes in vehicle design because of customer demand for the fuel-efficient vehicle, material intensity, safety, comfort, emissions, and recyclability. Innovations can be made incrementally such as material selection because weight, toxicity, and recyclability will have a big influence on the decision of vehicle manufacturers. IE is a set of interrelating systems that are perceived as a whole. Through IE integration, vehicle manufacturers will hopefully be able to develop efficient strategies to facilitate the use of materials and energy resources and to reduce hazardous waste. Innovation is the primary factor that changes the life-cycle of the automobile. Like the first car was made with Type 1 model and once reach its end-of-life, it ended up as junk. Heavy metal for junk but with the current Type 3, almost everything is reusable and recyclable. The Type 3 can become almost self-sustaining, only requiring maintaining the basic functions of the vehicle with little input. For example, the waste material of a discarded vehicle will automatically become useful raw materials for other processes and products.
IE is a new direction by making more efficient in resource and less dependent upon non-renewable resources. As stated by [24] for small vehicle manufacturers, IE will improve their strategic planning and compliant with environmental requirements. For medium sized manufacturers, IE will improve their manufacturing process without sacrificing the quality of their vehicle vis-a-vis environmental concerns. For large manufacturers, IE will make a big difference by designing policies with the government for local and community solutions. The three types of system models are presented below in Figure 9.
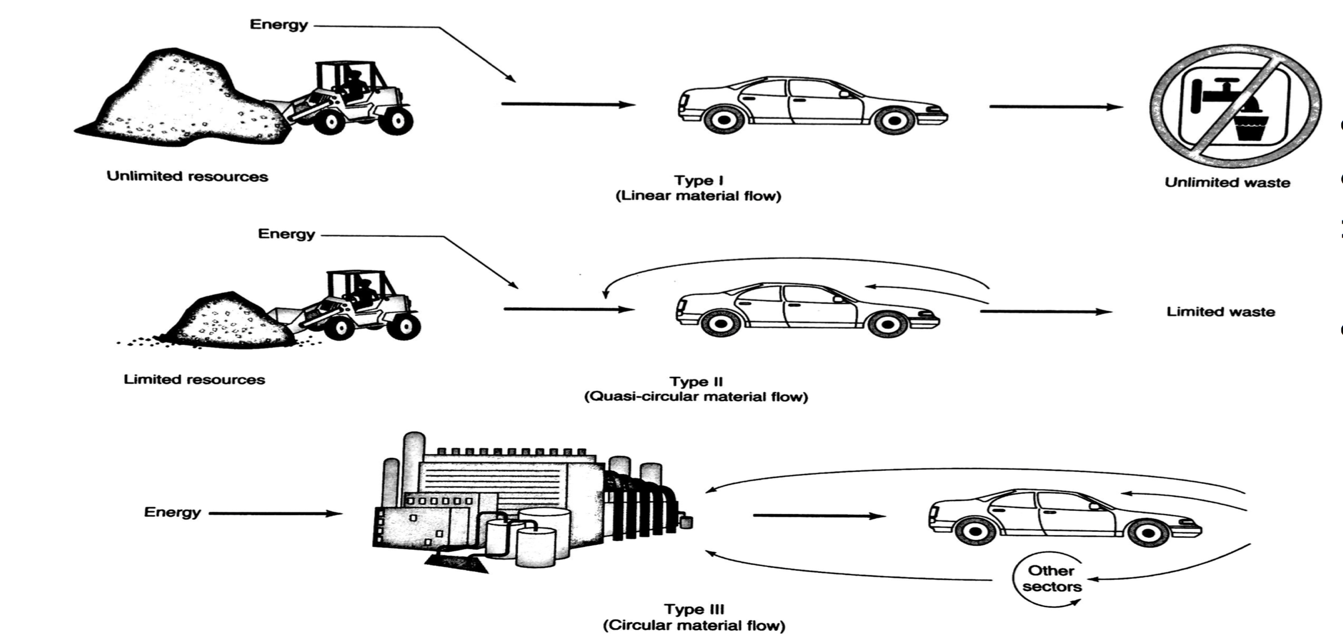
Types of System Models
Type I – Linear
In this system, the virgin material is entered into the system control volume and used only once. After the virgin material is used, it is disposed to like waste material. The term “waste” can be defined as the material that cannot be used further in the current or other systems without significant processing applied to it. The waste is different from residual that can be used in the system as a whole but not in the generation phase. The type I system is not the result of only technological changes, but it is also the result of some economic calculations and social factors. For example, cars may have been abandoned because of its inability to support recycling of the metal used in the car [25].
According to Jelinski, Graedel, Laudise, McCall, & Patel [26], material cycles has been involved in the earliest life forms on planet earth. At that time the usable resources were present in large quantities, and the amount was relatively short therefore there was no impact on the available resources. This individual component was described as linear where the flow of material at one stage to another is independent of all the other stages and flows [26]. According to Garner &Keoleian [27], Type I system is referred to as a linear process in which the energy and material enter one part of a particular system and come out of the other part in the form of a by-product/waste and products. The wastes of this system are not reused and recycled this scenario and are dependent on constant raw material supply [27].
Type II – Quasi-circular material flow
The complex Type II system arises because of growing population or scarcity. This type of system makes the Type I system inadequate and internal cycling loops and feedbacks often develop in this type of system. The material that flows in the system waste which comes out of system diminishes. In this type of system, internal reuse of material is significant. The internal velocity of the material within the system may be high, but the velocity throughout the system is reduced. An example of Type II or Quasi-circular material flow is the life cycle of the cars of today’s developed economies. The useful sub-assemblies of the post-consumer car are removed and recycled so that parts can be used effectively. The steel which is about 75% of the total material is recycled, and the remaining material is shredded. This is also known as the internal material loop. The “fluff” which is another material like plastic, liquids and glass are land filled [25].
According to Jelinski, Graedel, Laudise, McCall, & Patel [26], a contrasting picture of an ecosystem can be presented where the proximal resources are limited. In such type of ecosystem, the life forms are strongly interlinked to form the complex networks known as biological communities. According to the author in this type of system, the material flow in the proximal domain is quite large, but the material flowed out of the domain and is known as waste. The author advocates that Type II system is efficient in comparison to Type I system which is not sustainable for long-term as all the flows are in a single direction i.e. system is “running down.” To be sustainable, the ecosystems which have been evolved have to cyclic so that waste of one system can be the resources for other systems [26]. According to Garner &Keoleian [27], the Type II system characterizes the present day industrial system where some of the wastes are recycled within a system while other are left. According to Ginley [28], the Type II system can be applied in the industrial setting where some of the waste material can be recycled while other cannot be recycled.
Type III – Circular material flow
The Type III system is the system that has achieved full cyclicity. The Type III realization should be the ultimate goal of all the products and automobile design and management across the life cycle of products. This vision will, however, be difficult to achieve because the material is degraded after the first single use. In other words, some of the important aspects of the automobile technological systems are dissipative. For example engine oil has to be replaced regularly because fuel is burned and degraded (loss of viscosity) due to the heat in the combustion engine. Another example is the rubber tire that also disintegrates into residues on the roadways. The current technologies should, however, focus on reducing the amount of residue or the dissipative uses. The modern engine sensors are the solution for the dissipative uses. These sensors can help in determining the need of changing the oil which will help in reducing the number or frequency of oil changes [25].
According to Jelinski, Graedel, Laudise, McCall, & Patel [26] the Type III, material flow is the most efficient material flow because it is completely cyclic in nature and waste and material in this system is system is undefined. The author states that industrial ecosystem moves from Type I to Type II and to move to Type III material flow it is essential to create some of the missing entities [26]. Type III system represents a dynamic equilibrium of an ecological system. In this type of system, the energy and wastes are reused and recycled by the other processes and organisms within a particular system. The author agrees with the fact that this type of system is closed and highly integrated. In other words, it is an entirely closed system where only solar energy comes out outside whereas other products are consistently used within the system [27]. The study by Ginley [28] also highlights that Type III system should be the ideal goal of the industrial ecology as it represents the sustainable state. All the systems discussed above are energetically opened as the constant input is solar energy. One of the major constraints is that energy which is used in systems should be sustainable.
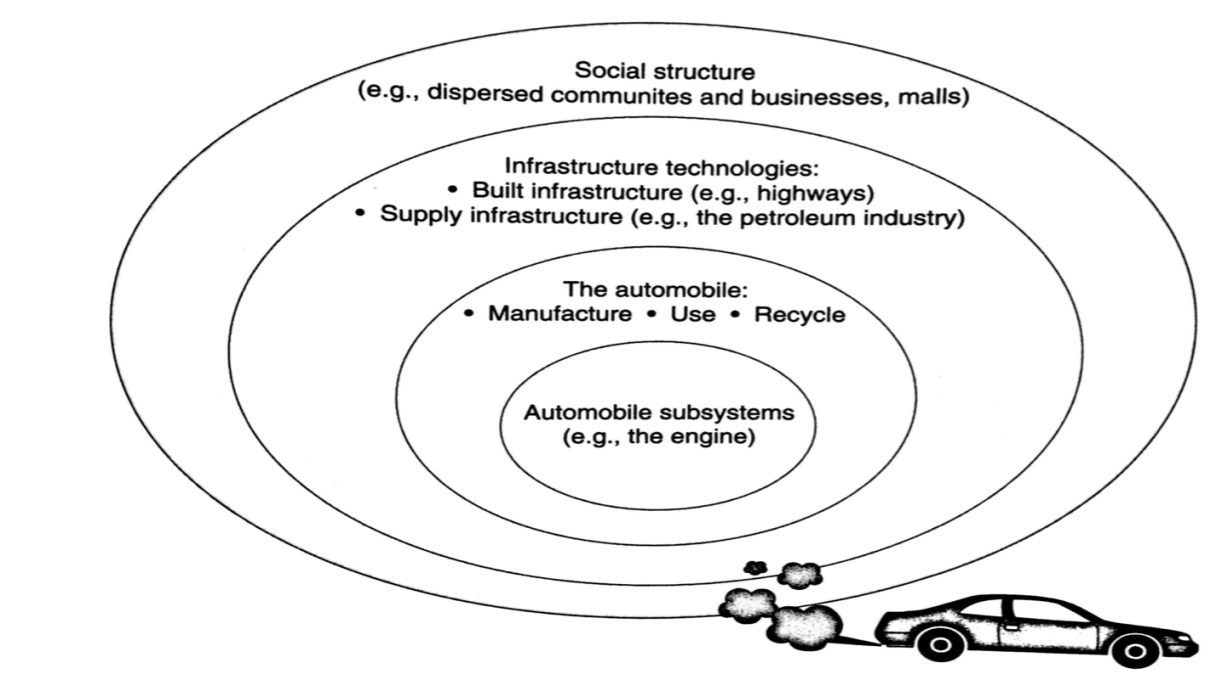
Steel and aluminum are good metals to manufacture the automobiles. The author also suggested the method to make steel lighter by adding aluminum to it. If in steel, aluminum is added then ultra-strong compounds with iron have formed that help in the longevity of the automobiles. The new steel according to the author is novel, and it has an interesting development. The major drawback is that steel is not a cheap metal. The new metals like titanium alloys are also expensive. Therefore they cannot be used in passenger vehicles. Aluminum is known as a lightweight alternative to steel [11]. The automotive industry is using the aluminum because of higher market prices. The strength of aluminum is, however, lower, but the strength of advanced steel is very high. The author advocates that new manufacturers are replacing steel completely with aluminum because of light weight metals. The domain of luxury manufacturers is also maintained because of the aluminum [12].
Automotive Components and Systems Development
There are some parts and systems that constitute the modern automobile. Below are some principle components of automobiles that affect the environmental aspects.
Chassis
The first automobiles were manufactured by the carriage makers. Therefore, those consist of chassis which were duplicates of the vehicles pulled by the horses. Chassis are made up of steel for the extremely rugged conditions. The chassis were heavy and were used according to the wish of drivers. There is a huge difference between olden days and modern day’s chassis. Modern day’s chassis is designed of high-strength steel so that chassis can get longer lives along with modest weight. The components of the body can be either of steel or aluminum. It is essential to use a diverse material in the chassis and frames to design a car with reliability, good performance, and light weight. In the original engine, most of the components were made up of steel like rods, pistons, shafts and axels [25].
Chassis can be referred to as basic framework of a particular automobile. It supports the different part of the vehicle that is usually attached to it. It is made of forged steel. The important systems of an automobile such as transmission, power plant, suspension, steering, and braking system, etc. are attached to chassis so that all these parts can get a support [14]. There are some essential functions of chassis such as it is used to carry the stationary loads, withstanding the torsional vibration that is caused because of the movement of the vehicle. The chassis is also used to resist the force called the centrifugal force that is caused by the movement of the vehicle [15].
Fuels
Another important component of the body is gasoline and fuel. In 1930’s engines were developed with compression ratios and there was a need of including fuels in the anti-knock elements of the body. In this case, TEL (Tetraethyl lead) was most effective fuel. The TEL has many positive attributes like it provided valve seat lubrication, but it was also associated with negative attributes like lead emission which provide human toxicity problem. The lead in motor vehicles was eliminated. Also, ethanol was mixed with different percentages of gasoline so that an effective fuel extender can be made. This type of fuel extender was made in Brazil decades ago [25]. The fuels prices are going up along with the increasing environmental concerns. Therefore, there is a need to develop the fuel alternatives that are efficient and less pollutant. There is pressure on the automobile industry to include the gasoline-hybrids, hydrogen, ethanol, diesel, and full electrics. This alternative fuel technology is rapidly changing [29].
Tires
In the original automobile, wheels were made up of iron stripes which were connected with spokes. These types of tires were however replaced by solid rubber tires in early 1990’s. These tires were the pneumatic tires which were filled with pressurized air. In 1950’s the tires also contained an inner tube, but soon they were replaced by a tight seal. In modern times, tires are not just the rubbers, but they have fiber belting that provided them strength by including other ref work in recycling automotive tires [25]. According to Islam [17], tire waste pyrolysis plants can be used for recycling the tires. Moreover according to Omar [30] also the pyrolysis process is clean and produces little waste.
Brakes
The brakes in automobile operate because of friction that is caused by rubbing the two surfaces together. On the accomplishment of the brake operation, one of the surfaces is abraded. Until 1930’s the brakes were operated using the foot pressure as well as cables. In other words brakes until then were completely mechanical. The mechanical brakes were replaced by hydraulic brakes because of the increased weight of the vehicles. The hydraulic fluids used in the brakes are glycol ethers and glycols [25]. According to Puttewar [19], electromagnetic brakes are another revolution in the category of brakes that is used in both the light weight and heavy weight vehicles. The author states that electromagnetic brakes system is composed of a combination of electro-mechanical concept [19].
Cooling systems
The engines in automobiles are cooled using a fluid that carried away the heat to the radiators. The original coolants which were used were methanol and ethanol. These were mixed with water appropriately so that freezing can be avoided. At the beginning of 1993, another coolant was used, the new vehicle was supplied with HCF-134a (CF3CFH2) which is now known as one of the biggest causes of ozone depletion [25]. According to Yadav [20], the refrigeration units that are being used currently in the vehicles is associated with vapor compression refrigeration (VCR). One of the most commonly used gas for cooling in vehicles is R14 refrigerant gas [20].
Lubrication
The first lubricant from the 19th century till present is composed of petroleum derivatives with the particular composition. Additives like detergents, corrosion inhibitors, and dispersants were used for lubrication. In other words, oil was not the only lubricator, but it was used for cleaning the engine, preventing the rust and reducing the friction. The motor oil, however, has to be replaced on time because it becomes less effective because of chemical breakdown [25].
Electric Power
The original installation of electric systems on the automobiles was done in the year 1912. The electrical systems in automotive used to operate in the complex environment. The platinum was used in the spark plugs in 1995. The use of platinum in the spark plug led to control in the spark process [25].According to Holmes 21, there was number of problems that are caused because of gasoline engines and hence there was a need to develop an electrical powered vehicle.
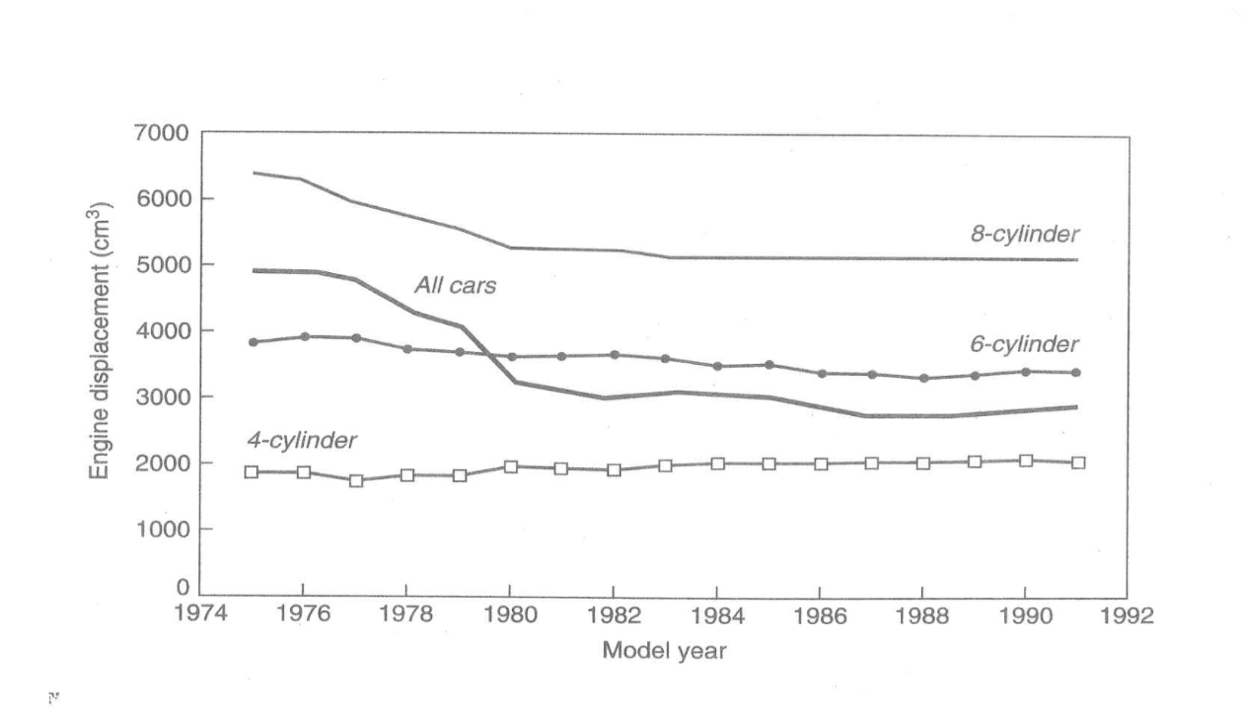
Bumpers and body trims
Historically the bumpers were made up of heavy gauge steel and until the middle of 1980’s the bumpers were chrome plated. The side stripping in the automobiles was also chrome plated. The steel is used in the front ends, and rear bumpers and the chrome plating has been reducing in the automobile industry. An alternative to steel f bumpers is aluminum that is also widely used because of light weight and ability to recycle. Aluminum can be used in all most all the nonstructural areas of automobiles. It is not that aluminum has replaced steel in all the aspects because welding of aluminum is a typical process [25]. According to a Szeteiová [22], nowadays plastic is one of the most important in manufacturing the bumpers and trim of the automobiles.
Paint
The body panel of the vehicles is always painted to prevent the body from corrosion as well as for the aesthetic reasons. The paints are the traditional pigments that are composed of an organic element. In 1980’s the efforts were made to make the aqueous paints and in 1990’s the powder paints were introduced so that they do not involve any solvent. According to Ju [23], quality flow model is one of the most widely used concepts for painting the automobiles.
Electronic monitoring of vehicle performance
In 1980’s the electronic monitoring the performance was introduced and eventually became an integral part of the overall automotive system. The copper was the major connector along with the mixed material circuit board. The recovery and recycling of the electronic components are necessary for an efficient performance of automobiles [25].
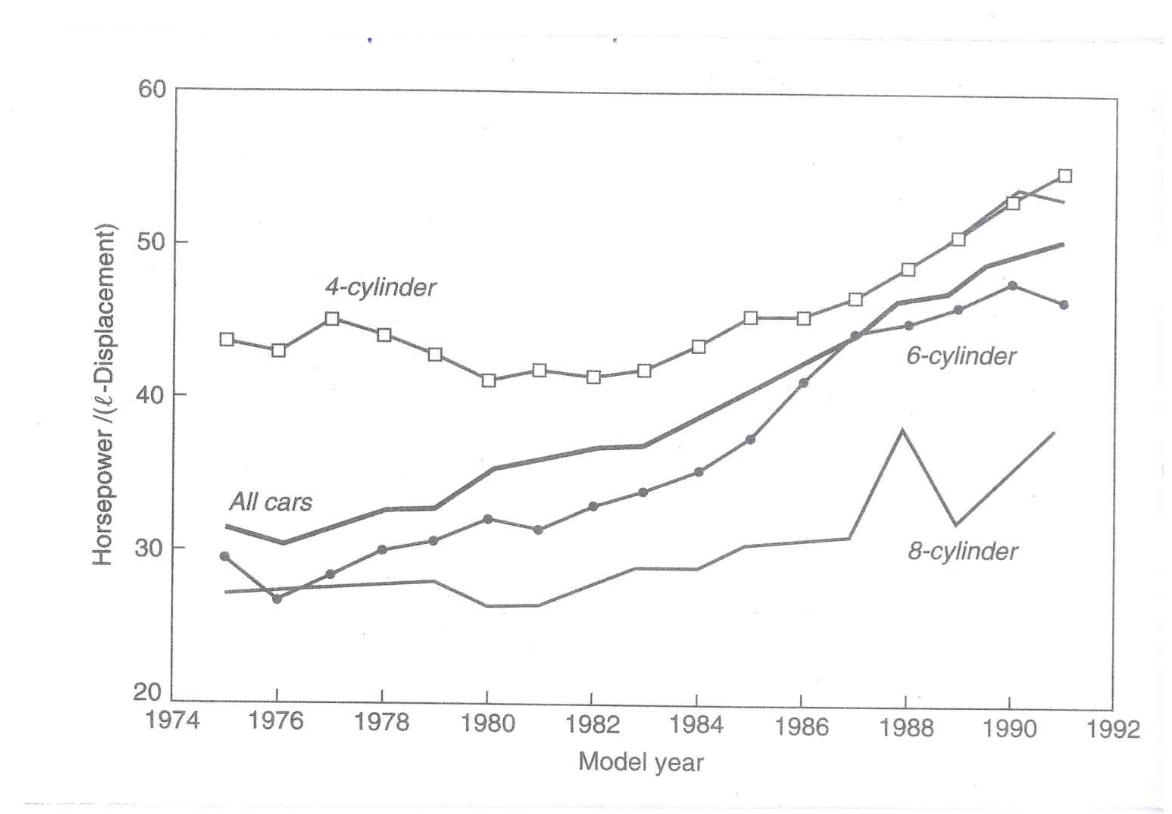
Emission control system
The vehicles in the 19th century emitted heavy clouds of smoke. In 1909, the oil control piston rings were developed to control the emission of smoke. With the gradual realization, the gaseous emission new ways of controlling the gaseous emission were evolved [25]. According to Millstien [24] in future the heavy-duty diesel vehicle emission controls systems will be used to reduce the amount of emission.
Airbags
In 1980’s the automobile manufacturers also installed air bags to protect the passengers from the incidents of a collision. From 1990’s the air bags were considered as a universal aspect of the automobile industry. In a context of the recycling of the airbags used in the automobiles, the use of OEM Non-Deployed Airbags is recommended by many of the researchers and industry professionals. The use of these bags is safe, viable and economical. These bags can be recycled so that the material can be used in the manufacturing.
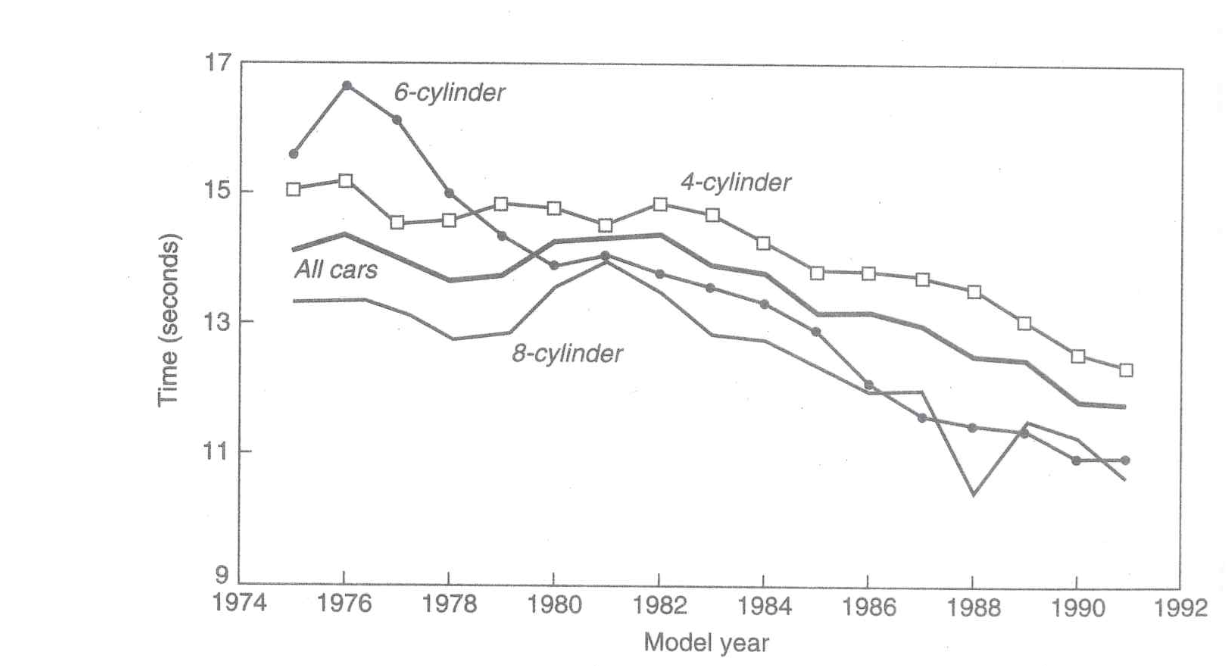
Lifecycle of an Automobile
An automobile has a particular life cycle with six stages. The lifecycle of a vehicle starts with the stage of extraction of raw material from the different sources. The sources can include the recycling stream and the virgin sources. The materials like rubber, metal ores, coal, and petroleum are extracted for manufacturing the automobiles. In the material processing stage, extracted raw materials are processed with the help of different industrial techniques. The processing is done to convert the extracted material into the finished material. This stage is one of the most important stages in the context of manufacturing the automobile. The next stage is manufacturing stage. The metals are bent and given a particular shape, and other processes associated with assembly and other operations are performed on the finished material. In this stage, operations are needed to manufacture the assemblies and subassemblies. The product completion stage is followed by the processes of packaging, delivery, and customer use. In this stage, the product is delivered to the customers. The last stage is the end of life that indicates that product after this stage is of no use and as to be disposed of or recycled [25].
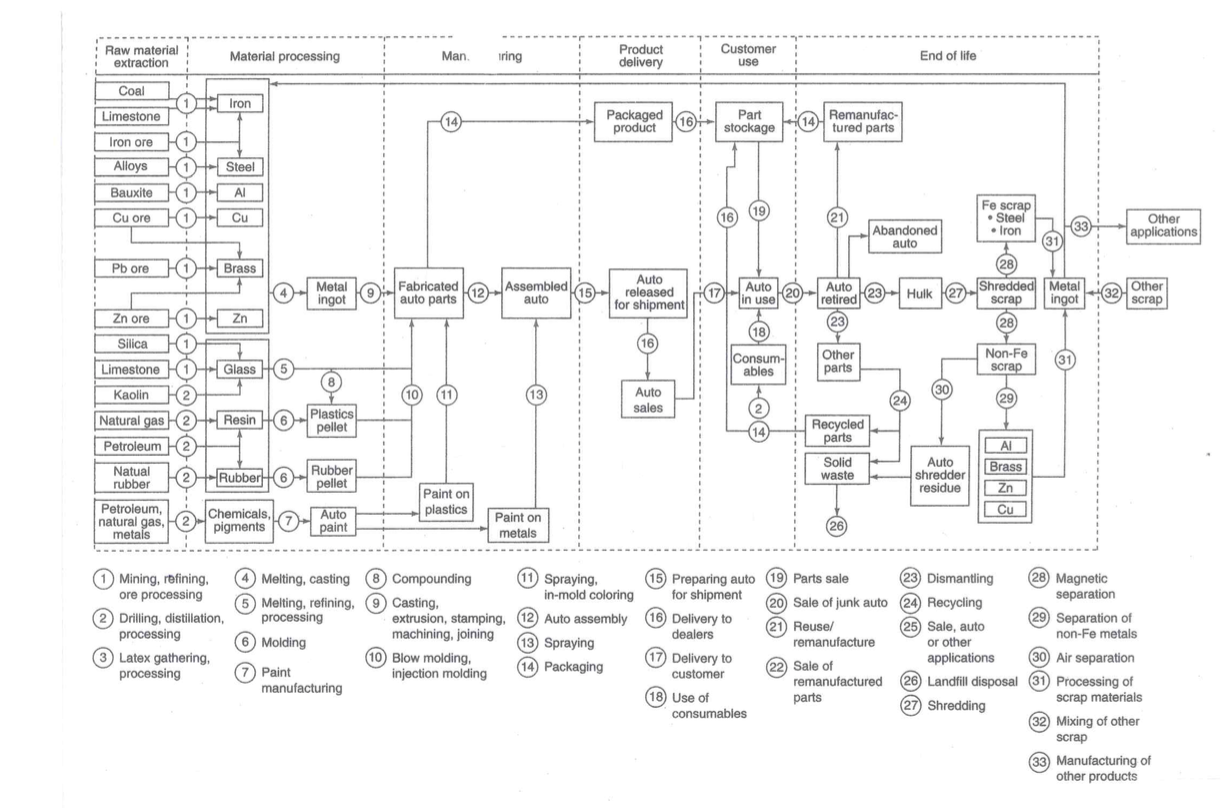
Manufacturing the Automobile
The manufacturing process of automobiles has changed with time. Examining such development show more engagement of automation-based processes and more complexity in the shaping and assembly of components. Revisiting the automobile manufacturing processes from the 1950s till the 1990s [25].
Cars from the 1950 era were some of the most classic and powerful cars ever driven, but the modern design and accelerations are getting more and more amazing year by year. The automobile manufacturing process of the 1950s adopted steel as the main structural material. After the formations of the each part, they were cleaned and welded together to form a frame for the automobile. The assembled frame and other components were then sent to the paint shop for the body paint. There were different departments for each process such as metal cleaning, welding, and brazing, painting, body assembly, system assembly, metal planting, test, and delivery, etc. At the same time, steel ingots were melted to produce transmission casings, engine blocks, and other high cross section components. After the painting process on the frames, the molded parts were trimmed, smoothed and cleaned. All the components were plated and then assembled into an active part of the automobile. After the final assembling the entire system was tested and then delivered to the end customers [25]. According to Friedrich [8], the Commission’s Auto – Oil I Program was one of the programs that were used for the future environmental legislation. The focus of the car manufacturers is the one adopting the regulations that are cost-effective and environment-friendly metal.
In the year 1990, the auto manufacturing process was almost the same, apart from a major change in the material. During the year 1990s, automobile manufacturing companies started using aluminum and plastic as the raw material along with steel. Aluminum was used as a material to design frames, windows, engine, and plastic were used to design fronts ends, interior fitting and non-load bearing body panels. Aluminum melts at much low temperature than steel. Initially, the parts were injection-molded, trimmed and smoothed and then delivered to the customer without further cleaning hence a different approach was taken to design plastic parts and die casting were used before the molding, trimming, and smoothing process [25].
The 1990s automotive manufacturing processes were more complex and spread over the larger footprint while adopting more diverse material types than the 1950s manufacturing processes. Trimming, smoothing, and cleaning was done in different sections for both aluminum and plastic.
Manufacturing Process of Automobiles
There are different processes of automobile manufacturing, and each process serves a different purpose. All the processes are interlinked with each other and functioning of some processes starts only after the completion of the previous process. The most significant process of automobile manufacturing are sand casting, metal forming, die casting, injection molding, metal plating, welding and brazing, painting, trimming and smoothing. The functioning of all the processes of the auto manufacturing has been discussed below.
The sourcing of raw material for the manufacturing of automobiles is one of the essential aspects. Most of the material used in the automobile comprises of the petroleum based products and the virgin steel along with some plastic material. The light weight material is derived from the overall process so that lighter and fuel efficient vehicles can be manufactured [31]. The design of the vehicle is one of the most important aspects of the overall manufacturing process of the vehicle. Therefore, manufacturers take a long time from the inception to the assembly of the different parts and components. The new ideas associated with the new models are being constantly developed so that public preferences and needs can be met effectively. The computer aided designs and equipment have been used so that best automobile designs can be developed. Simulation is one of the widely used techniques in the automobile industry that is used during the manufacturing process [29].
Sand Casting
Sand casting is the essential process of the manufacturing unit. During this process liquid is injected or poured into the molds and objects are formed. Detailed shape and patterns on the steel components are manufactured by the sand casting. With the hard sand images, the molds are formed and then the melted steel is poured into the mold and allowed to harden. After the hardening process, the excess sand is brushed away from the component. During this process, the energy use is very high [25]. Sand casting uses the expendable sand molds to develop the complex metal parts with the help of different types of alloys. The term “casting” is used because sand molds have to be destroyed so that the part can be removed from the mold. The production rate of sand casting is low. The overall process of sand casting comprises of metals, sand molds, patterns and the furnaces. Sand casting is a long process in which metal is first melted, laded and poured in the sand mold so that it can solidify and can be removed from the mold.
Die Casting
Die casting was not in existence in the manufacturing processes during the 1950s as it came into existence in the1990. Die casting is used to mold the frames of aluminum. Before pouring the melted aluminum, an organic parting agent is sprayed onto the die surface to keep the melted aluminum from welding itself to die [25]. According to Hsu [32], die casting is one of the processes that is widely used in the automobile industry because of its high productivity as well as the less post machining requirement. It is also light weighted and helps in the production of other components [32].
Metal Forming
Changing the shape and size of a metal part metal forming process is used in which parts are stressed to exceed the strength. The varieties of forming involve rolling, hammering, pressing and drawing. The metal forming process is an energy intensive process and lubricants are used to enhance the machinability. During the metal forming, the used material is somewhat recycled and energy use is high [25]. According to Tisza [33], there have been many advancements in the metal forming techniques in the automobile industry. The sheet metal forming is one of the most advanced and efficient technologies of forming the metal in the manufacturing industry because of its cost efficiency [33].
Injection Molding
Injection molding process involves the molding of plastic components. Plastic is injected into the mold under the high pressure. After the injection, the molded plastic is cooled and hardened to form the shape of the cavity. The mold is opened and then parts are removed after the hardening process. It is an energy intensive process and requires substantial energy inputs [25].
Welding and Brazing
Welding and the brazing process come after the formations of the components. Different components are welded and joined by applying heat and pressure to the joints between the parts. For basic welding, no added metal is required. The welding process requires a substantial amount of energy to melt the filler metal [25]. Mori [34] conducted a study in context of Welding and Brazing, and he identified that laser welding application is best for the automobiles because of its efficiency.
Metal Planting
A thin layer is placed over the components to protect or decorate the component. The process of placing the layer is called as metal plating. The protective metal used for coating on the component acts as an anode. For plating of the ions on the component, it is deposited in the solution coating [25]. According to Tangahu [35], Heavy metals are the most effective contaminants that are present in the environment.
Painting
Painting is the last coating on the component. The painting process is also called surface coating operation. Painting is performed almost on the components of the automobile. Painting process involves the capture and disposal of the paint overspray. The modern painting system uses the spray to paint the components which use a large quantity of air and energy [25]. The paints used in the automotive industry develop sludge of around 75,000,000 lbs every year. The sludge which is the waste makes significant contributions in developing the landfills. One of the proven solutions for this is to recycle the paint sludge into the ingredients associated with automotive sealants. It is one of the new approaches that can be used to minimize the wastage. The recycling of the paint sludge is useful for the paint industries and the sealant industries [31].
Trimming and Smoothing
After the casting and molding of the components, a further process is required to remove the extra material from the components and make their corners smooth. This excess material or plastic is termed as “sprues” and “runners.” This excess material is trimmed away and then smoothed to make the product compatible to fit along with the other components. Trimming and smoothing processes are not as energy intensive as other processes. It normally uses tool steel machinery to cut and abrade [25]. According to Shin [36], trimming and smoothening of the car is one of the essential parts of finishing and technology must be used to ensure the best trimming and smoothening. In this context, image processing must be used to enable more automation in the inspection process, via vision systems.
Metal Cleaning
Metal cleaning is the second last process of whole automobile manufacturing unit. During all the process dirt, oil, and other contaminants tend to collect at the metal parts, and these all must be removed from the surface before coating. The metal cleaning step removes all these elements from the component surface by using liquid solvents, organic and inorganic in the linked steel tank. The main solvents used for cleaning are CFC and HCFC [25]. According to Helmer [37], the catalyst can be used for cleaning the metal, and since 2002 this practice is continued. The catalyst containing platinum, rhodium, and palladium should be utilized [37].
The Automobile Recycling Sequence
Automobiles are among the most recycled consumer products in the U.S. The recycling rate of the automobiles is very high. Recycling of the automobiles serves as a vital role in preserving the natural resources, and it also reduces the demand for scarce landfill space. Every year recycling of the automobiles saves 85 million barrels of oil. The first process of recycling is dismantled. Dismantler removes usable parts that can be sold in the existing market for example tires, rubber hoses, lead acid battery, usable body panels and plastic reservoirs which are removed from the car. The remaining vehicle is called a hulk and sent to the shredder. Large machinery is used in the shredder to chop the car remains into the very small pieces of 10cm. After the chopping, these small pieces are sent to a variety of operations to produce three output streams. The magnetic process is used to separate the metal fragments into ferrous and non-ferrous metal. A ferrous fraction consists of iron, carbon steel, stainless steels, etc. and nonferrous metal consist of aluminum, zinc, and copper. The separated mill and the non-ferrous fractions recycled into a non-ferrous separator are used to separate the resalable metal. After the separation, the rest material is termed as “automotive shredder residue” [25]. Cole [38], there are two major barriers in the recycling process first is associated with the labor cost and the second is dependent on the plastic scrap.
Economic Aspects of Automobile Recycling
Recycling is the process of recovering the materials, components and other resources from the recyclable product. Recycling is related to technology but is also termed as an economic activity due to the involvement of the parties. During the recycling, the exchange of resources is made in exchange for payments [25]. According to Damuth [39], there are number economic aspects of automobile recycling as it helps in reusing the useful material and hence achieving the resource optimization.
Recycling process saves the natural resources and energy that has is being consumed while manufacturing different parts of automobiles. It saves the energy that is sufficient for powering 18 million households in a year. When metal is recycled, then its consumption of energy is 74% lesser than the energy used in manufacturing the metal. Thus, by recycling the end of life vehicles, approximately 85 million barrels of oil is annually saved that can be used for manufacturing the other parts of automobiles. Likely, recycling of car recovers 11 million tons of steel and 800,000 ferrous metals that can be reused by the manufacturing industry.
Design for Recycling
During the recycling, it is difficult to recover the pure material from the automobile hulk. There is a need to change the design of recycling to get the reusable material. Closed-loop recycling is one of the methods that prefer to separate the reusable material to make the same product over again. The design of the recycling should focus on minimizing the use of.material diversity by choosing the desirable material, making it efficient to disassemble, and making the material easy to recover [25]. Kozer and Doelman [40], the selection of material for recycling is one of the most important aspects. The focus should be on the heavy and light weight metals [40].
Vehicle components and parts that become potential waste or scrap or materials that have been sent to landfill that will be recycled and converted into usable products as shown in Figure 15. Based on the study of Chen et al. [41], the potential design for recyclability of a product is determined during the design stage when materials can be improved.
According to ARA, the primary objective of automotive recycling are “to harvest automobile components for reuse and to recycle the remaining valuable materials into specification-grade commodities that can be used in the manufacture of new basic materials such as steel, aluminum, plastic, copper, and brass.”Vehicle parts such glass, metals, tires, and plastics are commonly recycled via end-of-life, closed-loop material recycling, waste composition, and industrial ecology. For example, grinding of composites vehicle parts is used for fillers and reinforcements [42].
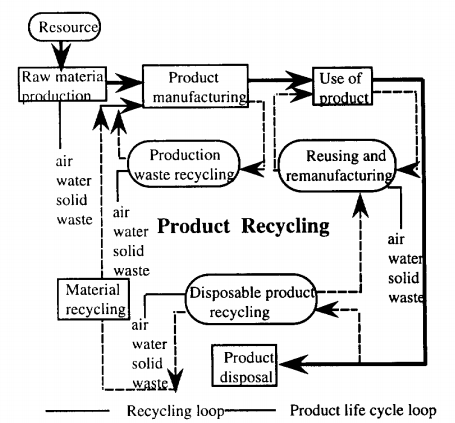
Bevilacqua et al. [43, p. 22] quoted Tsoulfas and Pappis [44] on the principles in product design, “design and develop recoverable products, which are technically durable, repeatedly usable, harmlessly recoverable after use, and environmentally compatible in disposal.” Used durable components of second-hand vehicles such as bumpers, doors, engines, and transmissions can be reused. Other parts such as batteries, carpets, catalytic converters, tires, some plastics are recycled into new products. Alternators, starters, and water pumps can be remanufactured. Coolant, engine oil, and gasoline are being reused or recycled. Metals are melted down and reused for manufacturing new products, building construction, or put back into the production of new vehicles.
Ogushi et al. [45, p. 50] provide a representation of the hierarchy of post use recovery options as shown in Figure 2, stating that the higher the recovery options the more environmental friendly it is. They further elaborate the life cycle options of product based on product stages that can relate to design of revalorization as shown in Figure 16.
Figure 16: Hierarchy of Post Use Recovery Options, Source:37.
Based on the research of Bevilacqua et al. [43] that advances in recycling technology are expected to improve in an increase rates such as number of recyclable product and both open- and closed-loop recycling options that will approach zero over the life of the product. Recycling infrastructure is major importance so number of vehicle manufacturers form alliances with United States Council for Automotive Research (USCAR) and European Recycling Platform (EUR) offering compliance and recycling services to number of countries and government around the world.
Cases of the application of automotive companies are presented by various studies: BMW and Mercedes Benz, two major German car manufacturers that introduce selection of environmentally compatible materials more recyclable components, and perform the material recovery process [46], [47]. According to Gungor and Gupta [48], the big three of American car manufacturers Chrysler, Ford, and General Motors are trying to enhance the disassembly features of their vehicle for efficient dismantling and disassembly techniques.
Figure 17: General overview of recycling, Source:37.
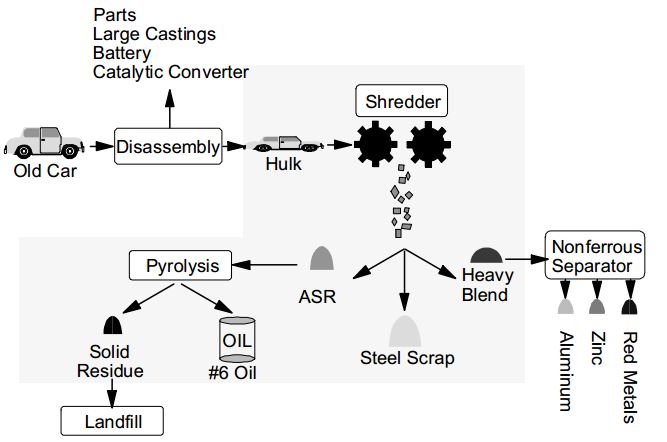
Other spare parts will be separated from engine parts, and it will be sold out as a second-hand part in the market. In the end, it will be brought to the shredder for shredding. It will sort out into the aluminum and steel by using high power magnets. Steel part will be separated into a container, and another part will be collected in another container. Further, each metal will be passed through furnace so that it can be melted which will result in another product as shown in Figure 8.
Recycling and Energy Requirements from the EPI Model
A key strategy of improving the energy efficiency and reducing carbon dioxide (CO2) emissions of the industrial sector in the US. The US Department of Energy and Environment Protection Agency (EPA) pursue this strategy by providing international standard service mark or certification through the trademark of ENERGY STAR program. ENERGY STAR is a statistical benchmarking tool embodied the Energy Performance Indicator (EPI) used to measure energy intensity (amount of energy per unit output) and energy efficiency (amount of output per unit of energy) of a production related activities such as plant-level energy use (e.g. auto assembly plant). Assembly plants consume the most energy within the motor vehicle sector. Table 12 shows the annual energy consumption by assembly plants spent over US$441 million on electricity [49].
Table 12: Annual energy consumption by assembly plants.
Through ENERGY STAR partnership has worked with automotive companies since 2002, (see Table 13) get engaged to develop guidelines, practices, technologies, metrics, and evaluation tools of monitoring plant energy efficiency. The performance indicators can be tracked from the type of raw material use, facility, process, and industry level. Each company goal is to achieve best in class energy performance by decreasing intensity and increasing efficiency. Energy efficiency production does not generally influence production rate and product quality, it is a direct effect on lowering production costs and supports customers’ energy management efforts. Energy is used in many different process applications in assembly plant as shown in Table 14.
Table 13: ENERGY STAR partnership with automotive companies.
Table 14: Energy use in variety of assembly plant process.
EPA has benchmarked the energy performance of U.S. automotive assembly plants as shown in Figure 19. The Energy Performance Score (EPS) of 75 percentiles or greater than is used as the benchmark for efficient plants. Less than 30% shows that needs greater improvements in energy consumption while greater than 50%, performance improvements focus more on optimizing systems.
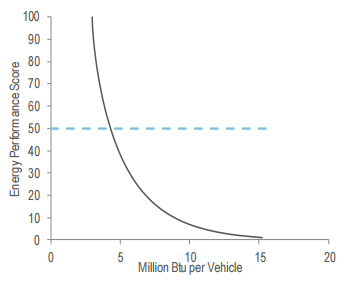
An assessment tool that provides a percentile ranking of an automotive manufacturing facility when compared with the best practices in the industry. This study analyzed the EPI stochastic model and complemented it with a gamma distribution function and loop up macro, to retrieve the actual energy consumption data.
where, ui is the process inefficiency, Ei is the energy consumed, Yi being the annual production, h is frontier specific energy use (kWhr/vehicle) which is a function of; Ii the system inputs and β a coefficient vector to be estimated, and finally θi is the noise in data set To develop a percentile ranking, inefficiency must be assumed to follow some statistical distribution, which yields an EPI score given by Equation (3); where P is the probability that energy use is greater than the “best practice” level and F is the probability density function for some appropriate one-sided distribution for inefficiency.

For predicting the energy consumed per vehicle (kWhr/vehicle) from the EPI model, a gamma distribution might be used to describe the inefficiency. The result of this statistical analysis yielded two equations for electricity and fossil fuel consumption as described mathematically in Equations (4) and (5) respectively; with the WBASE being the wheel base of the vehicle, and the Util is the facility utilization.
Microsoft Excel macro was operated using the EPI stochastic model in reverse i.e. it requires the plant rank as input to produce the energy electric and fossil-fuel consumptions and the HVAC portion. This computation quantifies the EPI ranking in terms of (kWhr/vehicle) and (MMBtu/vehicle) making it easier for production plants to assess their current consumptions (rank) in terms of actual energy expenses and to further quantify and monitor their future progress and goals. Also, the macro converts the fossil fuel consumption Fi/Yi (MMBtu/vehicle) into the total specific energy represented in (kWhr/vehicle), which is useful in translating the consumption into CO2 emissions, as will be discussed in section four.
Research methodology and results discussions
In the previous chapter, the discussion has been focused on the lightweight vehicle’ materials, lifecycle, manufacturing, and automobile recycling and its two important perspectives. The first one is technological while the other is based on the economic issues, thus when talking about the technological side of the recyclability, the focus should be on particular methods that can be specifically used for extracting the constituent material from the obsolete product. In the case of the economical side, the recycling depends on the market of the extract. Moreover, there must be a balance between cost of employing extraction technology, and quality of the extract. It should be ensured so that recycler always gets an economic incentive by undertaking the process of recycling.
This study will discuss the dismantler economic equation and the economic of shredding. The dismantler economic equation has five factors [1]:
- The cost of acquiring the old vehicle (to be scrapped, not used on the road).
- The labor cost of parts that can be sold after extracting sorting and distributing.
- The selling price that we can sell used parts.
- The cost of extracting and removing the parts and components (i.e., lead batteries, unexploded air bags and gas tanks, etc.)
- The price at which the stripped car can be sold to the shredder.
The economics of shredding depend on upon five factors
- The cost of acquiring the hulk.
- The cost of operating the shredder and ferrous separator.
- The cost of disposing of the ASR.
- The price the shredder gets for the shredded steel.
- The price the shredder gets for the mixed non-ferrous metal blend (Largely aluminum, zinc, and red metals).
In 2005, about 6.5 million automobiles were discharged from use in the United States; about 95% of these arrive at the recycling process [37]. Additionally, it is projected that at least 84% of the vehicle’s material content is reused. These records display that recycling plays a significant role in the automotive life cycle. There are many investors in the recycling of end-of-life vehicles (ELVs): Original Equipment Manufacturers (OEMs) design cars for Manufacturers and recycling; dismantlers eliminate workings from ELVs and make parts accessible for recycling, and shredding corporations separate the vehicle’s resources and forward it to those who process it into raw materials for new vehicles. According to Yi (2015) it is essential to monitor the recycling patterns of the end-of-life vehicles (ELVs) to facilitate the rate of recycling. The ELV recycling centers can even use the smart dismantling monitoring system along with smart trolley system [37].
The Processes Taking Place at the Dismantlers:
In practice, the processes taking place at a certified dismantler are the following:
- Recording of the vehicle information mainly the VIN and Chassis number in addition to any additional registration information, including the weight according to the registration document. The number of ELVs (end of life value) is called M, the total weight of the ELVs (end of life value) is called WM.
- De-pollution and dismantling for recycling. ELVs are de-polluted due to fluids that are stored in appropriate containers, which are later handed over to authorized receivers of such waste fractions, i.e. coolant, oils, brake-fluid etc. and these collectors then compute the total weights of these fluids received.
Following de-pollution, parts and components for recycling, i.e. catalysts, batteries, oil-filters etc., are dismantled. To compute the total weights of the parts received.
All fluids and/or parts and components for recycling, are now referred to as
WWF1 – WWFn, and the summation will be presented asWWF-SUM.
Dismantling for landfill, destruction or incineration
Some of fluids, components and materials will be considered as waste, and will be delivered for landfill, destruction or incineration. Here also, the weight of such items have to be considered and calculated by the dismantler.
The weight of those materials are represented as WLF1 – WLFnand the summation of it will be represented as: WLF_SUM.
Dismantling of parts and components for re-use
In addition to the above, the parts and components which are suitable for re-use will be checked and stored. The weight is also considered and represented as WRU.
Chassis to shredder
Coming up to the laststage of the process, after de-pollution, dismantling for recycling, dismantling for landfill and dismantling for re-use, the “Chassis” of the ELVs are now transmitted to shredders, where the total weight of the chassis is computed while loading to it.
The total weight of chassis is represented as SW.
Weight calculation
Weight of spare parts and components for re-use can now be calculated, based on the above indicators. Hence there is no specific need for measuring the weights of the spare parts put into stock – it can be calculated as:
Wwos = Wm – (Sw +Wwf – sum + Wlf – sum)
Similarly, the total weight of materials for re-use and recycling, at the dismantlers, can be calculated by the following
Wtmr = Wru + Wwf – sum
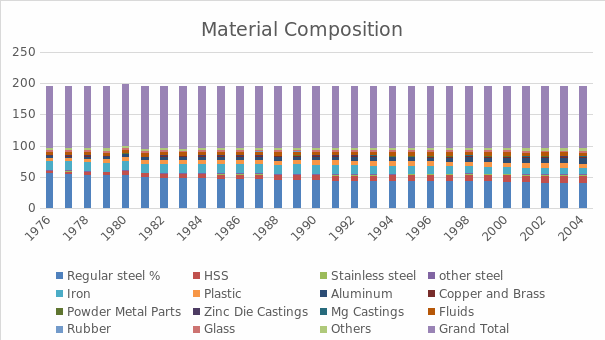
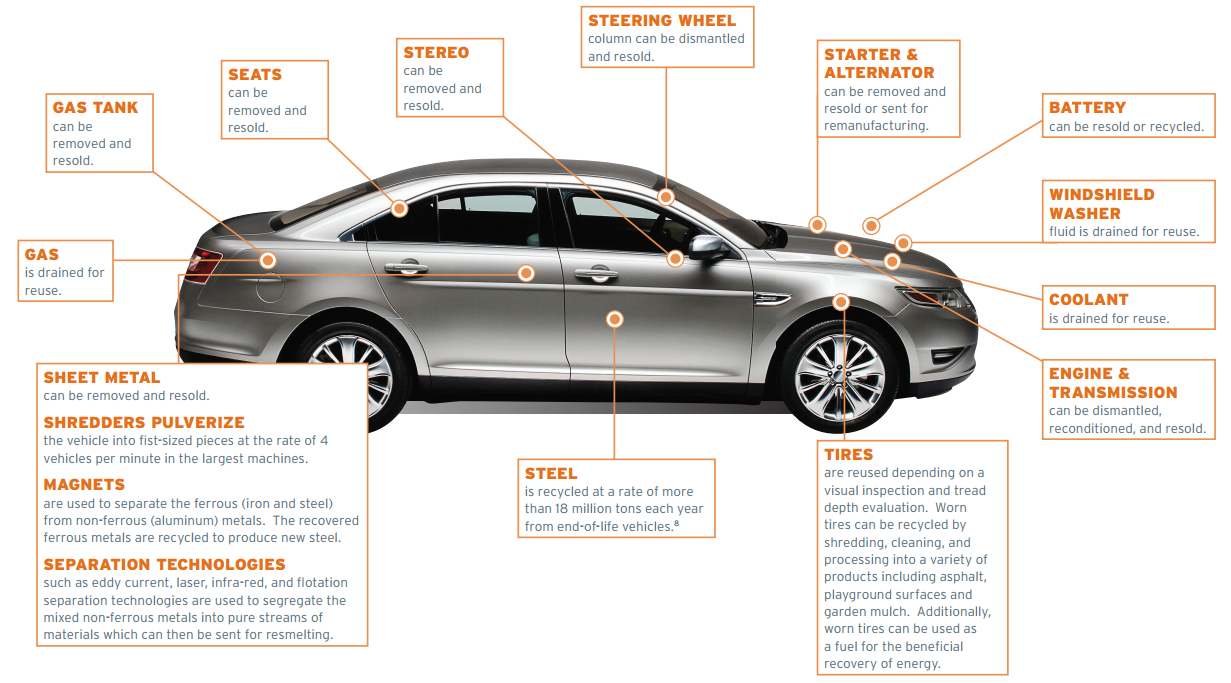
Shredding
- Before shredding, the parts and components that have been dismantled and stored to be re-used will be cut into plates and compressed in to sheets.
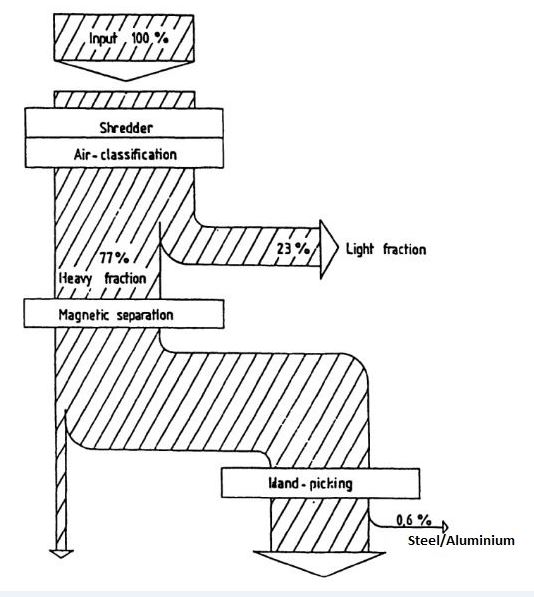
- Dismantled and pressed vehicles are shredded into pieces by shredder machines and segregated into iron, nonferrous-metal, dust, and others by magnetic selector, and nonferrous metals are typically recovered by using eddy-current separators. Iron is supplied to steel manufacturers; nonferrous metal is reused as material; dust is land-filled appropriately through auto manufacturers.
- Shredded pieces are passed under other magnet which removes any traces of the magnetic impurities.
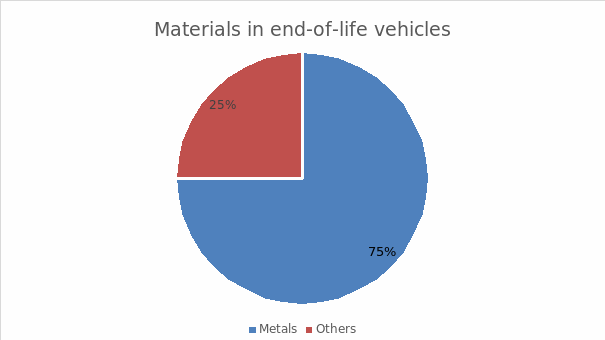
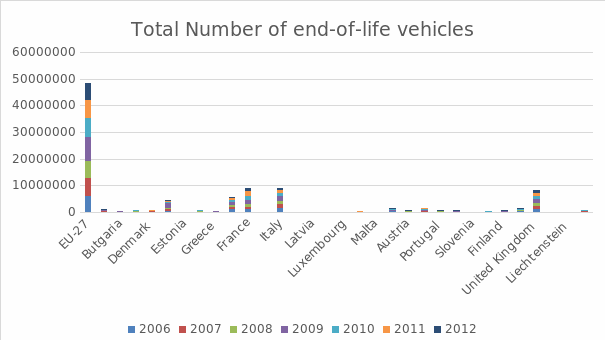
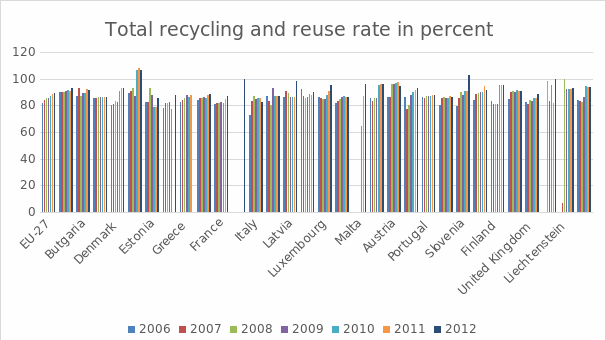
Specific Energy Analysis for automobile recycling
Energy required to get vehicle to shredder will be represented as Ets. It will be covering energy required to move scrap material to shredder. Energy required to run shredder will be represented as Ers. This will represent the energy as required by shredder to run.
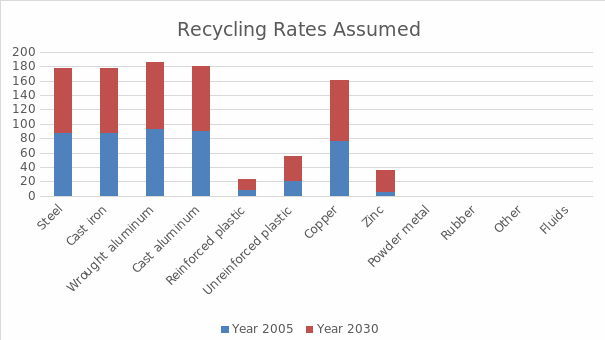
Energy required to separate aluminum and steel will be represented as Eas.
Energy required moving raw material of vehicle to furnace will be represented as Etf.
Energy required to run the furnace will be represented as Ef. Equ


the number of processes can be recorded sometimes.
The following equation will compute the total energy required while shredding.
Where, k will present the total processes in i starting point.
E is the energy consumed by respective process.
LYNXS shredder is considered in this paper as standard for specific energy analysis of automobile recycling [3]. For LYNXS Shredder 450 vehicles can be loaded per hour which is almost weigh350 tones. The below equation will compute the total shredded vehicles.
where, Vwrepresents the weight of a single vehicle.
Total weight represents total weight in tones being shredded per hour.
Total no. represents total number of vehicles being shredded per hour.
Using the standard equation to find the total weight of a vehicle:
Vw = 340/450 =0.78.tons which is nearly equal to 780 kg
The automobile body weighs 780 kg, and to find the energy consumed by one vehicle the below approach will be followed.
Knowing that the total number of vehicles is 450 and a shredder is using 6865kwh energy per hour, the energy used by one vehicle will be calculated as the below equation.
Energy required by one car=Eone car = ETotal KWH in an hour/ Vtotal no
Computing we will get the energy of one vehicle
Eone car= 6865 kwh/450 = 15.25 kWh per vehicle
To compute the energy required per Kg, the following equation will be used:
Ekg = Eone car/ (Vw*1000)
By computing the result will be,
Ekg = 15.25/(0.78*1000) = 0.0195kWh per kg
calculating the cost required for recycling per vehicle:
Amount of fuel used to generate 1 kWh:
- Coal = 0.00052 short tons or 1.04 pounds
- Natural gas = 0.01011 Mcf (an Mcf equals 1,000 cubic feet)
- Petroleum = 0.00173 barrels (or 0.07 gallons)
Kilowatt-hour generated per unit of fuel used:
- 1,927 kWh per ton, or 0.96 kWh per pound, of coal
- 99 kWh per Mcf (1,000 cubic feet) of natural gas
- 578 kWh per barrel, or 13.76 kWh per gallon, of petroleum [50].
Petroleum source will be used while producing 1KWh energy.
Total petroleum required for 1kwh energy equals to 0.00173 barrels so for 15.25 kWh will require
F used per vehicle =Eone car × Total Fossil requires to generate 1Kwh
where F represents fossil used per vehicle
The results for the above equation (Equation 8)will be:
F used per vehicle = 15.25 × 0.00173 = 0.02638 barrels
To find the cost per vehicle the following equation will be used:
Total cost per vehicle = F used per vehicle× Rate per unit Equation 14
Applying the result of Equation 6in Equation 9, the new result will be:
Total cost per vehicle = 0.02638 ×$48.72 = $1.285
Coming up to the total cost which will be calculated per Kg, the following equation will be used:
Total cost per kg = Total cost per vehicle/ (Vw*1000)
Applying Equation 10 the result will be:
Total cost per kg= (1.285) ⁄ (0.78×1000) = 0.00164$/kg
According to American Iron and Steel Institute the average of the vehicle weight is 60% of Steel and 40% remaining of other materials such as aluminum and plastic [4]. Going through the recycling process after dismantling, it has been found that 75% of it contained metal and the remaining 25% contained other materials such as plastic, glass and tires, etc. focusing on the 75% of the metal, 60% of it will be steel which is equivalent to 80% of 100%, and the remaining will be Aluminum which equals 15% of the total weight, and that will be equivalent to 20% of 100%
To calculate the metal cost per Kg the following equation has been used:
Total metal Cost per kg Al/Steel= Total cost per kg × Percentage of Metal Equation 16
Using the result of (Equation 10) the new result of the Aluminium will be:
Total Cost per kg of metalAl= 0.00164 ×20% = 0.000328$/kg
Calculating the cost of the steel per kg using the same equation, the result will be:
Total Cost per kg of metalSteel= 0.00164 ×80% = 0.001312$/kg
To find the energy consumed by specific metal using Equation 7 the following equation will be driven:
Energy consumed of metalAl/Steel= Ekg × Percentage of Metal Equation 17
Using the result of Equation 7 the energy consumption of the Aluminum and the Steel will be computed as the following below:
Energy consumed of metalAl/Steel= 0.0195× 20% = 0.0039kWh/kg
Energy consumed of metal Al/Steel= 0.0195× 80% = 0.0156kWh/kg
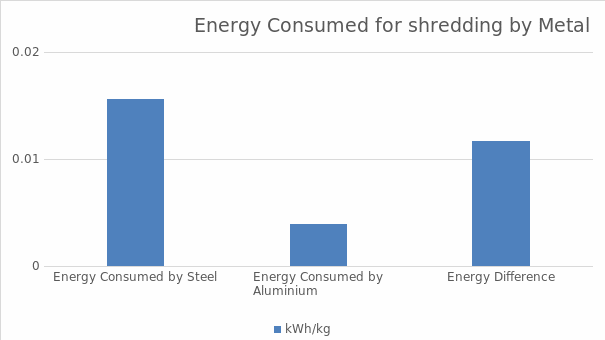
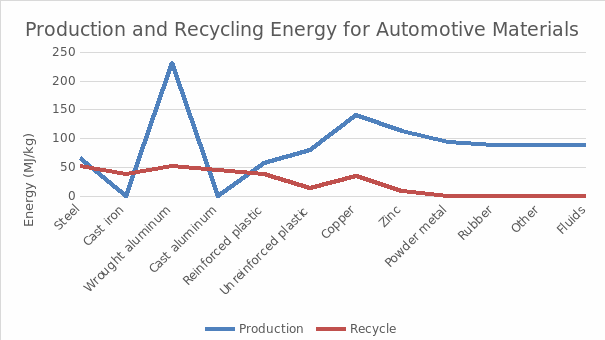
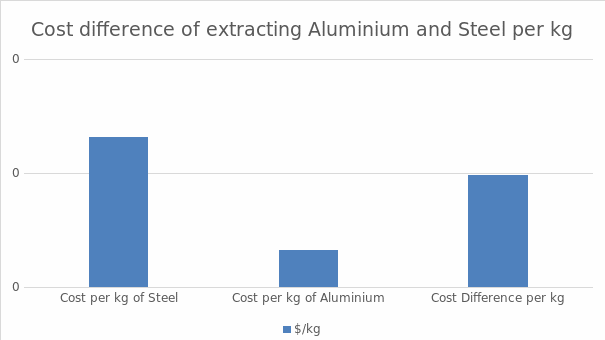
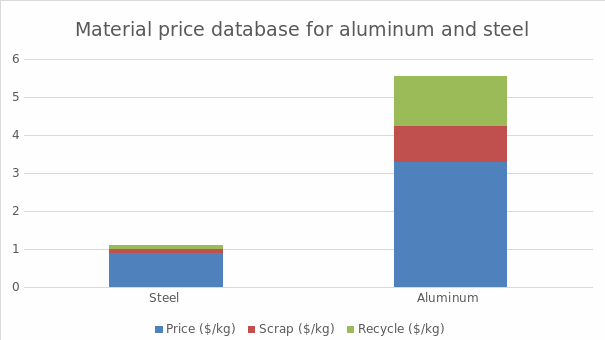
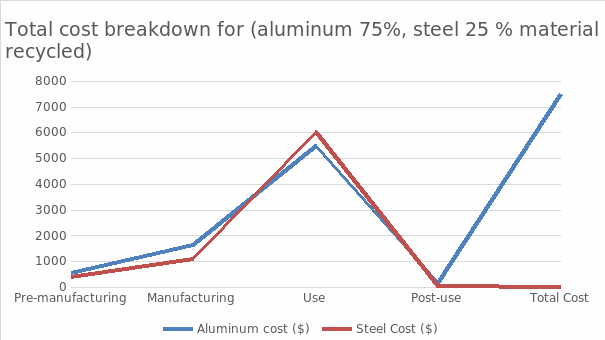
Application of Scrap Metal
Recycling of scrap metal makes good economic and environmental sense. The phrase, “circular economy,” depicts that everything made should be manufactured in such a way that they can be later dismantled and remade into an end product once the original product has lost its usability to the user. Scrap metal can be redesigned into many new uses [52].
Applications in Industry
Scrap iron/steel and aluminum metals are being used widely in the construction projects and transportation industry such as making of automobiles, aircraft, and other ways of transportation. One of more recent use is in detoxifying industrial waste water. Scrap metal is also used extensively in the production of containers, which are used widely by many companies. Many of appliances are also made up of scrap metal, especially aluminum. The use of scrap metal helped the environment in reducing the need for mining natural resources that are becoming scant [7].
New and Stronger Metal Products
Recycled steel metal scraps can be used in making of lower quality tools through a process using an electric arc furnace. Stainless steel can also be produced in this way. Copper scrap is made into different usable items using some of the same processes as used by steel, which also includes blast and reverberator furnace operations. Aluminum scrap metal can be melted at much lower temperature than virgin aluminum, so the process consumes lesser energy. It applies to all recycled metals, which not only saves a lot of energy but also Co2 emissions. This protects our environment, also providing economic savings in the manufacturing process, which is then hopefully passed on to the customer [44].
Helping to Preserve Our Environment
In addition to the above-mentioned usages of scrap metal, it is important to note just how much our environment is being saved. Just in the use of recycled steel, air pollution is reduced by 86%, water usage is reduced by 40%, and water pollution is reduced by 76%.
Uses of Plastic
Recycled plastic can be used in many applications, for example, packaging, construction, and automotive products.
Material Flow
The material flow analysis (MFA) tracks the flow of physical inputs and outputs that are associated with the production processes and lifecycle of a product. It is based on the application of the mass balance principle [25]. The goal is sustainability towards reducing environmental problems while maintaining economic growth. The total material flow as shown in Figure 31 and Figure 32 processes convert raw materials from one form to another adding value to each step in the most efficient way, with the least amount of waste so that materials and energy are used more efficiently manner. Based on MFA, losses can occur at each stage in the material flow which is often modeled through these five processes from material extraction, processing, fabrication, product use, and disposal considering the main inputs and outputs of the different production processes. With MFA, it will keep the losses of automobile raw materials to an unavoidable minimum while productively achieving greater reusability and recyclability of the materials.
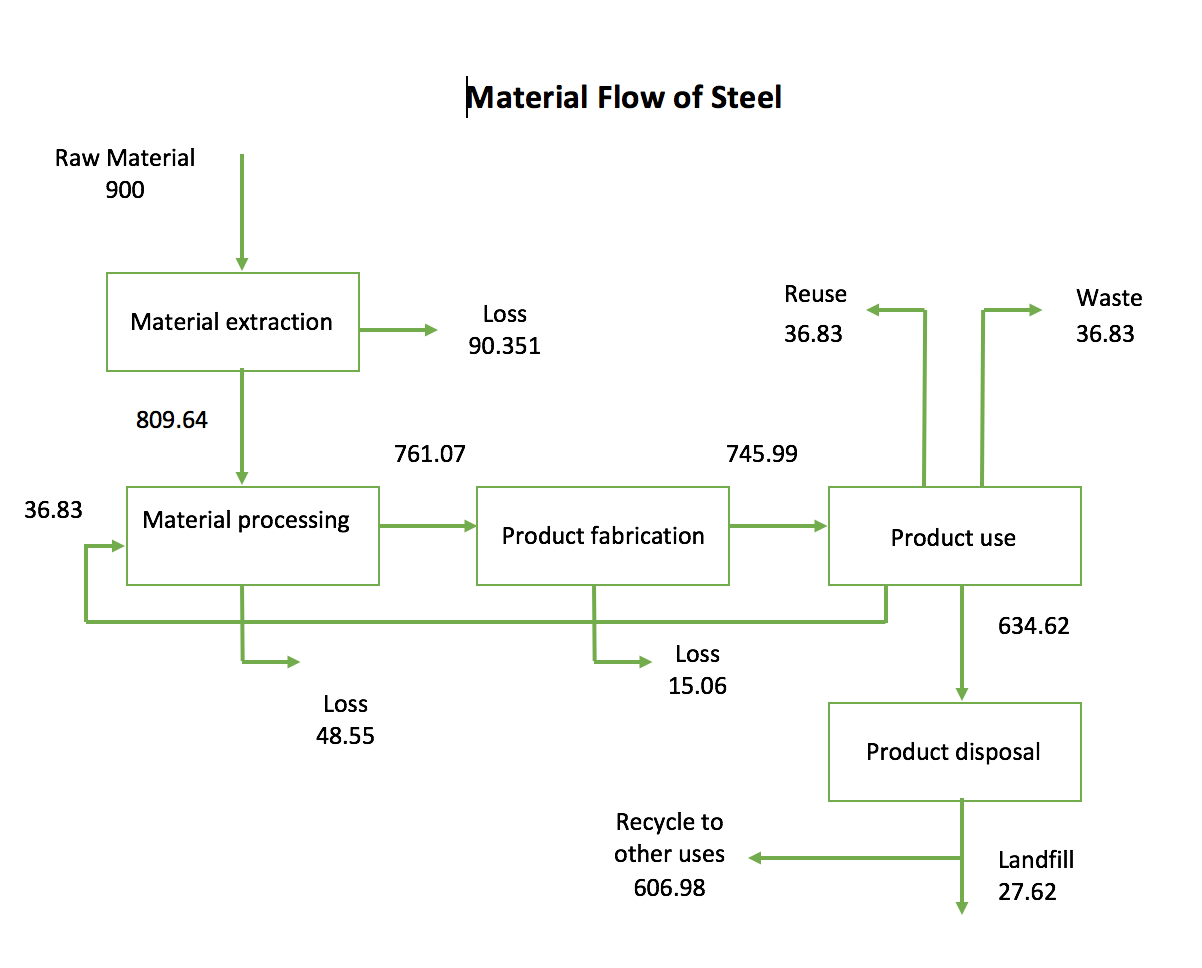
Applying material flow analysis to automobile steel (Figure 31) and aluminium lifecycle (Figure 32), it enabled to obtain robust estimate of amount of material to be reused, recycle, scrap, and landfill to assess the level of closure of the steel and aluminium cycle. With the increased reusability and recyclability of steel and aluminium, the costs become smaller. Aluminium has a higher assembly costs than steel but with the advancement of fuel efficient technologies in automobile, however, during the post-use stage costs with both materials to be 95% recycled, the aluminium has a higher scrap value $0.94 per kilogram compared to $0.10 per kilogram for steel, giving aluminium a costs advantage [54].
Table 15 shows the percentage of losses per stage of the MFA as well as reuse rates during product use and recycling rates during the product disposal stage. In the case of aluminium, during the first three stages, indicates that it will incur around 23.64% loss greater than steel with 18.01%. However, in the post-use and disposal stage, the reusability and recyclability aluminium outweighs steel which embodies greater savings of energy if aluminium is recovered from reuse and recycling than steel. Despite significant technological advancement, the use of aluminium as lighter mass equivalent material to replace traditional raw materials of automobile such as steels by maintaining the same vehicle design and using the same manufacturing processes for body components has been slow. There is a lack of comprehensive economic and material analysis of all types of aluminium and steel products which can serve as best substitute.
Table 15: the percentage of losses per stage of material flow.
Therefore, the choice of materials such as using lighter-weight materials and the design of the automobile should be considered with enormous concern to achieve better reusable rates. This highlights the need for detailed material flow analyses of each type of steel and aluminum used in the automobile to a clear scope of positive returns and economic value. In achieving economic value, automobile manufacturers will experience tradeoffs and compromises with regards to material performance, costs, and energy use as shown in Table 16 and Table 17.
Table 16: Energy Consumed during the production of steel and aluminium from Ores.
Table 17: Energy Consumed during the production of steel and aluminum from recycling process.
Future recycling possibilities
To develop a more efficient and effective infrastructure for the future, recyclers must consider the horizontal recycling of concrete as of now this process is not the part of the recycling process. By including this process in the recycling process the volume of the landfills will be decreased to some extent35. According to Crandall and Cameron35, there are immense opportunities associated with recycling in all the sectors but an appropriate recycling design must be chosen so that recycling process can be effective [35].
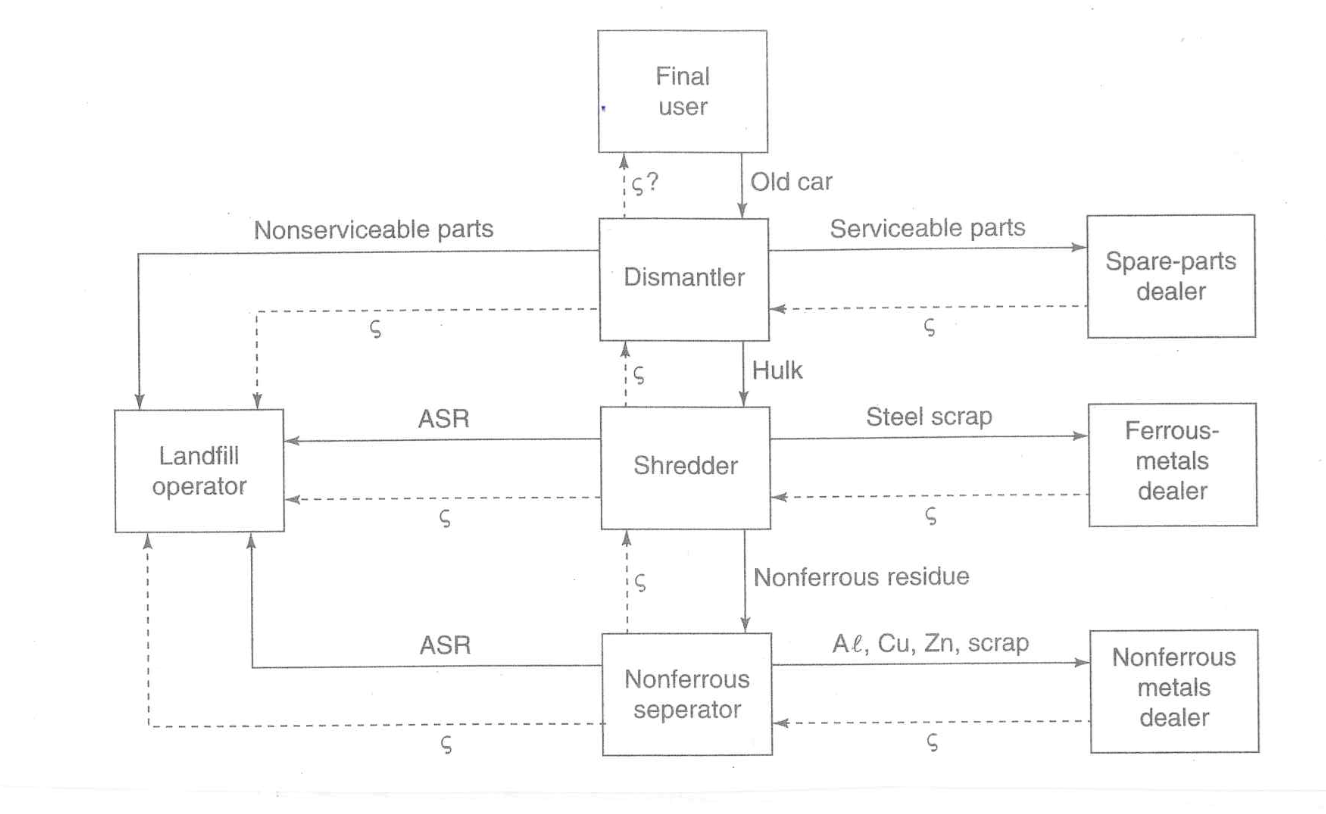
The above diagram was developed by Frank Field of Massachusetts Institute of Technology. This figure represents the interplay between economics and technology in the automobile recycling. It indicates both the economic flow and material flow. The initial transfer of the material was the last owner and the dismantler. The economic flow is in the either direction. There is an exception in the case of the disposition of the material where the material and payment is transferred from the last owner to landfill operator. The above figure shows that recycling infrastructure is a complex process with a number of actors. Another aspect that has not been reflected in the figure is that actors associated with recycling of automobiles are also involved in recycling of other products. It also shows that the recycling process of the automobile can be shut down at any point of flow of material if any of the economics or technology is not effective [55].
It also suggests that the environment of technology is constantly changing, but the focus of the automobile manufacturers should be on solving the environmental problems and minimizing the pressure on the natural resources. The flow of material in the automobile industry should be in such a way that all the resources and materials are optimally utilized, and they can be recycled in the future. Technology in this aspect is one of the most important things that can be used in each and every aspect of the manufacturing process. The above figure shows that there are four basic steps involved in the recycling process. These steps are associated with the use of the nonferrous separator, shredder, dismantler, and then the automobile is ready for the use by the new user. All these steps have a common aim of separating the useful material from the old car so that the material can be used for manufacturing the future automobiles.
Contribution, conclusion and future work
The work presented has two important contributions. One is the assessment and other is the energy analysis. In the automotive industry, the material is usually selected taking into consideration the technical factors, customer demands, and the legal requirements. To determine the cost and recycling capability, the material used should also meet traditional and emerging needs. The assessment done in the report calculates the amount of energy needed to recycle the structure of the vehicle and the cost incurred for the same. The assessment also includes the light-weight alternatives. To optimally utilize all the resources, the flow of material should be like that of such material which can be recycled in future.
The presented study analyzed the energy being used for automobile recycling in term of (kWH/vehicle/Kg) and the cost ($/kg) which has been spent to recycle automobile body. The study has concluded that energy consumed on recycling of vehicle to obtain aluminum and steel is way lower than the extraction of both materials. Previous theories stated that total energy for production of auto parts from virgin steel sheet is about 65MJ/kg and for recycled production is about 52 MJ/kg. For wrought aluminum, the total energy for virgin productions is about 231 MJ/kg and recycled production is about 52 MJ/kg. Energy use for extruded products is slightly lower because of lower scrap rates. The large difference is due to the high energy requirement for reduction of alumina (Al2O3) to elemental aluminum metal. Cast Aluminium castings are produced mostly from recycled material and therefore have a lower average embodied energy than wrought products, which are made from virgin raw materials. Therefore, the usual argument that aluminum is very energy-intensive and the use of aluminum in vehicle drives up the production energy is not entirely correct. When recycled material can be used, the energy per pound is comparable to that of steel, and the energy per part is lower. It is estimated that 80% of the aluminum used in cars today is recovered from scrap. The energy embodied in 1 kg of cast aluminum parts is about 44 MJ/kg. Therefore automobile recycling is always the best source of getting cheap aluminum and steel and it also saves natural resources as well in the form energy and in the form of natural ores plus save money. The total energy required for gray iron castings is about 37 MJ/kg, mostly in the form of coal for coke production.
Over the last ten years, the activities and innovations related to dismantling, shredding, and recycling of automobile parts have taken a new path in its history. But from the technical perspectives, the difficulties were increased with the entanglement of different issues. These efforts were also hampered due to lack of sustainable material in the market that can only be recovered using shredder residue. Despite all such facts, the areas that require the particular attention of the companies involved in the business of dismantling, recycling and shredding are recycling and recovery of polymers and conversion of fuel into energy. The records have revealed that in 2010, more scrap cars were recovered that were handled by the companies involved in the business of dismantling. The materials that are generated after recycling these cars are recyclable steel, light metals, copper, glass, plastics, precious metals, and tires.
References
Dara O’Rourke and Lloyd Connolly, “Industrial ecology: a critical review,” International Journal of Environment and Pollution, vol. 6, no. 2-3, pp. 89-112, 1996.
P. Wells and R. J. Orsato, “Redesigning the industrial ecology of the automobile,” Journal of Industrial Ecology, vol. 9, no. 3, pp. 15-30, 2005.
Paul Nieuwenhuis and Peter Wells, “15. Global versus Local: Regionalism in a Global Industry,” in The Global Automotive Industry.: John Wiley & Sons, 2015.
Henry Kallstrom. (2015) Raw materials – the biggest cost driver in the auto industry. Web.
Flake C. Campbell, Lightweight Materials: Understanding the Basics. 2012: ASM International.
Trefis Team. (2015) Trends In Steel Usage In The Automotive Industry. Web.
Michael D. Fenton and Reston, “Iron And Steel Recycling In The United States In 1998,” 1998.
Axel Friedrich, “new approach to EU environmental policy-making? The Auto-Oil I Programme,” Journal of European Public Policy, vol. 7, no. 4, 2000.
J. Sullivan, J. Kelly, and A. Elgowainy. (2015) Vehicle Materials: Material Composition of Powertrain Systems. Web.
P. Blain. (2012) Steel perspectives for the automotive industry. Web.
Emily Conover. (2015) Sciencemag.org. Web.
Stephen A. Mariano, “Comparing steel and aluminum auto structures by technical cost modeling,” Automotive Economic Research Summary, vol. 45, no. 6, pp. 20-22, 1993.
McKinsey & Company, “Towards the circular economy,” 2012.
A.Hari Kumar and V. Deepanjali, “Design & Analysis of Automobiles Chasis,” International Journal of Engineering Science and Innovative Technology, vol. 5, no. 1, 2016.
Patel Vijaykumar and R. I. Patel, “Structural Analysis of Automotive Chassis Frame and Design Modification for,” International Journal of Engineering Research & Technology, vol. 1, no. 3, 2012.
Elaheh Ghassemieh, “Materials in Automotive Application, State of the Art and Prospects,” in New Trends and Developments in Automotive Industry, Marcello Chiaberge, Ed., 2011.
M.R. Islam, “Thermal Recycling of Solid Tire Wastes for Alternative Liquid Fuel: The First Commercial Step in Bangladesh,” Procedia Engineering, vol. 56, 2013.
Julius I. Osayi, “Biocrude Production through Pyrolysis of Used Tyres,” Journal of Catalysts, 2014.
Akshyakumar S. Puttewar, “Enhancement of Braking System in Automobile Using Electromagnetic Braking,” Journal of Mechanical and Civil Engineering, 2014.
J.P. Yadav, “Experimental Set up of Air Conditioning System in Automobile,” vol. 5, 2014.
Ann Holms, “A Technical Research Report: The Electric Vehicle,” 2010.
Katarína Szeteiová, “Automotive Material,” Journal of automobile, 2012.
Feng JU, “Quality flow model in automotive paint shops,” International Journal of Production Research, vol. 51, no. 21, 2013.
Dev E. Millstein, “Effects of Retrofitting Emission Control Systems on In-Use Heavy Diesel Vehicles,” Environ. Sci. Technol., vol. 44, no. 3, 2010.
Thomas E. Graedel and Braden R. Allenby, Industrial ecology and the automobile.: Prentice Hall, 1997.
L. W. Jelinski, T. E. Graedel, R. A. Laudise, D. W. McCall, and C. K. Patel, “Industrial ecology: Concepts and approaches,” Proceedings of the National Academy of Sciences, vol. 89, no. 3, pp. 793-797, 1992.
Andy Garner and Gregory A. Keoleian, “Industrial Ecology: An Introduction,” 1995.
Douglas M Ginley, “Material flows in the transport industry,” Resources Policy, vol. 20, no. 3, pp. 169-181, 1994.
B.P. Bhardwaj, The Complete Book on Production of Automobile Components & Allied Products.: Niir Project Consultancy Services, 2014.
Mohammed A. Omar, The Automotive Body Manufacturing Systems and Processes.: John Wiley & Sons, 2011.
Michael J. Gerace, The Use of Recycled Solid Automotive Paint Wastes as Ingredients in Automotive Sealant Products.: cfpub, 1995.
Quang-Cherng Hsu, “Minimum Porosity Formation in Pressure Die Casting by Taguchi Method,” Mathematical Problems in Engineering, vol. 44, no. 3, 2013.
Miklós Tisza, “Recent development trends in sheet metal forming,” Int. J. Microstructure and Materials Properties, vol. 8, no. 1-2, 2013.
K Mori, “Laser Welding Application of Car Body in Nissan,” SAE Technical Paper, 2003.
Bieby Voijant Tangahu, “A Review on Heavy Metals (As, Pb, and Hg) Uptake by Plants through Phytoremediation,” International Journal of Chemical Engineering, vol. 42, no. 3, 2011.
Seong-Yoon Shin, “General Image Processing Technique and Car License Plate,” International Journal of Software Engineering and Its Applications, vol. 7, no. 6, 2013.
Helmer, “Chemistry: Cleaning up catalysts,” Nature News and Views, 2012.
Suzanne M. Cole, “Recycling the Automobile: ” Automotive Plastics Recycling, 1993.
Robert Damuth, “Economic Impacts and Environmental Benefits of Separating, Sorting, Processing,” 2010.
J. Krozer and P. Doelman, “Policy incentives for waste prevention. An economic approach to design for recycling,” The Journal of Sustainable Product Design, vol. 3, no. 1-2, pp. 3-17, 2003.
R. W. Chen et al., “A cost-benefit analysis model of product design for recyclability and its application,” IEEE Trans. Compon. Packag. Manuf. Technol, vol. 17, no.4, pp. 502-507, 1994.
J. Fiksel, Design for Environment: A Guide to Sustainable Product Development. New York, NY: McGraw Hill, 2009.
M. Bevilacqua et al., Design for Environment as a Tool for the Development of a Sustainable Supply Chain. London, UK: Springer-Verlag, 2012.
G. T. Tsoulfas and C. P. Pappis, “Environmental principles applicable to supply chains design and operation,” J Clean Prod, vol. 14, no. 18, pp. 1593-1602, 2006.
Y. Ogushi et al., “Assessing product life cycle strategies in the Japanese market,” in Innovation in Life Cycle Engineering and Sustainable Development, D. Brissaud et al., Eds. Dordrecht, the Netherlands: Springer, 2006, pp. 49-64.
S. B. Billatos and V. V. Nevrekar, “Challenges and practical solutions to designing for the environment,” in ASME Design for Manufacturing Conference. Chicago, IL: ASME, 1994, pp 49-64.
M. S. Hundal, “DFE: Current status and challenges for the future,” Proceedings of the 1994 ASME National Design Engineering Conference, vol. 67, pp. 89-98, 1994.
A. Gungor and S. M. Gupta, “Issues in environmentally conscious manufacturing and product recovery: a survey,” Comput Ind Eng, vol. 36, no. 4, pp. 811-853, 1999.
Energy Star. (2015). Industrial insights on automotive assembly plants. Web.
EIA. (2016) How much coal, natural gas, or petroleum is used to generate a kilowatthour of electricity? Web.
Gabrielle Gaustad1, “Design for Recycling,” Evaluation and Efficient Alloy Modification, vol. 14, no. 2, 2010.
Hwa-Cho Yi, “Design and Implementation of an End-of-Life Vehicle Recycling Center Based on IoT (Internet of Things) in Korea ☆,” Procedia CIRP, 2015.
Cameron S. Crandall, “Mortality Reduction with Air Bag and Seat Belt Use in Head-on Passenger Car Collisions,” Am. J. Epidemiol, vol. 153, no. 3, 2001.
Constantin Adrian Ungureanu. (2007) Design for Sustainability: Product Life-cycle Analysis in Aluminum Auto Body Applications. Web.
Bruno Figliuzzi, “Numerical simulation of thin paint film flow,” Journal of Mathematics in Industry, 2012.